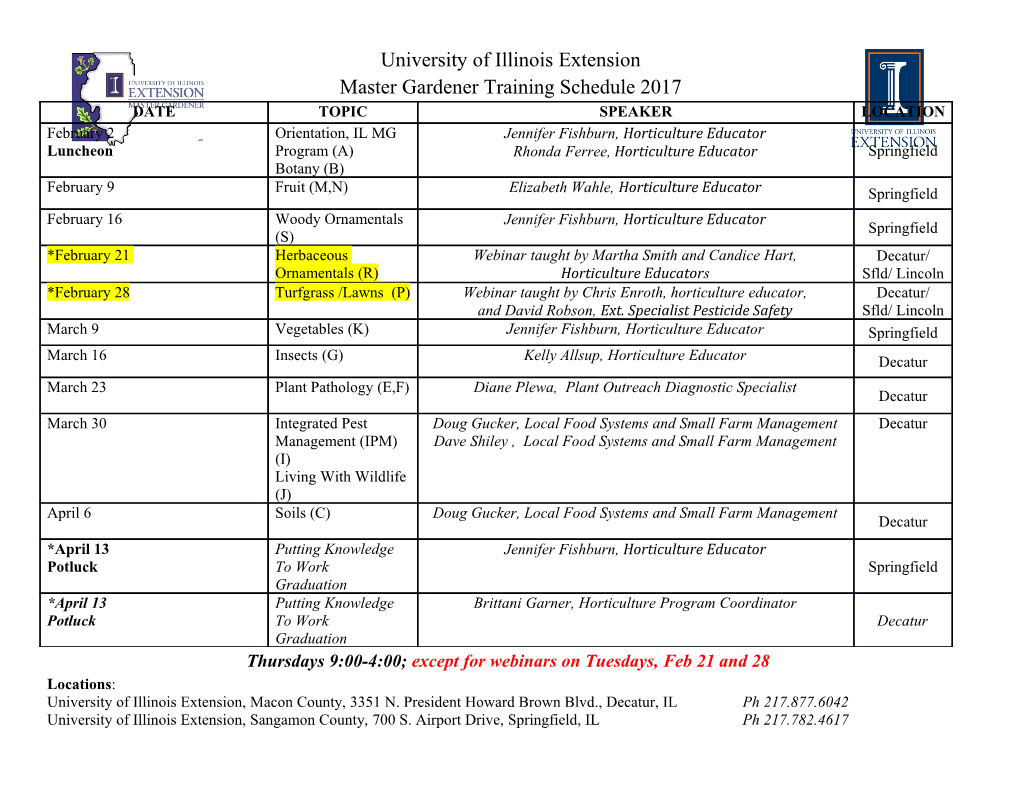
ME477 Fall 2004 Introduction • Metal Forming uses plastic deformation to Fundamentals of Metal change the shape of metal workpieces – Materials (metals) – plastic deformation Forming – External loads – Typically compressive • Sometimes Stretch the metal (tensile), bend the metal 1. Overview (tensile and compressive), shear stresses 2. Material Behavior – Shape - die and tools 3. Temperature Effects • Classification 4. Strain Rate Effect – Bulk Deformation 5. Friction and Lubrication – Sheet Metal Forming – High surface area-to-volume ratio • Parts are called stampings • Usual tooling: punch and die 1 2 Material Properties in Metal Introduction F F Forming v • Bulk Deformation + v Process • Desirable material properties: – Rolling + – Yield strength ? F – Forging – Ductility ? v – Extrusion F – Second phase or Inclusion ? – Drawing RAM F • These properties are affected by temperature: • Sheet metal forming v – When work temperature is raised, ductility increases – Bending and yield strength decreases while loosing on surface finish and dimension accuracy. – Drawing • Other factors: – Shearing – Strain rate and friction – (Stamping) 3 4 Theories of Failure Yielding: Ductile Materials • The limit of the stress state on a material A. Maximum Shear Stress Theory (Tresca Criterion) – Ductile Materials - Yielding S y In a tension specimen: τ = τmax – Brittle Materials - Fracture max 2 • In a tensile test, Yield or Failure Strength of a material. The diameter of the Mohr circle = Sy Sy • In a multiaxial state of stress, how do we For Plane Stress: σ1 = S y σ , σ have same signs. use Yield or Failure Strength? (σ3=0) 1 2 σ 2 = S y σ1 −σ 2 = S y σ1, σ2 have opposite signs. 5 6 Kwon 1 ME477 Fall 2004 Ductile Materials Problem #1 B. Maximum Distortion Energy Theory (von Mises Criterion) d =100mm P 1.5(103 ) σ y =170MPa σ = − = − = −1.91MPa For the three principal stresses; A 7.85(10−3 ) 1 1 2 2 2 3.056 Tc 600(0.05) u = []σ1ε1 +σ 2ε 2 +σ 3ε 3 = []σ1 +σ 2 +σ 3 − 2ν ()σ1σ 2 +σ 3σ 2 +σ1σ 3 600Nm 1.91 τ = = = 3.056MPa 2 2E J 4.9087(10−6 ) After taken out the hydrostatic stress (σ =(σ +σ +σ )/3) σ ,σ = −0.955 ± 3.202 ave 1 2 3 15kN 1 2 = 2.247 and − 4.156MPa Now substitute σ , σ and σ with()()σ1 −σ ave , σ 2 −σ ave ,(σ 3 −σ ave ) 1 2 3 σ 2 −σ σ +σ 2 = 2.252 − 2.245*(−4.16) + 4.162 = 31.73MPa << σ 2 1+ν 1 1 2 2 Y u = σ 2 −σ σ +σ 2 For plane stress; d []1 1 2 2 σ σ1=σ2 3E σ 2 2 2 2 170 1 +ν 2 R = 0.955 + 3.056 = 3.202 u d = S y in an uniaxial tension test. 3E 2.247 −.191 In a biaxial case, the same amount of distortion energy A C = = −0.0955 -170 170 σ 1+ν 2 2 1+ν 2 2 1 []σ1 −σ1σ 2 +σ 2 = S y σ 4.156 3E 3E 1 2 2 2 