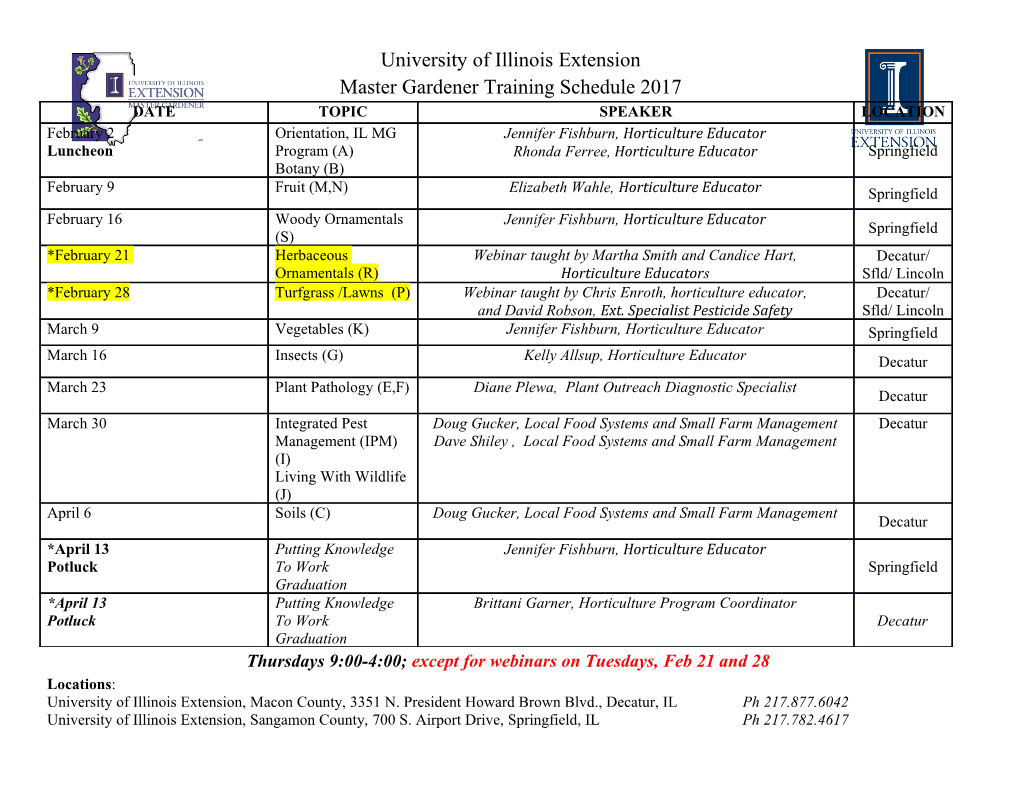
DG_2103_PL39_2104_160011 ICL88xx flyback design guide For high power factor flyback converter with constant voltage output About this document Scope and purpose The ICL88xx family of single-stage power factor correction (PFC)/flyback controllers for constant voltage (CV) output is tailored to meet LED lighting regulatory requirements and satisfy LED lighting applications, including LED drivers with dim-to-off requirements. This document is a design guide to using ICL88xx as a single-stage PFC flyback converter at 41.6 W. It has features such as low standby power consumption (ICL8810 and ICL8820) and outstanding PFC and low total harmonic distortion (THD) at full load as well as at low load conditions. The PWM jitter feature (ICL8820) allows for ease of EMI compliance, and reduces the size, count and cost of external components for emergency lighting application in DC operation. The evaluation board regulates a CV output, and is intended to be used with a constant current (CC) converter for LED lighting applications. The design guide takes the reader step by step through the design process of high power factor (HPF) flyback converters and explains each step using a 52 V/41.6 W converter as an example. Intended audience This design guide is intended for power supply design engineers and field application engineers. Table of contents About this document ....................................................................................................................... 1 Table of contents ............................................................................................................................ 1 1 Introduction .......................................................................................................................... 3 1.1 Pin configuration and description .......................................................................................................... 4 1.2 Design process ......................................................................................................................................... 5 2 Design specifications .............................................................................................................. 6 2.1 Specification of a 41.6 W PFC flyback reference design for LED lighting applications ......................... 6 3 PFC flyback converter design .................................................................................................. 7 3.1 Transformer design ................................................................................................................................. 8 3.2 Flyback MOSFET and secondary main output diode selection ........................................................... 17 3.3 Output capacitor ................................................................................................................................... 21 3.4 MOSFET snubber design ....................................................................................................................... 22 3.5 CS resistor and GD pin-related design .................................................................................................. 27 3.6 VIN pin-related design ........................................................................................................................... 28 3.7 On-time adjustment .............................................................................................................................. 34 3.8 VCC capacitance and output UVP design ............................................................................................... 37 4 THD optimization .................................................................................................................. 42 4.1 Output OVP-related design ................................................................................................................... 44 5 Secondary-side regulation feedback circuit design ................................................................... 47 6 PCB layout guide ................................................................................................................... 53 Design Guide Please read the Important Notice and Warnings at the end of this document V 1.1 www.infineon.com/icl88 page 1 of 64 2021-09-20 ICL88xx flyback design guide For high power factor flyback converter with constant voltage output 7 Tips and tricks ...................................................................................................................... 55 8 Debugging guide ................................................................................................................... 56 9 ICL8800 operation flow chart .................................................................................................. 