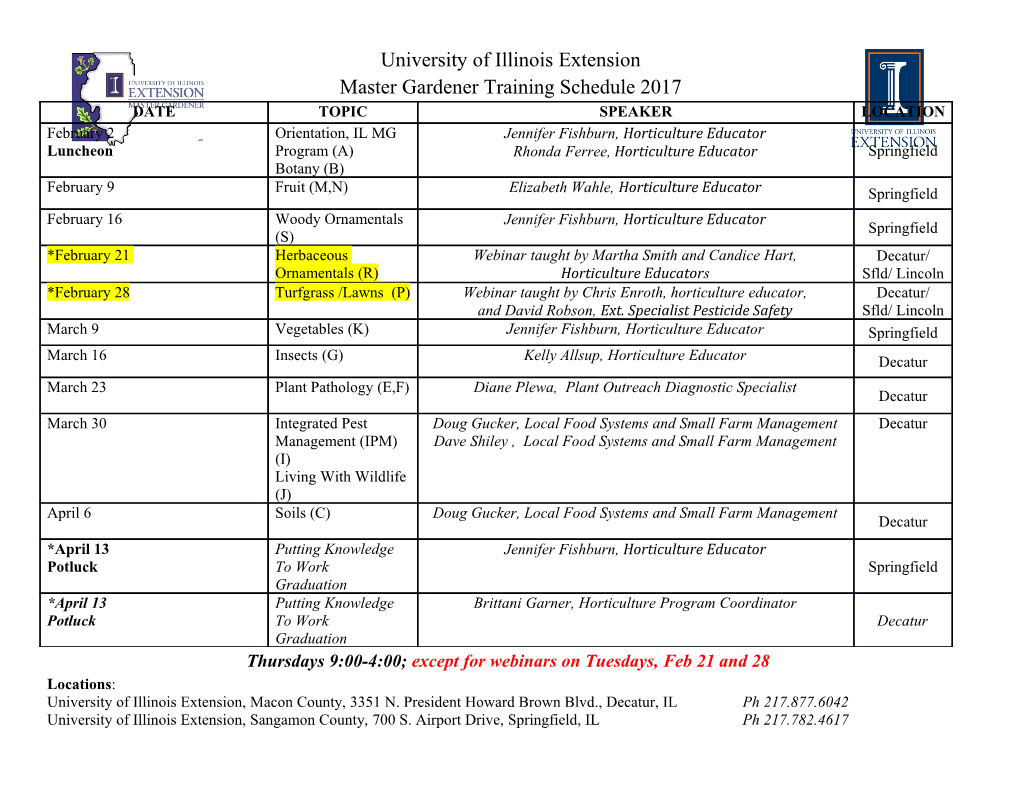
GAS CLEANING TECHNOLOGY Rectisol™ column design with structured packings By using a Rectisol™ demonstration unit at one of Air Liquide’s industrial production sites, Air Liquide Engineering & Construction has gained unique know-how in Rectisol™ column design with structured packings. S. Schmidt, R. Szabo, M. Linicus and S. Corbet report on how the application of commercially available structured packings in the absorber columns of a Rectisol™ unit results in significant capex and opex savings. ectisol™ gas cleaning technol- is correspondingly high. If the diameter of ogy is the leading technology for the column is reduced, the hoop stress is Rproviding high purity syngas for decreased, which leads to reduced capi- applications such as methanol, ammo- tal expenditure for the absorber. As the nia, Fischer-Tropsch fuels and synthetic absorber represents up to 10% of the total natural gas (SNG), as well as hydrogen. equipment costs for a Rectisol™ unit, the The Rectisol™ process uses methanol benefit of size reduction is clear. as a solvent for the selective removal of For most projects, the remote location CO2, sulphur (H2S, COS) and various trace of the plant site imposes a limit on the components (NH3, HCN, CS2, mercaptans, capacity to transport the sizeable equip- BTX, metal carbonyls). Air Liquide has ment by road. This often results in a parallel more than 110 references where Recti- absorber setup, instead of a setup with just sol™ units have been deployed worldwide, one absorber above the transportation limit. IMAGES: SULZER as well as operational experience from its Absorber diameters above this limit have to own production plants1. be avoided to prevent additional cost. In the Rectisol™ process, the absorp- Traditionally, absorber columns have tion takes place under high pressure been designed with trays. However, struc- and low temperature, i.e. process condi- tured packings in high pressure absorber tions that are favourable for absorption. columns offer considerable advantages The temperature in the absorber can be over trays making them of interest within as low as -75°C, the pressure is typically absorption applications. These advantages higher than 30 bar. At this pressure level, include lower pressure drop and a larger Fig. 1: Typical internals: structured packing the hoop stress of the column is consid- active area (no downcomer), enabling the (top) and trays (bottom). erable and the required shell thickness processing of higher liquid loads. Illustra- tions of trays and structured packings are Fig. 2: Integration of the Rectisol™ demonstration unit with the industrial Rectisol™ unit shown in Fig. 1. Fig. 2 shows a simplified setup of a purified syngas Rectisol™ unit. Raw syngas enters the absorber absorber column and is processed subse- CO2 product quently in the different absorption sections CO2 fine wash for sulphur removal (H2S, COS), CO2 bulk removal sections (CO2 cooling section and CO2 main wash reabsorber CO2 main wash section) and CO2 fine wash section. The laden solvents are then sent CO2 cooling CO2 flashing reabsorption to the flash regeneration sections, in which high purity CO ready for use or storage is raw syngas hot H