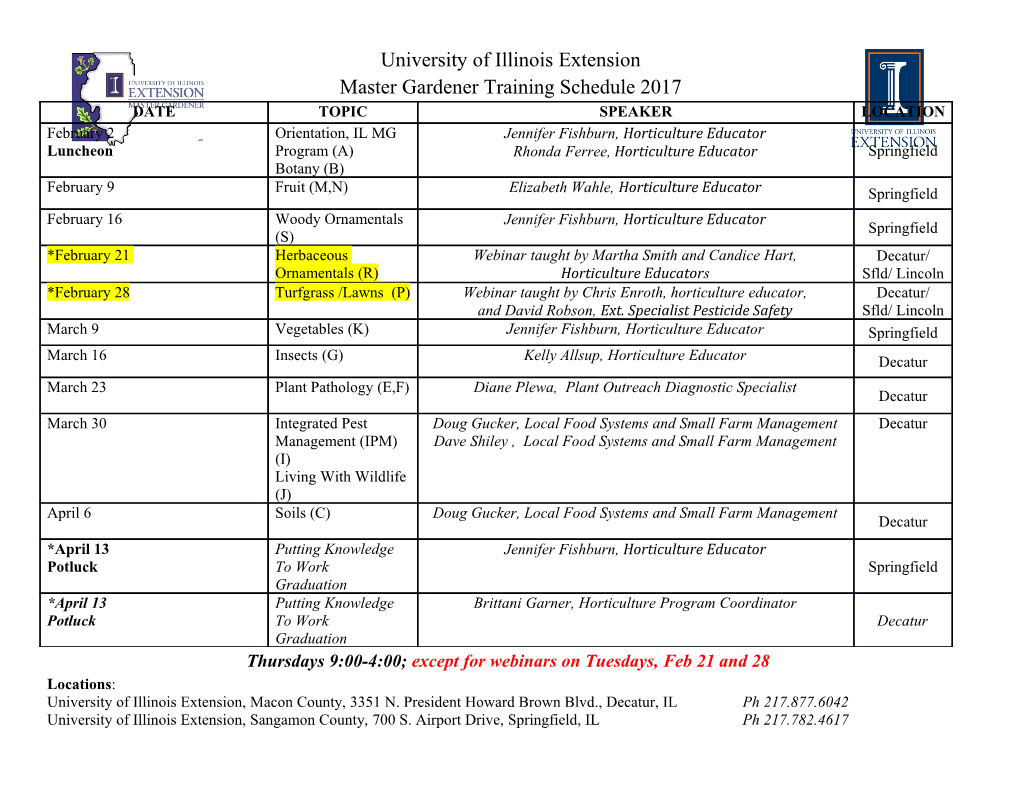
.. t , NASA CONTRACTO- REPORT LOAN COPY: RETURN TO AFWL (WLQL-2) KIRTLAND AFB, N bIEX FLIGHT TEST RESULTSOF A TRAILING EDGE FLAP DESIGNED FORDIRECT-LIFT CONTROL by Charles R. Taylor, Jr. Prepared by THE BOEING COMPANY Seattle, Wash. for Ames Research Center NATIONALAERONAUTICS AND SPACE ADMINISTRATION 9 WASHINGTON, D. C. OCTOBER 1969 I " NASA CR-1426 TECH LIBRARY KAFB. NU FLIGHT TEST RESULTS OF A TRAILING EDGE FLAP DESIGNED FOR DIRECT-LIFT CONTROL By Charles R. Taylor, Jr. Distribution of this report is provided in the interestof informationexchange. Responsibility for thecontents resides in the author or organization that prepared it. Prepared under Contract No. NAS 2-4200 by THE BOEING COMPANY Seattle, Wash. for Ames Research Center NATIONAL AERONAUTICS AND SPACE ADMINISTRATION - I. ~ ~ ~ . ... Forsale by the Clearinghouse for Federal Scientific and Technical Information Springfield,Virginia 22151 - CFSTI price $3.00 CONTENTS SUMMARY .............................. i INTRODUCTION ........................... i SYMBOLS .............................. 2 DESCRIPTION OFTEST VEHICLE .................... 3 TrailingEdge Flaps ......................... 3 BLC System ............................ 4 DLC FlapSystem ......................... 4 DLC SpoilerSystem ........................ 4 Powerplants ............................ 5 LeadingEdge Devices ........................ 5 VariableStability System ...................... 5 Instrumentation .......................... 5 TESTPROCEDURES .......................... 6 Direct-LiftControl Flaps ....................... 6 Steady-StateTesting ...................... 6 DynamicTesting ........................ 6 Direct-LiftControl Spoilers ...................... 7 Steady-StateTesting ...................... 7 DynamicTesting ........................ 7 RESULTSAND DISCUSSION ...................... 7 Direct-LiftControl Flaps ....................... 7 Steady-StateCharacteristics .................... 7 DynamicCharacteristics ..................... 10 AltitudeResponse ....................... 12 Direct-LiftControl Spoilers ...................... 12 Steady-StateCharacteristics .................... 12 DynamicCharacteristics ..................... 12 AltitudeResponse ....................... 13 CONCLUSIONS ............................ 13 APPENDIXA ............................. 75 APPENDIXB ............................. 78 REFERENCES ............................ 80 V / FIGURES Number Page 1 Boeing 367-80Airplane During Takeoff .............. 15 2 GeneralArrangement of 367-80 Airplane ............. 16 3 367-80Airplane with DLC Flaps ................ 17 4 BoundaryLayer Control System ................ 18 5 Planform View of DLC Flapsand Spoilers ............. 19 6 Detailsof DLC Flap System .................. 20 7 DLCFlap Actuators ..................... 21 8 Arrangement of Inboard Engine-Trailing Edge Flaps With 40" Main and 10" Auxiliary Flap .................. 22 9 Illustration of DLC Flap Effectiveness ............... 22 10-22 DLC FlapCharacteristics .................... 23 23 Steady-State DLC Flap Lift Capability at Constant Angles of Attackfor Approach ..................... 36 24-4 1 Time Histories of Airplane Response to Auxiliary Flap Step Inputs ... 