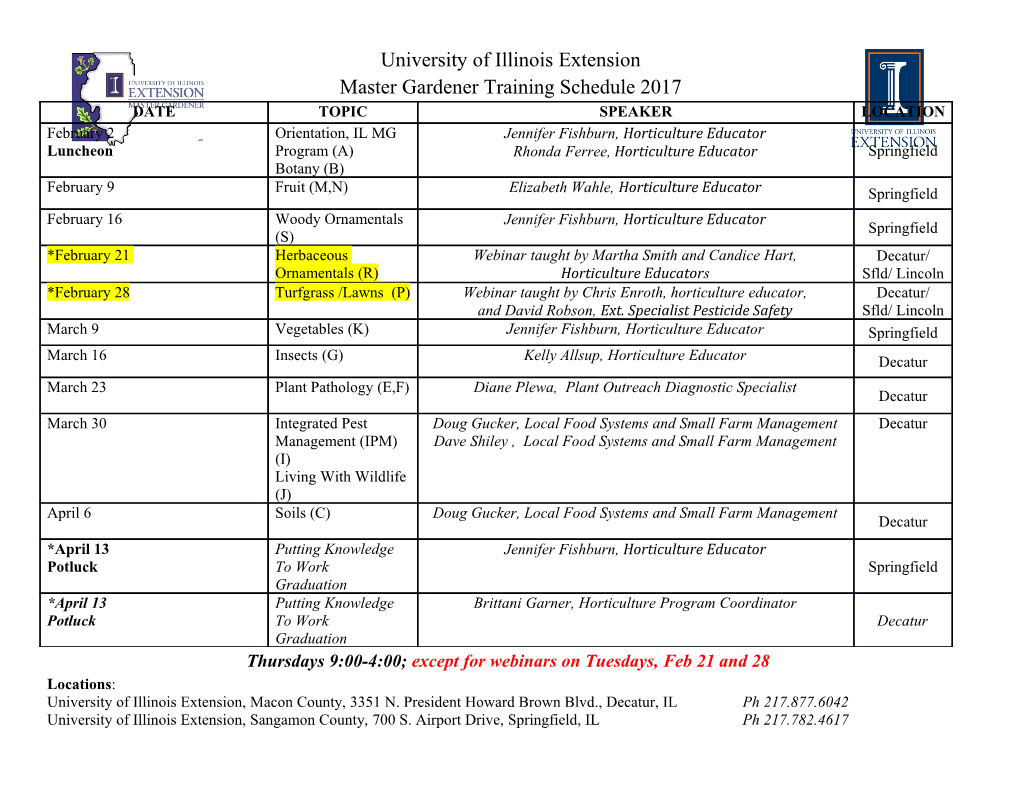
Algae Biorefinery Development for Biofuels and Bioproducts Lieve Laurens Bioenergy 2016 Washington, DC July 14, 2016 Algae-derived Commercial Products Reduce cost of algal biofuels: • Harness unique position of algae as highly efficient photosynthetic cell factories • Identify key targets to contribute to lowering the overall cost of algal biofuels production • Quantify impact of major components supporting a multi-product algal biorefinery model • Analogous to replacing the whole barrel paradigm; low volume product streams can provide large fraction of value • Integrate biomass composition with cultivation and conversion performance 2 *Davis *Davis + Co $491/ton* cost: production Biomass Polyunsaturated 3. 2. 1. Co Carbohydrate monomers Carbohydrate Algae as Photosynthetic Chemical Factories Chemical as Photosynthetic Algae et al et - - products biomass value $500 value biomass products Biomass components product criteria for commercial success commercial for criteria product performance unique with functional material New Functionally identical chemical an existing to Identical Whole biomass Whole Antioxidants Triglycerides 2016: Glycerol Phytol http:// fatty acids fatty www.nrel.gov ) l 50 a t o t 40 (including ethanol and di and ethanol (including Epoxies, Epoxies, Biopolymers, coatings, Rubber coatings, Biopolymers, % ( Di e S 30 l i Fermentation products Fermentation - urfactants, fuel additive fuel urfactants, /docs/fy16osti/64772.pdf f Health food additives food Health acids o r Food/feed markets Food/feed 20 p E polyols - $800/ton 10 M / nylon production nylon / A Product F 0 ) l a t 0 0 7 0 9 6 3 6 6 3 , . o n n n n n n n t 4 6 8 nutraceuticals 40 1 1 2 3 3 4 5 1 1 . 1 . % 6 8 8 8 8 0 0 C C C ( 1 1 1 1 1 2 2 30 e C C C C C C C l i f o r 20 - p : acids) E 10 M A F 0 35 0 0 7 0 9 6 3 6 6 3 . n n n n n n n 6 8 50 4 1 2 3 3 4 5 30 1 1 1 . 1 . 6 8 8 8 8 0 0 C C C 1 1 1 1 2 2 4025 1 C C C C C C 20 C 30 15 2010 105 FAME profile (% total) 0 FAME profile (% total) 0 ) l EPA a t o t 40 C14.0 C16.0 C18.0 % C14.0 C16.0 C18.0 ( C16.1n7 C18.1n9 C18.2n6 C18.3n3 C18.3n6 C20.4n6 C20.5n3 C20:5 30 e C16.1n7 C18.1n9 C18.2n6 C18.3n3 C18.3n6 C20.4n6 C20.5n3 l i f o r 20 p E 10 M A n F 3 fatty acid fatty 3 0 ) l 35 0 0 7 0 9 6 3 6 6 3 a . t n n n n n n n 4 6 8 o 1 1 2 3 3 4 5 t 30 1 1 . 1 . 6 8 8 8 8 0 0 C C C % 1 1 1 1 1 2 25 2 ( C C C C C C C e l 20 i f o r 3 15 p 10 E M 5 A F 0 0 0 7 0 9 6 3 6 6 3 . n n n n n n n 4 6 8 1 1 2 3 3 4 5 1 1 . 1 . 