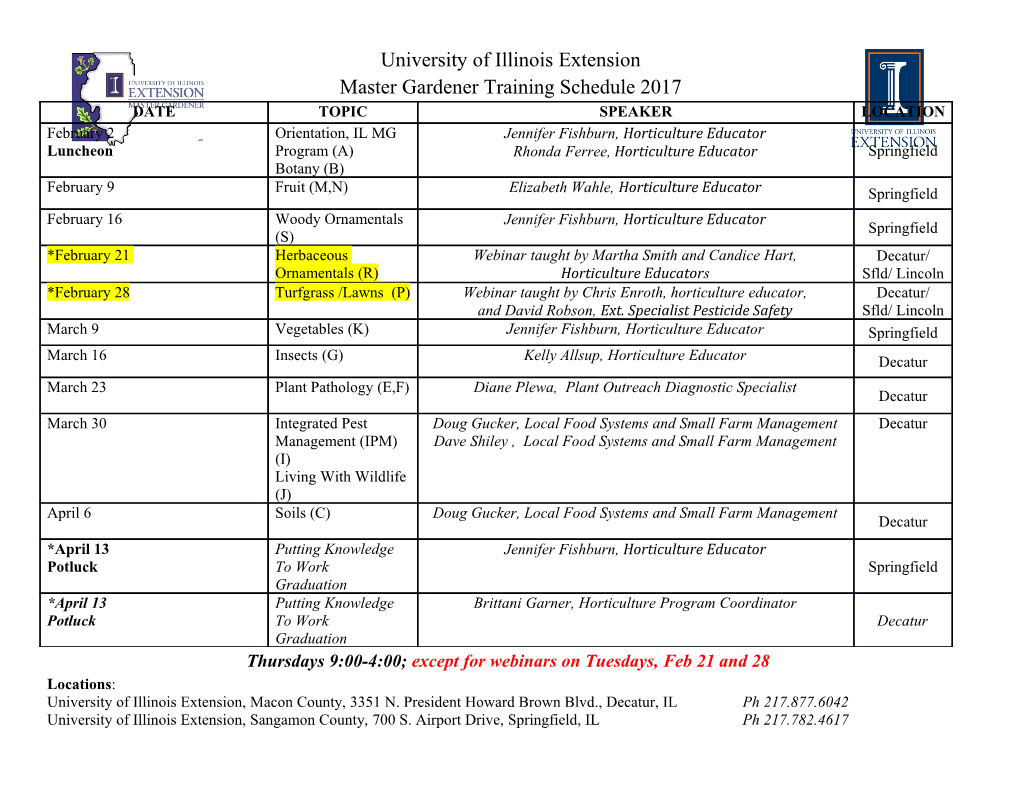
CNC Controller 2.01.02 Copyright © 1995, 1996 Microsystems of Buckhannon Inc. 14 East Lincoln Street, Buckhannon, WV 26201 (304)472-7206 Microsystems of Buckhannon Inc. makes no warranties, either expressed or implied, including any implied warranties of fitness for a specific purpose, for this software. This package is provided solely on an “as is” basis. All risk involved in the use of this software is the responsibility of the purchaser. Program errors, improper software configuration, hardware failures, or other problems can result in damage to the machinery being controlled. Failure of limit switches, cabling, or port components can result in machine movement past limits, potentially damaging the machine and endangering operators. It is imperative that a separate Emergency Stop system be in place which bypasses all computer control. Software features to abort motion from the keyboard and limit switch inputs are provided as conveniences only, and must not be relied upon to stop motion in an emergency. Microsystems of Buckhannon Inc. disclaims all liability for any and all damages, including incidental and consequential damages in connection with use of this software. The sole and exclusive liability of Microsystems of Buckhannon Inc. will be limited to the purchase price of this software package. If you do not understand and agree with these disclaimers, please do not use this product. Return all materials to the place of purchase for a full refund. CNC Controller Contents Installation 1 - 1 Program Operation 2 - 1 Command Reference 3 - 1 System Configuration 4 - 1 Error Codes 5 - 1 CNC Controller Installation CAUTION: DO NOT USE THIS SOFTWARE ON A COMPUTER CONNECTED TO A MACHINE UNLESS THERE IS AN EMERGENCY STOP READILY AVAILABLE WHICH WILL INDEPENDENTLY STOP THE MACHINE. Software features to abort moves from the keyboard and limit switch inputs cannot be relied upon in emergency situations and are provided as conveniences only! Requirements: CNC Controller requires a PC compatible computer with 386 or faster processor, and a hard drive. A 486DX or Pentium is recommended. Make sure your turbo button is on. Slower computers or turbo off will result in abnormal acceleration and other problems. CNC Controller will not run from Windows 3.1. It may be run in MS-DOS mode from a Windows 95 machine. Software Installation: Insert the CNC Controller diskette into th floppy drive and type a:install (or b:install if installing from drive B) The install routine will create the directory c:\cnc if it does not exist and copy the necessary files into it. If there is a previous installation of CNC controller the file cnc2.exe will be overwritten, the cnc2.ini file will not be changed. Plug the software key into one of the printer ports of the computer. Connect the cables from your motor driver to the ports you use. One cable may be connected through the software key. The software will only run in demo mode without the key. Some Terminate and Stay Resident Programs (TSR’s) may interfere with program operation. Specifically other software indexers and print spoolers should not be loaded while using CNC Controller. Check your config.sys file and remove or “rem” any print spoolers or indexer TSR’s. Run the program from the directory you created by going to the CNC directory (cd \cnc) and the typing “run” at the C:\CNC> prompt. If you add C:\CNC to the dos path then CNC Controller may be run from any directory. This can be useful if you want to keep associated part files in their own directory and change to that directory before running CNC Controller. It is also necessary to have the CNC directory in the path to edit files from CNC Controller. If you install CNC Controller into a directory other than C:\CNC then the “dir=” line in CNC2.INI must be changed to the new directory. Program Configuration: CNC2.INI is read on program startup. The default file is setup to work with minimal change for normal installations. To change configuration use a text editor to edit CNC2.INI. If your are running DOS verision 5 or later use EDIT. If you use a word processor to change CNC2.INI make certain that you save as in ascii text format. Example: (using edit) C:\> cd \cnc C:\CNC> edit cnc2.ini After editing type Alt-F Alt-S to save and Alt-F Alt-X to exit Users Guide 1 - 1 CNC Controller Installation CNC.INI Settings: Many CNC.INI settings are similar except for the axis specifier or the port number etc. In this case the reference below will specify the parameter to be changed in <>. For example: <axis>chan would be typed as