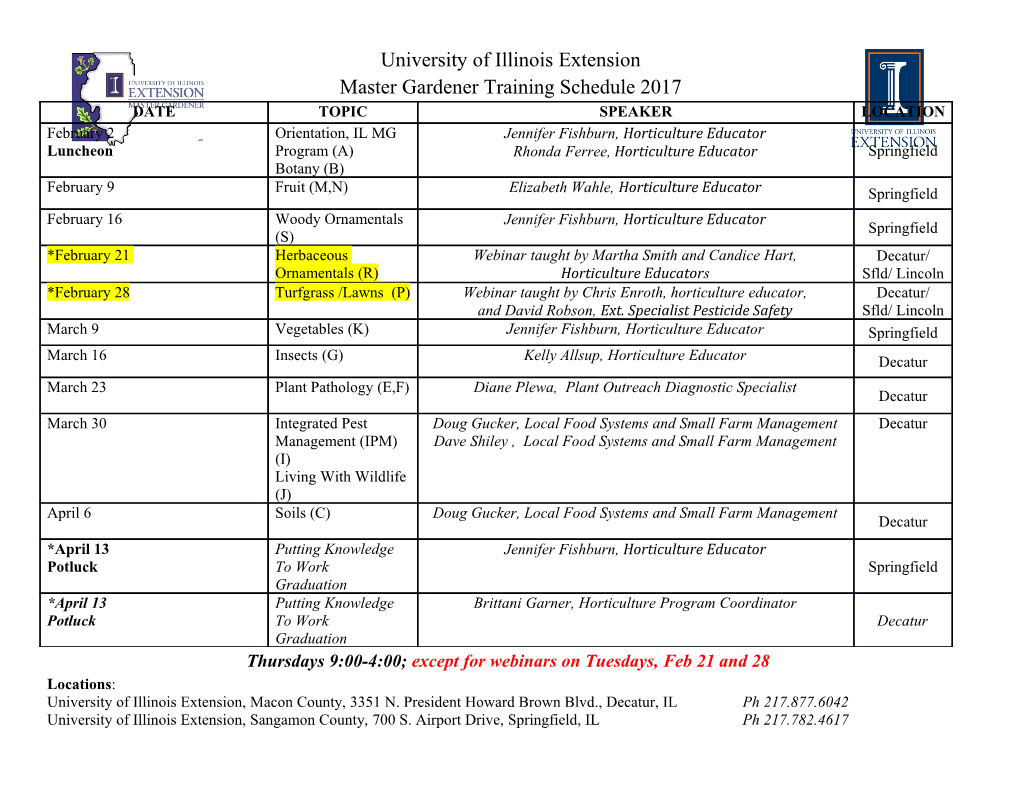
electronics Review A Literature Survey on Open Platform Communications (OPC) Applied to Advanced Industrial Environments Isaías González 1,* , Antonio José Calderón 1 , João Figueiredo 2,3 and João M. C. Sousa 3 1 Department of Electrical Engineering, Electronics and Automation, University of Extremadura, Avenida de Elvas, s/n, 06006 Badajoz, Spain; [email protected] 2 Centre of Mechatronics Engineering—CEM, University of Évora, R. Romão Ramalho, 59, 7000-671 Évora, Portugal; jfi[email protected] 3 IDMEC, Instituto Superior Técnico, Universidade de Lisboa; 1049-001 Lisboa, Portugal; [email protected] * Correspondence: [email protected]; Tel.: +34-924-289-600 Received: 31 March 2019; Accepted: 4 May 2019; Published: 8 May 2019 Abstract: Extensive digitization and interconnection through networks have ushered in a number of new paradigms over the last years: Internet of Things, cyber–physical systems, Industry 4.0, etc. These challenging systems rely on an effective information communication between distributed components. Therefore, the heterogeneity of entities, both hardware and software, must be handled to achieve an operative interoperability and a proper behavior. However, there is also a heterogeneous availability of solutions; different technologies, protocols, and architectures aim to achieve a seamless interconnection. Henceforth, the standardization still requires great efforts from industrial and scientific environments. In this sense, the interface of the open platform communications (OPC) has supported connectivity for automation and supervision infrastructures for more than two decades. The OPC comprises the so-called classic OPC, the original protocol, as well as the last specification, unified architecture (UA). The widespread utilization of the classic OPC together with the powerful functionalities of OPC UA, make the latter one of the main candidates to lead the standardization and systems integration. This paper presents a survey of recent OPC-based systems reported in scientific literature for different domains as well as research projects. The goal of this paper is to provide a broad perspective about the OPC’ applicability and capabilities in order to support the decision about communication interfaces. The results are analyzed and discussed putting special attention on the aforementioned new paradigms. Finally, the main conclusions and open research directions are highlighted. Keywords: industrial communications; OPC UA; classic OPC; SCADA; interoperability; Internet-of-Things; Industry 4.0; automation 1. Introduction Digitization and interconnection through networks are increasingly affecting industries. As the advances in information and communication technologies (ICTs) penetrate the whole chain of processes, the evolution towards new paradigms is unstoppable: Internet of Things (IoT), cyber–physical systems (CPS), Industry 4.0, big data, etc. Namely, CPS combine mechatronics and ICTs to control physical processes and systems, designed as a network of interacting software and hardware components, devices, and systems [1]. This approach applied to production systems is named cyber–physical production systems (CPPS) [2–4] or industrial CPS (ICPS) [5–8]. Electronics 2019, 8, 510; doi:10.3390/electronics8050510 www.mdpi.com/journal/electronics Electronics 2019, 8, 510 2 of 29 Even, the advent of the fourth industrial revolution is being performed by the penetration of information, communication, and control technologies (ICCT) into a networked industrial environment. This revolution is commonly referred to as Industry 4.0; however, such a term is a label similar to the German strategic program called Industrie 4.0 [9]. In addition, there are some initiatives around the world to develop the next-generation of industrial facilities: Nouvelle France Industrielle [10] in France, Connected Industry 4.0 [11] in Spain, China Manufacturing 2025 [12] in China, Smart Manufacturing Leadership Coalition [13] in the US, and the Japanese Robot Revolution Initiative [14] that has agreed to cooperate in the field of IoT/Industry 4.0 with the German initiative. In this context, physical operative technology (OT) and cyber information technology (IT) are integrated in order to seamlessly collaborate. Operative technology is composed of shop floor devices like automation units, sensors and actuators, whereas software management systems like manufacturing execution systems (MES), enterprise resource planning (ERP), and supervisory control and data acquisition systems (SCADA) constitute the IT level. The OT/IT connectivity and interoperability are a challenging task for Industry 4.0 implementation that receives important research efforts [15]. Systems integration requires an enormous effort, especially for large-scale infrastructures. In general, these facilities are