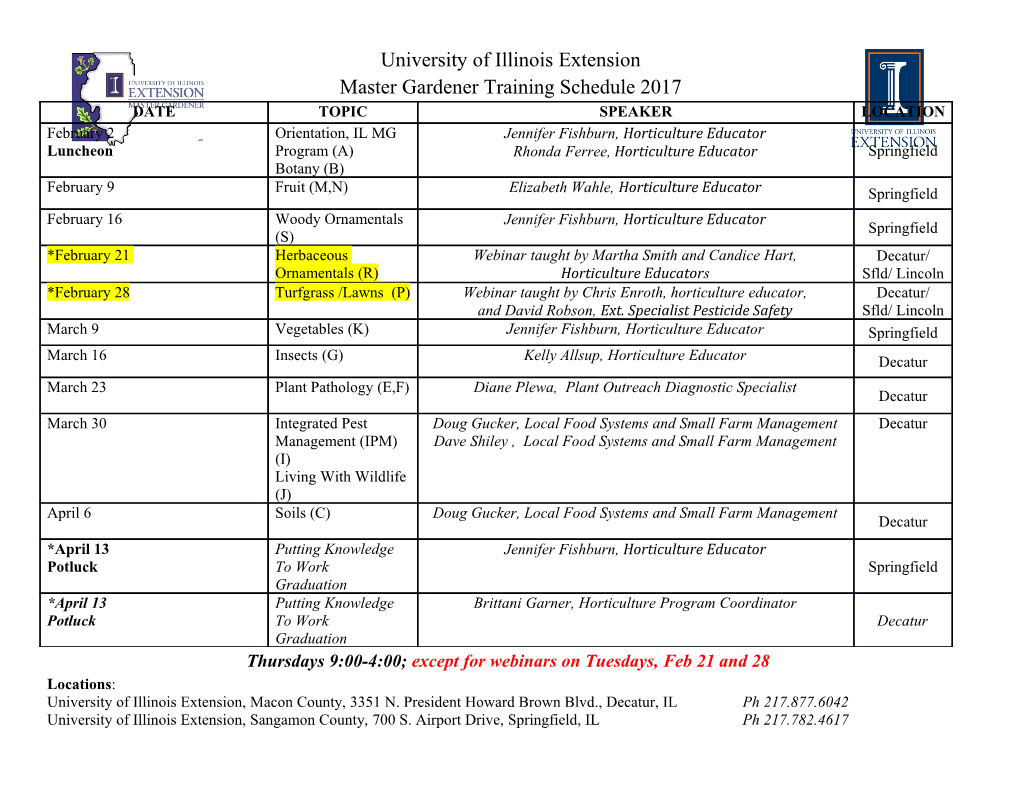
Plastic 1 Plastic A plastic material is any of a wide range of synthetic or semi-synthetic organic solids used in the manufacture of industrial products. Plastics are typically polymers of high molecular mass, and may contain other substances to improve performance and/or reduce costs. Monomers of plastic are either natural or synthetic organic compounds. The word plastic is derived from the Greek πλαστικός (plastikos) meaning capable of being shaped or molded, from πλαστός (plastos) meaning molded.[1] [2] It refers to their malleability, or plasticity during Household items made of various types of plastic manufacture, that allows them to be cast, pressed, or extruded into a variety of shapes—such as films, fibers, plates, tubes, bottles, boxes, and much more. The common word plastic should not be confused with the technical adjective plastic, which is applied to any material which undergoes a permanent change of shape (plastic deformation) when strained beyond a certain point. Aluminum which is stamped or forged, for instance, exhibits plasticity in this sense, but is not plastic in the common sense; in contrast, in their finished forms, some plastics will break before deforming and therefore are not plastic in the technical sense. There are two types of plastics: thermoplastics and thermosetting polymers. Thermoplastics are the plastics that don't undergo chemical change in their composition when heated and can be moulded again and again; examples are polyethylene, polystyrene, polyvinyl chloride and polytetrafluoroethylene (PTFE).[3] Thermosets can melt and take shape once; after they have solidified, they stay solid. The raw materials needed to make most plastics come from petroleum and natural gas.[4] Overview Plastics can be classified by chemical structure, namely the molecular units that make up the polymer's backbone and side chains. Some important groups in these classifications are the acrylics, polyesters, silicones, polyurethanes, and halogenated plastics. Plastics can also be classified by the chemical process used in their synthesis, such as condensation, polyaddition, and cross-linking.[5] Other classifications are based on qualities that are relevant for manufacturing or product design. Examples of such classes are the thermoplastic and thermoset, elastomer, structural, biodegradable, and electrically conductive. Plastics can also be classified by various physical properties, such as density, tensile strength, glass transition temperature, and resistance to various chemical products. Due to their relatively low cost, ease of manufacture, versatility, and imperviousness to water, plastics are used in an enormous and expanding range of products, from paper clips to spaceships. They have already displaced many traditional materials, such as wood; stone; horn and bone; leather; paper; metal; glass; and ceramic, in most of their former uses. The use of plastics is constrained chiefly by their organic chemistry, which seriously limits their hardness, density, and their ability to resist heat, organic solvents, oxidation, and ionizing radiation. In particular, most plastics will melt or decompose when heated to a few hundred degrees celsius.[6] While plastics can be made electrically Plastic 2 conductive, with the conductivity of up to 80 kS/cm in stretch-oriented polyacetylene,[7] [8] [9] [10] they are still no match for most metals like copper which have conductivities of several hundreds kS/cm. Plastics are still too expensive to replace wood, concrete and ceramic in bulky items like ordinary buildings, bridges, dams, pavement, and railroad ties. Chemical structure Common thermoplastics range from 20,000 to 500,000 amu, while thermosets are assumed to have infinite molecular weight. These chains are made up of many repeating molecular units, known as repeat units, derived from monomers; each polymer chain will have several thousand repeating units. The vast majority of plastics are composed of polymers of carbon and hydrogen alone or with oxygen, nitrogen, chlorine or sulfur in the backbone. (Some of commercial interests are silicon based.) The backbone is that part of the chain on the main "path" linking a large number of repeat units together. To customize the properties of a plastic, different molecular groups "hang" from the backbone (usually they are "hung" as part of the monomers before linking monomers together to form the polymer chain). This fine tuning of the properties of the polymer by repeating unit's molecular structure has allowed plastics to become such an indispensable part of twenty first-century world. Some plastics are partially crystalline and partially amorphous in molecular structure, giving them both a melting point (the temperature at which the attractive intermolecular forces are overcome) and one or more glass transitions (temperatures above which the extent of localized molecular flexibility is substantially increased). The so-called semi-crystalline plastics include polyethylene, polypropylene, poly (vinyl chloride), polyamides (nylons), polyesters and some polyurethanes. Many plastics are completely amorphous, such as polystyrene and its copolymers, poly (methyl methacrylate), and all thermosets. Molded plastic food replicas on display outside a restaurant in Japan Families Plastic 3 Plastics families Amorphous Semi-crystalline Ultra polymers PI, SRP, TPI, PAI, HTS PFSA, High performance PPSU, PEI, Fluoropolymers: LCP, polymers PESU, PSU PARA, HPN, PPS, PPA Other polyamides Mid range PC, PPC, COC, PMMA, PEX, PVDC, PBT, PET, POM, polymers ABS, PVC Alloys PA 6,6, UHMWPE Commodity PS, PVC PP, HDPE, LDPE polymers History The first human-made plastic was invented by Alexander Parkes in 1855;[11] he called this plastic Parkesine (later called celluloid). It was unveiled at the 1862 Great International Exhibition in London.[12] The development of plastics has come from the use of natural plastic materials (e.g., chewing gum, shellac) to the use of chemically modified natural materials (e.g., rubber, nitrocellulose, collagen, galalite) and finally to completely synthetic molecules (e.g., bakelite, epoxy, polyvinyl chloride, polyethylene). In 1866, Parkes formed the Parkesine Company to mass produce the material. The company, however, failed due to poor product quality as Parkes tried to reduce costs. Parkesine's successors were Xylonite, produced by Daniel Spill (an associate of Parkes), and Celluloid from John Wesley Hyatt. Parkesine was made from cellulose treated with nitric acid and a solvent. The generic name of Parkesine is pyroxylin, or Celluloid. Parkesine is often synthetic ivory. The Parkesine company ceased trading in 1868. Pictures of Parkesine are held by the Plastics Historical Society of London. There is a plaque on the wall of the site of the Parkesine Works.[13] Types Cellulose-based plastics Parkes developed a synthetic replacement for ivory which he marketed under the trade name Parkesine, and which won a bronze medal at the 1862 World's fair in London. Parkesine was made from cellulose (the major component of plant cell walls) treated with nitric acid and a solvent. The output of the process (commonly known as cellulose nitrate or pyroxilin) could be dissolved in alcohol and hardened into a transparent and elastic material that could be molded when heated.[14] By incorporating pigments into the product, it could be made to resemble ivory. Bois Durci is a plastic molding material based on cellulose. It was patented in Paris by Lepage in 1855. It is made from finely ground wood flour mixed with a binder, either egg or blood albumen, or gelatine. The wood is probably either ebony or rose wood, which gives a black or brown resin. The mixture is dried and ground into a fine powder. The powder is placed in a steel mold and compressed in a powerful hydraulic press while being heated by steam. The final product has a highly polished finish imparted by the surface of the steel mold. Bakelite The first so called plastic based on a synthetic polymer was made from phenol and formaldehyde, with the first viable and cheap synthesis methods invented in 1907, by Leo Hendrik Baekeland, a Belgian-born American living in New York state. Baekeland was searching for an insulating shellac to coat wires in electric motors and generators. He found that mixtures of phenol (C H OH) and formaldehyde (HCOH) formed a sticky mass when mixed together 6 5 and heated, and the mass became extremely hard if allowed to cool. He continued his investigations and found that the material could be mixed with wood flour, asbestos, or slate dust to create "composite" materials with different Plastic 4 properties. Most of these compositions were strong and fire resistant. The only problem was that the material tended to foam during synthesis, and the resulting product was of unacceptable quality. Baekeland built pressure vessels to force out the bubbles and provide a smooth, uniform product. He publicly announced his discovery in 1912, naming it bakelite. It was originally used for electrical and mechanical parts, finally coming into widespread use in consumer goods in the 1920s. When the Bakelite patent expired in 1930, the Catalin Corporation acquired the patent and began manufacturing Catalin plastic using a different process that allowed a wider range of coloring. Bakelite was the first true plastic. It was a purely synthetic material, not based on any material or even molecule found in nature. It was also the first thermosetting plastic. Conventional thermoplastics can be molded and then melted again,
Details
-
File Typepdf
-
Upload Time-
-
Content LanguagesEnglish
-
Upload UserAnonymous/Not logged-in
-
File Pages13 Page
-
File Size-