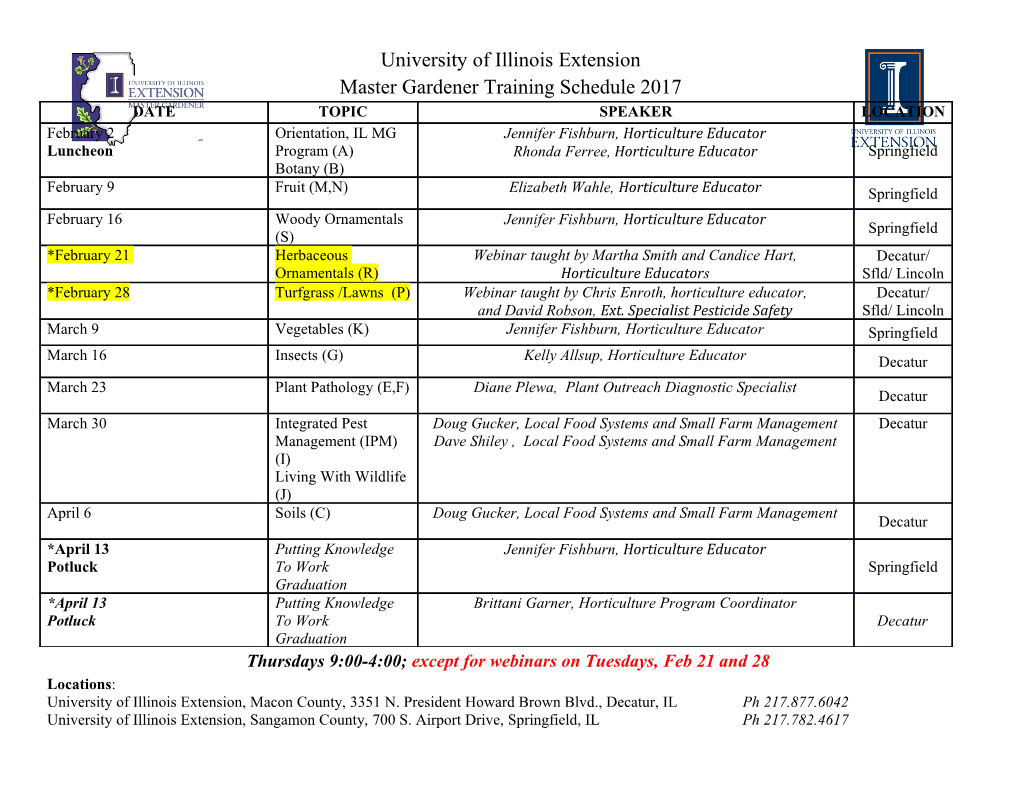
July 23, 1963 A, D, GUSMAN 3,098,235 CLOTHING WITH ADHESIVELY APPLIED BODYING LAYER Filed Dec. 10, 1959 PROR ART INVENTOR. AlAAA7 a 6/SMAM "ey 4. 4.4% A77 oRNEYS 3,098,235 United States Patent Office Patented July 23, 1963 1. 2 In FIGURE 1 there is shown a front fabricated in 3,098,235 CLOTHING WITH ADHESIVELY APPLIED accordance with the prior art. The front 10 comprises BODYNG LAYER a base canvas of haircloth 12 woven generally from Albert D. Gusman, 300 Central Park W., New York, N.Y. horsehair or other animal hair although jute fabrics and Filed Dec. 10, 1959, Ser. No. 858,728 other fabrics have been used. A breast piece 14 is 3 Claims. (C. 2-97) applied to reinforce and to shape the front. Shaping may be effected by darts 16 cut therein which shaping This invention relates to articles of apparel and, more may be brought out by shaping irons. The breast piece particularly, to improved bodying layers for such gar is also usually a woven material. ments and to an improved method of making such layers O The breast piece is then covered with a felt piece 18 and the garments incorporating such layers. to provide padding and body to the suit front and si In the manufacture of articles of apparel, such as multaneously to prevent the hair fibers, such as horse men's and Women's jackets, coats, raincoats and the like, hair fibers, from sticking the wearer of the suit. bodying layers or fronts have been employed to give the Each of the fabrics are held together in the desired outer fabric the desired drape, hand and stylish appear 5 orientation by a plurality of stitches 20 run over the ance. The front known to the art comprises a base entire material. The stitches are usually taken in parallel canvas or haircloth, a breast or chest piece and a felt rows of pikier stitches about a centimeter apart. piece. In addition to the expense of handling the pieces and The base canvas or haircloth is a woven material gen stitching the pieces together, the stitches will usually erally including horsehair or other animal hair for body 20 cause rippling or puckering of the material, particularly and strength. The haircloth is substantially a full lin during use thereof. It has been found impossible to ing material, being cut to the outline dimensions of the ensure that each layer of material and the thread used garment such as a man's jacket. To shape the garment to stitch the layers together have exactly the same shrink and to give the desired resiliency, a smaller chest piece age characteristics which would be necessary to avoid is provided. The chest piece is usually a woven fabric relative shrinkage therebetween. "darted' to the desired shape. The chest piece is at A front constructed in accordance with this invention tached to the haircloth by a plurality of parallel rows is shown in FIGURE 2. of stitching over the entire surface. A felt piece is usu In FIGURE 2 there is shown a front 22 which com ally applied over the chest piece for padding, to impart prises a base canvas or hairpiece 24 and a chest piece a smooth surface to the inside of the front, and to serve 30 26 secured thereto in manner which will be described as a shield preventing the animal hairs in the haircloth in detail in subsequent portions of the specification. from sticking the wearer. The felt piece may be stitched The chest piece is preferably a non-woven fabric formed to the assembled haircloth and breast piece or the three from long-staple, crimped synthetic fibers bonded together fabrics may be stitched together simultaneously. In any in a resilient, porous thin sheet by a latex rubber binder. case, a plurality of parallel rows of Stitching is neces 35 The method of manufacturing such fabric is described sary to prevent relative displacement of the respective in U.S. Patents Nos. 2,719,795, 2,719,802 and 2,719,806. layers during Wear. The non-woven material is both resilient and isoelastic. During fabrication of the front, shaping may be im The resiliency prevents wrinkling and the like. The parted by "darting' the hairpiece and the chest piece. isoelastic properties, that is the property of stretching The desired curves are then brought out by shaping irons. 