6 8 8 8 8 0 0 C C C 1 1 1 1 1 2 2 C C C C C C C Algal Biorefinery 4 Algae Biorefinery Potential – high volume products Biomass components wt % Product Market* (ton/yr) Fatty acids 10-45 Hydrocarbon fuel products (U.S. consumption) 16,000,000 8,000,000 – Omega-3-fatty acids 3-10 Polyols – epoxy resin – polyurethane 11,000,000 3-10 Nutraceuticals 22,000 Hydroxy-, branched-, fatty acids/alcohols ~1 Surfactants, fuel additives 3,500,000 Sterols 2-4 Surfactants 6,400,000 2-4 Phytosterol nutra-/pharmaceuticals 25,000 2-4 Emulsifiers N/A Phytol 3-4 Raw material for vitamin E, fragrance, soaps… 1 3-4 Surfactants, fuel additives 3,500,000 Polar lipids 10-35 Ethanolamine 600,000 Phosphatidylcholine, phosphoinositol and 10-35 20,000-30,000 phosphatidyl ethanolamine (lecithin ) Glycerol 2-6 Di-acids for nylon production 2,500,000 2-6 Feed, pharmaceuticals 25,000 Fermentable sugars (glucose, mannose) 10-45 Polylactic acid (PLA) polymers 300,000 10-45 Di-acids (e.g. succinic, muconic, adipic acid) 2,500,000 10-45 Ethanol 60,000,000 Mannitol 3-6 Polyether polyols 2,300,000¶ Alginate ~3-5 Alginate additives N/A Starch 5-40 Polysaccharide-derived bioplastics 2,000,000 Protein 19-40 Thermoplastics 5,000,000 Amino acids/peptides 19-20 Polyurethane 11,000,000 Amino acids/peptides 19-20 Biobutanol, mixed alcohol fuels 740,000 16,000,000 – Whole biomass 100 Animal/Fish feed 190,000,000 * Market size estimated based on displacement volumes ¶ based on sorbitol market size 5 5 Potential Options for co-Products 6 Algal Biorefinery Process Fuels Only Solvent recovery Naphta CO2 Flocculant Nutrients Diesel Fresh/marine Jet wastewater DAF SLS * Upgrading Extrac on Dis lla on Water/Nutrient recycle AD ** Return CO2 Co-production of Fuels and Chemicals Ethanol Naphta Solvent recovery Flocculant Product Diesel purifica on Jet DAF SLS Pretreatment Upgrading Fermenta on Extrac on Dis lla on Water/Nutrient recycle AD Return CO2 Davis et al 2014: www.nrel.gov/docs/fy14osti/62368.pdf Laurens, L. et al., 2015, Green Chemistry, 2015, 17, 1145-1158 Dong, T., et al., 2016. Algal Research, doi:10.1016/j.algal.2015.12.021 NREL Pilot Plant 7 Algae Biorefinery Ethanol • “Whole cell” fractionation after Naphta Solvent recovery acid pretreatmentFuel Only Flocculant Product Diesel purifica on • Techno-economic$19.80/GGEJet analysis (TEA) based on pilot scale data to show SLS DAF progress, cost reduction and Pretreatment Upgrading Fermenta on Extrac on Disreduced lla on risk AD Water/Nutrient recycle Fuel Yield + ethanol Return CO from sugars 2 Lipids (% DW) 27 $19.80/GGE Diesel Fuel Energy (103 btu/ton) 8,671 Fermentable Sugars (% DW) 48 Ethanol (gallon/ton) 79 Gasoline Fuel Energy (103 6,040 btu/ton) Combined Energy (103 btu/ton) 15,693 Davis et al 2014: www.nrel.gov/docs/fy14osti/62368.pdf Total Gasoline Gallon Equivalent Laurens, L. et al., 2015, Green Chemistry, 2015,135 17, 1145-1158 perDong, ton T., etbiomass al., 2016. (GGE/ton) Algal Research, doi:10.1016/j.algal.2015.12.021 8 Figure ES-1. Economic summary for ALU pathway v Value Proposition – Focus on co-Products *Based on mid-harvest Scenedesmus biomass and IHS Chemical Economics Handbook, Epoxy Resins, May 2014 & demonstrated composition Surfactants, Household Detergents and their raw materials, June 2013 R. Davis (NREL) preliminary unpublished report 9 Summary • Inclusion of co-products in algal biorefinery processes improves overall economics – 30% reduction in Fuel Selling Price • Value-added co-products are natively produced in photosynthetic algal cell factories • Novel products may support novel conversion process pathways including co-product development alongside fuels • Biomass composition drives conversion efficiency parameters and is highly linked with cultivation • Future R&D to support advanced algal systems economics based on the isolation and commercial harnessing of high-value, large market bioproducts and mapping over cultivation 10 Thank You! [email protected] Integration of Composition with Cultivation Nannochloropsis ASU CalPoly TRL Lipids (FAME) 60 Carbohydrates Protein ASU CalPoly Cellana ASU GT CalPoly TRL CellanaASU CGTalPoly CellanaTRL GT TRL 20 50 30 factor(Pond) 15 40 factor(Pond) factor(Pond) 40 0 factor(Pond) 0 1 0 0 1 1 1 20 2 2 2 2 3 3 3 3 4 4 4 4 5 5 Percent Percent WeightDry 5 Percent Percent WeightDry Percent DryWeight 10 5 6 6 30 6 10 EPA content(C20:5n3) 20 6 Inoculum 0 High N 5 Oct 15 Nov 01Nov 15 Dec 01 Oct 15 Nov 01Nov 15 Dec 01 Oct 15 NoOvct 01No 15v No15v De 01Noc 01v O ct15 15 De Noc v01 01NoOctv 1515 De Noc 01v 01No Oct 15v 15 Nov De01Noc 01v 15 O Dect c15 01Oct No 15v 01No Nov 01Nov 15v De15c De 01c 01 OctO 15ct 15 No Nov 01Nov 01Novv 15 15 De Decc 01 Octct 15 15 No Nov v01No 01Nov 15v 15 De Dec 01c O01ct 15 Nov 01Nov 15 Dec 01 Oct 15 Nov 01Nov 15 Dec 01 Harvest Date Harve0st Date Harvest Date Oct 15 Nov 01Nov 15 Dec 01 Oct 15 Nov 01Nov 15 Dec 01 Oct 15 Nov 01Nov 15 Dec 01 Low N Harvest Date 12.
Details
-
File Typepdf
-
Upload Time-
-
Content LanguagesEnglish
-
Upload UserAnonymous/Not logged-in
-
File Pages12 Page
-
File Size-