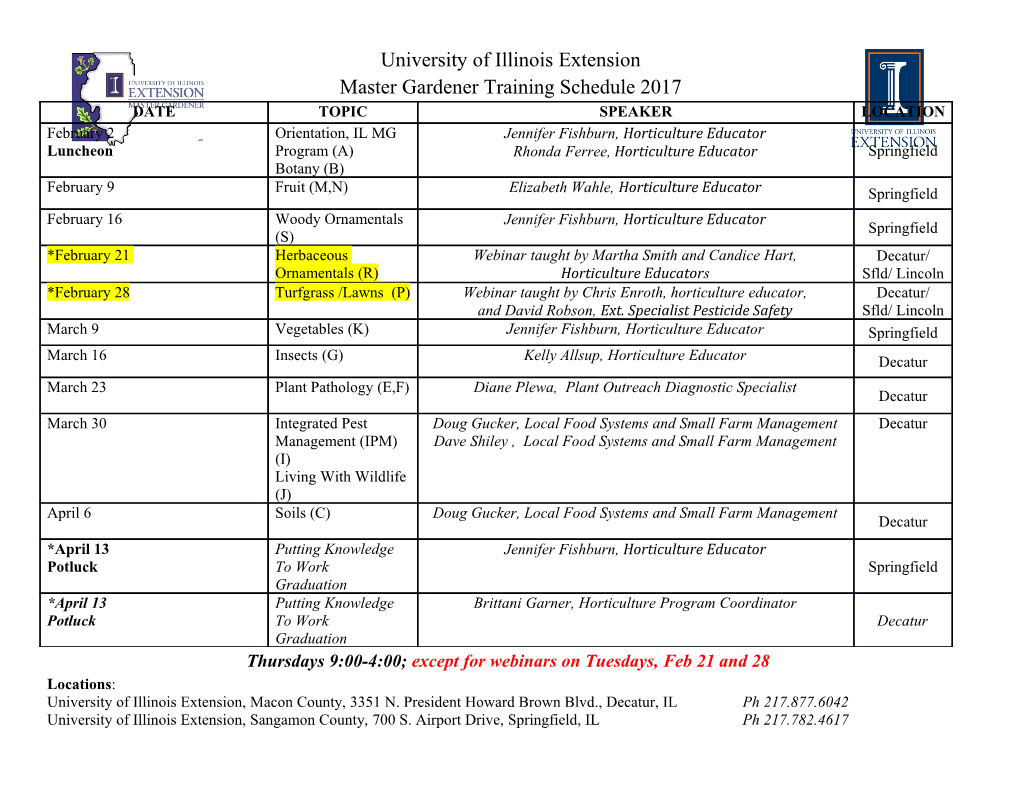
Unit 8 Other Concepts, Tools and Techniques-I Objectives After reading this unit, you.should be able to: + discuss the characteristics and structure of Quality Circles; + describe the took and techniques of Quality Circles; + explain the needfor and difirent Mes of benchmarking; and + implement and appreciate the usefulness of Quality Function Deployment (QFD) strum 8.1 Introduction 8.2. Quality Circles: Rationale and Brief History 8.2.1 Quality Circles: Essential characteristics 8.2.2 Structural Organisation for QC Circles 8.2.3 QC Circle Process 8.2.4 QC Circle Techniques 8.2.5 QC Circle Implementation 8.2.6 QC Circles: A Case Study 8.3 Benchmarking: Rationale 8.3.1 Principles of Benchmarking 8.3.2 Types of Benchmarking 8.3.3 Product Benchmarking 8.3.4 Performance Benchmarking 8.3.5 Process Benchmarking 8.3.6 Strategic Benchmarking 8.4 Quality Function Deployment (QFD): Rationale and Histofy 8.4.1 What is QFD? 8.4.2 QFDIHouse of Quality (HOQ) Table 8.4.3 Benefits of QFD 8.5 Summary 8.6 Keywords 8.7 Self-Assessment Questions 8.8 Further Readings , References 240 8.1 Introduodon TQM employs several tools and techniques. Some of these tools viz., Statistical Process Control (SPC), Acceptance Sampling,Taguchi's techniques, Parato analysis, 6-Sigma, etc. were discussed in the previous unit. In this unit we focus on three tools and techniques of TQM viz., Quality Circles, Benchmarking and Quality Function Deployment (QFD). This unit is the first of the two units dealing with "Other concept, tools and Techniquesn. The second unit will deal with the remaining other concepts, tools and techniques, e.g., Zen Defects, Reliability, Re-engineering, etc. 8.8 QualiwCircles: Rationale and Brief History Total Quality Management (TQM) has 'employee involvement' as one of its basic tenets. Such involvement does not mean only co-operation in carrying out tasks assigned by supervisors and managers but something more than that. All employees have basic intelligence and creativity. They acquire considerable amount of insights about their tasks and other related matters while carrying out any work, day in and out. The poten- tialities hidden within employees are normally not made use of. Quality Circles, alternatively known as Quality Control (QC) Circles, are the means of getting the potentialities utilized to solve problems that do arise in immediate work situations of the employees. Japanese industry was the first to discover and make use of this concept for very effectively bringing about the industrial recovery during the nineteen fifties. Such formations became so successful and widespread that quality circles are now said to be one of the sources of Japan's competitive advantages. Quality circles are also said to be the seeds of Total Quality Control (TQC) movement that became known as Total Quality Management (TQM) in the West. The beginning of the Quality Control Circle (QC Circle) idea can be traced to the Japanese drive for train- ing and accomplishment in quality control, and their conviction that effective quality control can only be achieved when the interest is aroused among the employees. With such a background, the logic of extending training to the workers was obvious. The Journal "Quality Control for the Foremann, published by the Japanese Union of Scientists and Engineers (JUSE), has played a key role in initiating the idea of QC Circles, to tap the immense potential for contribution by workers and first-line supervisors through training, moti- vation, and application of the techniques. The QC Circle idea was born around 1962. While the objective of QC Circle may vary from company to company, the following are identified as basic generalisations.: i) To encourage first-line supervisory personnel to educate themselves, and to develop legdership and supervisory capabilities ii) By including all workers, to raise the morale of the work force, to carry quality control to the ultimate degree, and encourage and develop employees' self-awareness of what quality is, what problems may arise, and what to do about them, and iii) To serve as 9 means of unifying company-widequality control activities and as a nucleus within the shop, and work t&rd clarification of executive and managerial policy, stablisation of work-place supervi- sion and guaranteeing of standards. By June 1962, there were three Circles registered with the Japanese Union of Scientists and Engineering (JUSE). As of August 1969, there were 24,000 QC circles registered with a membership of 2,80,000 and the 'num- ber was increasing by 700 to 1000 each month. By mid 1972, the Japanese estimated that the total QC Circles had reached 5,WOOO with a membership of about 5 million. The QCC movement grew very'fast since then till the A- . _. 