S, COS 2 CO flashing 2 S removal 2 stripping regeneration produced. Afterwards, the solvent enters the reabsorber column. In the reabsorber, N 2 the remaining CO2 is stripped out with RDU nitrogen under low pressure (stripping sec- tions) and flashed-out sulphur components Source: Air Liquide are “re-absorbed” again (hence the name) and routed to the hot regeneration section, 40 www.nitrogenandsyngas.com Nitrogen+Syngas 371 | May - June 2021 GAS CLEANING TECHNOLOGY Fig. 4: Capacity diagram with typical operating ranges for the tested Rectisol™ sections (typical structured packing performance data are given4) 0.25 X: flow parameter L ρG C : capacity factor, m/s X = S G ρL 3 1/2 Sulzer M125.X FS: F-factor, m/s (kg/m ) 0.2 L: liquid mass rate ρG G: gas mass rate C = v S ρL–ρG ρL: liquid density 0.15 ρv: gas density F = v ρG v: superficial gas velocity, m/s S Sulzer M250.X 0.1 ion t capacity factor, m/s capacity factor, oval m e eabsorp r r 0.05 r g u n pi lph p wash cooling u ri 2 2 e s t O s O n fi C C CO2 main wash PHOTO: AIR LIQUIDE 0 Fig. 3: Rectisol ™ demonstration unit. 0.01 0.1 1 10 Source: Air Liquide flow parameter where the solvent is cleaned of any remain- ing sulphur components and an H2S rich stream is generated. Fig. 5: Air Liquide Rectisol™ absorber diameter for structured packings and The lean solvent is then recycled back tray design; typical ranges derived from Air Liquide engineering and to the absorber after cooling and re-used construction projects for absorption. To investigate the per- formance of structured packings within 2 ™ 1.2 Rectisol technology, Air Liquide designed 2 and installed a demonstration unit at one of 1.1 its industrial production sites (Fig. 2 lower section and Fig. 3). The Rectisol™ Demonstra- 1 tion Unit (RDU) is operated in bypass to an FT fuels SNG industrial Rectisol™ unit and is thereby able 0.9 to operate under real process conditions. structured packing design, 35-55 bar, 25-35 mol-% CO 0.8 standard tray design, 35-55 bar, 25-35 mol-% CO Liquid and gas streams from the absorber and reabsorber of the industrial 0.7 production unit can be withdrawn at differ- methanol ent locations via 25 different tie-in lines, normalised absorber diameter 0.6 processed and tested at the RDU and hydrogen finally routed back to the production unit2. 0.5 waste-/biomas-to-fuel During the test campaigns at the RDU, 0.4 performance data for different structured 200,000 400,000 600,000 800,000 1,000,000 packing types in the absorber and reab- gas capacity, Nm³/hr sorber sections have been gathered and Source: Air Liquide column design rules developed. Fig. 4 gives an overview over the tested Rectisol™ sections with their typical flow data for typical structured packings4 are also plant. The operational and capital expendi- regimes. The ranges for liquid and gas shown in the diagram. It can be observed tures (opex, capex) are then compared to loads for the different operation sections that the loadings of the different sections the actual as-built plant. differ widely. While the three CO2 absorption have to be addressed by packings with high sections feature high liquid loads with flow capacities. Results: diameter reduction parameters between 1 and 3, the reabsorp- In this