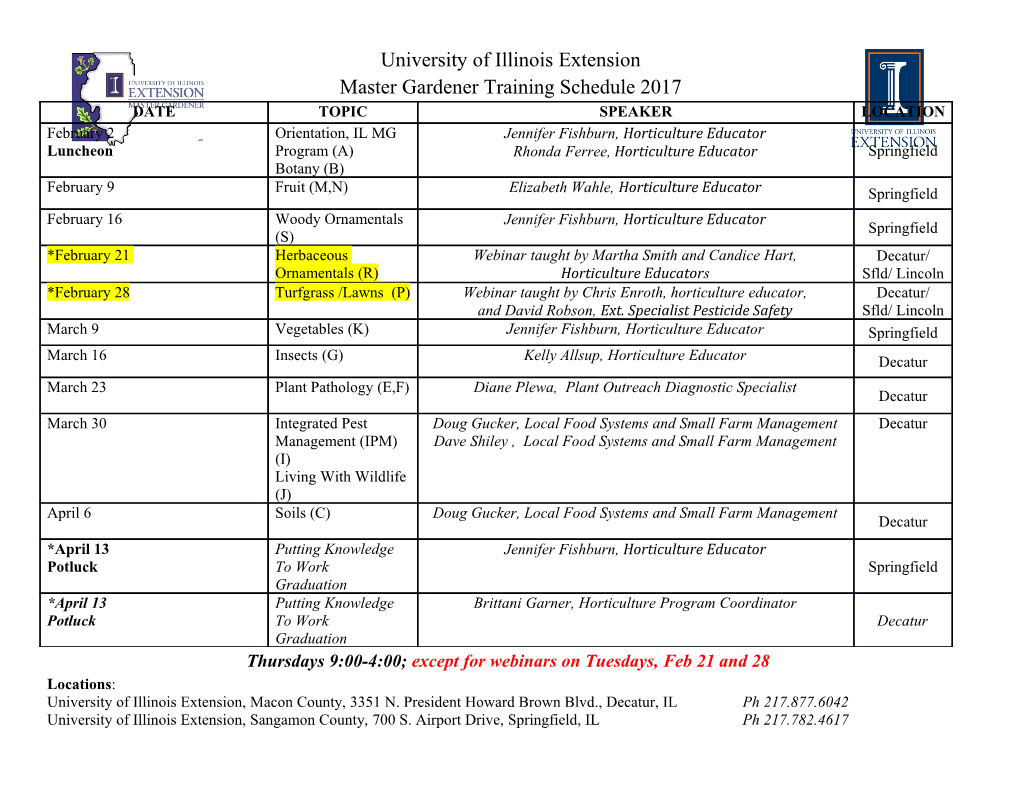
CRANFIELD UNIVERSITY School of Applied Sciences PhD THESIS Hydrogen Embrittlement Susceptibility of Super Duplex Stainless Steels Jalal Alsarraf CRANFIELD UNIVERSITY School of Applied Sciences PhD THESIS Academic Year 2006 - 2010 Jalal Alsarraf Hydrogen Embrittlement Susceptibility of Super Duplex Stainless Steels Supervisor: Dr. M. J. Robinson April 2010 © Cranfield University 2010. All rights reserved. No part of this publication may be reproduced without the written permission of the copyright owner. ABSTRACT This thesis describes the metallurgical and environmental factors that influence hydrogen embrittlement of super duplex stainless steels and presents a model to predict the rate at which embrittlement occurs. Super duplex stainless steel has an austenite and ferrite microstructure with an average fraction of each phase of approximately 50%. An investigation was carried out on the metallurgical and environmental factors that influence hydrogen embrittlement of super duplex stainless steels. Tensile specimens of super duplex stainless steel were pre-charged with hydrogen for two weeks in 3.5% NaCl solution at 50º C at a range of applied potentials to simulate the conditions that exist when subsea oilfield components are cathodically protected in seawater. The pre-charged specimens were then tested in a slow strain rate tensile test and their susceptibility to hydrogen embrittlement was assessed by the failure time, reduction in cross-sectional area and examination of the fracture surface. The ferrite and austenite in the duplex microstructures were identified by analysing their Cr, Ni, Mo and N contents in an electron microscope, as these elements partition in different concentrations in the two phases. It was shown that hydrogen embrittlement occurred in the ferrite phase, whereas the austenite failed in a ductile manner. An embrittled region existed around the circumference of each fracture surface and the depth of this embrittlement depended on the hydrogen charging time and the potential at which the charging had been carried out. The depth of embrittlement was shown to correlate with the rate of hydrogen diffusion in the alloy, which was measured electrochemically using hydrogen permeation and galvanostatic methods. A two-dimensional diffusion model was used to calculate the hydrogen distribution profiles for each experimental condition and the model could be employed to provide predictions of expected failure times in stressed engineering components. i Keywords: Ferritic-austenitic stainless steel, Hydrogen permeation, Diffusion, Hydrogen uptake, Cathodic protection, Cracking, Galvanostatic, Modelling, Austenite spacing. ii ACKNOWLEDGEMENTS It is difficult to overstate my gratitude to my Ph.D. advisor, Dr. Mike Robinson, for his advice and support throughout my research. His continuous enthusiasm, inspiration, and great efforts to explain things clearly and simply during the early parts of my graduate studies helped me understand the true values of research and set me on the right path to a smooth and easy journey to graduation. I would like to thank him for being such a great advisor, without him this work would not have been a success. I would also like to thank my committee members for their valuable input and guidance to improve this study. I greatly appreciate and wish to thank all the technical and library staff at Cranfield University for their great assistance during this project. I would further like to thank my friends and colleagues in the department, especially members of the corrosion group, with whom it has been very enjoyable to work. Furthermore, I must sincerely thank for the Public Authority for Applied Education and Training (PAEET, State of Kuwait) for their academic and financial support of the present thesis. Thanks to BÖHLER and Langley Alloys for partial support of the project. Lastly, I like to thank my family for their support, love and encouragement all this time, their phone calls cheered me up whenever was needed. To my parents for all that they did and who unfortunately never got to see this work. iii TABLE OF CONTENTS ABSTRACT ......................................................................................................... i ACKNOWLEDGEMENTS ................................................................................. iii LIST OF FIGURES ............................................................................................ ix LIST OF TABLES ......................................................................................... xviii 1 Introduction ............................................................................................... 1 2 Duplex Stainless steels ............................................................................ 3 2.1 Types of Duplex Stainless Steels ......................................................... 