4 nineteen eighties. It is estimated that during 1961-82,15 million projects had been completed. The QC Circle concept has spread to USA. It has been mentioned that the spread of QC Circle programmes throughout the American industries is unparallelled by any other organisational improvement programme. The Wall Street Journal reported (Sept. 1981) that about a thousand organisation had some form of Quality Circle programme. As early as 1974 Lockheed Missile and Space Company initiated a large- scale programme and during the years 1974-1977 the QC Circles had saved the company approximately 3 million dollars. The ratio of savings to the cost of operating the Circles was six to one, with great improvement in quality. Within the federal sector, Navy was the first to implement a QC Circle programme in 1979 in its Norfolk Naval Shipyard. By 1980 the shipyard claimed to have achieved a four- to-one cost-benefit ratio.The Navy has since expanded its QC Circle programme to a number of its bases and shipyards. In addition, a variety of other fed- eral agencies (including the Air Force, the Veteran's Administration, and the Public Health Service) have all begun to experiment with their own QC Circle programmes. Interest in the QC Circle process among federal agencies appears to be rapidly growing. In India, Bharat Heavy Electrical Ltd. (BHEL) has made an impressive start in introducing QC Circles (they call it Quality Circles). It began around 1980 in its Hyderabad Unit. It is reported that the Hyderabad Unit has introduced 51 cirdes with 455 members. 83 circles are working BHEL units with about 700 employees partici- pating. The names of the organisations which have introduced or shown interest are :Kirloskars,Shriram Group, -- Allwyns, ECIL, BEL and Heavy Engineering Corporation, Durgapur Steel (of SAIL). 8.8.1 QualityCircles: Essential Chara-tics Several definitions of QC Circles have emerged over the years. QC Circle is a small group of departmental work leaders and line operators who have volunteered to spend time outside their regular hours to help solve departmental quality problems (juran). QC Circles is a small work group which meets regularly to perform quality control activities voluntarily within the same workshop (Miyauchi). It is a small group of people doing similar work who meet voluntarily on a regular basis under the leadership of their supervisors to iden- tify, discuss and analyse their work problems and implement the solutions themselves if possible (attributed to Ishikawa). iL While one can thhk of some special small pupactivities existing in an organisation, QC Circle group has some unique features which are not present in most of the existing small groups or schemes. To understand the uniqueness of QC Circles, it is necessary to analyse the definition. (i) It is a small group of people who do similar works :This brings out that the group is small, the members belong to the same area of work who do similar activities ,know their environment, know each other well, and therefore can participate and contribute individuallyto the solution of problems on hand or for any other improvements. The most important aspect to note is that every member can be an active par- ticipant because of the structuring of the group. (ii) It meets voluntarily on a regular basis: Since the group is concerned with problems of their own >. work, they meet regularly (once in a week for an hour or so on company time or otherwise) and thrash but solutions. When circles have been introduced properly this effect can be observed anywhere. (iii) QC Circles identify problems, analyse the cause and recommend solutions : Because of the structuring of the group, it is in a position to identify problems with suitable training,and can compile information Other Conoepb, Tools aad Te&dquw-I and analyse the problem for possible solution and motivation. The challenge in the job thus introduced both for individual advancement and for working out possible solution. Upward communication in the structure is a new innovation of the circles. (iv) Where possible, employees implement the solutions themselves: QC Circles are not merely cbncerned in identifying problems, involved in analysing and providing solutions, but also implement them wherever possible, with of course, a planned trainifig efforts by the organisation.The implementation by the group or otherwise adds to the morale of the group and motivates them for improved performance. Though, initially, the QC Circles considered problems relating to quality ,their success has led to the broadening of the concept. One area of extension has been to deal with non-quality problems e.g. produc- tivity, safety, cost reduction etc. The most fruitful area of broadening the concept that has emerged is strengthening the relationship between the management and employees. Establiihment of QC Circles is not only cost effective but also improves morale, communications and attitudesin ways that promote long term benefits to the organisation. In fact, in the Indian context this aspect should be borne in mind.
Details
-
File Typepdf
-
Upload Time-
-
Content LanguagesEnglish
-
Upload UserAnonymous/Not logged-in
-
File Pages30 Page
-
File Size-