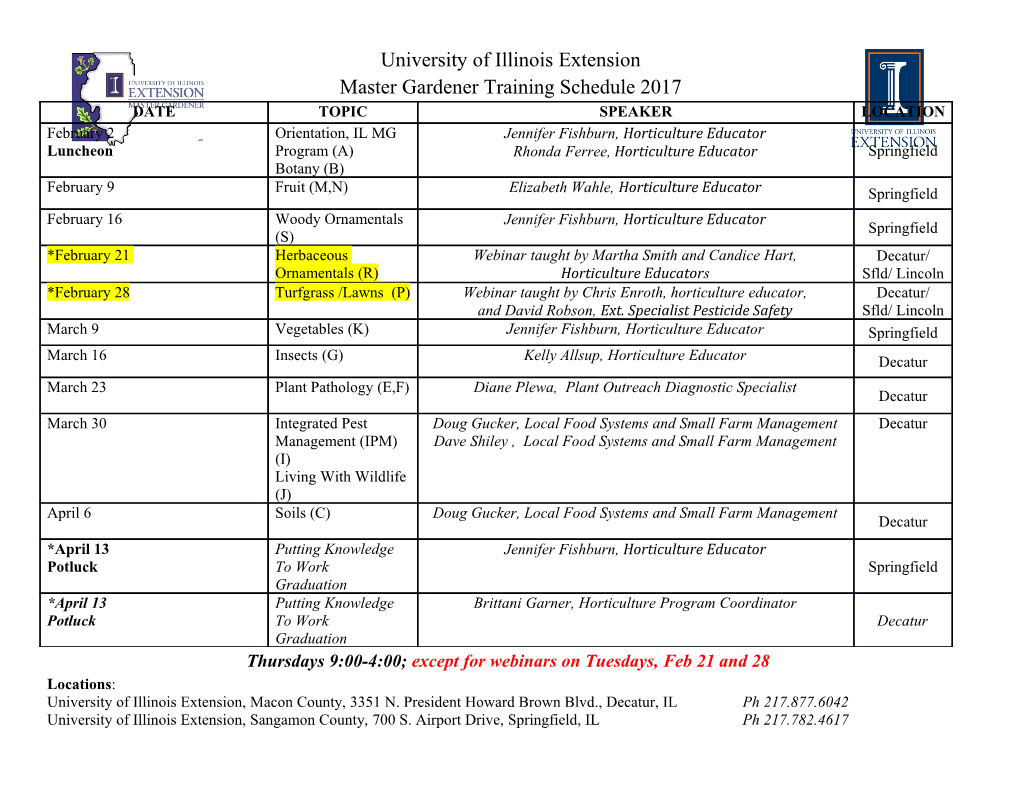
Montana Tech Library Digital Commons @ Montana Tech Bachelors Theses and Reports, 1928 - 1970 Student Scholarship 4-30-1948 Oxygen Enriched Atmosphere Roasting Clarence Wells Jr Follow this and additional works at: http://digitalcommons.mtech.edu/bach_theses Part of the Ceramic Materials Commons, Environmental Engineering Commons, Geology Commons, Geophysics and Seismology Commons, Metallurgy Commons, Other Engineering Commons, and the Other Materials Science and Engineering Commons Recommended Citation Wells, Clarence Jr, "Oxygen Enriched Atmosphere Roasting" (1948). Bachelors Theses and Reports, 1928 - 1970. 256. http://digitalcommons.mtech.edu/bach_theses/256 This Bachelors Thesis is brought to you for free and open access by the Student Scholarship at Digital Commons @ Montana Tech. It has been accepted for inclusion in Bachelors Theses and Reports, 1928 - 1970 by an authorized administrator of Digital Commons @ Montana Tech. For more information, please contact [email protected]. OXYGEN ENRICHED ATJrOSPHERE ROA&TING A Thesis Submitted to the Department of Metallurgy Montan~ School of Mines In Partial Fulfillment of the Refluirements for tbe Degree Bachelor of Science in Metallurgical Engineering oy Clarence ~"ells, Jr. April 30, 1948 OXYGEN ENRICHED ATMOSPHERE ROASTING A Thesis Submitted to the Department of Metallurgy Montana School of Mines In Partial Fulfillment of the Requt.r-emerrt >3 !cr the Degree Bachelor of Scic~ce in Metallurgical Engineering 19343 by Clarence Wells, Jr. April 30, 1948 TABLE -OF CONTENTS ~ CHAPTER I PAGE I GENERAL INTRODUCTION ••••••••••••••••••••••• 1 II THEORY ••••••••••••••••••••••••••••••••••••• 4 Reasons for oxygen atmosphere •••••••••••• 4 Amount of heat produced •••••••••••••••••• 5 Furnace requirements ••••••••••••••••••••• 6 Furnace capacity ......................... 6 Types of draft •• ••• ••••• •••• • • • •• • •••• • • • 6 Wall friction •••••••••••••••••••••••••••• ? Variable operating conditions •••••••••••• ? MOist feed •••••••••••••• ................. 8 Treatment of product ••..•••..0.........•• 8 Additional advantages • • • ••• • • • • • ••• • ••• •• 10 Problems encountered •• • • • • ••• •• • ••••• • ••• 11 III FURNACE DESI GN • • • • •• ••• ••• • • •••• •• • • ••• • • • • 13 Parts of furnace • •• • •• ••• • •• •• •• •• •• •• • • • 13 Construction of hearth ••••••••••••••••••• 14 Insulation • • • •••• • • • • • •• ••• •• • • • •• •• •• •• • 14 Oxygen feeding ••••••••••••••••••••••••••• 15 IV FEED FOR TESTS • • • • •••• •• • • • • • • ••••• • • • • •• • • 16 Analysis ••••...•.•...•..•...•...••••••..• 16 Mineral content • • ••• • • •• •• •• • • •• •••••• • •• 16 v PRELIMINARY TESTS • ••••• •• •• • • • ••••• •• • • •• • • 18 Equipment used ••••••••••••.•••••••••••••• 18 Types of tests ••••••••••••••••••••••••••• 18 Reasons for tests •••••••••••••••••••••••• 19 i CHAP'rER PAGE VI TESTS ••••••••••••••••••••••••••••••••••• ~•• 20 Temperatures used •••••••••••••••••••••••• 20 14ethod of feeding •••••••••..••..••••••••. 20 Rate of oxygen flow •••••••••••••••••••••• 20 Results of first test ••••••••• ~•••••••••• 21 Dust analysis ••••••.••••••••••••••••••••• 21 Test with fine feed ••••••••. ............. 