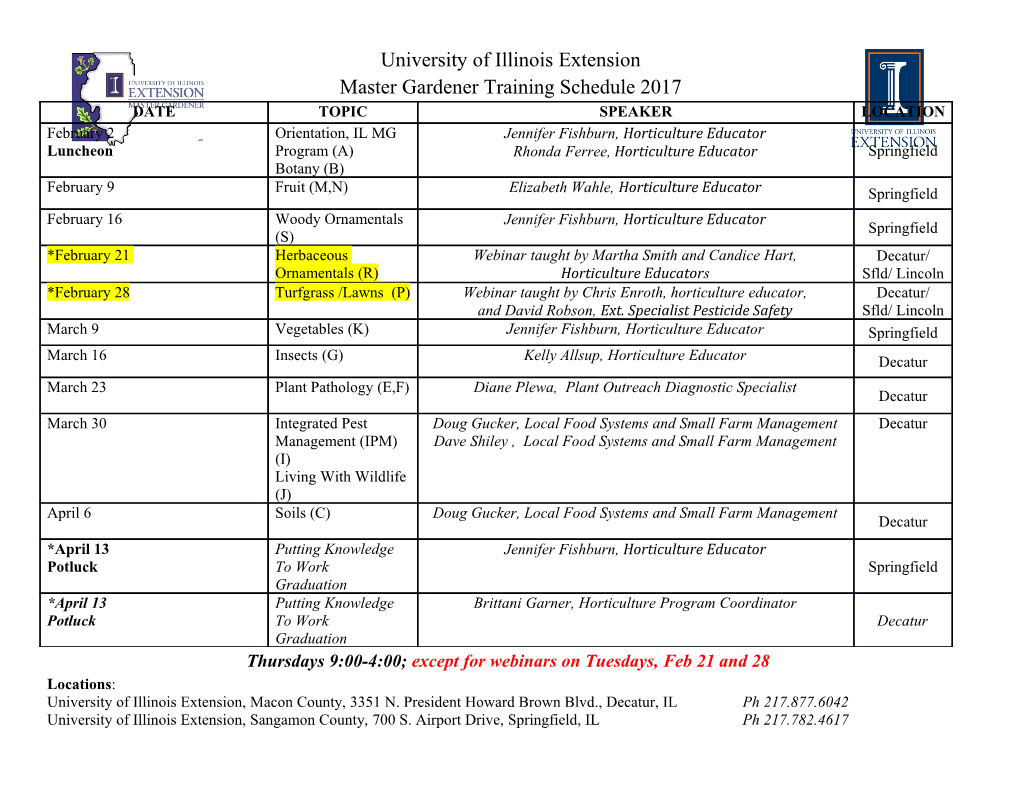
Hadar Jacobson Art in Metal Clay h [email protected] • www.hadarjacobson.com Finishing Fired Metal Clay Preparing a piece for firing (pre-finishing) makes it easier to finish after firing, but does not make finishing unnecessary. Because of the porosity and shrinkage of metal clay, surfaces that looked smooth prior to firing can look rough and grainy afterward. Now that the clay has turned into metal, it needs to be sanded and polished with various tools, just as in traditional metal fabrication, to produce the desired final finish. Sometimes, pieces come out of the kiln with beautiful colors. Unfortunately, this effect is not predictable or repeatable, and has nothing to do with the type of carbon used. Furthermore, there is no reliable way to preserve these colors; they will fade away with wear and tear, and sealing the piece will most probably alter the colors. My suggestion is: enjoy the colors while they last. Otherwise, just follow the finishing process. The earrings above have still not lost their color, but they have never been worn either. A rotary tool makes the finishing process easier and quicker. A flex shaft machine is a good professional tool, but is can be expensive and is not portable. It’s best to get the portable tool not as part of an expensive kit, since most of the accessories that you will need are not included in the kit and need to be purchased from jewelry suppliers. The attachments to the rotary tool have shanks that come in 1 3 diameter of /8" or /32". The rotary tool usually comes with a 1 3 collet that accepts /8"shanks. You can purchase a /32" collet at hardware stores, or a universal chuck, which accepts both sizes, and makes it unnecessary to switch collets when moving from one size shank to another. Sources for the rotary tool and attachments can be found on my blog, in the document entitled “Personal Toolkit,” accessible from the Collets Universal Chuck right-hand pane. 1. Check for sintering. The first thing to do after taking pieces out of the kiln is to check if it is fully sintered. Bending the pieces is not recommended as a test, since if the piece breaks, there is no way to salvage it. Instead, sand the back of the piece with 220-grit sandpaper mounted on a slotted mandrel. Here is how to prepare the slotted mandrel: Slotted (or Split) Mandrel, straight head a) Insert a 3" long piece of 220-grit sandpaper into the slot so that most of its length protrudes from the left side of the mandrel with the abrasive side facing you. This way of wrapping b) Cut the strip at the top the slotted mandrel of the mandrel and slant makes sure that the direction of the it at the end, as shown wrapping as the same in the photo. as the direction in which the rotary tool c) Wrap the sandpaper spins. If it were tightly backwards wrapped in the other direction, the around the mandrel, sandpaper would so that the abrasive come off. side is on the outside. d) Secure the sandpaper to the mandrel with tape, covering part of the sandpaper and part of the lower end of the mandrel. When the top layer wears out, cut off a piece of the strip. Now sand the back of your piece, moving back and forth with the mandrel. If the surface area becomes all metallic, it means that the piece sintered just fine. However, if you see spots which do not get metallic, but rather become darker and powdery, it means that the piece has not sintered properly. What to do? Just re-fire following the same firing schedule. If some powder came off, add some clay. No need to repeat the first phase. The piece is now ready for finishing. 2 2. Clean textured areas. In most cases pieces come out of the kiln covered with a thin dark film. This can be easily removed with radial discs, mounted on a screw mandrel. Assembling the discs Unscrew the screw mandrel with a small screw driver (some screw mandrels will screw to the right; some will screw to the left). Mount 2 radial discs, ¾" in diameter, of any grit, on the mandrel with the teeth turning clockwise (as shown in the top disc). Put the screw back on. Mount the screw This attachment can also mandrel on the rotary tool. be used to wipe off patina and to re-polish tarnished Turn the rotary tool on at minimum speed and buff off the areas of both silver and black film. base metals. The attachment on the right is called a course mini-fiber wheel. It is efficient for cleaning large textured areas and for texturing smooth areas. 