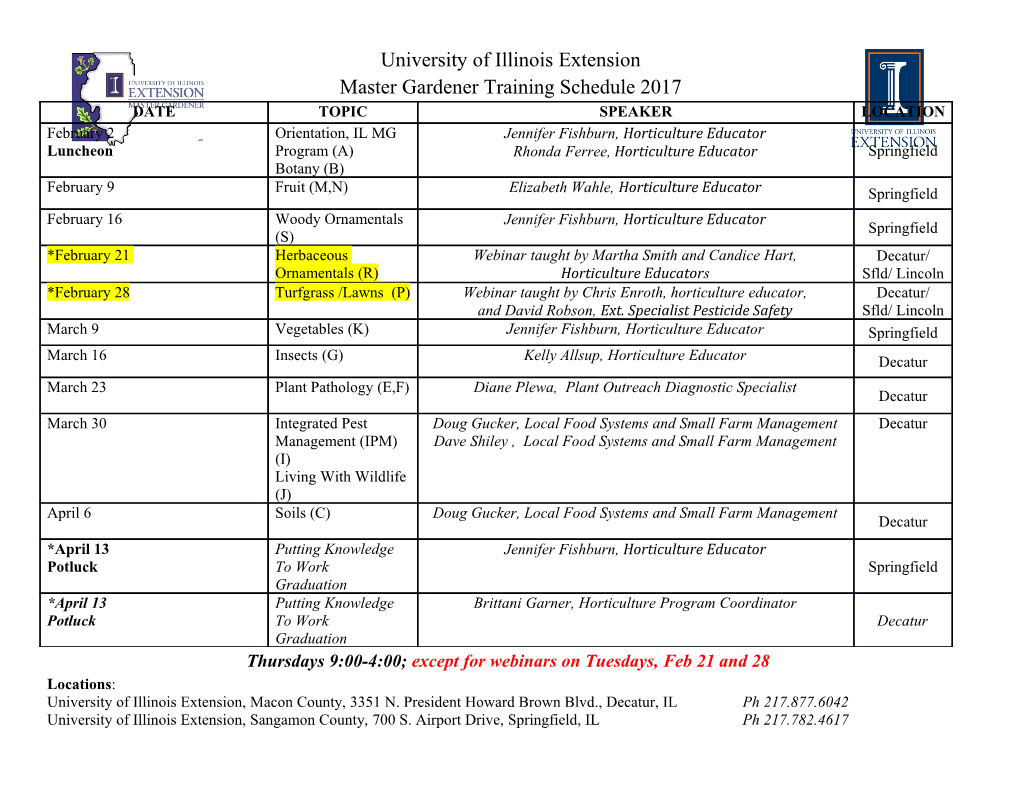
Experience of indirect cofiring of biomass and coal Rohan Fernando CCC/64 October 2002 Copyright © IEA Clean Coal Centre ISBN 92-9029-370-9 Abstract There has been increasing interest in the use of biomass for power generation in recent years. The principal reason for this is that the use of biomass can significantly reduce net CO2 emissions. Other advantages of utilising biomass are that it diversifies the power plant’s fuel portfolio, it can lead to reductions in SO2 and NOx emissions and that such use can help to dispose of a solid waste. There are some disadvantages of firing biomass which relate to its supply, transportation and composition and these can be reduced if the biomass is cofired with coal. Cofiring can be direct, where the biomass and coal are fired in the same boiler, or indirect, where the combustion or gasification of biomass occurs in a separate unit. This report concentrates on indirect cofiring which is taken to mean technologies in which the ash from the coal and biomass are kept separate. Direct cofiring is relatively straightforward but can lead to several technical concerns. Indirect cofiring incurs greater costs and is particularly suitable for biomass containing troublesome components or when the quality of the ash is of importance. Indirect cofiring is less common than direct cofiring. The report discusses the relative advantages and disadvantages of direct and indirect cofiring. It then describes the following plants which indirectly cofire biomass: Aabenraa in Denmark, Amergas in the Netherlands, Avedøre 2 in Denmark, Kymijärvi in Finland, Zeltweg in Austria and Västerås in Sweden. Acronyms and abbreviations BFB bubbling fluidised bed CFB circulating fluidised bed CFBC circulating fluidised bed combustion ESP electrostatic precipitator FBC fluidised bed combustion LHV lower heating value Mtoe million tonnes oil equivalent MWe megawatts electric MWth megawatts thermal pc pulverised coal PF pulverised fuel ppm parts per million ppmw parts per million by weight REF recycled fuel SCR selective catalytic reduction SNCR selective non-catalytic reduction USC ultra-supercritical 2 IEA CLEAN COAL CENTRE Contents 1 Introduction 5 2 Biomass cofiring 7 2.1 Direct cofiring 7 2.2 Indirect cofiring 11 2.3 Advanced biomass reburning 15 3 Indirect cofiring plant 17 3.1 Aabenraa 17 3.2 Amergas 19 3.3 Avedøre 2 21 3.3.1 Multifuel design 21 3.3.2 USC unit 23 3.3.3 Steam turbine 23 3.3.4 Gas turbine plant 25 3.3.5 Biomass plant 25 3.4 Kymijärvi 26 3.4.1 Gasifier 26 3.4.2 Fuels 27 3.4.3 Operating experience 28 3.5 Zeltweg 29 3.5.1 BioCoComb technology 30 3.5.2 Fuels 30 3.5.3 Gasifier 31 3.5.4 Boiler operation 32 3.6 Västerås 33 3.6.1 Biomass boiler 33 3.6.2 Connection with existing plant 34 3.6.3 Water chemistry 34 3.6.4 Feed water pumps and heaters 34 3.6.5 Steam connections 34 3.6.6 Boiler operation 34 4 Conclusions 36 5 References 38 Experience of indirect cofiring of biomass and coal 3 4 IEA CLEAN COAL CENTRE 1 Introduction There has been increasing interest in the use of biomass for a) The world