xchan, ychan, zchan etc. aux<#> would be typed as aux1, aux2, aux3, etc. Axis and Port Settings: CNC.INI Description [Number of Axises] axis=4 set number of axises from 2 to 6 (Level 1 is limited to 4 axis) pulse_12=2 set pulse width for 0x278 port ( Value must be 1,2 or 3) pulse_34=2 set pulse width for 0x378 port pulse_56=2 set pulse width for 0x3BC port stepdiv=4 pulse accuracy - use 4 for 486 and Pentiums - 2 or 0 for slower machines Pulse widths vary with cpu speed. Approximate pulse widths for 486DX-66 are : 1 = 5 microseconds 2 = 10 microseconds 3 = 15 microseconds Set Channels [<axis> Axis] <axis>chan=# # is channel 1 to 6 Each axis is assigned to a port channel. The channel setting assigns default control bits to the axis specified. Allowed axises are X,Y,Z,W,U, and V. Axises must be assigned in order. For example if you have a 3 axis machine X,Y, and Z must be used. Z may not be skipped. Channels 1, 3, and 5 use the lower 4 bits of the port. Channels 2, 4, and 6 use the higher 4 bits. Channels 1 and 2 refer to port 0x278 Channels 3 and 4 refer to port 0x378 Channels 5 and 6 refer to port 0x3BC Set Directions <axis>_dir_pos=0 The default for the direction setting is 1. If an axis moves in the wrong direction, then add this line after the channel setting otherwise leave this line out. Set Resolution <axis>res=#.# Set to the actual resolution in steps/unit. (ie. steps/inch) Users Guide 1 - 2 CNC Controller Installation Limit Switches: The default channel settings will normally provide proper interfacing with the machine’s limit switches. Before atttempting to move the machine verify that all limit switches are functioning properly. Limit switch status is displayed in the position window as “<“ and “>“ around the axis labels. If no limit switches are closed the position display should show only “X”,”Y”,”Z”,”W”. “<“ in front of an axis indicates that the low limit switch for that axis is closed. “>“ after the axis label indicates that the high limit switch is closed. First toggle your limit switches by hand. Verify that the appropriate limit display toggles. If it does not toggle then you need to adjust CNC2.INI. See the CNC2.INI reference section of the manual if the default settings are incorrect for your machine. It is recommended that you verify limit switch operation at the beginning of each operating session. Movement: Do not attempt movement until the limit switches and displays toggle correctly. Once the limits are working try a small move. If nothing moves, the wrong axis moves, or movement is in the wrong direction then adjust CNC2.INI. Perhaps the easiest way to do preliminary testing of movement is with the Jog mode. Push F6 to select Jog .1”. Use the LEFT and RIGHT arrow keys to move X, the UP and DOWN arrows to move Y, the PAGEUP and PAGEDOWN keys to move Z and U, and the HOME and END keys to move W and V. The SCROLL LOCK key toggles between ZW and UV. If the SCROLL LOCK light off Z or W will move. If the light is on U or V will move. Make certain that each axis moves in the proper direction. If it moves the wrong way the limit switch will not stop the motion in the event the limit is hit, possibly resulting in damage to the machine. Abort Cushions lim_step=# Set # to number of steps to compress limits after switch hit esc_step=# Set # to number of steps to move after Escape key pushed Some machines may be damaged if stopped suddenly at higher speeds. Abort cushions provide a method of deceleratiing quickly but not instantly when a limit is hit or the escape button is pushed. lim_step specifies the number of steps to continue after a limit is hit. This number must be calculated from the distance your switches may be compressed without damage and the lowest axis resolution of your machine. For instance if your X and Y resolution are 1018.592, your Z and W resolution are 2000 and your limit switches may be compressed .1” then you would set lim_step as follows: lim_step=1018.592*.1=100 steps esc_step may be set to any value that results in a quick stop without moving to far. 200 is suggested. Users Guide 1 - 3 CNC Controller Installation Initial Velocities: Initial Velocities may be specified separately for the XY, Z, W, U, and V velocities. Note that X and Y velocities are always the same, so only X velocities should be specified. Maximum, Feed, and Rapid Velocities may be specified for each axis. If you specify a maximum velocity then the axis velocity will be limited to that maximum.
Details
-
File Typepdf
-
Upload Time-
-
Content LanguagesEnglish
-
Upload UserAnonymous/Not logged-in
-
File Pages35 Page
-
File Size-