article, the impact of the appli- tion sections show lower liquid loads with cation of structured packings within a Rec- To evaluate the diameter reduction for lower flow parameters of 0.05-0.7. To show tisol™ unit is evaluated in relation to two Rectisol™ absorbers with structured pack- the exceptionally wide operating range of different aspects: first, the diameter reduc- ing design, two designs were prepared the columns within a Rectisol™ unit, the flow tion potential of the absorber is evaluated. for 16 different feed gases from actual parameters for high-pressure distillation are Second, the application of structured projects. One design featured a standard in the range of 0.1-0.33. As a reference for packings within the absorber and reab- tray design, the other a structured pack- structured packing performance, the capacity sorber is simulated for an industrial as-built ing design based on the know-how gener- Nitrogen+Syngas 371 | May - June 2021 www.nitrogenandsyngas.com 41 GAS CLEANING TECHNOLOGY Fig. 6: Capital cost for absorbers with tray design and stuctured packing recovery. Additionally, less electricity is required for pumps due to the lower oper- ating pressures in the regeneration sec- standard tion. All in all, the application of structured d= V= ™ tray design 92% 8% 100% 100% packings within the Rectisol unit results in 17% opex savings, including savings for refrigeration duty of 19%, electricity 16% structured d= V= and steam of 18% compared to the case packing design 54% 7% shell internals 73% 48% with the tray design. Taking account of the indirect CO2 emissions arising from steam 0 20 40 60 80 100 and electricity, 16% less CO2 is emitted. absorber capital cost Due to the reduced solvent flow rates Source: Air Liquide and the smaller absorber, the size of other equipment is also reduced, resulting in an overall capex reduction on the Rectisol™ ated by the RDU. The gas capacity ranged As a reference, this setup was com- equipment of 7%. from 180 kNm³/h-900 kNm³/h, pressure pared to an industrial as-built plant with Air Liquide Engineering & Construction ™ ranged from 35-55 bara and CO2 content tray design for both the absorber and reab- is able to tailor Rectisol column design in the feed gas ranged from 25-35 mol-%. sorber. The opex was evaluated using util- to the needs of its clients. It should be For a fair comparison, both designs have ity costs for a Chinese location. The capex noted that the benefits as evaluated and been conducted using widely commercially for both cases were also evaluated on a presented above can be obtained by imple- available mass transfer internals. high level basis. mentation of state-of-the-art, widely avail- Fig. 5 shows a normalised absorber The outcome for the absorber with dedi- able structured packing as mass transfer diameter against the feed gas capacity cated sections for CO2, H2S and COS and internals. Air Liquide Engineering & Con- for trayed and structured packing design. trace component removal is summarised struction is also able to apply sophisti- Most importantly, the diameter reduction in Fig.
Details
-
File Typepdf
-
Upload Time-
-
Content LanguagesEnglish
-
Upload UserAnonymous/Not logged-in
-
File Pages4 Page
-
File Size-