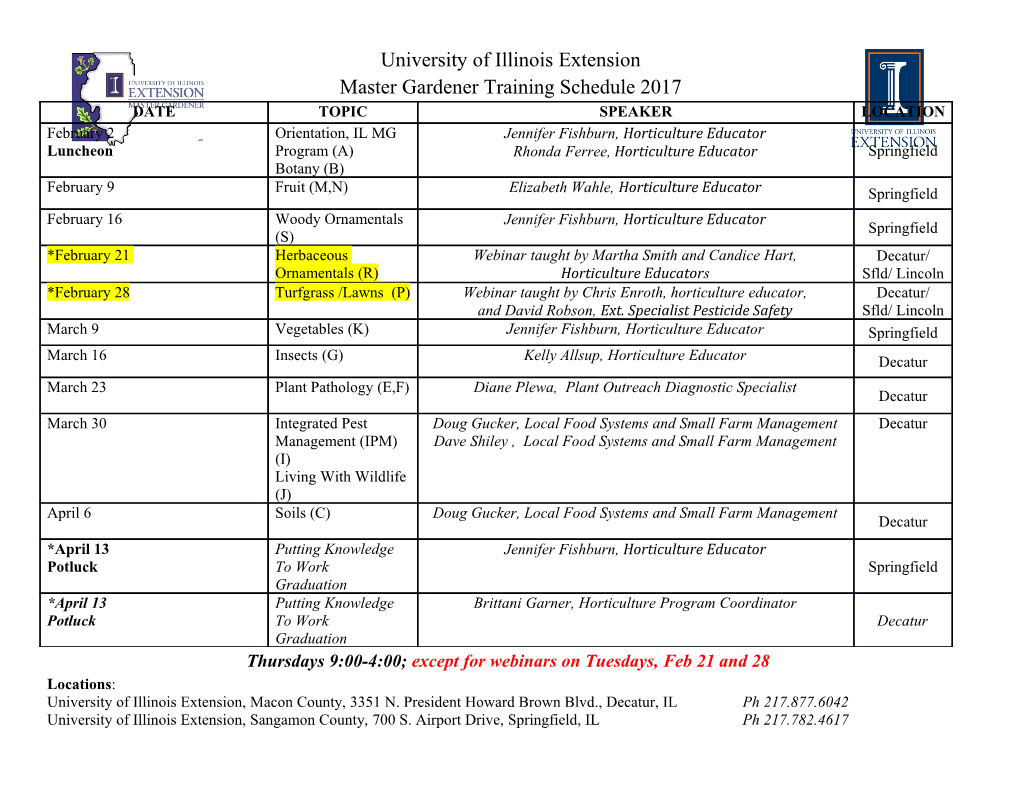
Chapter 4 Metal Matrix Composites Page .. .. ... ... .. .. ***********n”*’” ..... 99 Current Applications and Market Opportunities . .... 99 Longer Term Applications.. ● . .... ● .. 99 Research and Development Priorities . ... 99 Introduction ● ● ● ● ● ● ● ● ● . ● . ● ● ● ● ● ● . ● ● ● ● ● ● ● ● ● . ● ● ● .-. 100 Properties of Metal Matrix Composites ● ● ● ● . ● ● . ● . ● ● . 100 ● ● . 100 . Discontinuous Reinforcement . .’. Continuous Reinforcement ● . ... .. 102 MMC Properties Compared to Other Structural Materials . 102 Design,● Processing, and Testing . ,....., .*.. ...... 106 . Design . ● . ● ● ● . ● ● * ● ● * ● ● ● . .**.... ..*. ... ●☛✎✎✎✎✎ . 107 Processing. ● . * . ● ● . ● ● . ● ● ● . ● . ...,.. ● . 107 Costs. ● . ● ● .. ● , ● . ● ● ● ● ● ● . 110 . Testing . ● ● . ● ● . ● . ● ● ● ● ● ● . 111 Health and Safety . .. .... ● . 111 Applications.. ● . 112 Current Applications .. ....... ,.,.. ...... 112 Future Applications . .............. ... .*.*. 113 Markets . ● ... ● ... ● .... .... .... 115 Research and Development Priories . .... 115 Very Important.. .............. ● ☛✎✎☛✎✎ ✎ ✎ ✎ ✎ . .● 115. Important . ✎ ✎ ✎ ✎ ✎ ✎ ✎ ✎ ✎ ✎ ✎ . ...... 116 Desirable . ✎ ✎ ✎ ✎ ✎ ✎ ✎ ✎ ✎ ✎ ✎ . 117 Tables Table No. 4-1. Costs of a Representative Sample of MMC Reinforcements. ............101 4-2. Structural Properties of Representative MMCs, Compared to Other Materials . .. .. ... .............................103 4-3. Strength and Stiffness of Some Fiber-Reinforced MMCs. .. ....104 4-4. Properties of 6061 Aluminum Reinforced With Silicon Carbide Particulate .105 4-5. MMC Manufacturing Methods .. * . ...................108 4-6. Selected MMC Processing Techniques and Their Characteristics . ........109 i Chapter 4 Metal Matrix Composites FINDINGS Metal matrix composites (MMCs) usually con- 300,000 such pistons are produced and sold in sist of a low-density metal, such as aluminum or Japan annually. This development is very impor- magnesium, reinforced with particulate or fibers tant because it demonstrates that MMCs are at of a ceramic material, such as silicon carbide or least not prohibitively expensive for a very cost graphite. Compared with unreinforced metals, sensitive application. Other commercial applica- MMCs offer higher specific strength and stiffness, tions include cutting tools and circuit-breaker higher operating temperature, and greater wear contacts. resistance, as well as the opportunity to tailor these properties for a particular application. Longer Term Applications However, MMCs also have some disadvantages compared with metals. Chief among these are the Metal matrix composites with high specific stiff- higher cost of fabrication for high-performance ness and strength could be used in applications MMCs, and lower ductility and toughness. Pres- in which saving weight is an important factor. In- ently, MMCs tend to cluster around two extreme cluded in this category are robots, high-speed ma- types. One consists of very high performance chinery, and high-speed rotating shafts for ships composites reinforced with expensive continu- or land vehicles. Good wear resistance, along ous fibers and requiring expensive processing with high specific strength, also favors