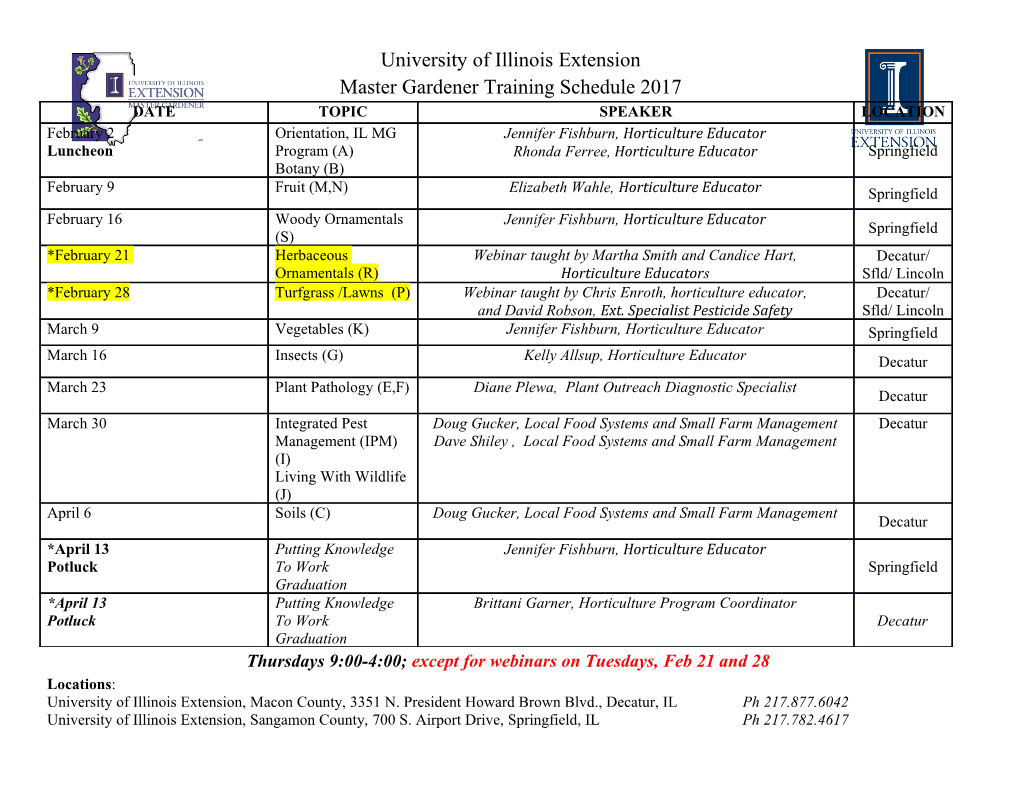
International Journal of Heat and Mass Transfer 43 (2000) 4267±4274 www.elsevier.com/locate/ijhmt Buoyancy eects on heat transfer and temperature pro®les in horizontal pipe ¯ow of drag-reducing ¯uids K. Gasljevic, G. Aguilar, E.F. Matthys Department of Mechanical and Environmental Engineering, University of California, Santa Barbara, CA 93106, USA Received 12 November 1999; received in revised form 7 February 2000 Abstract We have studied the extent to which buoyancy eects in horizontal pipe ¯ows of drag-reducing viscoelastic ¯uids cause distortions to both laminar and turbulent temperature pro®les. In the case of laminar ¯ows, these distortions may lead to variations in Nusselt numbers that are larger than those seen for Newtonian pipe ¯ows under similar conditions. In the case of turbulent drag-reducing ¯ows, the eects of buoyancy can also be large and may in turn result in large errors in estimated Nusselt numbers if not properly accounted for. These errors are quanti®ed and recommendations are made on how to reduce them. 7 2000 Elsevier Science Ltd. All rights reserved. 1. Introduction on experimental data, Morcos and Bergles [3] provided averaged Nusselt number (Nuavg) correlations which In heated ¯ows in horizontal pipes, gravity-induced take into account the eect of circumferential heat ¯ux body forces may result from density variations within variations for the problem of mixed convection on the ¯uid. Mori et al. [1,2] have shown ¯ow visualiza- laminar ¯ow of Newtonian ¯uids in horizontal tubes. tion results for mixed convection in laminar ¯ows of Metais and Eckert [4] proposed practical charts in Newtonian ¯uids in horizontal pipes, demonstrating which the regions of forced and mixed convection for that the local variations in the ¯uid density lead to Newtonian laminar and turbulent ¯ows in horizontal counteracting transverse vortices (or secondary ¯ow pipes can be clearly identi®ed in terms of the Re, Gr, patterns), which are superimposed to the main axial and Pr. ¯ow. More recently, viscoelastic drag-reducing ¯uids, They also showed that the dierences between their and particularly surfactant solutions, have attracted local measurements of temperature and velocity, and the attention of researchers because of their poten- the theoretical laminar pro®les with no buoyancy tial for energy savings applications. The buoyancy eects, could be as high as 50%, and that Ð for heat- eects on laminar and turbulent ¯ows for these ing of the ¯uid Ð the point of lowest temperature was ¯uids is not only interesting from a theoretical displaced from the center towards the lower portion of point of view, but also for the proper design of ex- the pipe. All these experiments were conducted in the perimental procedures. Shenoy and Ulbrecht [5] stu- range of Re  Ra =2 104±1.6  105. On the other died the eect of natural convection on a laminar hand, their measurements of turbulent temperature ¯ow next to a vertical ¯at plate for various sol- and velocity pro®les in the range of Re  Ra between utions of a viscoelastic ¯uid, and they found that 3.87  105 and 4.7  105 showed a negligible dierence the local convective