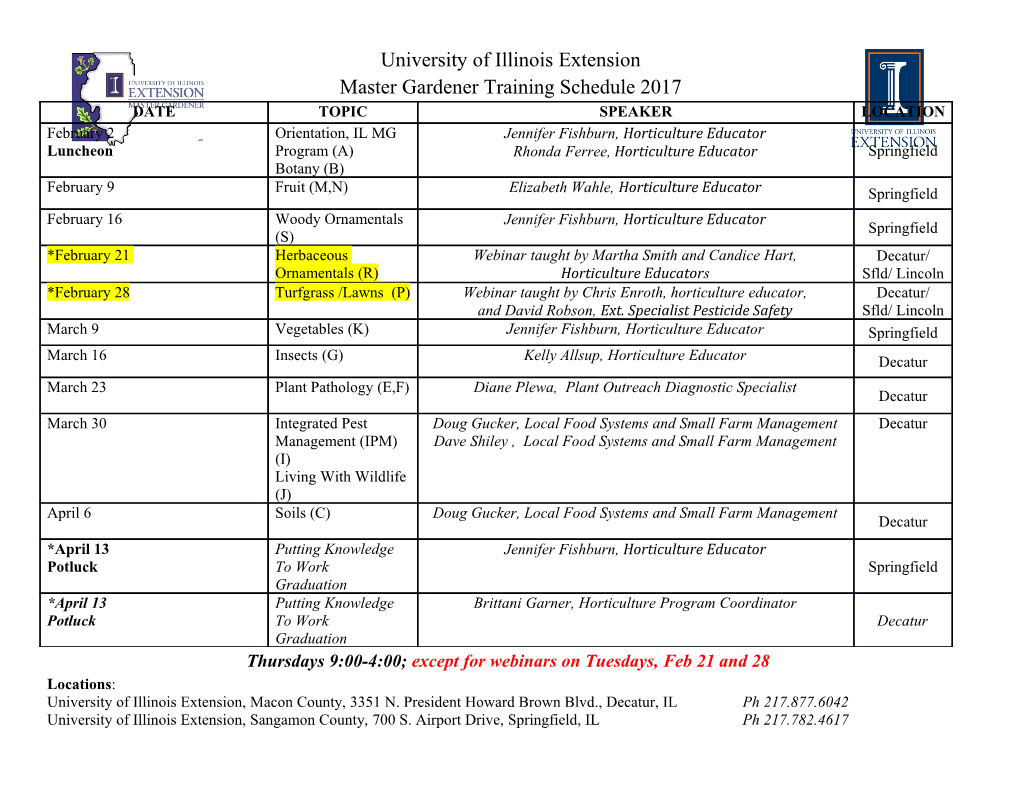
365 The Space Exposure Experiment of PEEK Sheets under Tensile Stress∗ Takashi NAKAMURA∗∗, Hiroshi NAKAMURA∗∗, Osamu FUJITA∗∗, Toru NOGUCHI∗∗ and Kichiro IMAGAWA∗∗∗ To find out the degradation behavior of polymer in the real space, space exposure ex- periments utilizing the International Space Station (ISS) were scheduled. PEEK sheets under tensile stresses were exposed to the environment around the ISS orbit, and were irradiated by atomic oxygen (AO), ultraviolet ray, and electron beam (EB) in the ground test facility. This study introduces the outline of these experiments, and shows the results of AO and EB pilot irradiation tests as follows: (1) Test piece surfaces after AO exposure exhibited significant morphological damages characterized by micron-sized conical pits. (2) Thickness reduc- tions of the test pieces by AO exposure increased with increasing tensile stress. (3) Residual strength after AO exposure could be estimated by taking account of thickness reduction. (4) No significant change was observed on surface morph, mass, chemical structure, and tensile properties of the test pieces after EB exposure regardless of tensile stress. Key Words: High Polymer Materials, Tensile Properties, Material Testing, PEEK, Interna- tional Space Station, Low Earth Orbit, Atomic Oxygen, Ultraviolet Ray, Elec- tron Beam vironment. 1. Introduction To investigate these phenomena, we organized two In recent years, polymeric materials are getting im- kinds of experiments: one was a space exposure experi- portant for fabricating space structures. Especially, poly- ment and the other was a ground control experiment. Fig- meric sheets are essentially needed for inflatable struc- ure 1 shows an outline of these experiments. The space tures(1), the state of the art technology in construction of exposure experiments expose Poly-Ether-Ether-Ketone space facilities such as moon bases, large space antennas. (PEEK) sheets with tensile loads to the real space envi- These space-based structural members have to hold a cer- ronment. This research is a part of a space exposure ex- tain amount of load in the real space. However, space periment program named as Micro-Particles Capturer and can be extremely harsh to polymers due to the presence of Space Environment Exposure Device (MPAC&SEED) ex- (4) several types of radiation and atomic oxygen (AO)(2).In periment implemented by the Japan Aerospace Explo- particular, it is known that many polymeric materials are ration Agency (JAXA). This exposure experiment started damaged by AO in low earth orbit, altitudes from 200 to in October 2001, utilizing the ISS Russian Service Mod- 700 km where the International Space Station (ISS) goes ule, and is still ongoing now. In contrast, the ground con- around(3). At this stage, we have insufficient data on inter- trol experiments irradiate AO, ultraviolet ray (UV) and relation between tensile stress and degradation behavior electron beam (EB) artificially to the PEEK sheets of the of polymeric materials suffered from the “real” space en- same kind using ground facilities of JAXA. This report introduces the outline of the space and ∗ Received 26th January, 2004 (No. 04-4036) the ground experiments, and shows the first available re- ∗∗ Division of Mechanical Science, Graduate School of Engi- sults of