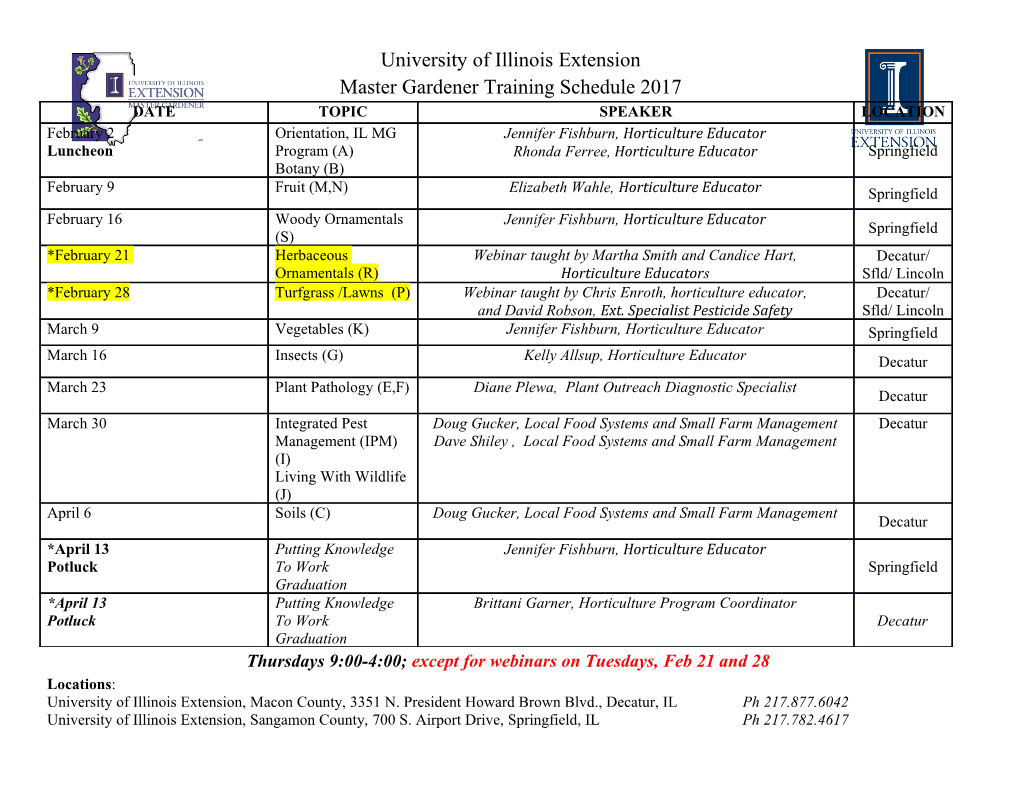
A Dissertation entitled Study of the influence of nanosized filler on the UV light-curable resin bonded abrasive tool by Lei Guo Submitted to the Graduate Faculty as partial fulfillment of the requirements for the Doctor of Philosophy Degree in Mechanical Engineering ________________________________________ Dr. Ioan Marinescu, Committee Chair ________________________________________ Dr. Abdollah Afjeh, Committee Member ________________________________________ Dr. Sorin Cioc, Committee Member ________________________________________ Dr. Liangbo Hu, Committee Member ________________________________________ Dr. Chunhua Sheng, Committee Member ________________________________________ Dr. Patricia R. Komuniecki, Dean College of Graduate Studies The University of Toledo May 2016 Copyright 2016, Lei Guo This document is copyrighted material. Under copyright law, no parts of this document may be reproduced without the expressed permission of the author. An Abstract of Study of the Influence of Nanosized Filler on the UV-Curable Resin Bonded Diamond Abrasive Tools by Lei Guo Submitted to the Graduate Faculty as partial fulfillment of the requirements for the Doctor of Philosophy Degree in Mechanical Engineering The University of Toledo May 2016 As one of the most broadly employed machining process, abrasive machining is a complex material removal process in which a number of abrasive grains randomly cut material off from the workpiece. Common examples including grinding, lapping, honing and polishing can be all categorized to abrasive machining process. In the manufacturing of abrasive tools like grinding wheel and lapping plate, two of the most significant components are primarily considered: the abrasive grain and the bonding agent. Abrasive grains are usually selected from Aluminum oxide, Silicon carbide, Diamond and CBN in modern industry, while metal bonding agent and resin bonding agent is the most widely used matrix material. Thanks to a remarkable development on rapid prototyping, the ultraviolet (UV) curing technology has been applied at a wide range in manufacturing. In this research, the UV curing techniques was introduced into the fabrication of resin bond abrasive tool. In order to optimize the time consuming, reduce the energy cost of the traditional iii manufacturing process and improve the machining performance of the tool, the thermosetting resin agent was replaced with UV light-curable resin. To verify the manufacturing feasibility and examine the machining performance of the tool, an UV light-curable resin bond grinding wheel was developed with diamond as the abrasive grain. A group of comparative experiments on ceramic workpiece was carried out to study the machining capacity of the tool, in terms of surface finishing and material stock removal. Moreover, nanosized alumina particle was selected as a filler additive in the manufacturing process in order to improve the material properties of the resin matrix, and strengthen the bonding between the matrix and the diamond grain. Interestingly, the result showed that the utilization of nanosized alumina filler influenced not just the manufacturing of the tool, but also the performance of the tool in a very positive way. In order to determine the influence of filler loading on the bonding mechanism of each single diamond grain, a theoretical force model was established based on elastic mechanics to quantitively describe the retention capability of the resin matrix, in terms of compressive stress generated from the shrinkage of resin. Because of the micron scale of diamond grains in resin matrix, it is hard to experimentally verify this force model. Therefore, a numerical model was also developed based on FEM simulation to validate the reliability of above-mentioned force model. A series of calculation and simulation were carried out to comparatively study the retention force on each diamond grain in pure resin matrix and filler loaded resin matrix. The results obtained are consistent with reasonable errors that could be explained by the difference in application conditions of each model. From a perspective of process prediction, these models could provide not just a direct output including matrix volume shrinkage and compressive force generated on each iv diamond grit, but also an indirect output as the tool’s machining capacity that largely determined by diamond retention. v Acknowledgements I would like to express my greatest gratitude to my advisor, Dr. Ioan Marinescu. I would never have been able to finish this work without the help and guidance from him. I would like to thank the entire dissertation committee: Dr. Abdollah Afjeh, Dr. Sorin Cioc, Dr. Liangbo Hu and Dr. Chunhua Sheng, for providing me all sorts of help and suggestion. I would like to thank to all the members from PMMC for creating