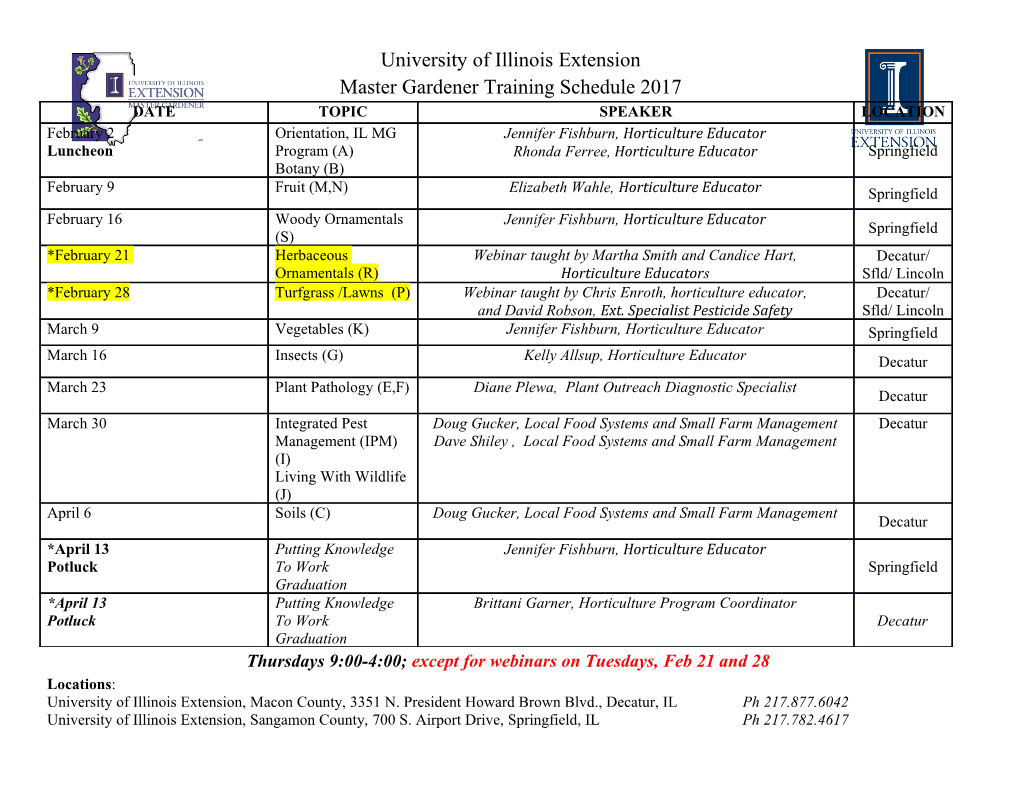
CH0200021 O o hi Q> PAUL SCHERRER INSTITUT PSI Bericht Nr. 02-06 CQ February 2002 5) ISSN 1019-0643 a Nuclear Energy and Safety Division Laboratory for Materials Behaviour Literature Survey on the Stress Corrosion Cracking of Low-Alloy Steels in High-Temperature Water H.P. Seifert Paul Scherrer Institut CH - 5232 Villigen PSI 33/13 Telefon 056 310 21 11 Telefax 056 310 21 99 Literature Survey on the Stress Corrosion Cracking of Low-Alloy Steels in High-Temperature Water H.P. Seifert Nuclear Energy and Safety Division Laboratory for Materials Behaviour Structural Integrity Group Abstract The present report is a summary of a literature survey on the stress corrosion cracking (SCC) behaviour/ mechanisms in low-alloy steels (LAS) in high-temperature water with special emphasis to primary-pressure-boundary components of boiling water reactors (BWR). A brief overview on the current state of knowledge concerning SCC of low-alloy reactor pressure vessel and piping steels under BWR conditions is given. After a short introduction on general aspects of SCC, the main influence parameter and available quantitative literature data concerning SCC of LAS in high-temperature water are discussed on a phenomenological basis followed by a summary of the most popular SCC models for this corrosion system. The BWR operating experience and service cracking incidents are discussed with respect to the existing laboratory data and background knowledge. Finally, the most important open questions and topics for further experimental investigations are outlined. TABLE OF CONTENTS ABSTRACT 2 INDEX 4 0. ABBREVIATIONS 6 1. INTRODUCTION 8 1.1 REPORT OUTLINE 8 1.2 REFERENCES 9 2. GENERAL ASPECTS OF STRESS CORROSION CRACKING 10 2.1 ENVIRONMENTALLY-ASSISTED CRACKING 10 2.2 BASIC ASPECTS AND CHARACTERISTIC FEATURES OF SCC 12 2.3 LABORATORY EAC TEST METHODS AND THEIR RELEVANCE TO LWR COMPONENTS .. 17 3. SCC/SICC OF LOW-ALLOY STEELS IN HIGH-TEMPERATURE WATER 19 3.1 MAIN INFLUENCING FACTORS FOR SCC/SICC 19 3.2 SCC/SICC SUSCEPTIBILITY CONDITIONS 19 3.3. ENVIRONMENTAL PARAMETERS 22 3.4 MECHANICAL/LOADING PARAMETERS 30 3.5 MATERIAL PARAMETERS 32 3.6 INCUBATION PERIOD 36 3.7. QUANTITATIVE SCC/SICC CRACK GROWTH RATE DATA 36 4. MECHANISTICAL ASPECTS OF EAC OF LAS 41 4.1 CRACK GROWTH MECHANISMS 41 4.2 LOCAL CRACK-TIP CHEMISTRY AND MASS TRANSPORT 58 