3. Sanding smooth (non-textured) areas. Sometimes, an area that was smooth and flush before firing comes out of the kiln grainy and bumpy. This is especially the case with mixed metal pieces, where some of the metals shrink more than others. You will need a drum mandrel and sanding bands. The sanding bands are sold separately and it is best to stock up on 120- and 240-grit bands, since they wear out quickly. When the band is worn out, replace it with a new one. a) Use a small screwdriver to loosen the screw at the top of the mandrel. b) Slide the sanding drum onto the mandrel, and tighten the screw. 3 Sand the surface until it is all flush. If the surface is very bumpy, start with a 120-grit drum; if it is slightly bumpy, start with 240 grit. Move on to 220-grit sandpaper on the slotted mandrel, with which you tested sintering earlier. Sand the surface by slowly going back and forth, without removing the mandrel from the surface. Apply some pressure during this process; the pressure is more important than quick movements. The photo on the left shows the process When using the of sanding the non-textured surface of a portable rotary tool, back of a piece. Customers have a habit lean the back of your of flipping a piece over when you show it hands on the work to them, so it’s best to make sure that the surface and move back is just as well finished just as the your wrist back and front. forth; otherwise you’ll get tired quickly. The pressure should be coming from your shoulder. Keep changing directions. Each time you change direction you will still see the scratches of the sandpaper underneath going in the other direction. Keep changing directions until you see the lines going in only one direction. When the sandpaper wears out, tear When the sandpaper off a piece of it and you’ll have a fresh one underneath. wears out and the mandrel shows through, it’s time to wrap the Sand the sides of the piece as well. Feel with your fingers for sharp mandrel with a new strip corners and edges, and round them off using a round motion. of sandpaper, or the Keep sanding until all you can see on the surface is the scratches mandrel will scratch the caused by the sandpaper. silver and you will have to start sanding all over again. Repeat the sanding with 400-grit sandpaper. This step is less time consuming as it’s only meant to refine the scratches left by the 220- grit sandpaper. It also makes the surface look shiny. Tapered-head Mandrel This mandrel is used for hard-to-reach spots and small areas, such as the space between the bail and the back of a pendant. For this mandrel cut the sandpaper strip shorter, no longer than 1½", and a little bit wider than the length of the slot. 4 4. Matte finish Mount an extra-fine mini-fiber wheel (red color) on the rotary tool. Use light touches and daubs to wipe off the marks left by the sandpapers. If you press hard, the surface will look brushed. This kind of finish is also called satin finish or white finish. As a result of sanding and matting mixed metal pieces, the contrast between the metals will almost disappear. The contrast is easily recovered by using Baldwin's Patina. a) Wet a cotton or sponge swab with a drop of the patina. Rub the surface of the circle. Keep rubbing until the full pattern reappears. b) Wash the pendant well with warm water to stop the patina from reacting (or else your piece may turn green). Baldwin's Patina darkens steel and copper, but not silver or any type of bronze (regular, XT, White or Brilliant.) The patina tends to give the surface a shiny look, so there is no need to polish the piece afterward. The patina is the last step on mixed metal pieces. It also provide a sealing film that will keep this look for a long time. For more on using Baldwin’s Patina, see my video clip on YouTube: go to youtube.com/artinsilver and click on the video entitled “Baldwin’s Patina on Metal Clay.” 5 To summarize the process, here is a photo demonstration of finishing the under-fired earrings shown on the bottom of page 2. These earrings were made from copper and White Bronze. Sanding with a drum mandrel Sanding with 220-grit sandpaper mounted on a straight head slotted mandrel Sanding with 400-grit Buffing with an extra-fine sandpaper mounted on a mini-fiber wheel straight head slotted mandrel When the patina stays on the surface as shown in the photo on the left, and does not get immediately absorbed into the piece as into a sponge, it means that you have done a good sanding job.
Details
-
File Typepdf
-
Upload Time-
-
Content LanguagesEnglish
-
Upload UserAnonymous/Not logged-in
-
File Pages8 Page
-
File Size-