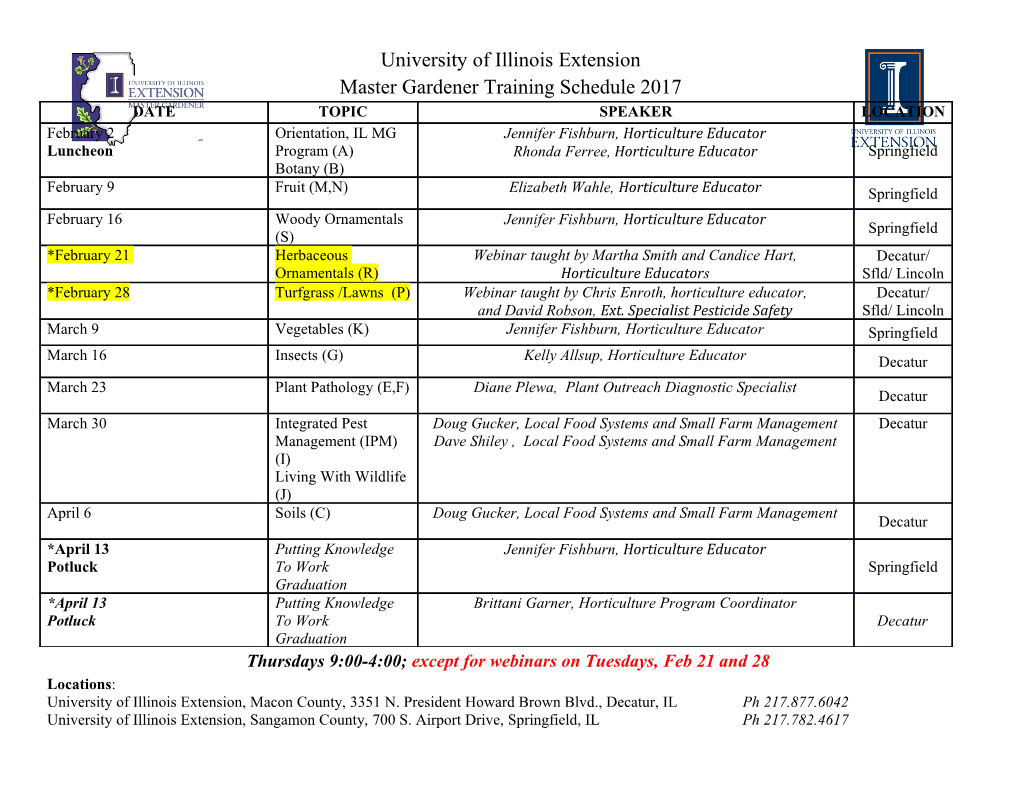
Journal of International Scientific Publications: Materials, Methods & Technologies, Volume 5, Part 1 ISSN 1313-2539, Published at: http://www.science-journals.eu SUPERHARD MATERIALS BASED ON THE DENSE FORMS OF CUBIC BORON NITRIDE (cBN). PROPERTIES AND APPLICATION AREAS Alexander A. Antanovich, Vitalii P. Modenov, Georgii N. Stepanov and Vladimir P. Filonenko Russian Academy of Sciences, Institute for High Pressure Physics, 142190 Troitsk, Russia Abstract A method for the production o f samples of cBN-bctsed superhard materials by a directional infiltration o f a cBN micropowder mixture with aluminum at high pressures and temperatures has been proposed. Some physical-mechanical properties and applications o f obtained materials are described. Key words:superhard materials, cubic boron nitride, high-pressure device, Bridgman anvils, metal­ working 1. INTRODUCTION Cubic boron nitride (cBN)-based polycrystalline superhard materials, having strength properties comparable to those of diamond composites, are superior to diamond composites in temperature and chemical stability. Over time since the synthesis of cBN micropowders became commercialized, a fairly wide range of cBN micropowder-based superhard materials has been developed. It should be stressed that when sintering the cBN micropowders, high pressures are necessarily used to prevent a reverse phase transition of the micropowders from a diamond-like to soft graphite-like structure. A successful sintering of cBN powders without activating additives can be performed at pressures of no less than 7.0 FHa. Therefore the sizes of the compacts produced in the above way cannot be large due to limited dimensions of the working volumes of high pressure apparatus capable of generating such high pressures. A maximum diameter of compacts in this case does not exceed 6-7 mm. A thermobaric sintering with the activating additives allows using lower pressures of 5.0-6.0 GPa. These pressures are used by world leading companies (Element six, SECO and others) for an activated sintering of cBN micropowders in the shape of plates on a hard alloy substrate. These plates are of a fairly large size but their working layer thickness amounts to 0.5-0.7 mm. To reduce the thermobaric parameters of the production of composites based on dense modifications of boron nitride, one can quite efficiently use various metals (titanium, zircon, chromium, cobalt, copper) or their alloys. The low melting temperature of aluminum (660 °C), as well as high physical and mechanical properties of ceramics, resulting from a chemical interaction between aluminum and boron nitride (AIN, A1B2 h A1B12) and ensuring strong binding of cBN grains, make aluminum a technologically advantageous activating additive. Thus, for example, superhard material Kiborit [1], fabricated as plates of 7.0 mm in diameter and 3,18 mm in height, is obtained by reaction sintering of a cBN powder (up to 98%) with aluminum. In this case, as well as in many others, the A1 and cBN powders are initially premixed to prepare a reaction mixture which is then subjected to reaction sintering under high pressures and temperatures. Heterogeneity of reagent mixture in this case may cause inhomogeneity of the structure and deterioration of the physical and mechanical properties of a sintered