4.3 CRACK-TIP ELECTRO- AND WATER CHEMISTRY IN LAS UNDER LWR CONDITIONS 63 4.4 DISCUSSION OF SOME SPECIFIC ASPECTS OF CRACK CHEMISTRY AND EAC 64 5. LWR OPERATING EXPERIENCE AND EAC CRACKING INCIDENTS 74 5.1 EAC CRACKING INCIDENTS IN LWR 74 5.2 OPERATING EXPERIENCE VS. LABORATORY BACKGROUND KNOWLEDGE 78 5.3 POSSIBLE EAC PREVENTION STRATEGIES AND MITIGATION ACTIONS 81 6. OPEN QUESTIONS AND NEEDS FOR FUTURE WORK 83 6.1 CORROSION FATIGUE/ STRAIN-INDUCED CORROSION CRACKING 83 6.2 STRESS CORROSION CRACKING 85 7. EXTENDED SUMMARY AND CONCLUSIONS 87 8. ACKNOWLEDGEMENT 91 9. REFERENCES 92 INDEX ABSTRACT 2 INDEX 4 0. ABBREVIATIONS 6 1. INTRODUCTION 8 1.1 REPORT OUTLINE 8 1.2 REFERENCES 9 2. GENERAL ASPECTS OF STRESS CORROSION CRACKING 10 2.1 ENVIRONMENTALLY-ASSISTED CRACKING 10 2.1.1 Types of EAC 10 2.1.2 Classical and Non-Classical SCC 10 2.2 BASIC ASPECTS AND CHARACTERISTIC FEATURES OF SCC 12 2.2.1 SCC Fracture Features 13 2.2.2 Crack Initiation vs. Crack Growth 13 2.2.3 SCC Crack Growth Rate vs. Stress Intensity Factor Curves 75 2.3 LABORATORY EAC TEST METHODS AND THEIR RELEVANCE TO LWR COMPONENTS .. 17 3. SCC/SICC OF LOW-ALLOY STEELS IN HIGH-TEMPERATURE WATER.. 19 3.1 MAIN INFLUENCING FACTORS FOR SCC/SICC 19 3.2 SCC/SICC SUSCEPTIBILITY CONDITIONS 19 3.3. ENVIRONMENTAL PARAMETERS 22 3.3.1 Temperature 22 3.3.2 ECP and Oxygen Content 25 3.3.3 Sulphate Concentration of Environment 27 3.3.4 Possible Irradiation Effects on EAC 28 3.4 MECHANICAL/LOADING PARAMETERS 30 3.4.1 Critical Strain-rates and Strains 30 3.4.2 Stress Intensity Factor Threshold for SCC KJSCC 32 3.5 MATERIAL PARAMETERS 32 3.5.1 Steel Sulphur-Content, MnS-Inclusions 32 3.5.2 Yield Strength Rp, Micro structure 34 3.5.3 Dynamic Strain Ageing, Free Nitrogen and Carbon Content in Steel 35 3.6 INCUBATION PERIOD 36 3.7. QUANTITATIVE SCC/SICC CRACK GROWTH RATE DATA 36 3.7.1 SICC Crack Growth Rates 36 3.7.2 SCC Crack Growth Rates andKiscc 37 3.7.3 Possible Reasons for Data Scatter and High SCC Crack Growth Rates 39 4. MECHANISTICAL ASPECTS OF EAC OF LAS 41 4.1 CRACK GROWTH MECHANISMS 41 4.1.1 Film Rupture / Anodic Dissolution Mechanism (FRAD) 41 4.1.2 Hydrogen-Assisted EAC (HAEAC) 46 4.1.2.1 Sources of Hydrogen in LAS under LWR Conditions 46 4.1.2.2 Effects of Hydrogen [see references in 20, 140-144, 160-163] 46 4.1.2.3 General Aspects of HAEAC in Aqueous Environments 47 4.1.2.4 HAEAC Model for