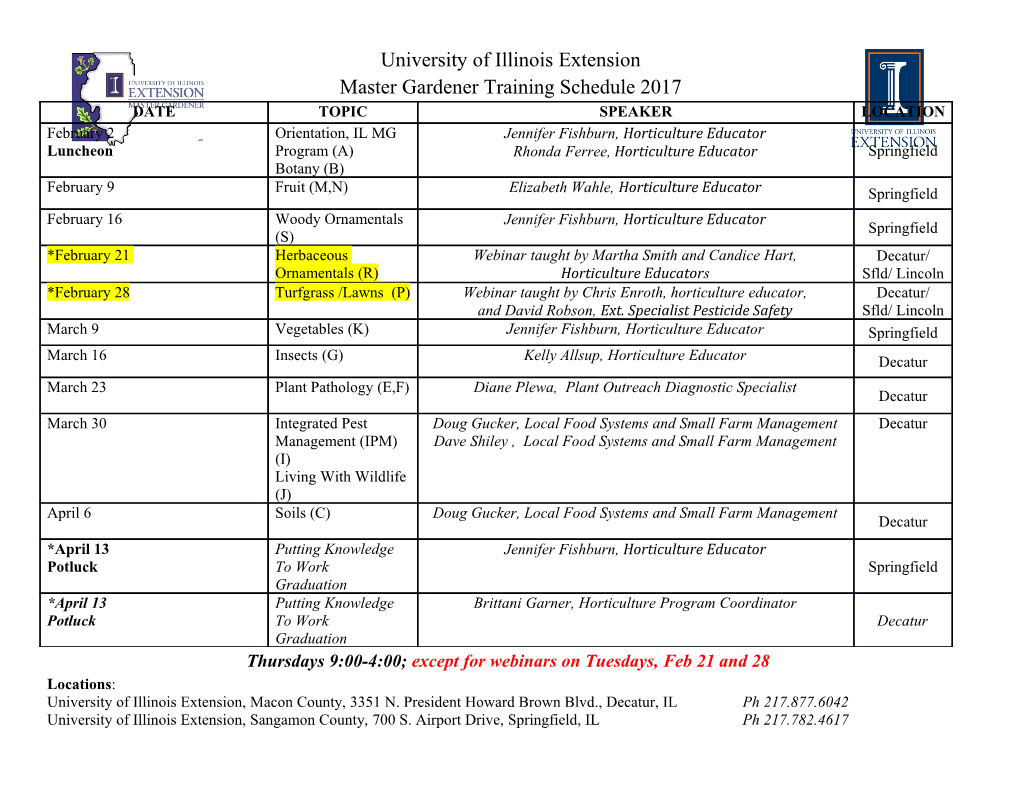
University of Tennessee, Knoxville TRACE: Tennessee Research and Creative Exchange Masters Theses Graduate School 8-2014 Design and Fabrication of a Low-Cost Turbine Engine Component Testbed (TECT) Joshua A. Hartman University of Tennessee - Knoxville, [email protected] Follow this and additional works at: https://trace.tennessee.edu/utk_gradthes Part of the Heat Transfer, Combustion Commons, and the Propulsion and Power Commons Recommended Citation Hartman, Joshua A., "Design and Fabrication of a Low-Cost Turbine Engine Component Testbed (TECT). " Master's Thesis, University of Tennessee, 2014. https://trace.tennessee.edu/utk_gradthes/2821 This Thesis is brought to you for free and open access by the Graduate School at TRACE: Tennessee Research and Creative Exchange. It has been accepted for inclusion in Masters Theses by an authorized administrator of TRACE: Tennessee Research and Creative Exchange. For more information, please contact [email protected]. To the Graduate Council: I am submitting herewith a thesis written by Joshua A. Hartman entitled "Design and Fabrication of a Low-Cost Turbine Engine Component Testbed (TECT)." I have examined the final electronic copy of this thesis for form and content and recommend that it be accepted in partial fulfillment of the requirements for the degree of Master of Science, with a major in Mechanical Engineering. Trevor Moeller, Major Professor We have read this thesis and recommend its acceptance: Milton Davis, James Simonton Accepted for the Council: Carolyn R. Hodges Vice Provost and Dean of the Graduate School (Original signatures are on file with official studentecor r ds.) Design and Fabrication of a Low-Cost Turbine Engine Component Testbed (TECT) A Thesis Presented for the Master of Science Degree The University of Tennessee, Knoxville Joshua A. Hartman August 2014 Copyright © 2014 by Joshua A. Hartman All rights reserved. This work or any portion thereof may not be reproduced or used in any manner whatsoever without the express written permission of the author. ii DEDICATION I dedicate this work to my family and friends who have supported me throughout this extensive effort. I particularly would like to thank my wife, Shayne, who witnessed all aspects of this work from the 8 years since its original inception, and encouraged me at every opportunity along the way. I dedicate my work to you. iii ACKNOWLEDGEMENTS I would like to thank the following individuals for their contributions to this project. Without their support, none of this would have been possible. I would like to thank a few individuals for making this work a success. Aaron Marshall worked with me early in the project when this work started at Wright State University and without his knowledge of CAD and his skills for fabrication it would not have been possible. I would also like to thank Jonathan Kolwyck from University of Tennessee for all of the help with setting up the lab. He was invaluable for help with the LabView programming and various engine subsystems. I would also like to recognize Steve Arnold for all of his assistance with setting up the high speed data system as well as being a champion for a portion of the funding required to make the TECT a reality. I am deeply indebted to all below. Dr. Trevor Moeller Advisor Dr. Milton Davis Advisor Dr. James Simonton Advisor Jonathan Kolwyck University of Tennessee Space Institute Andrew Davis University of Tennessee Space Institute Joel Davenport University of Tennessee Space Institute Dr. Rory Roberts: Wright State University Aaron Marshall Wright State University Steve Arnold Aerospace Testing Alliance David Patko Aero-Composites Frank Beafore, Eric Wise Select-Tech iv ABSTRACT With gas turbine engine testing becoming very expensive because of the increasing complexity involved with the engine, engine subsystems, and test support systems, a low-cost Turbine Engine Component Testbed (TECT) is proposed. This engine build is given the designation J1-H-02. In the present study, a small augmented gas turbine engine (GTE) is constructed. The TECT engine is built with modularity as a key design consideration to allow for flame-tube patterns and augmentor sections to be changed quickly for combustion experiments that have gained impetus due to combustion anomalies/instabilities inherent with future military engine augmentors. This testbed allows for an effective way to test new sensors or analytical techniques before full scale testing by allowing an intermediate Technology Readiness Level (TRL) at low-cost and quick schedule turnaround. The TECT was completed using a minor financial investment when matched to comparable capabilities. A data acquisition and control system was developed and tested that allows for real-time engine feedback and control schemes. The components were analyzed for the proper failure modes and performance was predicted using a combination of hand calculations and engine performance prediction software. The compressor performance was predicted using turbomachinery relationships and geometry, then compared with experimental data. The TECT engine was tested across its intended operational envelope at sea-level static (SLS) conditions, with the baseline performance data documented. The applied data reduction approaches were developed and presented. v TABLE OF CONTENTS CHAPTER I Background and Project Goals ......................................... 