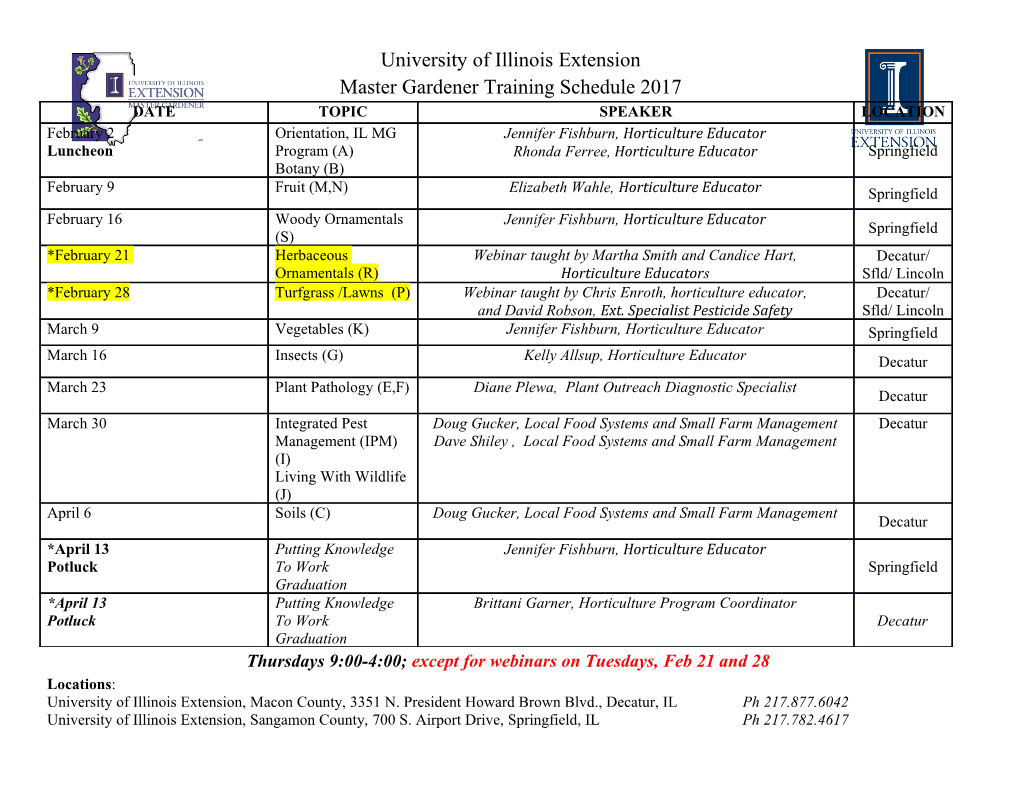
Reviews G. M. Whitesides et al. DOI: 10.1002/anie.201101024 Nanofabrication Use of Thin Sectioning (Nanoskiving) to Fabricate Nanostructures for Electronic and Optical Applications Darren J. Lipomi, Ramses V. Martinez, and George M. Whitesides* Keywords: nanofabrication · nanoskiving · plasmonics · soft lithography · ultramicrotomy Angewandte Chemie 8566 www.angewandte.org 2011 Wiley-VCH Verlag GmbH & Co. KGaA, Weinheim Angew. Chem. Int. Ed. 2011, 50, 8566 – 8583 Nanoskiving This Review discusses nanoskiving—a simple and inexpensive method From the Contents of nanofabrication, which minimizes requirements for access to cleanrooms and associated facilities, and which makes it possible to 1. Introduction 8567 fabricate nanostructures from materials, and of geometries, to which 2. Ultramicrotomy and more familiar methods of nanofabrication are not applicable. Nano- Nanoskiving 8569 skiving requires three steps: 1) deposition of a metallic, semi- conducting, ceramic, or polymeric thin film onto an epoxy substrate; 3. Electronic Applications of 2) embedding this film in epoxy, to form an epoxy block, with the film Nanoskiving 8573 as an inclusion; and 3) sectioning the epoxy block into slabs with an 4. Optical Applications of ultramicrotome. These slabs, which can be 30 nm–10 mm thick, contain Nanoskiving 8576 nanostructures whose lateral dimensions are equal to the thicknesses of the embedded thin films. Electronic applications of structures 5. Summary and Outlook 8580 produced by this method include nanoelectrodes for electrochemistry, chemoresistive nanowires, and heterostructures of organic semi- conductors. Optical applications include surface plasmon resonators, 1.2. Nanofabrication plasmonic waveguides, and frequency-selective surfaces. Nanofabrication refers to the gen- eration of patterns whose individual elements have at least one lateral 1. Introduction dimension between approximately 1 nm and 100 nm.[9] Nano- fabrication, along with microfabrication before it, has been a 1.1. Why Nano? key enabler of modern science and technology, and has underpinned essentially all electronics since the invention of Many of the most important phenomena in nature—e.g., the integrated circuit in 1958.[5] Nanofabrication, as practiced the binding of proteins and ligands, the absorption of light by in electronics and related areas of technology, has two molecules, and the mean free path of electrons in metals— principal steps: mastering (e.g., forming master structures involve forces or processes operating over distances of 1– such as amplitude and phase masks for photolithography) and 100 nm. Processes that occur over this range—which begins replication.[9] Mastering encodes nanoscale information about with large molecules, and ends with objects that are resolved patterns in a form from which the pattern can be replicated with conventional microscopes—are the purview of the field (usually with a reduction in lateral dimensions). In semi- known as “nanoscience”. Nanoscience represents an exten- conductor manufacturing, the principal tool for mastering is sion of, and the overlap between, the chemistry of materials, electron-beam lithography (EBL), which creates patterns in a solid-state physics, electrical and mechanical engineering, photomask. Mastering is a time-intensive and expensive biology, and other fields. Nanostructured materials display process, and may require twenty hours to produce a single properties not found in bulk materials. These properties mask.[10] Replication of this pattern takes the form of include the effects of size confinement, including size- photolithography, in which light passes through the photo- dependent band gaps in quantum dots,[1] localized surface mask and creates an image on a wafer coated with a film of a plasmon resonances in metallic nanoparticles,[2] exceptional light-sensitive polymer called a photoresist. Modern exposure strength and ballistic transport of electrons in carbon nano- tools generate around 100 copies minÀ1.[10] After chemical tubes,[3] and consequences of the fact that these structures are processing, the surface of the material comprising the wafer “all—or mostly—surface”.[4] can be modified in the areas of the film unprotected by Beyond discovery-based scientific inquiry in these areas, photoresist (e.g., by etching, vapor deposition, ion implanta- there are also opportunities for technological development. tion, or other processes). Iteration of these processes gen- Nanostructured materials have already enabled the electron- erates the devices and connections on a chip. ics industry to fabricate faster, cheaper, and more efficient An empirical trend—Moores Law—shows that the devices,[5] are making inroads into medicine,[6] and could number of transistors per microprocessor has doubled contribute in significant ways to sensing, communication, and approximately every 18 months, with concomitant decreases computation based on nanophotonics.