LAS under LWR Conditions 49 4.1.2.5 HAEAC vs. FRAD 50 4.1.3 Dynamic Strain Ageing (DSA) 52 4.1.3.1 Background 52 4.1.3.2 Phenomenological and Microscopical Features of DSA 52 4.3.1.3 Physical Metallurgy of DSA 53 4.1.3.5 Possible Interaction between DSA and EAC in LAS 57 4.2 LOCAL CRACK-TIP CHEMISTRY AND MASS TRANSPORT 58 4.2.1 Basic Concepts of Crack Chemistry in Low-Alloy Steels under LWR Conditions 58 4.2.2 Differential Aeration Cell at the Crack Mouth 60 4.2.3 Dissolution Cell at the Crack-Tip 60 4.2.4 Mass Transport Process in the Crack Enclave 61 4.2.5 Critical Crack-Tip Sulphur-Anion Concentration for EAC 61 4.3.6 Critical Crack Growth Rate for EAC 62 4.3 CRACK-TIP ELECTRO- AND WATER CHEMISTRY IN LAS UNDER LWR CONDITIONS 63 4.3.1 Crack-Tip ECP 63 4.3.2 Crack-Tip pH and Crack-Tip Sulphur-Anion Concentration 63 4.3.3 Crack-Tip Conductivity 63 4.4 DISCUSSION OF SOME SPECIFIC ASPECTS OF CRACK CHEMISTRY AND EAC 64 4.4.1 ECP and Dissolved Oxygen Content 64 4.4.2 Impurity Content and Conductivity 64 4.4.3 Effect of MnS-Inclusions 65 4.4.4 Asymmetry of Transients and Hysteresis Effects 66 4.4.5 Effect of Flow Rate 69 5. LWR OPERATING EXPERIENCE AND EAC CRACKING INCIDENTS 74 5.1 EAC CRACKING INCIDENTS IN LWR 74 5.1.1 Common Features of EAC Cracking Incidents 74 5.1.2 EAC of BWR RPV Feedwater Nozzles 76 5.1.3 SICC of Thin-Walled Pipings in German BWR 77 5.2 OPERATING EXPERIENCE VS. LABORATORY BACKGROUND KNOWLEDGE 78 5.2.1 Reasons for Higher EAC Cracking Frequency in Laboratory Tests 79 5.2.2 Reasons for High SCC Cracking Susceptibility in Some Lab Tests 80 5.2.3 Summary 80 5.3 POSSIBLE EAC PREVENTION STRATEGIES AND MITIGATION ACTIONS 81 5.3.1 Critical Components 82 5.3.2 Mitigation Actions 82 6. OPEN QUESTIONS AND NEEDS FOR FUTURE WORK 83 6.1 CORROSION FATIGUE/ STRAIN-INDUCED CORROSION CRACKING 83 6.2 STRESS CORROSION CRACKING 85 7. EXTENDED SUMMARY AND CONCLUSIONS 87 8. ACKNOWLEDGEMENT 91 9. REFERENCES 92 0. Abbreviations ASME American Society of Mechanical Engineers ASME BPV ASME Boiler and Pressure Vessel Code ASTM American Society of Testing and Materials ASTME399 Test Method for Plane-Strain Fracture Toughness of Metallic Materials BWR Boiling Water Reactor BWR VIP Boiling Water Reactor Vessel and Internals Project C(T) Compact Tension Specimen CERT Constant Extension Rate Test CF Corrosion Fatigue CGR Crack Growth Rate CODLL Crack Opening