1 INTRODUCTION ................................................................................................... 1 Background ........................................................................................................... 2 Basic Gas Turbine Review ................................................................................. 2 Project Goals ..................................................................................................... 4 Challenges ......................................................................................................... 5 Potential Work.................................................................................................... 5 CHAPTER II Theoretical Analysis ........................................................ 8 Parametric Cycle Analysis ..................................................................................... 8 Results ............................................................................................................. 10 Performance Cycle Analysis ................................................................................ 11 Results ............................................................................................................. 12 CHAPTER III Design and Fabrication ................................................. 15 Theory of Operation ............................................................................................. 15 CAD Modeling ..................................................................................................... 17 Fabrication Techniques ....................................................................................... 18 Compressor ......................................................................................................... 20 Combustion Chamber .......................................................................................... 28 Turbine ................................................................................................................ 39 Augmentor ........................................................................................................... 40 Engine Control ..................................................................................................... 46 Engine Control Unit .......................................................................................... 46 Main Fuel Control Technique ........................................................................... 49 Main Computer Control Graphical User Interface ............................................ 52 Completed TECT Engine ..................................................................................... 57 CHAPTER IV Experimental Analysis .................................................. 58 Data Acquisition .................................................................................................. 58 Core Speed Measurement Technique ............................................................. 60 vi Temperature Measurements ............................................................................ 61 Pressure Measurements .................................................................................. 62 Centrifugal Compressor Analysis ........................................................................ 63 Baseline Engine Performance ............................................................................. 71 Data Corrections .............................................................................................. 71 Engine Starting ................................................................................................ 74 Engine Vibration Response ............................................................................. 76 Engine Performance Characteristics ................................................................ 79 CHAPTER V Conclusions and Recommendations .............................. 86 LIST OF REFERENCES ..................................................................... 87 APPENDICES ..................................................................................... 90
Details
-
File Typepdf
-
Upload Time-
-
Content LanguagesEnglish
-
Upload UserAnonymous/Not logged-in
-
File Pages143 Page
-
File Size-