37 42 and 43 Comparison of DLC Flap Dynamic and Steady-State Lift Change- -30" Main Flap and Idle Power; BLC Off .............. 55 44-6 1 AltitudeResponse to AuxiliaryFlap Step Inputs .......... 56 62 and 63 DLC SpoilerCharacteristics ................... 65 64 Total Steady-State DLC Spoiler Lift Capability at ConstantAngles of Attack for Landing Approach ................. 67 65-68 Time Histories of Airplane Response to Spoiler Step Inputs ...... 68 69 and 70 Comparisonof Steady-State and Dynamic Lift Change ........ 72 7 1-74 AltitudeResponse to SpoilerStep Inputs ............. 73 A1 JT3D-1 Engine Gross Thrust and Characteristics; BLC On and Off .... 76 A2 JT3D-IEngine Airflow Characteristics; BLC Onand Off ....... 77 B1 Effect on Momentum Coefficient of Compressor Speed and Main Deflection . 79 vi FLIGHT TEST RESULTS OF A TRAILING EDGE FLAP DESIGNED FOR DIRECT-LIFT CONTROL by Charles R. Taylor, Jr The Boeing Company Seattle, Washington SUMMARY A flight test investigation was conducted with the Boeing 707 prototype to obtain the performance characteristics of a trailing edge flap for direct-lift control (DLC). The flap was designed and tested by The Boeing Company for the National Aeronautics and Space Administration. The flap system consisted of a main flap with blowing boundary layer control (BLC) and a slotted aft auxiliary flap for DLC. The auxiliary flap had a deflection range of IOo up and 30° down with respect to a faired position with the main flap. The DLC-null angle was loo down from the faired position. Steady-state aerodynamic characteristics -of the flap system were obtained from steady trimmed flight at several speeds plus slow deceleration to the stall. Airplane response and dynamics were obtained from step inputs to the auxiliary flap from their null setting. Similar maneuvers using wing spoilers for DLC also were accomplished. The steady-state results showed that lift coefficient increments (ACL) of about 0.30 to 0.40 generally were obtained with 40° of auxiliary flap travel, while increments of 0.52 to 0.60 were noted with 15' of spoiler travel. Thrust impingement and BLC both tended to increase the ACL'S of the flaps, whereas higher main flap settings decreased them. Incremental normal accelerations on the orderof +O. 10 and-0.1 2 g were obtained with f 20" flap steps from the null flap. Spoiler stepsof f 8" from the null spoiler gave +0.22 and -0.10 g increments. INTRODUCTION A flight test program was conducted to investigate a trailing edge flap system designed for direct-lift control (DLC). The investigation was part of a program to develop and evaluate systems designed for noise abatement approaches to landing using low-power settings and/or steeper than conventional flight'paths. The Boeing 367-80 airplane (KC-135/ 707 prototype) was used as the test vehicle for the program. DLC has been proposed (refs. 1 and 2) as a means of improving longitudinal flight- path control and response. Direct control of lift at constant pitch attitude angle and/or airspeed requires the modulation of a control surface that will vary the lift on an airplane without a corresponding large pitching moment change. Two control surfaces that have been considered for DLC are trailing edge flaps and