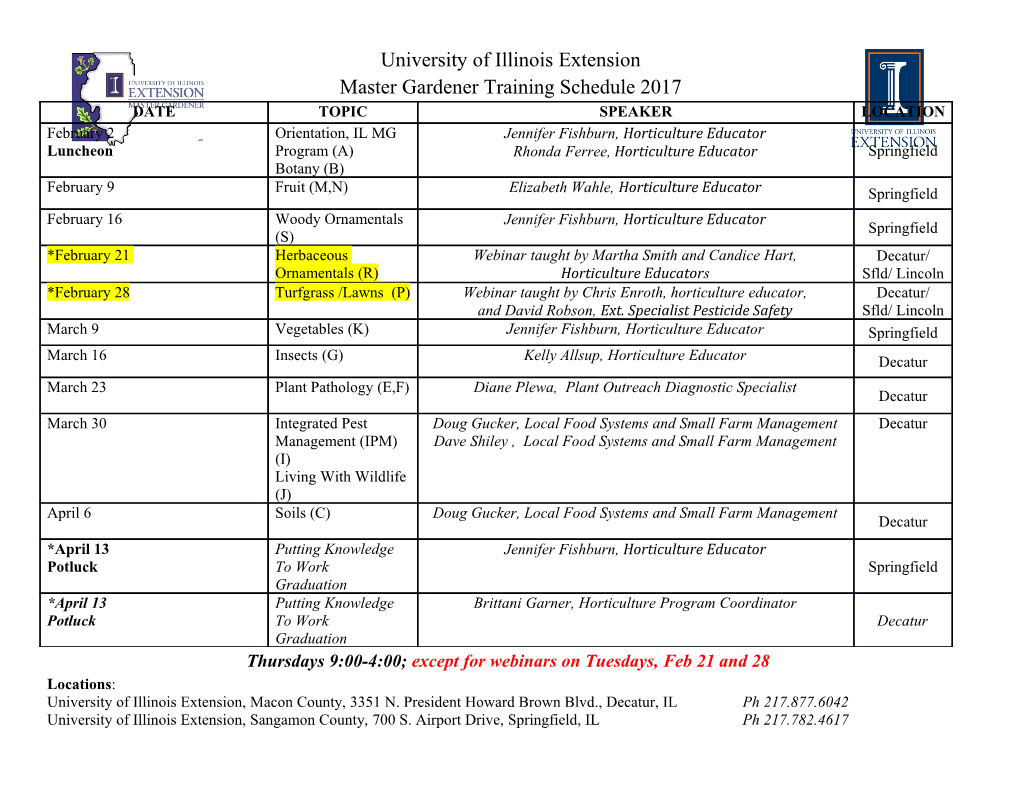
Concepts and Approaches for Mars Exploration (2012) 4353.pdf NOFBX™ MARS ASCENT VEHICLE: A SINGLE STAGE TO ORBIT APPROACH J. M. Vozoff1, D. J. Fisher2, and G. S. Mungas3, 1mv2space, 2Firestar Technologies, 3 Firestar Technologies, 1122 Flight Line Street #76, Mojave, CA 93501, [email protected]. Introduction: Nitrous Oxide Fuel Blend ing TRL 6, having successfully begun testing in a vac- (NOFBX™) is a nitrous-oxide-based mono-propulsion uum test facility. technology developed specifically for a Mars Ascent NOFBX™ technology is more than the propellants Vehicle (MAV) application by Firestar Technologies. themselves: it is also the essential surrounding tech- This development was funded primarily by the NASA nologies that enable this propellant to be safely and Mars Program Office, NASA Small Business Innova- effectively employed to generate thrust in spacecraft tion Research (SBIR), and NASA International Space and rocket propulsion applications. Some examples Station (ISS). NOFBX™ propulsion system specific are flashback arrestor technologies, porous media in- impulse performance equals or exceeds state-of-the-art jectorhead technology, microfluidic regererative thrust nitrogen textroxide/ monomethyl hydrazine chamber technology and the associated thin-film fabri- (NTO/MMH) systems, with the added advantages of cation technique, Firestar’s developments to-date have restartability via spark ignition, deep throttleability demonstrated practical application of the technology (100:1), and high thrust-to-weight ratio. For a Mars [2]. MAV application, NOFBX™ mono-propellant and Some advantages of NOFBX™ technology are engine technology provides a Single State to Orbit listed in the table below. (SSTO) ascent vehicle design option with significant benefits over solid and storable liquid propulsion ap- Characteristic NOFBX™ Advantage proaches, including: 1) the reduced complexity and Monopropellant Less complex, reliable, low mass & cost risk of a liquid monopropellant system compared to bi- Self-pressurizing No pressurant source required prop systems, 2) the reduced complexity and risk of a High Isp Vacuum Isp up to 325 s Higher density than hypergolics – no single stage design over 2-stage systems by eliminating High density Isp thermal control demands the upper stage, the associated interfaces, and stage- Spark-ignited Unlimited restarts related critical events, and 3) lower pre-flight test cost Storable Storage temperature: -70ºC to >+60ºC and risk with the elimination of multiple configura- Deep throttle 100:1, can be throttled down to ~1% tions. NOFBX™ technology also provides operational Cool-running Outer thruster surfaces operate at <150ºC benefits, as the propellant is non-toxic, non- Thrust/Weight 100:1 thrust:weight for Al thrusters contaminating to the planetary environment and stora- Propellant level Remaining prop can be measured to within ble over a very wide range of temperatures (<-70ºC to monitoring 0.1% for the final 15% of load Compatible with most conventional feed >+70ºC). Together these attributes offer the potential Compatibility system hardware components for dramatic simplification to the MSR program archi- Non-toxic Safe and lower cost ground handling and tecture as well as to the MAV itself, increasing mar- constituents transportation – can be mixed on-site gins, eliminating failure modes, improving reliability Non-toxic N2, CO, H2O, H2, CO2. Water is only and decreasing cost. effluents condensable. NOFBX™ Technology: NOFBX™ is a complete- Lower cost Lower cost to manufacture and operate ly non-toxic nitrous-oxide--based monopropulsion Low acoustics Smooth steady combustion – no popping technology (14 patents published or pending in both Liquid, gas, or Can accommodate liquid, gas, and 2- 2-phase phase, reduces unusable propellant U.S. and foreign jurisdictions) offering high perfor- mance (Isp up to ~325 seconds), storability over a NOFBX™ SSTO MAV: In 2001, a NASA and wide temperature range, and lower cost compared to Jet Propulsion Laboratory (JPL) commissioned indus- systems using hydrazine and its derivatives. NOFBX™ try study was performed to look at different