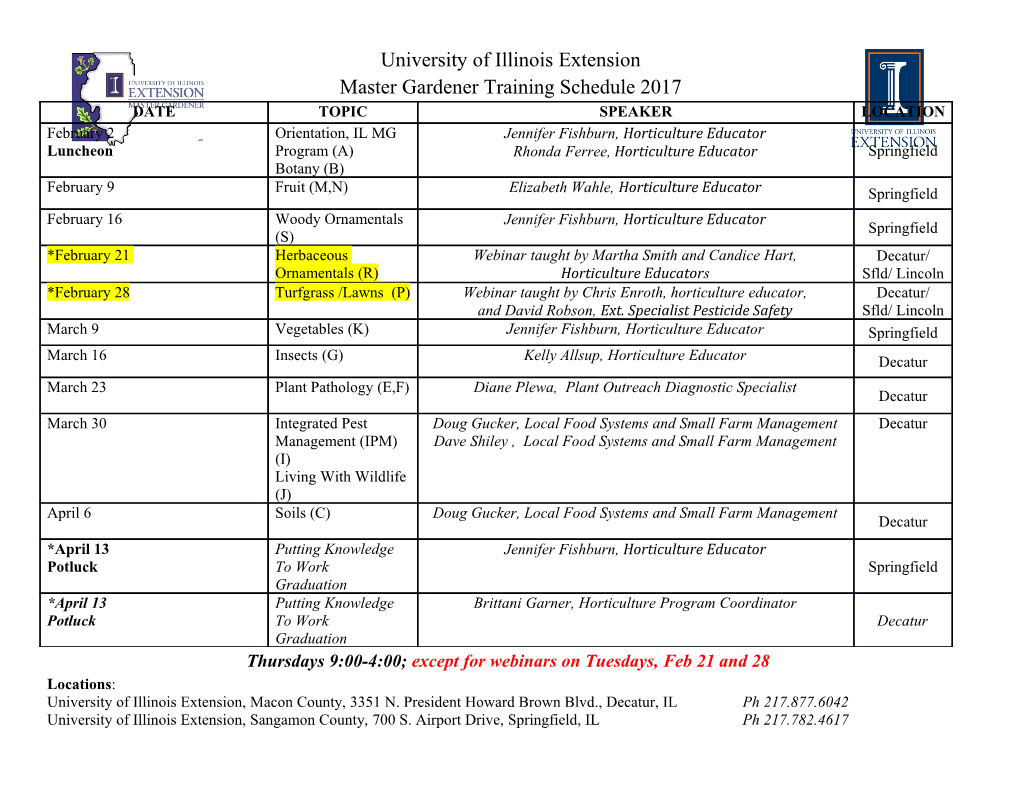
08 Technology Electro Magnetic Casting-Pit (EMC) at AMAG Premium rolling slabs for premium rolled products AMAG rolling slabs achieve the highest quality standards. This article gives a Possible types of inclusions review about essential and quality-decreasing inclusions appearing during pro- for EN AW-7075 duction of rolling slabs of the alloy EN AW-7075 and how to avoid them [1,2]. AMAG understand itself as an expert in minium alloys. For this purpose, com- Non-metallic inclusions the field of hardening aluminium alloys. prehensive knowledge of the formation • Al 2O3, MgO, Al 2MgO 4 As a premium supplier, AMAG produces mechanisms for each type of inclusion is • Carbides high-strength sheets and plates for aer- required in order to avoid inclusion gen- • Silicates ospace and sportive applications. Fur- eration as well as for efficient melt treat- • Reacted and non-reacted thermore, 7xxx series alloys (e.g. AMAG ment actions. Exemplary, the formation refractory material ® TopForm UHS) can be used in ambitious mechanisms of non-metallic inclusions • Salts (NaCl, KCl, MgCl 2) and light weight structure elements after half are mostly process step independent, e. chlorinated oxides warm forming. For a first class rolling g. oxide generation depends only on the • Graphite product, a first class casting microstruc- presence of oxygen or an oxygen carrier • Aluminium nitride ture is a precondition, which is not only in- (ambient moisture). In contrast to this, • Bone ash fluenced by the chemical composition and the formation of inter-metallic inclusions solidification conditions, but also by avoid- is strongly depending on melt composi- Oxide films ing unwanted influences like inclusion tion and temperature. • Al 2O3 – aluminium oxide content etc. The following article gives a • MgO – magnesium oxide short introduction in the complex topic of After successful inclusion removal actions, • Mixed oxides (Spinel) inclusion formation mechanisms and the the avoidance of inclusion re-entry has to responsible influences. be ensured by an optimized design of the Intermetallic inclusions process chain in order to guarantee the • TiB 2- Agglomerates Inclusions are representing separated customer oriented product quality. The box • Cr-Aluminides phases of particles or clusters in the below gives an overview about possible • Non dissolved alloying elements microstructure of aluminium and alu- types of inclusions. e. g. Cr- u. Ti-pre-alloys Technology 09 Non-metallic Inclusions and Oxide Films Nonmetallic inclusions and oxide films, • Magnesium Oxide – MgO generation are organic substances and which have to be considered in a separate Due to the related character of aluminium carbon in contact with liquid metal. The fol- way, are representing the main group of and magnesium the formation of mag- lowing important sources for carbide gen- inclusions. They usually cover 90 to 95 % nesium oxide happens also by the three eration are known: reaction of oil or other of a typical inclusion spectrum. mechanisms discussed above. Compar- organic substances which are covering ing the formation tendency of Al 2O3, MgO scrap, reaction of melt with silicon carbide • Aluminium Oxide – Al O 2 3 and Al 2MgO 4, magnesium offers a higher (heating elements or refractory