6 2.2 Metallurgy of Duplex Stainless Steels .................................................. 8 2.3 Alloy Design ......................................................................................... 8 2.3.1 Chromium ................................................................................... 10 2.3.2 Molybdenum ............................................................................... 11 2.3.3 Nickel .......................................................................................... 11 2.3.4 Copper ........................................................................................ 12 2.3.5 Nitrogen ...................................................................................... 14 2.3.6 Manganese ................................................................................. 15 2.3.7 Tungsten ..................................................................................... 16 2.3.8 Silicon ......................................................................................... 16 2.4 Mechanical Properties of Duplex Stainless Steel ............................... 18 2.5 Applications of Duplex Stainless Steels ............................................. 19 2.6 Limitations of DSS.............................................................................. 20 2.6.1 Hydrogen Embrittlement Failures ................................................ 21 2.6.1.1 BP ........................................................................................... 21 2.6.1.2 Shell ........................................................................................ 23 2.7 Segregation of Alloying Elements ...................................................... 24 2.7.1 Sigma Phase............................................................................... 25 3 Corrosion Behaviour of Duplex Stainless Steels ................................. 27 3.1 Types of Damage Due to Hydrogen ................................................... 29 3.2 Hydrogen Embrittlement .................................................................... 29 3.2.1 Mechanisms of Hydrogen Embrittlement .................................... 30 3.2.1.1 The Internal Pressure .............................................................. 30 3.2.1.2 Surface Energy ........................................................................ 30 v 3.2.1.3 Decohesion Theories .............................................................. 31 3.2.2 Methods for Hydrogen to Enter Metals ....................................... 32 3.2.2.1 Pickling and Chemical metal Removal .................................... 33 3.2.2.2 Plating Operations (another cathodic Process) ....................... 33 3.2.2.3 Crevice Corrosion Conditions .................................................. 33 3.2.2.4 Service Condition .................................................................... 33 3.2.3 Comparison of SCC and HE ....................................................... 33 3.2.4 Diffusion of Hydrogen in Duplex Stainless Steels ....................... 36 3.2.4.1 Diffusion .................................................................................. 36 3.3 Pitting Corrosion................................................................................. 37 3.3.1 Effect of Alloying Elements on Epit ............................................. 37 3.3.2 Pitting Mechanism ....................................................................... 38 3.3.3 Pit Growth ................................................................................... 39 3.3.4 Pit Initiation ................................................................................. 41 3.3.5 Initiation Mechanism ................................................................... 42 3.3.5.1 Defect Theory .......................................................................... 42 3.3.5.2 Chloride Ion Dissolutions ......................................................... 42 3.3.5.3 Peptisation............................................................................... 42 3.3.5.4 Local Cells ............................................................................... 43 3.3.5.5 Stress Theory .......................................................................... 43 3.3.5.6 Vacancy Theory ...................................................................... 43 3.3.5.7 Breakdown and Repair ............................................................ 43 3.3.5.8 Inclusions ................................................................................ 44 4 Experimental Methods ............................................................................ 45 4.1 Materials ...........................................................................................
Details
-
File Typepdf
-
Upload Time-
-
Content LanguagesEnglish
-
Upload UserAnonymous/Not logged-in
-
File Pages250 Page
-
File Size-