22 Test with air atmosphere ................. 23 Discussion of results • • • • •• • • • • • • • •• • • • • • 23 Problems encountered •• • •••• •• • • • ••• •••• • • 24 VII CONCLUSIONS •••••••••••••••••••••••••••••.•• 25 VIII RECOHMENDATIONS • ••• •••• ••• • •••• • • • • • • •• •• •• 26 XIX BIBLIOGRAPHY ••••••••••••••••••••••••••••••• 27 XX ACKNOWLEDGMENT • • • •• • •• • • •• • • •• • •• • • • • • • • • • • 28 ii --LIST OF TABLES TABLE PAGE I Distribution of elements in concentrates •••• 16 II Screen analysis of feed ••••••••••••••••••••• 17 ~ OF FIGURES FIGUHE PAGE I Shaft roaster ••• • • • • • • • • • • • •• ••• •••••••• •• • 13 ill OXYGEN ENRICHED ATMOSPHERE ROASTING GENERAL INTRODUCTION The possible benefits of oxygen enriched atmosphere roasting have been known to metallurgists for many years, but only since the development of equipment and processes to produce cheap oxygen in very large amounts has,much ser- ious consideration been given this matter. In the early 1930's the Germans started work on produc- ing cheap oxygen for metallurgical uses.l The Russians have also done much work in this field, but very little informa- tion has been published by either country. A German, Mathias Frankl, suggested the use of regener- ators on a short reversing cycle to transfer refrigeration, rather than continuous counterflow heat exchangers like steam condensers. He devised a low-pressure cycle that produced 98% oxygen for about one-third the power consumption of the earlier high pressure cycles. At the present time, medium sized plants in the United States are producing oxygen for $6.00 per ton, but these plants would not be large enough for metallurgical operations. A plant is being built in Brownsville, Texas which is the size required for metallurgical operations, ana the builders est- imate the oxygen will be produced for $2.00 per ton. The capacity of this plant will be 2,000,000 cubic feet per hour. Two dollars per ton of oxygen compares favorably with the German cost figures. Oxygen at twice this figure would still make oxygen atmosphere roasting an attractive possibility. Experts on oxygen production say that efficiency will increase -1- with the size of the plant and thereby lower the cost per unit weight of oxygen. The requirements of only a'small amount of storage space and the use of low pressure systems help greatly in reducing oxygen costs. In 1935, Mr. T. E. Norman of Toronto, Canada made a series of calculations on different concehtrates to show the amount of heat that would be produced by roasting a high sulphide concentrate in an oxygen enriched atmosphere.2 The concentrates used by Mr. Norman for his calculations varied widely in composition and mineral content, but all had a high sulphur content. His results indicated that the heat produced was theoretically great enough to roast and smelt the concentrates without the use of extraneous fuel. As far as known, there were no actual experiments performed on this problem at that time, and there are still no pub- lished results of work done. Very recently the Consolidated Mining and Smelting Company of Canada has been doing work in their plant at Trail, B. C. on the roasting of zinc concentrates in an oxygen atmosphere, but at the present time they have