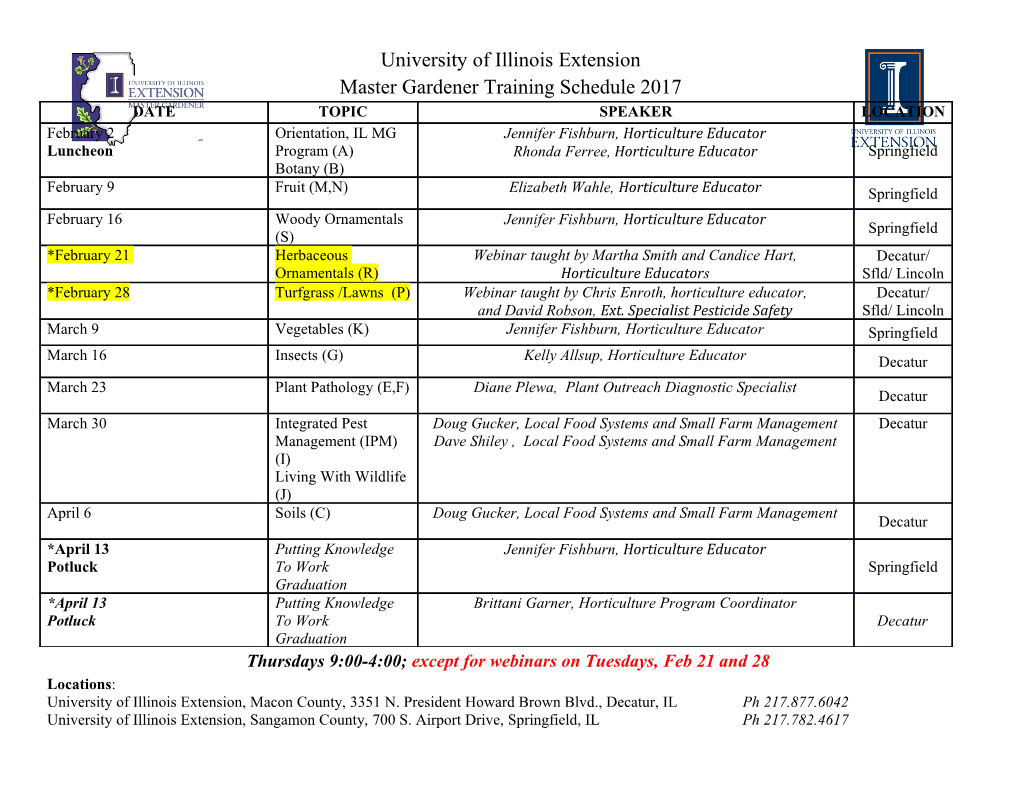
Improving the distillation energy network Energy-efficient design applied to the refit of a distillation unit was achieved through optimisation between the distillation column and heat network system SOUN HO LEE GTC Technology KWANG GIL MIN GS Caltex Corporation nergy costs are the largest process conditions. The following location is a section of the distilla- percentage of a hydrocarbon are common strategies that can be tion column where the composition Eplant’s operating expenditures. applied to practical energy of column internal liquid traffic is This is especially true of the distil- improvement projects. similar to feed stream composition. lation process, which requires In this case, the composition gradi- substantial energy consumption. Feed temperature ent between feed stream and Concerns over recent high costs Feed temperature is a major factor distillation internal fluids is mini- and economic pressures continually influencing the overall heat balance mised. In actual operation of the emphasise the need for efficient of a distillation column system. distillation column, feed composi- distillation design and operation Increments in the feed enthalpy can tions are often changed from the without a loss of performance. help reduce the required energy original design conditions. In cases This article illustrates how input from the reboiler at the same of significant deviation, discrepancy energy-efficient design can be degree of separation. Installing a between column internal liquid applied in a distillation unit through feed preheater is a very common composition and feed stream optimisation between the distillation process option to minimise reboiler composition can increase, which column and heat network system. heat duty. If the feed preheater can results in a non-optimum feed loca- Through a case study, a successful be integrated with other valuable tion. Therefore, evaluating feed retrofit of an aromatics distillation process streams (as a heating location is an essential step for unit is discussed. Detailed retrofit medium), overall energy efficiency successful distillation unit energy activities, including complex heat of the distillation system can be improvement. network evaluation, process simula- improved further. However, tion modelling and energy-friendly, increasing the feed temperature Inter-condensers and inter-reboilers high-performance distillation equip- does not always improve the over- Adding inter-condensers and/or ment implementation, are described. all energy efficiency of a distillation inter-reboilers can help improve unit. Excessive feed temperature overall energy efficiency. Strategies for improving the increments can cause a significant Pumparound, one of the inter- distillation energy network amount of flash of heavy key and condenser concepts, has been As continuous distillation requires non-key components at the distilla- widely applied to numerous petro- simultaneous heat input and tion column feed zone. In this case, leum multi-product fractionators. removal (thus requiring significant a higher amount of reflux stream is On the other hand, implementing energy consumption), complex heat necessary to maintain required an intermediate reboiler can reduce integration becomes more common overhead distillate purities. This the main reboiler duty. As the for modern distillation units to augmented reflux ratio thus required temperature of an inter- improve unit energy efficiency. requires a higher boil-up ratio. mediate reboiler is lower than that Since a distillation column’s degree Overall energy efficiency is eventu- of the main reboiler, this strategy of separation and enthalpy balance ally aggravated.1 Therefore, careful may allow heat integration with influence each other, it is critical to review of the feed temperature and other valuable heat sources that are evaluate and optimise the distilla- phase is critical to minimise the not as costly or not fully utilised in tion column and heat exchanger overall energy consumption of the the plant. networks together in order to distillation unit. maximise plant economics. Column operating pressure There are numerous strategies to Feed location Relaxation of the column top oper- improve the energy efficiency of Improper feed location of a distilla- ating pressure decreases the distillation processes, with the tion column can also increase the distillation column’s temperature amount of improvement through reflux/boil-up ratio and energy profile and results in a lower each strategy varied according to consumption. An ideal feed reboiler duty. It has been observed www.eptq.com Revamps 2013 3 The function of the xylene column is to separate the feed mixture to xylene components and heavier C9+ components. This column has two different feed sources. The reformate splitter bottom