MAV sys- propellants were invented by Firestar Technologies tem design options. Several propulsion system options (majority owner of ISPS) between 2003 and 2005 un- were studied including a two stage solid, a liquid der funding from NASA’s Mars Technology Program NTO/MMH bipropellant, and a gelled propellant sys- [1]. Since that time, Firestar has developed and tested tem [3]. These previous MAV studies had not included five different NOFBX™ thruster designs, ranging from NOFBX™ monopropulsion systems as the NOFBX™ 0.45 N (0.1 lbf) to 445 N (100 lbf) thrust. The 445 N monopropulsion systems did not yet exist. The follow- (100 lbf) version, with associated carbon-carbon noz- ing NOFBX™ SSTO MAV design described below is zle, solenoid valve, throttle valve, flashback arrestor, injector head and igniter system, is currently approach- Concepts and Approaches for Mars Exploration (2012) 4353.pdf a new and exciting option for future planetary ascent design and operational requirements vehicles. • Significantly decreased scope, complexity, cost, NOFBX™ SSTO MAV Point Design. Key system and schedule risk of pre-flight testing by avoiding design features for a baseline NOFBX™ monopropul- multiple flight configurations sion, SSTO MAV are summarized below: • Ascent trajectory optimization with restartable and • High performance single stage system capable of deeply throttable propulsion system. delivering a 5 kg Orbiting Sample (OS) into the re- • Storability and operability over a wide temperature quired orbit range. • Three 445 N (100 lbf) regeneratively cooled • Mild human safety toxicity characteristics NOFBX™ thrusters derived from Firestar’s Tech- • Less contaminating to the martian surfaced nology Readiness Level (TRL) 9 NOFBX-100 • Fewer high-risk gimbals and other mechanisms by model using differential throttling of fixed engines to • A 3-cluster engine configuration with pitch and provide vecor control yaw control provided by differentially throttling in- • Greater on-orbit vehicle surface area and internal dividual engines, which eliminates the need for volume. mechanisms and associated complexity • Potential for in situ propellant top-off • Helium-over-liquid as a low complexity, low risk • Mitigation of critical challenges identified by the pressurization approach NASA Mars program (thrust vector control, propel- • Composite Overwrap Pressure Vessel (COPV) lant compability, pre-flight testing, sufficient de- tanks for significant mass reductions velopment lead time). Figure 1 shows a comparison of a resulting Summary: A liquid NOFBX™ monopropulsion NOFBX™ SSTO MAV configuration with the NASA SSTO MAV clearly presents many technical, opera- 2001-2002 2-stage solid rocket MAV. Note the in- tional, and programmatic advantages for the currently creased usable volume and surface area in the held MSR architecture. The point design presented NOFBX™ MAV over the 2-stage solid MAV, which above illustrates the NOFBX™ MAV’s inherent sim- enhances design flexibility. plicity, high performance, and flexibility, all of which Benefits of an NOFBX™ SSTO MAV. The baseline translate to risk mitigation and cost reduction for MSR. NOFBX™ MAV described above affords significant We believe this SSTO ascent engine concept is an ele- advantages over the original 2001 baseline MAV ar- gant, yet legitimate, approach to solving the technical chitecture, including: challenges of designing, testing, and operating the • Inherently simpler overall MAV system design MAV within the constraints of the MSR architecture. • Only one propellant tank required, which increases References: [1] Mungas G. S et al. (2008) JPL the usable volume inside the MAV Technical Report to Subcontract 1265181. [2] Mungas • Eliminates upper stage, which greatly simplifies G. S. et al. (2010) JANNAF, May 2010 [3] Stephenson, D. D. (2002) 38th AIAA/ASME/SAE/ ASEE Joint Propulsion Conference & Exhibit, July 7- 10. Figure 1. Left – NASA 2001-2002 two stage solid rocket MAV baseline. Center – average size person for scale. Right – NOFBX™ SSTO MAV .
Details
-
File Typepdf
-
Upload Time-
-
Content LanguagesEnglish
-
Upload UserAnonymous/Not logged-in
-
File Pages2 Page
-
File Size-