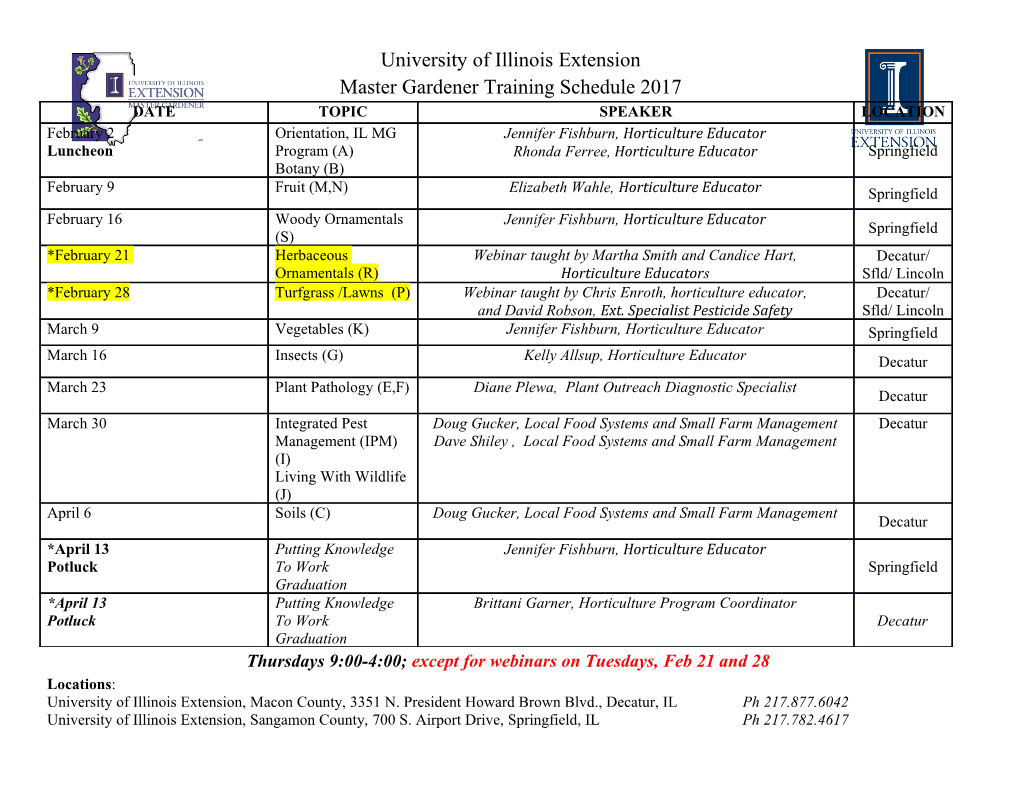
Thermal Spraying Thermal Spraying DIN 32530: Thermal spraying comprises processes that feature: - full or partial melting of spraying feedstock (or at least sufficient heat transfer in order to provide a state of high plastic deformation capability) inside or outside a spraying torch - propelling of spray particles onto a prepared substrate surface - substrate surface is (usually) not melted Definition Heat and Momentum Substrate Transfer Spraying gun Energy source -Flame -Arc -Plasma Spraying feedstock -Powder -Wire -Rod Principle of Thermal Spraying Coating formation Thermal Spraying Spraying direction Pores Oxides Heat flux Lateral spreading Contact zones Impact of spray particles on substrates Pore Oxidized particle Not fully molten particle Substrate Formation of thermal spray coatings t = 0.00 µs -50 µm 0 50 t = 0.08 µs t = 0.03 µs -50 µm -50 0 µm 0 50 50 t = 0.13 µs d = 50 µm, v = 200 m/s Spreading of a AlPart. Part. -50 µm 0 50 2 O 3 particle on a substrate t = 0.23 µs -50 µm 0 50 t = 0.62 µs t = 0.36 µs -50 µm -50 0 µm 0 50 50 t = 5.00 µs d = 50 µm, v = 200 m/s Spreading of an AlPart. Part. -50 µm 0 50 2 O 3 particle on a substrate 15 30 45 60 75 > 75 P [MPa] t = 0.04 µs t = 0.10 µs -0.1 0.1 -0.1 0.1 mm mm t = 0.06 µs t = 0.23 µs -0.1 0.1 -0.1 0.1 mm mm t = 0.09 µs t = 0.36 µs -0.1 0.1 -0.1 0.1 mm mm Pressure distribution in an Al2O3 particle during spreading on a steel substrate white dashs: t = 0.62 µs solidification boundary -0.10 0.10 [mm] Temperature [K] t = 3.00 µs -0.10 0.10 > 1550 [mm] > 1300 >1050 t = 10.00 µs -0.10 0.10 >800 [mm] > 550 > 300 Temperature distribution in an Al2O3 spray particle during impact on a steel substrate Powder injection Free plasma jet v too low v optimal v too high Coating Substrate 2D view of particle trajectories for radial powder injection into a plasma jet Time to heat down to particle core [10-5 s] Target temperature: 1750 K Ni Flight time of particles Particle radius [µm] Time to heat particles down to the core Substrate surface temperature [K] Distance to particle center [mm] Substrate temperature distribution after impact of an Al2O3 spray particle Pre-cleaning Grit blasting (Ultrasonically Removal of Assisted) Cleaning Dirt Roughening Removal of Oil and grease Decontaminating grit blasting residues Paint, etc. Activating Pre-treatment of substrate surfaces Grit Sand (impermissible because of health risks) Alumina (corundum) Hard cast iron particles Steel wire chips Silicon carbide 40 µm < d Particle < 4 mm Pre-treatment of substrate surfaces Bonding mechanisms Mechanical interlocking Adhesion Diffusion in small microstructure areas Chemical bonding Electrostatic forces Bonding of spray coatings Bond strength is a function of interface temperature spray particle / substrate particle impulse at impact on the substrate properties of particle and substrate surface thermal conductivity of substrate and spray particles evolution of residual stresses in coatings Bonding of thermal spray coatings Bond strength is influenced by bonding mechanisms and coating residual stress state. - High tensile residual stress state can result in coating failure Bond strength > Coating strength Bond strength < Coating strength Bonding