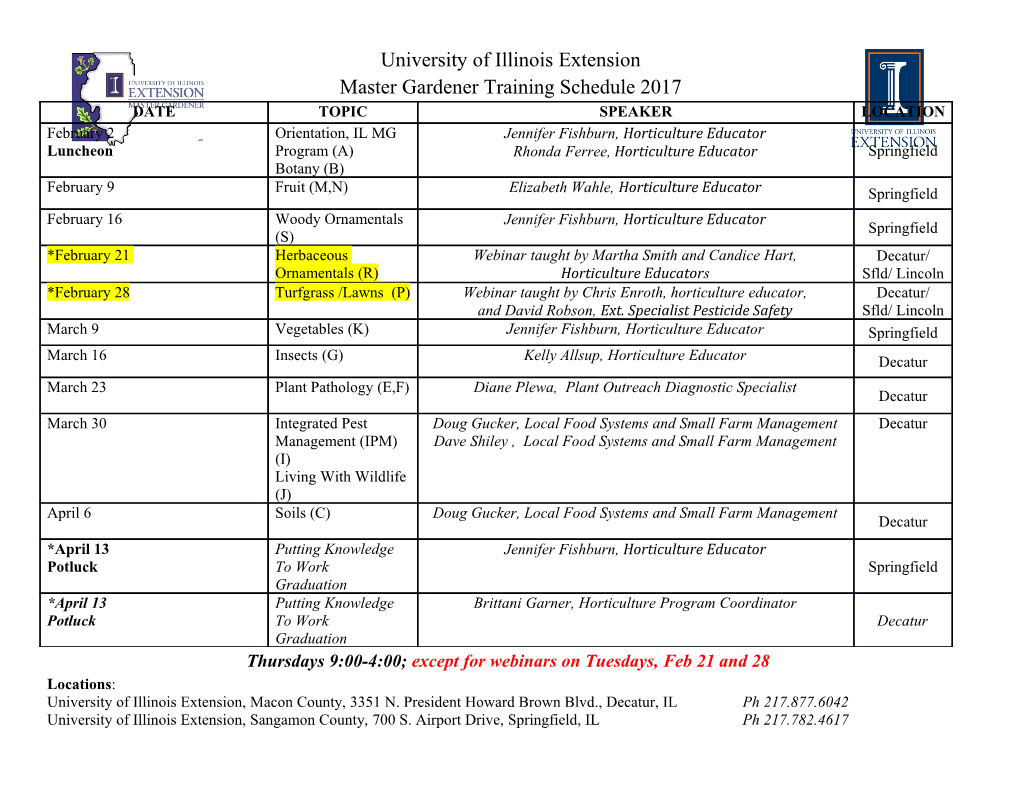
INDUSTRIAL TECHNOLOGIES PROGRAM Nissan Showcases the Results of an Energy-Wise Corporate Culture Nissan, a global automotive giant, showcases the importance of instilling a deep-rooted, company-wide culture of energy efficiency for achieving long-term success in energy management. Nissan’s emphasis on “aggressive learning” encourages its staff to challenge themselves Nissan’s commitment to smart energy “Working to manage our energy to always be the best at what they do— management goes well beyond bringing use is just good business. By including managing plant energy use. its cutting-edge electric car, the Nissan increasing our energy efficiency, LEAF™ to the market—it starts at Part of Nissan’s recipe for success in energy we use resources wisely, save the top with corporate leaders who are management is the company’s strong money on our energy bills, and true environmental champions and partnership with government agencies, reduce our carbon footprint. This have nurtured an energy-wise culture regional coalitions and nonprofit groups that approach aids in our quest to be a that flows throughout the company’s support energy efficiency. Nissan is a proud sustainable 21st century three U.S. manufacturing facilities to partner of both Environmental Protection manufacturer.” improve their technologies, operations, Agency’s ENERGY STAR® program and processes. In partnership with the and the U.S. Department of Energy’s - Mike Clemmer, Director/Plant U.S. Department of Energy’s Industrial (DOE’s) Industrial Technology Program Manager of Paint and Plastics Technologies Program, Nissan has (ITP). The ENERGY STAR program and Sub-Leader for the Energy gainfully implemented a highly offers multiple energy management tools Management Team productive energy management program and communications support resources. that has yielded reduction in energy usage Benchmarking tools also help participating even as the production scheduling has companies identify how various aspects of their energy management program are provided a unique set of challenges. performing against peer industries. ITP, in turn, facilitates the implementation of energy efficiency improvements through a variety of tools, training, and technical and The Company financial resources. Further, Nissan leverages both ENERY STAR and ITP’s resources Nissan Motor Company was founded in to forge relationships with other leading companies so it can share ideas and help these 1933 with its first manufacturing location companies meet their goals for energy reduction.3 \ in Japan. It now has 16 sites worldwide and employs 180,000 staff members Partnership with ITP 1 across the globe. Nissan North America Nissan has a long history of partnering with ITP. Its three U.S. manufacturing plants has three production plants—the Smyrna have received a combined total of nine Energy Savings Assessments from ITP and Decherd facilities in Tennessee and in conjunction with the Oak Ridge National Laboratory, and the Tennessee Tech 2 a third location in Canton, Mississippi . University and Mississippi State University Industrial Assessment Centers. These These three U.S. facilities will be the assessments yielded recommendations for a variety of energy savings projects. focus of this case study. Implementation of several of the recommended projects has enabled the plants to reduce their overall energy consumption by more than 30% and save more than $11.5 million The corporate leadership in Nissan’s per year in energy costs. These energy savings projects included the following: U.S. plants has established the mindsets and actions necessary for continuous • Installed variable-frequency drives • Upgraded and replaced chillers improvements within the company. No • Upgraded lighting and controls matter what goals the company may • Reduced number of air compressors reach or how many awards it wins, • Sub-metering & monitoring • Air recirculation continued > PROGRAM NAME 2 In its continual quest for energy 2010. While underscoring ITP’s extensive working group—an appropriate choice efficiency improvement, Nissan became support to companies in implementing as that segment of the automotive a Save Energy Now LEADER in October energy efficiency projects, the event manufacturing process typically 2009, pledging to reduce its energy showcased Nissan’s energy management consumes 70% of the energy used in intensity by 2.5% annually. Nissan also best practices to more than 100 attendees. production. The founding members of became the first company to host the These included other LEADER the Energy Management Team were Save Energy Now LEADER Industrial Companies, DOE and state-level officials, given the choice to build the best team Sustainability and Energy Management university representatives, and personnel they could by hand selecting the right