40 the same amount in response to the same pull despite Such fronts have not been entirely satisfactory. Han the direction of pull, provides support for shaping of the dling of the multiple layers of fabric during stitching garment. The two properties provide the hand, loft or unduly increases the cost of the Suit front. Further, padding properties desired in the finished garment. during the life of the garment, puckering or rippling of The chest piece is bonded to the base canvas at sep the interlining due to variation in shrinkage between the 45 arated discrete points by thermoplastic pellets 28 bonded respective materials forming the front as well as variation to both the chest piece and the base canvas. in shrinkage between each material and the thread used The pellets hold the chest piece in the proper posi for stitching thereof adversely effect the appearance of tion. The separated bonding positions ensure that the the suiting. chest piece supports the base canvas with the resiliency It is therefore an object of this invention to provide of the chest piece fabric. The support between the bond a front which can be assembled without stitching. ing positions is afforded by the isoelastic stretch charac It is a further object of this invention to provide an teristics of the non-woven fabric. The separated bonds improved method of fabricating fronts and the Wearing thus give the front the hand, loft and feel desired. apparel using such fronts. The bonds must be spaced sufficiently closely together It is a further object of this invention to provide a 55 to provide the requisite mechanical strength. However, front which does not require padding such as a felt piece. the closeness of the bond affects the stiffness of the It is a further object of this invention to provide an front. For example, if the layers were bonded over the improved front manufacturable in more economic entire interface, the front would be very stiff and un fashion. suitable for wearing apparel. It has been found prefer It is a still further object of this invention to provide 60 able to distribute the thermoplastic pellets so that ap an improved front including an isoelastic fabric bonded proximately 50 percent of the material surface is bonded. at discrete, separated points. Such distribution provides the requisite bond strength This invention will be more readily understood by reference to the accompanying description and accom without adversely affecting the hand of the material. panying drawings of which: It will be noted that the chest piece can be shaped by FIGURE 1 is a partially sectioned plan view showing 65 darting before bonding of the chest piece to the hair a front constructed in accordance with the prior art. piece. The isoelastic properties of the chest piece allow FIGURE 2 is a partially sectioned plan view of a darting without regard to fabric orientation. The woven front fabricated in accordance with this invention, and chest piece known to the art must be oriented for darting FIGURE 3 is an enlarged perspective view of the since the stretch characteristics vary with the direction material in construction of the front shown in FIG 70 of pull; that is, the woven fabric is more resistant to a URE 2 pull along the warp or Woof than on the cross. 8,098,235 3 4 The method of forming the fabric for the chest piece If the base canvas or hairpiece is a woven material, may best be understood by reference to FIGURE 3. the front is stitched to the outer fabric and lining in con In FIGURE 3 there is shown the fabric 30 composed ventional fashion. I have found that it is often advan of long-staple, highly crimped synthetic fibers, bonded tageous to use the pelletized non-woven material for the together by a binder into a resilient, isoelastic fabric in 5 base "canvas” or "haircloth.” In such cases, after bond the manner described in U.S. Patents Nos. 2,719,795, ing of the chest piece thereto, front is bonded to the outer 2,719,802 and 2,719,806. fabric in the manner outlined above. The material is preferably formed of long-staple, In addition to the elimination of manufacturing steps crimped nylon fibers bonded by latex and formed in a in accordance with the method of this invention, an im sheet between 25 and 75 mill thickness. 10 proved front and article of apparel is produced. The A plurality of thermoplastic pellets 28 are dusted or bond not only eliminates the problem of rippling and salted on one surface thereof. The pellets or pebbles are puckering, but also does not interfere with the "breath formed of thermoplastic material. Polyethylene pebbles ing' attributes of the fabric. Further, the material gives have been found satisfactory. The melt index of the the article of apparel a better hand. thermoplastic pebbles can be adjusted for application in This invention may be variously embodied and modi tended. Materials having a low melt index will fuse at fied within the scope of the subjoined claims. a lower temperature, but the bond cannot be subjected to What is claimed is: high temperatures in use, such as in cleaning and drying 1.
Details
-
File Typepdf
-
Upload Time-
-
Content LanguagesEnglish
-
Upload UserAnonymous/Not logged-in
-
File Pages3 Page
-
File Size-