of spray coatings Spraying feedstock Thermal Spraying Hard material Zr Al W C B Cr Metal Mo Metalloid N Si Ti Ta V O Metallic hard material Non-metallic hard material Carbide Nitride Boride Oxide Nitride Carbide Cr32xCy TiN TiB2 Al2 O 3 BN SiC WC TaN ZrB2 Cr2 O 3 Si 3N 4 B 4C VC TiO2 ZrO2 Metal Metal Hardmetal Hard alloy Cermet WC/Co Fe-Cr-C-Base Co/ZrO2 WC/CoCr Co-Cr-W-C-Base Al/Al 2O 3 (W, Ti, Ta)C/Co Ni-Cr-B-Si-Base Material spectrum Powder 5 µm < dparticle < 120 µm Narrow powder size fractions ease optimization of process parameters and permit optimal coating properties. Drawback: high powder costs Spraying feedstock Powder geometry spherical (usually optimal) irregular (optimal only for cold gas spraying) spattered (not useful) hollow spheres (especially ceramics) „special development“ Spraying feedstock Powder types Homogeneous powder Composite powder melt atomized agglomerated and sintered fused and crushed mechanically clad precipitated (chemically) chemically clad SHS (Self Propagating High Temperature Synthesis) sintered and crushed mechanically alloyed (high energy milling) Powder production methods Crucible Molten metal Insert Cast opening Melt stream Nozzle Atomization medium Atomized particles Melt atomization open close-coupled NANOVAL Ma < 1 Ma = 1 Ma >< 1 Nozzle configurations for melt atomization In crucible In atomization chamber Vacuum Inert gas Inert gas Air Air Water vapor Influencing parameters of melt atomization - Atmosphere - Chemical composition Viscosity Surface tension Difference between melting and vaporization temperature Melt beam velocity Crucible diameter Influencing parameters of melt atomization - Melt - Gas or liquid Pressure Flow rate Velocity (nozzle design) Temperature Viscosity Influencing parameters of melt atomization - Atomization medium - Nozzle diameter Nozzle design (e.g. opening angle) Distance between insert and nozzle Height of atomization chamber Cooling medium (water or gas) Influencing parameters of melt atomization - Atomization conditions - Atomization Typical oxygen content Vacuum - Inert gas 40 ppm Inert gas - Inert gas 100 ppm Inert gas - Water 150 ppm Water 500 - 1000 ppm Gas content of melt atomized NiCrBSi powder Melt atomized NiCrBSi (gas / gas) Melt atomized Ni5Al (gas / water) Principle Melting and atomization of wires in converging plasma jets of three plasma torches Special process for melt atomization gas atomized water atomized Al, Cu, Ni, Mo, Ti Ni Al12Si FeCrNi, FeCrNiMo CuNi, CuAl CoMoCrSi FeCrNi, FeCrNiMo Ni20Cr, Ni5Al, NiCrBSi CoCrNiWTaC Ni20Cr, Ni5Al, NiMoAl, NiCrAl, NiCrBSi MCrAlY (M: Ni, Co, Fe) Ti6Al4V Typical melt atomized powder Principle After casting of melt into a mould and cooling the compact body is crushed and milled. Examples: Mo WC/Co Cr2O3, Al2O3, Al2O3 / TiO2 / Cr2O3 / MgO / SiO2 ZrO2 / Y2O3, ZrO2 / MgO, ZrO2 / CaO Fused and crushed powder Fused and crushed Cr2O3 powder Fused and crushed ZrO2 / Y2O3 93/7 Principle After sintering of fine powders and cooling the compact body is crushed and milled. Examples: Mo WC / Co, e.g. WC/Co 94/6 WC, WSC (WC/W2C) TiC, Cr3C2, NbC, TaC TiO2, TiO2 / Cr2O3, ZrO2 / Y2O3, ZrO2 / MgO Sintered and crushed powder Heat exchanger Gas distributor Gas filter Exhaust air Atomizer Exhaust