material), Aluminium tends to oxidise in the presence driving force for oxidation. In combination reaction with graphite components (impel- of pure or bounded oxygen (e. g. water va- with the subsequent reaction to spinel, lers for gas purging treatments) and reac- pour, metal oxides) to aluminium oxide. In both types of magnesium oxides are most tion with carbon which comes along with common casthouse practice three main responsible for the input of non-metallic alloying elements (e. g. silicon). mechanisms for the formation of alumin- inclusions to the melt. The generation of ium oxide are known: MgO can also be caused by the vaporiza- • Silicates – SiO 2 tion of magnesium combined with a follow- The presence of little silicon dioxide par- Reaction with Atmospheric Oxygen ing oxidation [8]. ticles (< 5 µm) can be related to the Due to the fact that the contact between charged material and mostly as a product the melt and the surrounding air can hardly • Aluminium – Magnesium of erosion processes on refractory materi- be avoided in normal casthouse practice, mixed oxide (Spinel) – Al 2MgO 4 als. Due to their small sizes, they are not this oxidation mechanism is present per- The formation of Aluminium-Magnesium critical (they do not agglomerate according manently. Furthermore, this chemical re- mixed oxide spinel can happen according to their spherical shape). action is not only restricted to aluminium: to four different mechanisms [1,2]: Melt all oxygen-affine elements, like magne- Oxidation, Reaction of MgO with Al 2O3, sium, are reacting to their oxides: Reaction of Melt with Refractory Material and Reaction of Melt with Al 2O3. The first 2 Al (l) + 1½ O 2 (g) g-Al 2O3 (s) mechanism represents the main formation mechanism. During oxide formation within the melt/ air-layer on the bath surface, amorphous Spinel-formation can occur after the rip- oxide films are generated [3]. This modi- ping of the protective oxide layer on the fication is absolutely stable on dry air [4], bath surface, which leads to a direct con- however, on humid air the crystalline al- tact of aluminium and magnesium with lotrope g-Al 2O3 is formed after a certain oxygen from ambient air. The reaction can incubation time (5 to 10 min at 750 °C happen directly by oxidising the elements [5,6]). The incubation time is going to be reduced by increasing temperature, Mag- 2 Al (l) + Mg [Al] + 2 O 2 (g) Al 2MgO 4 (s) nesium content and humidity. or stepwise Reaction with Air Moisture This oxide formation mechanism is strong- Mg [Al] + ½ O 2 (g) MgO (s) ly dependent on ambient conditions and additionally causes a disposal of hydrogen. 2 Al (l) + MgO (s) + 3/2 O 2 (g) Al 2MgO 4 (s) 2 Al (l) + 3 H 2O (g) Al 2O3 (s) + 6 H (g) 2 Al (l) + 4 MgO (s) Al 2MgO 4 (s) + 3 Mg [Al] Reaction with Metal Oxides with or without a pure oxygen source. The reaction of aluminium with oxides is strongly driven by the oxygen affinity of • Aluminium Carbide – Al 4C3 the containing metal ion. If the affinity is Aluminium Carbides Al 4C3 usually come less than the one for aluminium (at 700 °C: along with primary aluminium. They are CaO > MgO > Al 2O3 > SiO 2 > all other produced in the Hall-Heroult process oxides [7]), the following reaction occurs: and cannot be fully removed by the metal treatment actions (gas purging treatment 2y/3 Al (l) + M xOy (s) y/3 Al 2O3 (s) + x M (s/l) or filtration). Other sources for carbide AluReport 10 Technology non-reacted refractory material reacted refractory material 100 µm Fig. 1: Refractory particles with reaction zones in a PreFil ® sample • Salts (Chlorides) – chloride. These are almost unstable, which NaCl, KCl, MgCl 2 leads to subsequent reactions [2]. Salt inclusions, especially magnesium chloride, are very critical regarding the fi- Input with Remelted Secondary nal product quality. This is based on the Aluminium fact that some chlorides are liquid at usual Secondary aluminium may contain little melt temperatures and therefore hardly amounts of chlorides due to the melting precipitate in the ceramic filtration unit. process with salt slags. The density of salt inclusions is between 2,0 and 2,16 g/cm 3, whereby they are Salt Treatment floating in the melt. Consequently, this Nowadays, salts with MgCl 2, KCl and NaCl separation mechanism is depending on as main components are used for melt size and therefore time. Therefore, qual- treatment actions instead of chlorine gas. ity problems may occur due to insufficient They are also used before furnace skim- dwell time in the in-line refining steps. The ming to reduce the quantity of metallic alu- formation of chlorides during melt treat- minium in dross. Due to the fact that salts ment generally happens by the reaction are in a liquid state at usual melt tempera- with chlorine. Otherwise, the the addi- tures, skimming actions have to be done tion of salts (additive) or impurities of the very carefully to ensure that no residues charged raw material can be sources for remain on the bath surface. salt inclusions. Slab casting pit Intermetallic Chlorination process During the chlorination process all ele- Inclusions ments with the affinity to chlorine gener- • Reacted and Non Reacted ate chlorides. The formation of aluminium Coarsely dispersed intermetallics are un- Refractory Material chloride is favoured due to the over- wanted inclusions and the formation mech- The applied refractory materials in the supply of chlorine. Since AlCl 3 is thermo- anisms are strongly dependent on the al- aluminium industry can be character- dynamically unstable in the presence of loy composition. Based on the chemical ised as alumina rich with contents of elements with a higher chlorine affinity, composition of alloy EN AW-7075, only 45 to 98 % Al 2O3 in the form of mullite the following subsequent reactions can titanium boride and chromium alumide can (Al 8[(O,OH,F)|(Si,Al)O 4]4) and/or corun- be observed [7]: occur. These inclusions represent hard and dum. The second main component is less ductile particles which above a critical silicon dioxide. As a reason of mechani- 3 Na [Al] + AlCl 3 (g) Al (l) + 3 NaCl (s) size can cause a significant reduction of cal and erosive loading, refractory material product quality. can get into the melt during the produc- 3 Mg [Al] + 2 AlCl 3 (g) 2 Al (l) + 3 MgCl 2 (l) tion process. After that, refractory material • Titanium Boride – TiB 2 reacts to spinel like inclusions with imple- 3 Ca [Al] + 2 AlCl 3 (g) 2 Al (l) + 3 CaCl 2 (s) As an essential component of the grain mented SiO2 phases.
Details
-
File Typepdf
-
Upload Time-
-
Content LanguagesEnglish
-
Upload UserAnonymous/Not logged-in
-
File Pages4 Page
-
File Size-