power generation in recent years. This has been due to nuclear 5% hydro 6% several reasons, the principal one being that the utilisation of biomass can significantly reduce net CO2 emissions. The other advantages of the use of biomass include the fact that it oil 33% diversifies the power plant’s fuel portfolio by adding a biomass 13% potentially less expensive non-fossil fuel. Furthermore biomass firing can reduce NOx and SO2 emissions and it helps to dispose of a solid waste that would otherwise need to be landfilled. However, there are some disadvantages of utilising biomass which relate to its supply, transportation and composition but these can be reduced if the biomass is cofired with coal. Issues which arise when waste, including gas 19% biomass, is cofired with coal have been discussed by coal 24% Davidson (1999). Cofiring can be direct, where the biomass and coal are fired in the same boiler, or indirect, where the Total 386 EJ, 9206 Mtoe combustion or gasification of the biomass occurs in a Population: 5.3 billion separate unit. This report describes indirect cofiring which is taken to mean technologies in which the ash from the coal and biomass are kept separate. b) Industrialised countries nuclear 8% Typical biomass fuels used for power generation include hydro 6% gas 24% wood-based fuels such as wood chips, sawdust and bark; biomass 3% agricultural wastes such as straw and rice husks; sludges from paper mills and municipal sludges. Though residue fuels can provide an important initial feedstock for the bio- energy industry, large-scale energy production from biomass will need to rely on energy crops such as sugar cane, rapeseed and short rotation forestry. Approximately 13% of world energy demand is met by biomass which is fired at a rate of about 1200 Mtoe (millions tonnes of oil equivalent) per annum as shown in Figure 1. Whereas biomass is the largest energy source (33%) in developing countries, it oil 36% coal 23% represents only 3% of energy consumption in industrialised countries. In the United States 4% of primary energy is Total 257 EJ, 6131 Mtoe (67%) produced by biomass whereas the corresponding figures in Population: 1.3 billion (25%) Finland and Sweden are 21% and 17% as the latter two countries have large forest-based pulp and paper industries (Swanekamp, 1995; Engström, 2000). The European c) Developing countries Parliament has set targets for Member States that biofuels hydro 6% nuclear 1% should account for 2% of fuels sold by December 2005 and gas 8% 5.75% by 2010 (Cordis Focus, 2002). biomass 33% The drawbacks to using biomass for power generation include the fact that in many countries the supply of biomass is widely dispersed and there may not be an established infrastructure for harvesting and transporting it to the power plant. The seasonal nature of biomass raises further oil 25% complications. It is readily available during harvesting but scarce during cultivation and growth. The composition of biomass is very different from coal as shown in Table 1 which compares hard coal and brown coal with several coal 