MMC use methods. The other consists of relatively low-cost in automotive engine and brake parts. Tailorable and low-performance composites reinforced with coefficient of thermal expansion and thermal con- relatively inexpensive particulate or fibers. The ductivity make them good candidates for lasers, cost of the first type is too high for any but mili- precision machinery, and electronic packaging. tary or space applications, whereas the cost/ben- However, the current level of development ef- efit advantages of the second type over unrein- fort appears to be inadequate to bring about com- forced metal alloys remain in doubt. mercialization of any of these in the next 5 years, with the possible exception of diesel engine Current Applications and Market pistons. Opportunities Based on information now in the public do- main, the following military applications for Current markets for MMCs are primarily in mil- MMCs appear attractive: high-temperature fighter itary and aerospace applications. Experimental aircraft engines and structures; high-temperature MMC components have been developed for use missile structures; and spacecraft structures. Test- in aircraft, satellites, jet engines, missiles, and the ing of a National Aerospace Plane (NASP) pro- National Aeronautics and Space Administration totype is scheduled for the early to mid 1990s, (NASA) space shuttle. The first production appli- which might be too early to include MMCs. How- cation of a particulate-reinforced MMC in the ever, it may be possible to incorporate MMCs in United States is a set of covers for a missile guid- the structure or engines of the production vehicle. ance system. The most important commercial application to Research and Development Priorities date is the MMC diesel engine piston made by Toyota. This composite piston offers better wear MMCs are just beginning to be used in produc- resistance and high-temperature strength than the tion applications. In order to make present ma- cast iron piston it replaced. It is estimated that terials more commercially attractive, and to de- 99 100 . Advanced Materials by Design velop better materials, the following research and cost fiber reinforcements is a major need. development priorities should receive attention: Continued development work on existing materials is important to lower costs as well. ● Cheaper Processes: To develop low-cost, ● Coatings: Research in the area of reinforce- highly reliable manufacturing processes, re- ment/matrix interface coatings is necessary. search should concentrate on optimizing These coatings can prevent deleterious chem- and evaluating processes such as plasma ical reactions between matrix and reinforce- spraying, powder metallurgy processes, ment which weaken the composite, particu- modified casting techniques, liquid metal in- larly at high temperature, and optimize the filtration and diffusion bonding. interracial fiber/matrix bond. ● Cheaper Materials: Development of Iower INTRODUCTION Metal matrix composites (MMCs) generally in dramatic improvements in MMC properties, consist of lightweight metal alloys of aluminum, but costs remain high. Continuously and discon- magnesium, or titanium, reinforced with ceramic tinuously reinforced MMCs have