Displacement at Load Line DCPD Direct Current Potential Drop Method DO Dissolved Oxygen DSA Dynamic Strain Ageing EAC Environmentally-Assisted Cracking ECP Electrochemical Corrosion Potential EPFM Elastic-Plastic Fracture Mechanics EPRI Electric Power Research Institute FRAD Firm Rupture/Anodic Dissolution Mechanism FW Feed Water GÈ General Electric HAEAC Hydrogen-Assisted EAC Mechanism HAZ Heat-Affected Zone HSK Hauptabteilung für die Sicherheit der Kernanlagen HWC Hydrogen Water Chemistry International Co-operative Group of Environmentally-Assisted Cracking ICG-EAC of LWR Materials IGSCC Intergranular SCC KrThreshold for SCC KTA Kerntechnischer Ausschuss, Germany LAS Low-Alloy Steel LCF Low-Cycle Fatigue LEFM Linear-Elastic Fracture Mechanics LFCF Low-Frequency Corrosion Fatigue LWR Light Water Reactor LWV Labor fur Werkstoffverhalten MPA Staatliche Materialprufungsanstalt, University of Stuttgart, Germany NDT Non-Destructive Testing NRC National Regulatory Commission, USA NWC Normal Water Chemistry PEER Panel of Experts for Evaluation and Review PWHT Post-Weld Heat Treatment PWR Pressurized Water Reactor QA Quality Assurance RPV Reactor Pressure Vessel SCC Stress Corrosion Cracking SEM Scanning Electron Microscopy SHE Standard-Hydrogen-Electrode SICC Strain-Induced Corrosion Cracking SRL Slow Rising Load Test SS Stainless Steel SSRT Slow Strain Rate Test SSY Small Scale Yielding TGSCC Transgranular SCC UTS Ultimate Tensile Strength VGB Technische Vereinigung der Grosskraftwerksbetreiber, Deutschland YS Yield Strength 1. Introduction The reactor pressure vessel (RPV) of both boiling water (BWR) and pressurized water reactors (PWR) is the most critical pressure-boundary component as far as safety and plant life are concerned [1.1, 1.2]. The high standards of safety and reliability on this pressure- boundary component in light water rectors (LWR) require that all potential relevant ageing and degradation mechanism affecting structural integrity are sufficiently understood so that even low probability failures can be ruled out by adequate (counter)measures. RPV structural integrity continues therefore to be a key concern within the context of both reactor safety and evaluation/extension of plant service life.
Details
-
File Typepdf
-
Upload Time-
-
Content LanguagesEnglish
-
Upload UserAnonymous/Not logged-in
-
File Pages107 Page
-
File Size-