composite. That is why in our work we use a method of directional infiltration of the cBN powder with aluminum with subsequent reaction sintering. I l l Publishing by Info Invest, Bulgaria, www.sciencebg.net Journal of International Scientific Publications: Materials, Methods & Technologies, Volume 5, Part 1 ISSN 1313-2539, Published at: http://www.science-journals.eu 2. APPARATUS AND SINTERING TECHNIQUE For the sintering of large-size samples of superhard composites, we used a high pressure apparatrus of a “chechevitsa” type [2], developed in the 1960s in the Institute for High Pressure Physics of the Russian Academy of Sciences. A photo of the half of this apparatus of 32 mm in the tapered cavity diameter with a fdled container and a sectional drawing of a fdled container are presented in Fig. 1. r r r ^ r T T Fig. 1 (a) High pressure apparatus “chechevitsa'’, (b) Sectional drawing of a filled container: (1) lithographic stone container, (2) end heater pressed from the mixture of hexagonal boron nitride (hBN) and graphite powders, (3) graphite busing-heater, (4) aluminum washer, (5) cBN powder or mixture of cBN powders, (6) cap pressed from the mixture of hBN and graphite powders The high pressure apparatus was preliminary pressure calibrated (by fixing the phase transitions of bismuth) and temperature calibrated (by using a chromel-alumel thermocouple inserted into the central part of the container). Then the apparatus was placed into a hydraulic press of up to 500 ton press- force, which enabled creating a 2.5 - 3,0 GPa pressure in the working volume of the container. To attain a maximum density of a superhard material, two compositions of mixtures of cBN powders of different graininess were designed: (1) 14/10 pm (80%), 3/2 pm (15%), 3/0 pm (5%) and (2) 5/3 pm (80%), 3/0 pm (20%). It was experimentally found that if filling the container as above and using the above compositions of a cBN powder mixture, the complete infiltration of the powders with aluminum occurs at temperatures of 1100-1200 °C. In actual practice, the sintering process goes like this. Using a hydraulic press, we create the working pressure in the container. Then, using a transformer, we set the experimentally predetermined working voltage to achieve a required sintering temperature. Then the current is turned on for a certain period of time; the current is then switched off. The infiltration of the cBN powders with aluminum lasts about 5 seconds, which is followed by the reaction sintering resulting in the formation of aluminum nitride AIN and aluminum diboride A1B2. By varying the hold time of the sintering process at maximum power, one can obtain both conducting and non-conducting 12 I Publishing by Info Invest, Bulgaria, www.sciencebg.net Journal of International Scientific Publications: Materials, Methods & Technologies, Volume 5, Part 1 ISSN 1313-2539, Published at: http://www.science-journals.eu ceramics, which significantly expands the application area of said ceramics. Fig.2 shows diffraction patterns of two samples of composite ceramics sintered with different hold times. 