heat transfer coecients (h ) with respect to those of pure forced convection. Based were systematically higher for elastic ¯uids than for 0017-9310/00/$ - see front matter 7 2000 Elsevier Science Ltd. All rights reserved. PII: S0017-9310(00)00065-X 4268 K. Gasljevic et al. / Int. J. Heat Mass Transfer 43 (2000) 4267±4274 Nomenclature 2 à 0:5 Cf 2tw=rV friction coecient u tw=r friction or shear vel- Cf; water friction coecient for ocity 1:58  ln Re3:28 2 turbulent newtonian V bulk velocity (m/s) ¯ow (Filomenko) y yuÃ=n dimensionless distance D pipe diameter (m) from the wall DR 1 Cf =Cf, waterÂ100 drag reduction level (%) Greek symbols 3 2 Gr gbD DTw; avg-b=n Grashof number a thermal diusivity based on D (m2/s) 00 h q =DTw-b convective heat trans- b thermal expansion fer coecient (W/m2 coecient (1/K) K) DTw-b inner wall-bulk tem- kf thermal heat conduc- perature dierence (K) tivity (W/m K) DTw, avg-b average inner wall- 00 Nu q D=DTw-bkf Nusselt number based bulk temperature on D dierence for the three 00 Nuavg q D=DTw; avg-bkf average Nusselt num- wall locations (K) ber (based on the eM momentum eddy diu- average temperature sivity (m2/s) of the three wall sen- eH heat eddy diusivity sors) (m2/s) Pr n=a Prandtl number n kinematic viscosity 2 Prt eM=eH turbulent Prandtl (m /s) number r ¯uid density (kg/m3) 4 Ra gbDTw; avg-b=na Rayleigh number tw wall shear stress (N/ Re VD=n Reynolds number m2) based on D q0 heat ¯ux at the wall Subscripts (W/m2) up refers to top portion 00 Tb Ti q =rCpV bulk temperature (8C) of the pipe à 00 T Tw T u rCp=q dimensionless wall-to- dn refers to bottom por- ¯uid temperature tion of the pipe dierence inelastic ones at similar heat and ¯ow rate con- of drag-reducing ¯uids in horizontal pipes, however, ditions, being in some cases higher by 40%. Other although one might guess that buoyancy can induce researchers have studied, for viscoelastic ¯uids, the secondary ¯ows perpendicular to the main free-stream eect of buoyancy on laminar ¯ows over vertical direction, presumably similar to those seen in laminar and horizontal plates, as well as around the stag- ¯ows. The only reference to the eects of buoyancy in nant region of a heated cylinder [6±8]. In all cases, channel ¯ows of drag-reducing surfactant solutions there is an increase in the convective heat transfer that we know is the one by Kawaguchi et al. [10]. coecient with increasing ¯uid viscoelasticity. They measured temperature pro®les in the cross sec- Regarding internal ¯ow, Ref. [9] appears to be the tion of a square channel heated at the bottom wall, only study that has addressed the problem of mixed and found a region of very high diusivity in the vis- convection of viscoelastic drag-reducing ¯uids on cous sublayer. They also measured an increase in Nus- vertical pipe ¯ow under turbulent conditions. For selt number (Nu ) of 20% due to a twofold increase in this particular case, the turbulence generation is the heat ¯ux, with all other conditions remaining con- aected by the redistribution of the shear stress stant. The increased diusivity and Nu were attributed across the pipe, which is in turn aected by the to buoyancy eects, although they also considered