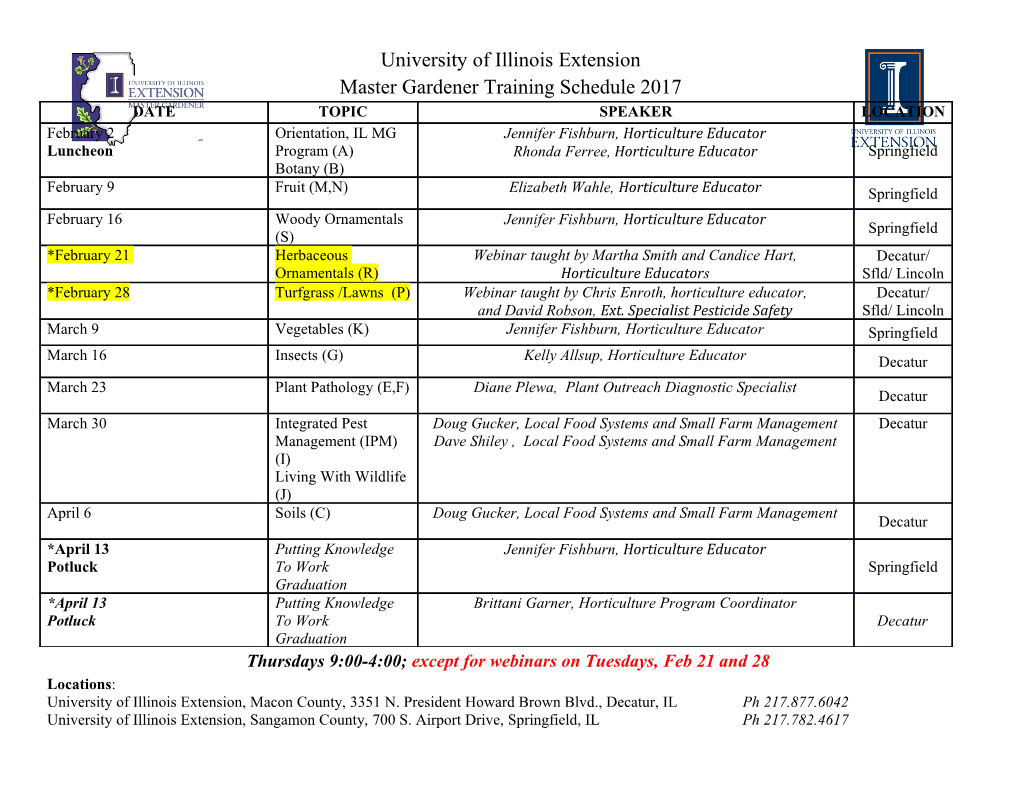
TWR-P (TerraPower, U.S.A.) FIG. 13. Schematic View TerraPower's Prototype Reactor Full name: Travelling Wave Reactor-Prototype (TWR-P) Designer: TerraPower Reactor type: Pool-type, Sodium-cooled Fast Reactor Electrical capacity: 600 MWe Thermal capacity: 1475 MWth Primary Circulation Forced convection using mechanical pumps System Pressure: 0.1 MPa System Temperature: 360/500 °C Fuel Material: Composed of uranium-zirconium metal alloy fuel slugs with a sodium thermal bond in ferritic-martensitic steel cladding Fuel Cycle: 18-24 Months Residual heat removal systems: Passive - Direct Reactor Auxiliary Cooling System Design Life: 40 Years Design status: Conceptual Design Planned deployment/1st date of Start of Construction by 2018 completion: New/Distinguishing Features: Traveling wave reactor 29 Introduction significantly enhanced when compared to A TWR is a class of reactors that is designed currently operating LWRs. to operate indefinitely after a startup period The TWR-P employs enriched fuel using only natural or depleted uranium. The assemblies (driver assemblies) with sealed waves that breed and deeply burn fissile sodium bonded metallic U-Zr10% fuel pins nuclides in-situ travel relative to the fuel and with 70% smear density, for which data and provide the possibility for very long core life experience is available. To achieve flux (~60 years). This long core life allows for profile and power and temperature gradients higher fuel utilization, up to about 30 times similar to those of a TWR and reproduce greater than light water reactors (LWRs). prototypical power histories of breed and The breed and burn process is achieved burn assemblies, the core also employs feed through a “standing wave” by periodic re- fuel assemblies made of depleted uranium. shuffling of the fuel in such a manner that These fuel assemblies have also U-Zr10% higher burn-up assemblies are moved to the metal fuel with 70% smear density. periphery of the core and depleted uranium The core and all primary cooling system fuel assemblies replace the high burn-up components are contained in the reactor fuel. Excess reactivity in the TWR core vessel with the addition of a number of in- increases and control rods are slowly inserted vessel structures. All vessels and structures to offset this increase. The re-shuffling is in direct contact with primary sodium performed during the reactor is shut down coolant are fabricated from 316H stainless each 18 to 24 months. TWR uses advanced steel. Both vessels and a number of major metal fuel and advanced ferritic-martensitic components are supported from the reactor steel cladding with capabilities to reach high head, which is supported by a bearing system peak burnups of ~30% and high doses interfaced to a concrete ledge in the reactor necessary to enable breed and burn operation building on depleted uranium. The TWR-P is a Description of the Safety Concept prototype of TWR to demonstrate TWR core TWR-P is similar to other pool-type, fuel management, qualify TWR advanced sodium-cooled fast reactors in that Loss of fuel assemblies, and validate core radial Coolant Accidents are eliminated from the expansion reactivity feedback and design bases. The primary design basis effectiveness of the core restraint system. accidents are Loss of Flow and Loss of Heat Description of the Nuclear System Sink. Transient overpower events are less TWR-P is a1475MWth/600MWe gross liquid frequent because interlocks prevent sodium cooled, fast neutron spectrum reactor excessive rod withdrawal during operation. that uses U-10%Zr metallic fuel with HT-9 The TWR-P plant employs for emergency ferritic-martensitic stainless steel clad. The decay heat removal four Direct Reactor plant’s 4m diameter, 5.5m tall cylindrical Auxiliary Cooling System (DRACS) loops core sits near the bottom of a 13.3m dissipating heat to air as an ultimate heat diameter, 17.65m tall reactor vessel which is sink, each of which is capable of removing enclosed within a guard vessel. This pool- enough heat to protect public health and type configuration has no radial piping safety. These NaK filled loops are penetrations through either vessel so the risk completely passive and require no electricity of loss of coolant accidents is eliminated. to activate or operate. The large volume of sodium acts as a huge Deployment Status and Planned Schedule heat sink, so transients are much slower, The TWR-P is expected to be constructed providing operators much longer time to between 2018 and 2023. After a period of respond to off-normal events and the overall testing and optimization, commercial plants safety performance of the plant is are expected to be licensed with start up in the late 2020s or early 2030s. 30 .
Details
-
File Typepdf
-
Upload Time-
-
Content LanguagesEnglish
-
Upload UserAnonymous/Not logged-in
-
File Pages2 Page
-
File Size-