spoilers. Lowering the flaps or closing the spoilers from a DLC-null deflection angle will increase the lift. Conversely, raising the flaps or opening the spoilers from the null angle will reduce the lift. Thus, DLC enhances the handling qualities of an airplane by quickening its response in vertical motion to pilot or autopilot commands. The test program was conducted in three phases. Phase I consisted of initial DLC flap design using NASA data from the Ames full-scale wind tunnel and preliminary flight investigation of noise abatement approaches. During a portion of the flight investigation, initial flap design characteristics of the DLC flap were simulated on the airplane. Phase I1 consisted of installation, airworthiness checks, and the initiation of inflight performance testing of the DLC flap system. Phase I11 consisted of additional flap performance testing and evaluation of DLC and other systems while performing normal and noise abatement approaches to landing. This report presents the results of the DLC flap per- formance testing accomplished in Phases I1 and 111. Performance data obtained during Phase I11 using spoiler DLC are also included. A report of the systems evaluation con- ducted in Phases I and I11 of the program is presented in ref. 3. Reference 4 presents a comparison of the flight data presented in this report with wind tunnel results acquired by NASA in the Ames 40- by 80-foot tunnel using a 1/3-scale model of the 367-80. The wind tunnel results are documented in ref. 5. SYMBOLS CD Drag coefficient CL Lift coefficient C Maximum lift coefficient Lmax ccc Momentum coefficient D Drag, Ib dh/dt Altitude change with time, ft/sec dv/d t Velocity change with time, ft/sec2 FG Gross thrust, lb FN Net thrust, Ib g Acceleration due to gravity, ft/sec2 hi Indicated altitude, ft NCG Acceleration normal to body axis at center of gravity, g units N2 High-pressure compressor speed, percent 2 Freestream dynamic pressure, lb/ft2 Wing area, ft2 True airspeed, kn Equivalent airspeed, kn One g stall speed, kn Gross weight, lb Engine airflow rate, lb/sec Body angle of attack, deg Ambient pressure ratio Auxiliary flap deflection, deg Elevator deflection, deg Spoiler deflection, deg Engine inlet total pressure ratio Body pitch attitude, deg Total air temperature ratio ABBREVIATIONS BLC Boundary layer control DLC Direct-lift control MCT Maximum continuous thrust PLF Power for level flight SAS Stability augmentation system DESCRIPTION OF TEST AIRPLANE The Boeing Model 367-80 (fig. 1) has been used as a developmental test bed for several company programs and for NASA research studies. Figure 2 presents a two-view drawing of the airplane with pertinent geometrical data. The following paragraphs describe the various systems which made up the test airplane. Trailing Edge Flaps The trailing edge flap system consisted of a main flap with blowing boundary layer control (BLC),and an aft auxiliary slotted-type flap for direct-lift control. Both the main and auxiliary flaps were simple-hinged assemblies that extended along 68 percent of the wing span. The flaps were modified for Phase I11
Details
-
File Typepdf
-
Upload Time-
-
Content LanguagesEnglish
-
Upload UserAnonymous/Not logged-in
-
File Pages85 Page
-
File Size-