57 10 Protection features ............................................................................................................... 58 10.1 Schematic .............................................................................................................................................. 59 11 References ........................................................................................................................... 62 12 Revision history .................................................................................................................... 63 Design Guide 2 of 64 V 1.1 2021-09-20 ICL88xx flyback design guide For high power factor flyback converter with constant voltage output Introduction 1 Introduction The ICL88xx family is optimized for secondary-side regulated (SSR) HPF flyback converters. The simplified schematic is shown in Figure 1. The ICL88xx family can also be used in a primary-side regulated (PSR) configuration – please visit Infineon to find more information on this topic. RVCC VOUT + L CMC CVCC VOUT- CXa CXb RZCD VCC ZCD N CMC DMC GD ROVP ICL88xx CS VIN VS RVINhigh TD GND CVS RVS RCS VINlow CVIN R RTD Figure 1 ICL88xx flyback converter – simplified circuitry with secondary-side regulated CV output ICL88xx is a quasi-resonant (QR) controller operating in a critical conduction mode (CrCM) at full load and minimum input voltage. The IC will try to stay in CrCM for as long as possible. QR control helps to minimize switching noise and increases efficiency by turning on the main power MOSFET at the lowest possible drain- source voltage during transformer demagnetization. The IC regulates the CV output, according to its feedback (FB) pin current signal, which is controlled by the secondary-side regulation FB circuit via an optocoupler. For LED lighting applications, the ICL88xx flyback CV output is usually converted to a CC output by a second- stage DC-DC converter, which is either a switching or linear regulator. Design Guide 3 of 64 V 1.1 2021-09-20 ICL88xx flyback design guide For high power factor flyback converter with constant voltage output Introduction 1.1 Pin configuration and description The ICL88xx comes in a PG-DSO-8 package with eight pins. The main functions of each pin are shown in Table 1 and Figure 2. Figure 2 Pin-out of ICL88xx Table 1 Pin definitions and functions Name Pin Function ZCD 1 Zero crossing detection Connected to an auxiliary winding via a resistor to detect the zero crossing of the switching current. When the zero crossing is detected, the controller initiates a new switching cycle. The resistor from the ZCD pin to the auxiliary winding is used to set the maximum on-time and therefore tune the output power limit. VS 2 Voltage sense Connected to the feedback circuit. The current drawn out of this pin determines the on- time. A resistor Rvs of 12k is mandatory to set the correct operation point. VIN 3 Input voltage detection Measure the AC or DC input voltage for power limitation, input overvoltage protection (OVP), brown-in (BI) and brown-out (BO). TD 4 THD correction Sets the THD correction using a resistor to GND. The voltage on this pin can be used to control an external start-up circuit. CS 5 MOSFET current sense and output voltage protection Primary-side overcurrent protection (OCP). A series resistance to the shunt resistor is used to tune a secondary OVP for the flyback topology. GD 6 Gate driver PWM gate drive for the main power MOSFET. GND 7 Ground Connected to ground, and represents the ground level of the IC for the supply voltage, gate driver and sense signals. VCC 8 Power supply Supplies the IC. Design Guide 4 of 64 V 1.1 2021-09-20 ICL88xx flyback design guide For high power factor flyback converter with constant voltage output Introduction 1.2 Design process Figure 3 shows the design guide and design step sequence for the ICL88xx family of devices. ICL88xx system Power up system Performance check Create system design and optimization based on system design (If any problem, refer (Refer to section to section 8 for (Refer to section 7 (Refer to section 6) 3 to 5) debugging guide) for tips and tricks) Figure 3 ICL88xx design guide document outline for each step of the recommended design flow Design Guide 5 of 64 V 1.1 2021-09-20 ICL88xx flyback design guide For high power factor flyback converter with constant voltage output Design specifications 2 Design specifications The ICL88xx PFC flyback converter design guide describes a step-by-step process for creating a 43.2 W CV converter. By following the step-by-step process, an engineer can develop a similar ICL88xx controlled converter with their own target specification. 2.1 Specification of a 41.6 W PFC flyback reference design for LED lighting
Details
-
File Typepdf
-
Upload Time-
-
Content LanguagesEnglish
-
Upload UserAnonymous/Not logged-in
-
File Pages64 Page
-
File Size-