very different particulate, whiskers, or fibers.1 The reinforce- applications, and will be treated separately ment is very important because it determines the throughout this chapter. mechanical properties, cost, and performance of Tailorability is a key advantage of all types of a given composite. composites, but is particularly so in the case of Composites reinforced with particulate (dis- MMCs. MMCs can be designed to fulfill require- continuous types of reinforcement) can have ments that no other materials, including other ad- costs comparable to unreinforced metals, with vanced materials, can achieve. There are a num- significantly better hardness, and somewhat bet- ber of niche applications in aerospace structures ter stiffness and strength. Continuous reinforce- and electronics that capitalize on this advantage. ment (long fiber or wire reinforcement) can result PROPERTIES OF METAL MATRIX COMPOSITES There are considerable differences in published Property data given in this chapter are therefore property data for MMCs. This is partly due to the given as ranges rather than as single values. fact that there are no industry standards for Some MMC properties cannot be measured as MMCs, as there are for metals. Reinforcements they would be for monolithic metals. For in- and composites are typically made by proprie- stance, toughness is an important but hard-to- tary processes, and, as a consequence, the prop- define material property. Standard fracture me- erties of materials having the same nominal com- chanics tests and analytical methods for metals position can be radically different. The issue is are based on the assumption of self-similar crack further clouded by the fact that many reinforce- extension; i.e., a crack will simply lengthen with- ments and MMCs are still in the developmental out changing shape. Composites, however, are stage, and are continually being refined. Numer- non homogeneous materials with complex inter- ous test methods are used throughout the indus- nal damage patterns. As a result, the applicabil- try, and it is widely recognized that this is a ma- ity of conventional fracture mechanics to MMCs jor source of differences in reported properties.2 is controversial, especially for fiber-reinforced ma- 1 As used i n this chapter, the terms 1‘al u m inu m, ‘‘magnesium, ” terials. and “titanium” denote alloys of these materials used as matrix metals. ~Carl Zweben, “Metal Matrix Composites, ” contractor report for OTA, January 1987. — Ch. 4—Metal Matrix Composites ● 101 Table 4-1 .—Costs of a Representative Sample of MMC Reinforcements Reinforcement Price ($/pound) Alumina-silica fiber. 1 Silicon carbide particulate . 3 a Silicon carbide whisker . 95 Alumina fiber (FP) . 200 Boron fiber. $262 Graphite fiber (P-100) . 950a Higher performance reinforcements (e.g., graphite and boron fibers) have sig- nificantly higher costs as well. aJoseph Dolowy, personal communication, DWA Composite Specialties, Inc., JuIy 1987. SOURCE: Carl Zweben, “Metal Matrix Composites, ” contractor report for OTA, January 1987. In terms of tailorability, a very important
Details
-
File Typepdf
-
Upload Time-
-
Content LanguagesEnglish
-
Upload UserAnonymous/Not logged-in
-
File Pages21 Page
-
File Size-