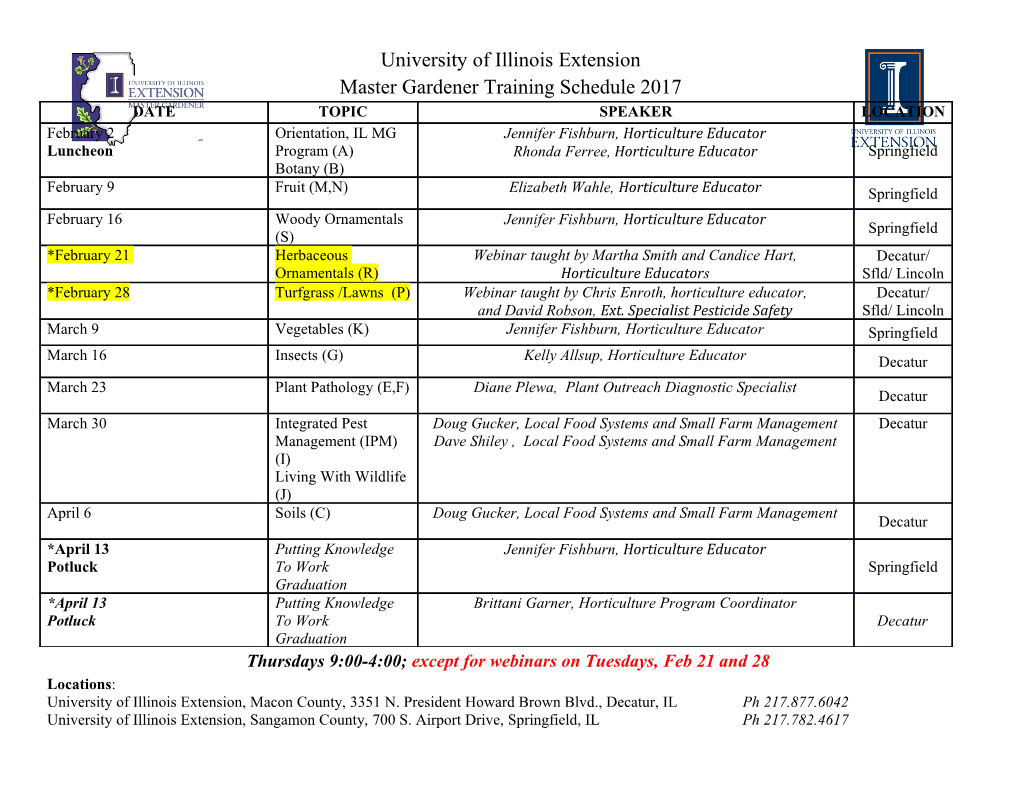
UHTCs: Ultra-High Temperature Ceramic Materials for Extreme Environment Applications by E. Wuchina, E. Opila, M. Opeka, W. Fahrenholtz, and I. Talmy .That’s not just hot SiO(g) instead of a protective SiO2 layer) 3000°C..– it’s EXTREMELY can occur at very high temperatures hot. It is above the melting or (> 1350°C, depending on PO2) and decomposition temperatures for most reduced system pressures. In addition, of the materials known to man. But decomposition of already-formed SiO2, in the world of extreme environment or the interface reaction between SiC engineering, it is just a baseline. The list and SiO2 results in SiO(g) formation at of materials with melting temperatures high temperatures and reduced pressure above 3000°C is limited to perhaps 15 environments. Other materials, such as elements or compounds (Table I). That TiB2, TiC, NbB2, NbC, while having high is a pretty small palette of materials to melting temperatures, form oxides with draw from for an engineer or designer. low melting points (TiO2 – Tm = 1840°C and Nb2O5 – Tm = 1485°C). Graphite has Table I. Materials with melting temperatures the highest melting temperature of any above 3000°C. material known, but starts to burn Carbon TaB Re thet 800°C. While it is a most widely 2 used material in high-temperature W HfC BN applications, it must be protected by HfB HfN ZrC coatings for long-term use. 2 What we are left with are the borides, TaC ZrB2 TiC carbides, and nitrides of the Group IV & V elements, as well as mixtures based on TaN NbC ThO 2 these compounds. While these materials of interest have been known since the Since the late 1960s, the world 1930s, it wasn’t until the seminal works of high-temperature materials has sponsored by the U.S. Air Force6 as focused primarily on SiC and Si N 3 4 well as the work of Samsonov7 in the as the materials of choice. Entire 1960s that the class of UHTC materials industries have developed to produce became more widely known. As the ball bearings, armor, fibers, and even ZrB and HfB -based UHTCs are the turbine blades. But recently, there has 2 2 most widely studied of these materials been a revival of sorts in materials due to their good oxidation resistance originally studied in the 1960s for FIG. 1. Conceptualized drawings of hypersonic from room temperature to over 2000°C, potential aerospace applications, driven 1 2 vehicle and missile as potential applications we will start by discussing them. by “the need for speed”—with new for UHTC leading edge and nozzle components. propulsion and hypersonics concepts as shown in Fig. 1. Current increasing Borides interest in hypersonic vehicles and thermal expansion, density, fabric- weapons points to the need for new ability, and cost are also important It is well known that Zr and Hf are ultra-high-temperature materials for factors in determining the optimal very chemically similar elements, with wing leading edges and nosetips, as material for a given application. their primary differences being density well as propulsion system components. For the purposes of this paper, we and nuclear capture cross section, so it is There are more than 300 materials will simply define UHTC materials by not surprising that the borides of these with melting temperatures over their usefulness in a real structural elements are also very similar. Both exist 2000°C, including the aforementioned (load-bearing) application where the in hexagonal crystal structures of the very high temperatures are generated SiC, refractory metals (Hf, Nb, AlB2 prototype, with layers of B atoms Ir, Re, Ta, W), oxides (HfO , ZrO , rapidly by burning fuels or friction in 2D graphite-like rings, alternating 2 2 with the atmosphere (not steady state). UO2, ThO2), a variety of transition with Zr or Hf layers in a hexagonally metal carbides, nitrides, and borides This will quickly eliminate most of close-packed array. Because of the very as well as other compounds. For real the materials mentioned above. While high strengths of the B-B rings and M-B engineering applications, though, oxides are reasonable to consider for bonds, these materials have very high melting temperature is only one of use in oxidizing environments, poor hardness and temperature stability. many of properties used in the materials thermal shock resistance due to high While most extrinsic properties such as selection process.3 As most engine and thermal expansion and low thermal strength are dependent on processing hypersonic leading edge applications conductivity eliminates them from and microstructure, the intrinsic will involve exposure to oxidizing further discussion. The silicon based thermal conductivities of the diborides fuels or aeroheating, all nonoxide refractory compounds (SiC, Si3N4, are very high, approaching copper at materials will undergo oxidation to MoSi2, etc.) possess