[7,8] Developing meth- in cost and power consumption, and increases in speed for ods of generating and patterning nanostructures that are reproducible, scalable, inexpensive, applicable to different types of materials, and as widely accessible to as many users as [*] Dr. D. J. Lipomi, Dr. R. V. Martinez, Prof. G. M. Whitesides Department of Chemistry and Chemical Biology, Harvard University, possible, is thus an important motivation for the sciences of 12 Oxford St., Cambridge, MA 02138 (USA) materials chemistry and nanofabrication. Prof. G. M. Whitesides Kavli Institute for Bionanoscience and Technology, School of Engineering and Applied Sciences, Harvard University, 29 Oxford St., Cambride, MA 02138 (USA) Angew. Chem. Int. Ed. 2011, 50, 8566 – 8583 2011 Wiley-VCH Verlag GmbH & Co. KGaA, Weinheim 8567 Reviews G. M. Whitesides et al. information processors and in storage capacity for memory 1.3. Soft Lithography devices.[11,12] This trend has become a self-fulfilling prophecy, which has motivated the development of new steppers for Soft lithography[25] is a set of techniques whose key step is projection photolithography,[13] chemistry for photoresists,[14] the transfer of patterns by printing or molding, usually using and other technologies.[5] The state-of-the-art in photolithog- an elastomeric stamp or mold, which often is made from raphy produces features with an average half-pitch in memory poly(dimethylsiloxane) (PDMS), perfluoropolyethers, or devices of 32 nm using 193 nm light combined with immersion other polymers.[26] There are three general modes of soft optics,[15] phase-shifting masks,[16] and multiple exposures.[17] lithography: 1) molding (replica molding,[22,27,28] solvent- Next-generation lithographic tools, including extreme ultra- assisted micromolding,[29] and micromolding in capillaries[30]); violet lithography (EUVL),[18] maskless lithography (ML2, 2) printing (microcontact printing,[31–34] charge printing,[35] and which would use thousands of electron beams to replicate nanotransfer printing[36]); and 3) near-field optical lithogra- patterns without the need for a physical master),[19] and step- phy (in two or three dimensions).[37–39] The key steps of all and-flash imprint lithography (SFIL)[20] are expected to drive forms of soft lithography rely on physical contact. The limits the average half-pitch down to 16 nm by 2019, according to of fidelity in replication in soft lithography are not deter- the International Technical Roadmap for Semiconductors.[10] mined by the diffraction of light, or scattering of beams of Informed speculation suggests an ultimate limit that may be charged particles, but rather by van der Waals interactions, as small as 8 nm. physical deformation of the stamp, wicking or spreading of Semiconductor devices are manufactured using the most liquid inks, and related processes.[9] Nanoimprint lithography sophisticated processes ever employed for commercial prod- (NIL) and step-and-flash imprint lithography (SFIL)—tech- ucts. The scale of investment in these tools is so high (and the niques pioneered by Chou[9,40,41] and Willson[20,42]—largely precision in replication is so precise), that it does not make circumvent errors due to mechanical deformation by using sense to compete with them for their designed purpose— hard masters. manufacturing multilayered semiconductor devices on planar, Unconventional approaches to nanofabrication that do rigid substrates. There are, however, at least five reasons to not involve a stamp or mold include variants of lithography explore “unconventional” methods of fabrication. 1) Cost: using scanning probe tools.[43] Dip–pen nanolithography, photolithographic steppers and other tools can be prohib- invented by Mirkin and coworkers, uses an atomic force itively expensive, particularly for universities.[21] 2) Accessi- microscope (AFM) tip dipped in “ink” (e.g., small molecules, bility: scanning-beam lithographic and photolithographic polymers, or other materials) to draw patterns on surfaces tools are usually found in a cleanroom, whose construction, with linewidths as small as 10 nm with approximately 5 nm operation, and maintenance impose a significant financial spatial resolution.[44] This method operates using single AFM burden on an institution. 3) Incompatibility: organics, bio- tips or arrays of thousands of tips connected in parallel.[45] logics, and other materials not normally used in (or compat- Related techniques include local oxidation, nanoshaving and ible with) electronic devices often cannot be patterned nanografting using an AFM tip.[46] Indentation
Details
-
File Typepdf
-
Upload Time-
-
Content LanguagesEnglish
-
Upload UserAnonymous/Not logged-in
-
File Pages18 Page
-
File Size-