re- leased very little information on their tests. They have, however, stated that their tests are proving to be very encouraging. Shaft roasters are being used for the work at Trail. The primary objectives of the work are to reduce the circulating dust load and to get better operational control. The actual tests in this investigation were run in a small shaft roaster, which is described on page 12, with -2- copper sulphide conceritrates of the analysis given on page 14, as the feed. The tests were run with the idea of determining and studying the problems that wou ld be encountered in oxygen enriched atmosphere roasting as well as studying the physical and chemical properties of the roasted product. It was undersood that the size of the equipment used would prevent the obtaining of re- sults which would hold for plant practice, but they would at least give an indication as to what might be expected. -3- THEORY Enriched atmosphere roasting in this CBse refers to the roasting of copper sulphide concentrates in an atmosphere of oxygen rather than in air. Oxygen is used in order to expose the concentrates to a maximum amount of oxidizing atmosphere with a minimum amount of gases being introduced into the roasting chamber. Since air is approximately seventy-nine per cent nit- rogen, it is necessary to introduce four parts of this gas into the roasting chamber for everyone part of oxygen. The use of pure oxygen as the roasting atmosphere would reduce the volume of gases four times. Large amounts of heat are required to bring the nitrogen in air up to the temperature of the roasting operation, and most of this heat is lost through the flue gases. The high dilution of the oxygen in air causes the oxida- tion reactions in roasting to take place very slowly and results in higher losses of heat by radiation, convection, and conduction. If the heat producing reactions were rapid enough, most of the heat would be maintained by the particles instead of being transferred to the furnace and the gases. An oxygen enriched atmosphere would greatly increase the speed of reaction and thereby reduce these 108ses. An oxygen atmosphere would greatly reduce the height of the shaft roaster required, because the concentrates would be subjected to a great amount of oxidation in a very short fall. There are several factors which affect the rate and -4- completeness of the oxidation reactions, but the three most . , important are the size of the particles to be roasted, the temperature of the roasting chamber, and the oxygen content of the roasting atmosphere. A finer feed tends to give a faster and more complete reaction, because there is a greater surface area exposed per unit weight of material. ' If the particles are coarse, there will be a core at the center which will not be oxidized unless the roasting takes place over an extended period of time. A higher temperature in the roaster will give a faster and more complete oxidation of the sulphide material and greatly reduce the core effect. A high oxygen content in the roasting atmosphere causes the oxidation reactions to take place more rapidly
Details
-
File Typepdf
-
Upload Time-
-
Content LanguagesEnglish
-
Upload UserAnonymous/Not logged-in
-
File Pages34 Page
-
File Size-