the buoyancy-driven ¯ow moving in the ¯ow direction. possibility of thermal destruction of the micelles. In Little work has been done on the mixed convection our recent studies on the heat transfer and temperature K. Gasljevic et al. / Int. J. Heat Mass Transfer 43 (2000) 4267±4274 4269 pro®le measurements of various drag-reducing polymer shape with a mean diameter of about 0.007±0.008 in. and surfactant solutions, we have found that buoyancy (0.18 mm). This sensor is displaced across the pipe by eects are present in laminar as well as in turbulent an external mechanism that allows it to move in incre- ¯ows. The aim of this paper is to draw attention to the ments of 0.001 in. (0.025 mm). This pro®le temperature eect of buoyancy in drag-reducing turbulent pipe sensor was located at approximately the same axial lo- ¯ows, which may aect experimental results if there is cation as the RTD temperature sensors, so that the a lack of awareness of its presence. values of h measured by the RTDs, and those calcu- lated by integration of the temperature pro®le should be about the same for symmetric pro®les. 2. Experimental installation The experimental setup consists of a stainless steel 3. Results and discussion tube of 19.95 mm (20 mm nominal) inner diameter and 680 diameters length, a centrifugal pump or a 3.1. Laminar pro®les pressurized tank used for ¯uid circulation, and various pressure taps installed along the pipe for drag re- Fig. 1 shows the results of temperature pro®le duction measurements (DR). A more detailed descrip- measurements for a 1500 ppm polyacrylamide tion of the setup is given elsewhere [11]. (Separan AP-273) solution in deionized water. The Two types of heat transfer measurements were con- span of our device covers only approximately 8 mm, ducted: overall heat transfer coecients (h ), and local and the two halves of the pro®le had to be measured temperature pro®les across the pipe. A DC Joule heat- by turning the pipe 1808, leaving a small gap in data at ing source provided a good approximation of a con- the center. A theoretical no-buoyancy laminar pro®le stant and uniform heat ¯ux condition. We used four is shown for comparison, and there are two eects of temperature sensors: three sensors (miniature RTDs 10 buoyancy which one can readily see: a distortion of  2 mm, 100 O), which were cemented with RTD the temperature pro®le (or circumferential variation of epoxy adhesive (Omega OB-101-2) on the outer wall at local convective heat transfer), and a change in the the top, side, and bottom of the pipe at 675 diameters average Nu compared to the ¯ow without buoyancy. downstream of the entrance to detect the possibility of The pro®le looks similar to that measured for a New- circumferential asymmetry of h; and one temperature tonian ¯uid [1], and shows also the coldest point sensor, a shielded type RTD, which was inserted across shifted towards the bottom wall, presumably due to the pipe at the inlet in order to measure the ¯uid inlet the action of secondary ¯ows generated by buoyancy, temperature Ti).
Details
-
File Typepdf
-
Upload Time-
-
Content LanguagesEnglish
-
Upload UserAnonymous/Not logged-in
-
File Pages8 Page
-
File Size-