Showcase at its Smyrna facility in April from Oak Ridge National Laboratory. employees to fill the additional roles. Attendees also received a tour of the plant floor and demonstration of several The team started by addressing no-cost energy efficiency and sustainability operational improvements like turning Nissan’s Energy Efficiency projects that have been implemented by off anything they could when it wasn’t Showcase: Smyrna Plant, Nissan and have generated significant needed during weekends or between Tennessee financial and environmental benefits. shifts. In the first year, the Energy Management Team saved 11.4% in Nissan’s Smyrna, Tennessee, plant absolute energy usage. In 2007, they were opened in 1983. The first vehicle the Cultivating a Culture tasked with trimming another 30% over facility produced was the Datsun of Energy Efficiency the next four years—a goal they achieved truck. The plant has since grown to What makes Nissan’s approach to energy by the end of 2008, shortly before the occupy close to 6 million square feet of efficiency notable is it’s all out emphasis floor space with an annual production economic downturn began. on creating and maintaining a corporate- capacity of 550,000 vehicles per year, Responsibility for the energy budget falls as of 2010. wide culture of energy efficiency. To this end, Nissan developed its energy program on each plant’s director. This not only • Since 2007, the facility has in 2006. The energy management team supports the development of an energy undergone three Energy Savings was one of 10 cross-functional teams culture at the plant level but also implies Assessments. created by the newly-appointed Nissan that the person who is responsible for • In 2010, the facility received a $1.4 North America Senior Vice President Bill decisions on the shop floor is deeply billion loan from the DOE Loan Krueger. Mr. Krueger took his post with attuned to the importance of energy use. Guarantee Program to retrofit the a major goal in mind – to empower all of As they see and become aware of projects plant for producing the zero- Nissan’s employees to take responsibility and opportunities for energy savings, an emission, electric NISSAN LEAF®. for the future of the company and to drive empowered choice or decision can be • Production of the NISSAN LEAF® is its competitiveness in the marketplace. made with limited delay for approval. expected to create up to 1,300 jobs. The team’s success is based on • In 2010, Nissan North America was The Energy Management Team named ENERGY STAR® Partner of Initially dubbed “Manufacturing transparent, data-driven systems. Each the Year. The facility has received Competitiveness Teams” or MCTs, the of Nissan’s plants has energy meters that multiple ENERGY STAR awards and Energy Management Team was the measure the facilities’ usage and over is a distinguished ENERGY STAR first of the new cross-functional teams time, their progress toward efficiency labeled facility. established. Mr. Krueger appointed the goals. Nissan’s measurement and paint plant director as the head of this verification (M&V) system takes a broad continued > PROGRAM NAME 3 approach to data gathering on a variety of processes, including lighting, space temps, production equipment and hourly utilities monitoring. Seeing the results of their efforts motivates employees and has raised awareness of the team company- wide. The Energy Management Team regularly has a waiting list of employees volunteering to serve on the team, but with this energy culture, everyone has the opportunity to participate. “Employees are encouraged to Nissan 2010 Employee Earth Day Fair internalize sustainability at a bring unique perspectives and value to newsletters, scrolling messages on personal level, at home and in their the process. The Energy Management TVs located in break areas, as well as community, so they come to the Team is made up of personnel from presentations in company meetings. workforce with a new perspective manufacturing, engineering, legal, Utilizing more than one communication and new vision.” environmental, finance and other method allows employees to take in operational roles. Nissan thus effectively the information through their preferred - Susan Brennan propagates a corporate-wide culture of method, increasing the chances of Vice President, energy efficiency – driven by the top retention and implementation. In Smyrna & Decherd Facilities management and implemented at the addition, Nissan has established plant level. internal certificates and awards to provide recognition to high-performing This model’s value is reiterated by NNA’s employees from each plant. Onsite Energy Team Facilitator, Ken Roden: Top-Down / Bottom-Up Approach contractors
Details
-
File Typepdf
-
Upload Time-
-
Content LanguagesEnglish
-
Upload UserAnonymous/Not logged-in
-
File Pages4 Page
-
File Size-