a friendly research group to work with. I would like to thank all my friends, my family, especially my parents AiMin and Yaohui, to whom this work is dedicated. vi Table of Contents Abstract .............................................................................................................................. iii Acknowledgements ............................................................................................................ vi Table of Contents .............................................................................................................. vii List of Tables ..................................................................................................................... xi List of Figures ................................................................................................................... xii List of Abbreviations ...................................................................................................... xvii List of Symbols .............................................................................................................. xviii Chapter 1 Introduction ........................................................................................................ 1 1.1 Rapid Prototyping and UV Light Curing Technology ...................................... 1 1.2 UV-curable Resin in Manufacturing of Abrasive Tools ................................... 4 1.3 Introduction of Abrasive Machining Process ................................................... 6 1.3.1 Fixed Abrasive Machining Process ................................................... 8 1.3.2 Loose Abrasive Machining Process ................................................. 11 1.4 Mechanism of Resin Bond Abrasive Machining ............................................ 15 1.5 Filler Additive in Manufacturing of Resin Tool ............................................. 18 1.6 Introduction Summary and Research Motivation ........................................... 23 1.6.1 Introduction and Background Summary .......................................... 23 1.6.2 Research Motivation ........................................................................ 24 vii Chapter 2 Research Objectives and Dissertation Structure .............................................. 27 2.1 Research Objectives ........................................................................................ 27 2.2 Research Framework and Dissertation Structure ............................................ 29 Chapter 3 UV Light-Curable Resin Bond Diamond Lap Grinding Wheel ....................... 32 3.1 Experimental Procedure .................................................................................. 32 3.1.1 UV Light-curable Resin Prepare ...................................................... 32 3.1.2 Abrasive Prepare .............................................................................. 33 3.1.3 UV Light Curing System Setup ....................................................... 36 3.1.4 Manufacturing of the UV-Resin Bond Diamond Grinding Wheel .. 38 3.2 Experiment of Lap-Grinding on Ceramic Workpiece .................................... 43 3.3 Results and Discussion ................................................................................... 45 3.4 Conclusion ...................................................................................................... 52 Chapter 4 Influence of Nanosized Aluminum Dioxide Filler Additive ............................ 54 4.1 Experimental Procedure .................................................................................. 54 4.1.1 Materials Prepare ............................................................................. 54 4.1.2 Methods............................................................................................ 56 4.2 Results and Discussion ................................................................................... 59 4.2.1 Cure Depth of Resin-Diamond Composite ...................................... 59 4.2.2 Hardness of Cured Resin-Diamond Composite ............................... 62 4.2.3 Ultimate Tensile Strength ................................................................ 64 4.2.4 Worn Surface Microscopy Observation ........................................... 65 4.3 Lap Grinding Experiment on Ceramic Workpiece ......................................... 69 4.3.1 Surface Roughness of Workpiece .................................................... 69 viii 4.3.2 Material Removal Rate .................................................................... 72 4.4 Conclusion ...................................................................................................... 75 Chapter 5 Study on
Details
-
File Typepdf
-
Upload Time-
-
Content LanguagesEnglish
-
Upload UserAnonymous/Not logged-in
-
File Pages162 Page
-
File Size-