complex, vast networked systems that comprise a vast number of devices and applications with different communication protocols. Therefore, data acquisition, exchange, and processing are achieved in a distributed way between heterogeneous data sources and consumers. Cyber–physical systems and IoT are represented by platforms that are integrated through connectivity protocols that permit a wide sharing of information among different devices [16]. In fact, a big challenge in these innovative scenarios is related to the wide heterogeneity of devices, operating systems, platforms, and services [17]. Interoperability is one of the major advantages of Industry 4.0 [18], but proprietary approaches must be replaced by open and standardized communications solutions to make it a successful reality [19,20]. Consequently, standardization is essential for the real development and deployment of these systems. The lack of standards is actually considered a big issue, so research efforts must be performed in the direction of defining standard protocols, languages, and methodologies to enable the full potential of such concepts [17]. There is also heterogeneity referred to the availability of diverse communication protocols devoted to the shop floor like OPC, MTConnect, message queue telemetry transport (MQTT), distributed network protocol (DNP3), as well as modelling information languages, such as the common information model (CIM) or the unified modelling language (UML). Even, for these paradigms, there are numerous conceptual frameworks to perform their orchestration and deployment. For instance, the reference architectural model for Industry 4.0 (RAMI) [21], the industrial internet reference architecture (IIRA) of the industrial internet consortium [22], and many others [7,23–25] that are continuously enriching the possibilities of these approaches. Despite the fact that each one of the available options has pros and cons, such heterogeneity constitutes a significant obstacle for a real standardization and seamless interconnection of the ecosystems. This difficulty must be overcome when facing the design and systems integration of infrastructures under these advanced approaches. The selection of the communication interface to achieve an effective interoperability and heterogeneity management is a transcendental decision that seriously affects aspects such as economic costs, maintainability, expandability, security, and resilience. In this sense, open platform communications (OPC) has proven to be an effective communications middleware mainly in industrial applications. Due to its powerful functionalities, the last specification, called unified architecture (UA), is one of the main candidates to lead the standardization and systems integration for present and future frameworks. Open platform communications is an industrial communication interface also known as open process control, or openness, productivity, collaboration. It has even been termed the network glue for control systems [26]. Open platform communications provides a technology to support interoperability and heterogeneity in control and automation applications, mainly devoted to industrial Electronics 2019, 8, 510 3 of 29 manufacturing. The so-called classic OPC was developed by an industrial automation industry task force in 1996 to provide a communication protocol for personal computer (PC)-based software applications and automation hardware. Currently, OPC comprises ten specifications that are established and managed by the OPC Foundation [27]: Data access (DA), historical data access (HDA), alarms and events (A&E), XML-data access (XML-DA), data exchange (DX), complex data (CD), security, batch, express interface (Xi), and unified architecture (UA). The classic OPC includes the first eight specifications and the OPC DA is the most widely applied. In fact, initially the term OPC corresponded to object linking and embedding (OLE) for process control. It is primarily used to provide real-time access to process control and manufacturing data. One of the main reasons for the rapid diffusion of OPC classic specification was also the most criticized aspect: it was based on Microsoft’s distributed component object model (DCOM), and thus, platform-dependent and not suitable for use in cross-domain scenarios and for the Internet [28]. Classic OPC is nowadays a legacy technology, and hence, is not further developed. Far from being left behind, the last specification, OPC UA, is gaining ever-increasing attention. Developed as the successor to classic OPC, UA specification was released in 2006 and is an IEC international standard of the international electrotechnical commission (IEC), namely, IEC 62541. This new version is intended to provide greater
Details
-
File Typepdf
-
Upload Time-
-
Content LanguagesEnglish
-
Upload UserAnonymous/Not logged-in
-
File Pages29 Page
-
File Size-