fan Drying chamber Cyclone Suspension Powder channel Feeding pump Spray drying (Agglomeration) Atomization of suspensions proceeds by centrifugal forces on top of the drying chamber, where drying gas is also injected. - bucket shaped rotating, impeller and perforated wheel atomizers Spray drying by rotating atomizers Atomization of suspensions is carried out against force of gravity in a chamber with a swirled drying gas stream injected on its top. - long dwell time of agglomerates in the drying gas stream - only relatively small chamber required Spray drying by pneumatic nozzle Usually agglomerated powders are subject to thermal post-treatment (sintering) in order to improve the compound strength of the individual particles. -T < Tm (Tm of the compound is usually much smaller than the Tm of the components) - T < Temperature initiating impermissible metallurgical reactions (in particular exothermic reactions have to be avoided) - Atmosphere must be chosen adequately in order to avoid impermissible reactions Post-treatment of agglomerated powder Agglomerated and sintered Mo Metals Mo Cermets WC / Co(Cr), z.B. WC/Co 88/12, WC/CoCr 86/10-4 Cr3C2 / Ni20Cr, z.B. Cr3C2/Ni20Cr 75/25 Ceramics Al2O3 / TiO2, z.B. Al2O3 / TiO2 87/13 Al2O3 / Cr2O3 / MgO / TiO2 ZrO2 / Y2O3, z.B. ZrO2 / Y2O3 93/7 ZrO2 / CaO / CeO2 / MgO / SiO2 Typical agglomerated powders Principle By control of temperature, pH value and addition of neutralizing agents usually very fine powders are precipitated from salt solutions. Depending on the applied salts purity high purity products are possible. Usually agglomeration and sintering is required. Examples: usually oxide ceramic powders ZrO2, TiO2, CeO2 co-precipitation also permits production of multi- component oxide powders ZrO2 / TiO2 / CeO2 / HfO2 Precipitation of powders Principle: After activation and seeding of ceramic powder particle surfaces with palladium complete chemical cladding preferrably with Ni or Cu is carried out. Examples: Graphite - clad with nickel WC single crystals - clad with nickel Drawbacks: - High production costs - Long processing times Chemically clad powders Graphite powder chemically clad with Ni Graphite powder chemically clad with Ni process gas (inert / reactive) Pressure control ignition reaction front cooling water outlet cooling water inlet Principle of Self Propagating High Temperature Synthesis Igniter Reaction product Synthesis zone Reaction front Initial powder Principle of Self Propagating High Temperature Synthesis Chemical composition (incl. purity) Atmosphere (inert / reactive) Chamber pressure Cooling rate Initial powder particle size distribution Distribution of initial powder composition Controlling parameters of Self Propagating High Temperature Synthesis SHS laboratory reactor Reaction front propagation: 1 - 250 mm/s Synthesis temperature: 800 - 3500 °C Ignition temperature: 500 - 800 °C Temperature gradient: 105 -106 K/m Heating rate: 103 -106 K/s SHS reaction progress 20 µm TiC/Fe30Cr 55/45 SHS powder Principle: High energy ball milling auf powder mixtures is carried out with the aim to achieve alloy formation
Details
-
File Typepdf
-
Upload Time-
-
Content LanguagesEnglish
-
Upload UserAnonymous/Not logged-in
-
File Pages181 Page
-
File Size-