27% biofuels. Biomass can contain much higher moisture levels, up to 50%, which can adversely affect combustion by Total 129 EJ, 3074 Mtoe (33%) absorbing heat during evaporation. Its heating value is also Population: 4.0 billion (75%) significantly lower than coal. Moreover, its bulk density is much less than coal hence a greater quantity of fuel needs to Figure 1 Primary energy consumption (1990) be collected, handled, transported and stored. The costs (Engström, 2000) Experience of indirect cofiring of biomass and coal 5 Introduction Table 1 Fuel analysis of coals and selected supplementary fuels (Hein and Scheurer, 2000) dried sewage hard coal brown coal wood straw RDF sludge LHV, raw, MJ/kg 28 9 12.4 15 23.5 10.6 moisture, raw, % 5.1 50.4 33 10.6 4.1 3 volatile matter, dry, % 34.7 52.1 83.2 74.4 82.6 49.5 ash, dry, % 8.3 5.1 0.34 6.1 12.2 45.1 Fixed C, dry, % 57.1 42.8 16.5 19.9 5.2 2.4 C, dry, % 72.5 65.9 48.7 47.4 56.8 25.0 H, dry, % 5.6 4.9 5.7 4.5 7.9 4.9 N, dry, % 1.3 0.69 0.13 0.4-0.78 0.74 3.2 S, dry, % 0.94 0.39 0.05 0.05-0.11 0.25 1.1 Cl, dry, % 0.13 <0.1 <0.1 0.4-0.73 0.82 <0.1 O, dry, % 11.1 23 45 40.4 21.3 17.7 ash fusion temperature, °C 1250 1050 1200 850 1120 1200 associated with these activities mean that large biomass power plants (>300 MWe) are impractical. The smaller plant size and the lower fuel heat contents result in biomass plant being inefficient compared with coal-fired plant. Existing biomass fired plant in the USA have heat rates in the range 14–21 MJ/kWh compared to 9.5–14 MJ/kWh for coal-fired plant. However, if the biomass cost is very low, the efficiency may not be a key economic criterion. Other technical issues can also arise. For example, the use of some biofuels such as switchgrass can lead to increased slagging and fouling on boiler surfaces. Biofuels containing high chlorine levels such as straw can cause corrosion. Fly ash resulting from biomass firing does not always meet the requisite standards and this can reduce fly ash marketability (Paul and Maronde, 2001). This report describes the indirect cofiring of biomass and coal in hybrid plant. Indirect cofiring is much less common than direct cofiring. The plants which are described are: ● Aabenraa in Denmark; ● Amergas in the Netherlands; ● Avedøre 2 in Denmark; ● Kymijärvi in Finland; ● Zeltweg in Austria; ● Västerås in Sweden. For each of these, the design of the plant is described. What modifications were needed to allow the plant to fire biomass are discussed. The types of biomass fired and the operational issues that have arisen during biomass firing are included. Though the report concentrates on indirect cofiring technologies, the relative advantages and disadvantages of direct and indirect cofiring will first be considered. 6 IEA CLEAN COAL CENTRE 2 Biomass cofiring Cofiring biomass with coal has the potential to overcome around 50 $/kW for cyclone or fluidised bed boilers that some of the drawbacks of firing pure biomass.
Details
-
File Typepdf
-
Upload Time-
-
Content LanguagesEnglish
-
Upload UserAnonymous/Not logged-in
-
File Pages40 Page
-
File Size-