1 - AIN 0 - AIB _0 2 6 oI— o X mx o X 2a CD\- X 20 25 30 35 40 45 50 55 60 65 7 0 7 5 80 26 Fig.2 Diffraction patterns of two samples of composite ceramics (1) Hold time of 30 seconds at maximum power ((la) from the infiltration side, (16) the opposite side), (2) Hold time of 10 seconds at maximum power ((2a) from the infiltration side, (26) the opposite side) The main phase, cubic boron nitride, fills 82-88% of the volume of ceramics. Aluminum nitride (AIN) and aluminum diboride (A1B2), formed from the reaction between A1 and cBN, are a binder phase in this composition. The binder phase is considerably softer than the main phase, which imparts some plasticity to superhard ceramics. The hardness of AIN and A1B2 is 12.5 GPa and 10 GPa, respectively; the hardness of cBN is 60-80 GPa. A rough quantitative composition of the phases of a sintered superhard material (%), estimated from the peak intensity, is given in Table 1. Table 1 Phase Sam]pie 1 Sampie 2 Bottom Top Bottom Top cBN 82 86 86 88 AIN 15 6 6 3 AlBo 3 3 4 A1 _ 5 4 7 gBN - - - 2 13 I Publishing by Info Invest, Bulgaria, www.sciencebg.net Journal of International Scientific Publications: Materials, Methods & Technologies, Volume 5, Part 1 ISSN 1313-2539, Published at: http://www.science-journals.eu As is seen from the Table, Sample 1 is not conductive because there is no metal phase on its bottom surface, while Sample 2 is a conductor; its resistivity measured by the van der Pauw technique amounts to 10"4 ohm-cm. 3. SOME PROPERTIES OF THE MATERIAL The high pressure apparatus described above enables sintering large-sized samples of a superhard material of 15-20 mm in diameter (with the respective heater diameter) and 6-8 mm in height. Fig.3 presents an external view of some of the samples and items made from these samples. 0,1 o 1 2 3 4 Fig.3 Measurements of physical and mechanical properties were conducted on many of the sintered samples. The following properties were measured. Density (p) of the samples was determined by the hydrostatic weighing technique [3] based on Archimedes' law. Elastic moduli (the Young modulus E, shear modulus G and bulk modulus K) were calculated using the known formulae [4] from the experimental data on the propagation velocity of ultrasound waves in the samples and from the density of the material. To measure the ultrasound velocity, the end surfaces of the samples were grinded and the deviation from the plane parallelism did not exceed 5 pm. Strength characteristics were measured using the Instron setup with the recording of the force- deformation diagram, which permitted high accuracy registration of the load at the moment of failure. To carry out the measurements, samples with a rectangular cross-section were cut from a sintered ceramic half-finished product, which was followed by the grinding of the side and end surfaces of the cut samples. The samples for compression strength testing with the sides of 2-3 mm cross-section had the ratio of the height to the side of the cross-section of the order of 2. The samples for bending 14 I Publishing by Info Invest, Bulgaria, www.sciencebg.net Journal of International Scientific Publications: Materials, Methods & Technologies, Volume 5, Part 1 ISSN 1313-2539, Published at: http://www.science-journals.eu strength testing with the length of 14 mm and cross-section ~ 2x3 mm were tested in a device having a 10 mm distance between the supports with the load applied in the center of the sample.
Details
-
File Typepdf
-
Upload Time-
-
Content LanguagesEnglish
-
Upload UserAnonymous/Not logged-in
-
File Pages8 Page
-
File Size-