7 8 σ1 −σ1σ 2 +σ 2 = S y B -170 Stresses in 3D Plasticity y ⎡σ11 σ 21 σ 31 ⎤ ⎡σ x τ yx τ zx ⎤ ⎢ ⎥ • Flow theory (Classical theory) []σ = ⎢σ σ σ ⎥ = τ σ τ ij ⎢ 12 22 32 ⎥ ⎢ xy y zy ⎥ – The current strain rates depend on the stress. ⎢σ σ σ ⎥ ⎢τ τ σ ⎥ x ⎣ 13 23 33 ⎦ ⎣ xz yz z ⎦ • Deformation theory (Hencky theory) z ⎡ 5 − 1 − 1⎤ ⎢ ⎥ – The total strain is related to the stress. To find Principal Stresses: []σ = − 1 4 0 MPa ij ⎢ ⎥ – Ideal for nonlinear elasticity ⎣⎢− 1 0 4 ⎦⎥ – Still work for monotonically increasing stresses 5 − σ − 1 − 1 n ⎡ 1 ⎤ everywhere in a body − 1 4 − σ 0 ⎢n ⎥ = 0 ⎢ 2 ⎥ • Pressure-independent – Hydrostatic pressure − 1 0 4 − σ ⎣⎢n3 ⎦⎥ 2 does not affect dislocation motion. ()()()()5 − σ 4 − σ − 4 − σ − 4 − σ = ()()()4 − σ []5 − σ 4 − σ − 2 = ()()()4 − σ 3 − σ 6 − σ = 0 • Bauschinger effect σ 1 = 3MPa – The different behaviors in tension and compression σ 2 = 4 MPa and 9 10 σ 3 = 6MPa Yield function in 3D Plasticity 3 Stress Tensor : [σ ij ]= [σ `ij −σ mδij ] S`Y 2 where σ ` = DeviatoricStress Tensor, ij SY Bauschinger effect 1 σ m = ()σ1 +σ 2 +σ 3 = Hydrostatic Component of Stress 3 SY δij =1 for i = j Isotropic hardening Three Stress Invariants 0 for i ≠ j Three Deviatoric Stress Invariants σ 3 − I σ 2 − I σ − I = 0 1 2 3 σ '3 −J σ '2 −J σ '−J = 0 1 2 3 S<S where I1 = σ x +σ y +σ z = σ1 +σ 2 +σ 3 Y where J1 = 0 1 I = −()σ σ +σ σ +σ σ +τ 2 +τ 2 +τ 2 2 x y y z x z xy yz zx J = − σ ' σ ' +σ ' σ ' +σ ' σ ' 2 ()1 2 3 2 3 1 Maximum Distortion Energy Theory = − σ σ +σ σ +σ σ ()1 2 3 2 3 1 J = σ ' σ ' σ ' 2 3 x y z f ()J , J = J = k = C 2 2 2 2 3 2 I3 = σ xσ yσ z + 2τ xyτ yzτ xz −σ xτ yz −σ yτ xz −σ zτ xy ∂f 1 2 2 2 Loading: f ()σ ij = C, df = σ ij > 0 J 2 = []()()()σ1 −σ 2 + σ 2 −σ 3 + σ 3 −σ1 ∂σ ij = σ1σ 2σ 3 6 ∂f Based on uniaxial yielding σ1 = SY ,σ 2 = σ 3 = 0 Yield function: f (σ ij )= f ()σ I = f (I1, I2 , I3 )= f (J 2 , J3 )= C Unloading: f ()σ = C, df = σ < 0 ij ∂σ ij ij 1 For example, Max. Shear Stress Theory can be represented ()S 2 + S 2 = k 2 Neutral: ∂f 6 Y Y 3 2 2 2 4 6 f ()σ ij = C, df = σ ij = 0 f ()J 2 , J3 − C = 4J 2 − 27J3 − 36k J 2 + 96k J 2 − 64k = 0 ∂σ ij 11 SY = 3k 12 f ()σ I = σ1 −σ 3 = C Kwon 2 ME477 Fall 2004 Strain Hardening 2. Behavior in Metal Forming Isotropic Hardening Kinematic Hardening • The stress-strain relationship beyond elastic range assuming no unloading at anytime and anywhere. σ = Kε n • Flow stress – The instantaneous value of stress required to continue deforming the material. Y = Kε n Convexity f Normality Rule: ∂f dε ij = dλ Kε n ∂σ ij • Average Flow Stress f Yf Yf = 1+ n Yf Y • For any metal, K and n in s the flow curve depend on temperature ε 13 f 14 Combined Hardening General