stream and the toluene column bottom stream (which belongs to the aromatic extraction Reflux ratio unit) are introduced as the xylene column bottom feed stream. The Steep Moderate Flat sensitivity sensitivity zone sensitivity zone zone bottom feed stream is split equally and charged to two different feed trays. The reformate splitter’s Theoretical stage bottom stream is treated at the clay towers to eliminate traced olefin Figure 1 Typical column efficiency vs reflux ratio curve components before charging to the xylene column. Meanwhile, the that numerous commercial distilla- analysis. A typical curve is shown deheptaniser bottom stream (from tion columns have been operated in Figure 1. This curve visualises the xylene isomerisation unit) is with lower operating pressures column efficiency sensitivity and charged as the xylene column top than their original design values. energy-saving gain. The curve can feedstock. This stream is also split However, this strategy is not appli- be categorised by three district and introduced to three different cable to columns operated under an zones: steep, moderate and flat feed trays. atmospheric pressure range. sensitivity.2 The xylene column overhead Column overhead circuit pressure Column efficiency improvement vapour stream is split into three drop and condenser temperature is usually very feasible when the parallel streams. Two vapour approaches both heavily influence reflux ratio falls into the steep streams are utilised as the heat feasibility. In addition, column sensitivity zone and at ratios source of the extract column pressure reduction expands vapour considerably in excess of the mini- reboiler and the raffinate column traffic and pushes the limits of mum reflux ratio. In this scenario, reboiler, respectively. The existing distillation equipment. even the small addition of stages, condensed xylene column overhead or an increase in distillation equip- liquid streams are returned to the Column pressure drop ment efficiency, can enhance overall xylene column receiver. The other Reducing column pressure drop column separation with significant vapour stream is supplying heat to can lower reboiler duty at the same energy reductions. the xylene column overhead steam degree of separation. The amount Improvement gain is diluted in generator, which produces #250 of reboiler duty saving relies on the moderate sensitivity zone. steam. The condensed overhead operating pressure and enthalpy Further detailed feasibility study is liquid stream is also returned to the balance. This strategy is generally necessary through economic analy- xylene column receiver. The over- feasible when the distillation sis. The magnitude of energy head distillate of the xylene column column is operated under vacuum savings is negligible when reflux is sent to the paraxylene recovery pressure range. Meanwhile, pres- ratio variation follows flat motion unit. sure drop improvement does not in the remaining zone. In the xylene column reboiler often provide noticeable energy circuit, the xylene column bottom savings in high-pressure range Case study: unit description reboiler inlet stream is first trans- distillation service. The following is a revamp case ported to the other two distillation study of a xylene mixture separa- column reboilers as heating medi- Column efficiency improvement tion unit that demonstrates ums. After providing heat to these Column efficiency improvement well-thought-out, proven design reboilers, the xylene column bottom can reduce the reflux/boil-up ratio practices and a selection of the streams are combined and intro- at a given degree of separation. correct, high-efficiency distillation duced to the furnace-type xylene This strategy can be delivered by equipment to fulfill the improve- column reboiler. increasing the number of theoreti- ment in energy efficiency. Figure 2 In the paraxylene recovery unit, cal stages and/or enhancing the illustrates the xylene mixture sepa- the xylene components from the efficiency of distillation equipment. ration unit’s configurations under xylene column are separated The feasibility can be gauged by a discussion. This schematic reveals through the adsorption process. dedicated sensitivity analysis. that the original distillation units The pre-separated extract stream Constructing a column efficiency have implemented the full heat from the adsorption process is curve with a reflux ratio is one of integration network for energy- charged to the extract column in the core tools for sensitivity efficient operation. order to separate paraxylene from 4 Revamps 2013 www.eptq.com the desorbent. At the same time, the pre-separated raffinate stream Extract from the adsorption process is column charged to
Details
-
File Typepdf
-
Upload Time-
-
Content LanguagesEnglish
-
Upload UserAnonymous/Not logged-in
-
File Pages7 Page
-
File Size-