excellent oxidation room temperature, with little dropoff resistance up to 1700°C due to the form some combination of solid, liquid, up to 2500°C. This makes ZrB2 and HfB2 or gaseous reaction product. It is the formation of a layer of SiO2 glass that very appealing for applications where oxidation behavior that is a second inhibits oxygen diffusion to the parent thermal stress response is an important 4 primary property associated with the material. This is the primary reason for issue. A good example of this is rocket materials selection process. Strength the popularity of these materials for a motor nozzles. In these applications, the (room temperature and at application wide variety of applications. However, temperature rise on the inside surface temperature), thermal conductivity, active oxidation (the direct formation of can approach 2000°C in less than 0.15 30 The Electrochemical Society Interface • Winter 2007 FIG. 2. Finite element modeling results showing the peak tensile stresses generated in rocket motor nozzles during the early stages of firing.8 seconds, while the outer wall is still at processing and microstructure (as well Cougherty, et al.,9 in the 1960s as a room temperature. This ∆T generates a as test methods used to measure the grain refiner to improve its strength. compressive stress on the inside (hot) property). It is not surprising, then, More recent second phase additions surface, while the outside (cool) surface that the strength values reported in the include carbides and silicides. While carries a tensile stress. Depending literature have a wide range. Because these additions also influence the on the thickness of the nozzle, the ZrB2 and HfB2 are hexagonal crystals, the strength of the diboride ceramics, the thermal conductivity and strength will properties exhibit anisotropic behavior primary interest of research on ZrB2 determine the success or failure of the within individual crystals. However, and HfB2 has primarily focused on part. A finite element model of thick the bulk data reported are traditionally improving their oxidation resistance. and thin-walled cross-section (Fig. 2) gathered from polycrystalline ceramics, The presence of a silica-forming shows the highest tensile loads in red.8 and therefore do not show anisotropic species in the diborides greatly With higher thermal conductivity, the behavior. As is common in ceramic increased their oxidation resistance borides can more readily transmit the systems, the strength of the diborides due to the in-situ formation of a heat through the part and equilibrate is generally shown to increase with borosilicate glass on the surface of the temperature within the cross- decreasing grain size according to the the material, which impeded oxygen section, thereby reducing the thermal Hall-Petch relationship. The influence diffusion to the parent material. It was stress. of second-phase additions has also been found that an optimal composition of As mentioned previously, the reported. Silicon carbide was originally ZrB2 plus 20 to 30 vol% SiC, produced strength of materials is dependent on incorporated into HfB2 and ZrB2 by the highest oxidation resistance up to 2000°C.10,11 Pure diborides form liquid B2O3 during oxidation that can be protective up to around 1200°C, but the B2O3 evaporates at higher temperatures and no longer provides a diffusion barrier. The addition of the SiO2- forming species helps increase the oxidation resistance by “tieing- up” the boria by the formation of a borosilicate glass that can be stable up to at least 1600°C. A cross-section of a ZrB2-SiC material oxidized at 1627°C for ten 10-minute cycles in air is shown in Fig. 3.12 Efforts to model this oxidation behavior and the complex porous ZrO2-glass scale are FIG. 3. Scanning electron micrograph and composition profile of a cross session of ZrB2-SiC material after ten 10-minute being undertaken cycles at 1627°C in air.12 by a variety of The Electrochemical Society Interface • Winter 2007 31 Wuchina, et al. (continued from previous page) 14 FIG. 4. Scanning electron micrographs of top surface of ZrB2-SiC modified with TaB2 oxidized at 1300°C in air. researchers13 and will hopefully lead glasses during oxidation to further been in the form of powder-processed to further improvements in oxidation reduce the oxygen diffusion rates materials. Most boride powders have resistance. Hypersonic aerosurfaces will through the glass. An example of the been synthesized by reduction, chemical need to have lifetimes on the order immiscible glass microstructure and or reactive processes. Carbothermal of hundreds to thousands of hours a thermogravimetric oxidation curve reduction of ZrO2 + B2O3 is the most to become cost-effective
Details
-
File Typepdf
-
Upload Time-
-
Content LanguagesEnglish
-
Upload UserAnonymous/Not logged-in
-
File Pages7 Page
-
File Size-