pilot irradiation tests carried out before the regular neering, Hokkaido University, North 13, West 8, Kita-ku, ground experiments. After exposure in space, data will be Sapporo, Hokkaido 060–8628, Japan. analyzed together with these ground results to investigate E-mail: [email protected] the degradation process of tension-loaded polymers in the ∗∗∗ Institute of Space Technology and Aeronautics, Japan space environment. Aerospace Exploration Agency (JAXA), 2–1–1 Sengen, Tsukuba, Ibaraki 305–8505, Japan JSME International Journal Series A, Vol. 47, No. 3, 2004 366 Fig. 1 Outline of the space exposure experiment program using PEEK sheets under tensile stresses Fig. 2 Chemical structure of PEEK 2. Space Exposure Experiment Program 2. 1 Material Materials to be used in space must have a high heat resistance. More specifically, we have to select mate- rials capable of withstanding temperatures higher than +100◦C∼+150◦C according to estimated temperatures of exposure devices. After narrowing the candidate materials to several varieties in terms of heat resistance, PEEK was finally selected by the AO and UV pre-irradiation test. Fig. 3 Test pieces for the space exposure experiments PEEK is one of crystalline thermoplastic polymers. Its molecular structure is shown in Fig. 2. We use FS- 1100C (produced by Sumitomo Bakelite Co., Ltd.) with a 0.4 mm thickness as our PEEK sheet. The high heat re- sistance (Continuous service temperature: 260◦C) of this material is achieved by the aromatic structures. PEEK has an excellent heat resistance and a radiation proof property similar to polyimide, which is a well-known space mate- rial at present. Compared with the polyimide, PEEK has a better workability to fabricate thin sheet type products resulting from its thermo-plastic properties. 2. 2 Space exposure experiments Figure 3 shows the test pieces for the space exposure experiments. Three types with different widths were fab- ricated from sheets with a 0.4 mm thickness. The axial direction of each test piece was same as the drawing di- Fig. 4 Test piece attachment for the space exposure experi- (5) rection of the sheets. A test piece attachment is shown in ments Fig. 4(5). A tensile load was applied to the specimen by a tension spring. The initial stresses were determined to 0, mounted were four test piece attachments: two were with 1.57, and 4.70 MPa by the different specimen widths. The no stress but one each was with low stress and high stress. ratios of initial stresses to yield stress (≈ 85 MPa) were 0, Onboard also were many other samples proposed by other 2, and 5%, respectively. researchers. Three sets of sample holders were fixed to A sample holder is shown in Fig. 5. On this holder the outside of the service module. The surfaces of the test Series A, Vol. 47, No. 3, 2004 JSME International Journal 367 Table 1 Performance of the Combined Space Effects Test Fa- cility of JAXA Fig. 5 Sample holder for the space exposure experiments pieces were set perpendicular to the forward direction of the ISS. The ISS goes around its orbit at an altitude of about 400 km at a velocity of about 8 km/s. The individual sample holders were scheduled to be exposed for 1, 2, and 3 years with an annual recovery by a Soyuz spacecraft as Fig. 6 Test piece attachment for the ground control experi- shown in Fig. 1. One sample holder