Hardening 3. Temperature in Metal Warm Working Forming • Cold Working – Performed at room • Performed at above room temperature but below temperature or slightly above recrystallization temperature – Near net shape or net shape • 0.3Tm, where Tm = melting point (absolute – Better accuracy, closer tolerances & surface finish temperature) – Strain hardening increases strength and hardness – Lower forces and power than in cold working – Grain flow during deformation can cause desirable – More intricate work geometries possible directional properties in product – Need for annealing may be reduced or eliminated – No heating of work required • Isothermal Forming – eliminate surface cooling – Higher forces and power required especially highly alloyed steels and Ti and Ni – Surfaces must be free of scale and dirt alloys – Ductility and strain hardening limit the amount of forming 15 16 Hot Working 4. Effect of Strain Rate • Deformation process at temperatures above recrystallization temperature (0.5Tm) • Sensitive to strain-rate at elevated temperatures v • A perfectly plastic material - Strain hardening • Strain rate: ε& = exponent is zero (theoretically) h • Relationship: m – Lower forces and power required Yf = Cε& n m – Metals become ductile • A more complete relationship: Yf = Aε ε& – Strength properties are generally isotropic • Evaluation of strain rate is complicated by – No work hardening of part – Workpart geometry – part can be subsequently cold formed – Variations in strain rate on the part – Lower dimensional accuracy • Strain rate can reach 1000 s-1 or more for some – Higher total energy required metal forming operations – Poorer surface finish including oxidation (scale), – Shorter tool life 17 18 Kwon 3 ME477 Fall 2004 Effect of temperature on flow 5. Friction and Lubrication stress Yf Yf Yf • Friction – retard metal flow and increase power and wear Categories Temp. Range Strain-rate Coefficient of C C Sensitivity exponent Friction Cold Working <0.3Tm 0<m<0.05 0.1 Warm Working 0.3Tm-0.5Tm 0.05<m<0.1 0.2 Hot Working 0.5Tm-0.75Tm 0.05<m<0.4 0.4-0.5 • Lubrication – reduce friction & heat, improve surface finish – Choosing a Lubricant – Type of operation, reactivity, work 1 2.0 0.11 10 100 0.11 10 100 materials, cost and ease of applications • Cold working – mineral oil, fats, fatty oils, water-based emulsions, • Increasing temperature decreases C, increases m soaps and coating At room temperature, effect of strain rate is almost negligible • Hot working – mineral oil, graphite and glass 19 20 Kwon 4.
Details
-
File Typepdf
-
Upload Time-
-
Content LanguagesEnglish
-
Upload UserAnonymous/Not logged-in
-
File Pages4 Page
-
File Size-