exposed for one year ments in space was returned to the earth in November 2002, and the analyses and evaluations of the test pieces are ongoing similar to those in the space exposure experiments were at Hokkaido University. scheduled for the irradiated samples. The major contents of the analyses are as follows: Figure 6 shows the test piece attachment for the • Physical factors: Change in mass loss, thickness, ground control tests. Four test pieces were mounted on surface morph, and reaction efficiency the attachment, and two of them were loaded by different • Chemical factors: Change in chemical structure, coil springs. Although the test piece shapes were slightly molecular weight, and crystallinity different from those shown in Fig. 3, as the widths were • Mechanical factors: Change in tensile properties 25 mm, 7.8 mm, 11 mm for no stress, low stress, and high (elastic modulus, yield strength, tensile strength, necking stress, respectively, the initial stresses were same as those stress, elongation, and energy at break) and fracture pro- of space exposure experiments. Two AO monitors (Kap- cesses ton) are also shown in Fig. 6. The AO fluence was mea- By measuring these factors, we hope to clarify the sured by using mass losses of these monitors. time dependant degradation process affected by different 3. Pilot Irradiation Tests before the Ground Control exposure periods. We understand, however, that it will Experiments be difficult to distinguish environmental effects clearly be- cause AO and other various types of radiation will affect Before the regular ground control experiments men- test pieces at a time. To address this problem, we planned tioned in section 2.3, we conducted pilot irradiation tests ground control experiments. using AO and EB beams. The pilot irradiation tests were 2. 3 Ground control experiments programmed to blush up experimental methods and analy- Ground control experiments use AO, UV, and EB as sis points of the ground control experiments. This chapter representatives of the residual atmosphere, direct sunlight, introduces main results of the pilot irradiation tests. and particulate radiation, respectively. Irradiation tests are 3. 1 AO exposure ongoing using the Combined Space Effects Test Facility 3. 1. 1 Experimental procedure The experimen- of JAXA. As shown in Table 1, this facility can irradiate tal conditions of pilot AO exposure tests are shown in Ta- single source of AO, UV, and EB to test pieces in the vac- ble 2. The AO fluence was 2.79 × 1020 atoms/cm2.Thisis uum environment. The fluence of each irradiation was se- an average value measured by the two AO monitors, and is lected to be equivalent to that during six months, one year, equivalent to about 1 – 3 weeks on the ISS orbit. The AO and three years on the ISS orbit. Analyses and evaluations velocity, 8.1 km/s, was same as the ISS speed. The trans- JSME International Journal Series A, Vol. 47, No. 3, 2004 368 Table 2 Conditions of AO exposure (a) Before exposure Fig. 7 Test piece surface after AO exposure lational energy of the AO beam with this velocity is 5 eV. The applied stresses during exposure were same as those of the regular space exposure and ground control experi- ments.
Details
-
File Typepdf
-
Upload Time-
-
Content LanguagesEnglish
-
Upload UserAnonymous/Not logged-in
-
File Pages6 Page
-
File Size-