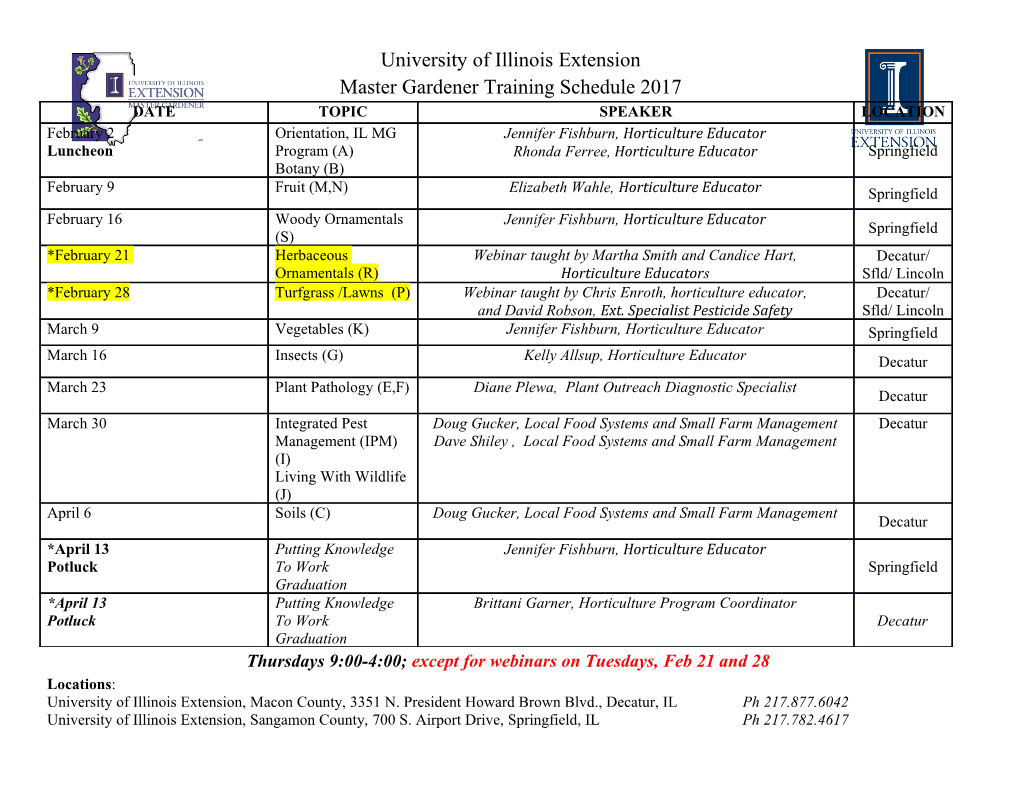
metals Article Effect of Heterogeneous Microstructure on Refining Austenite Grain Size in Low Alloy Heavy-Gage Plate Shengfu Yuan 1, Zhenjia Xie 2 , Jingliang Wang 2, Longhao Zhu 3, Ling Yan 3, Chengjia Shang 2,3,* and R. D. K. Misra 4 1 School of Materials Science and Engineering, University of Science and Technology Beijing, Beijing 100083, China; [email protected] 2 Colarborative Innovation Center of Steel Technology, University of Science and Technology Beijing, Beijing 100083, China; [email protected] (Z.X.); [email protected] (J.W.) 3 State Key Laboratory of Steel for Marina Equipment and Application, Anshan Steel, Anshan 114021, China; [email protected] (L.Z.); [email protected] (L.Y.) 4 Laboratory for Excellence in Advanced Steel Research, Department of Metallurgical and Materials Engineering, University of Texas at El Paso, El Paso, TX 79912, USA; [email protected] * Correspondence: [email protected]; Fax: +8610-6233-2428 Received: 18 November 2019; Accepted: 13 January 2020; Published: 16 January 2020 Abstract: The present work introduces the role of heterogeneous microstructure in enhancing the nucleation density of reversed austenite. It was found that the novel pre-annealing produced a heterogeneous microstructure consisting of alloying elements-enriched martensite and alloying-depleted intercritical ferrite. The shape of the martensite at the prior austenite grain boundary was equiaxed and acicular at inter-laths. The equiaxed reversed austenite had a K-S orientation with adjacent prior austenite grain, and effectively refined the prior austenite grain that it grew into. The alloying elements-enriched martensite provided additional nucleation sites to form equiaxed reversed austenite at both prior austenite grain boundaries and intragranular inter-lath boundaries during re-austenitization. It was revealed that prior austenite grain size was refined to ~12 µm by pre-annealing and quenching, while it was ~30 µm by conventional quenching. This is a practical way of refining transformation products by refining prior austenite grain size to improve the strength, ductility and low temperature toughness of heavy-gage plate steel. Keywords: alloying element enrichment; heterogeneous microstructure; nucleation site; grain refinement 1. Introduction Low carbon low alloy steels have been widely used in fields of marine engineering, engineering machines, and other structural applications due to their high strength, excellent toughness, good weldability and low cost [1–3]. With the structural components becoming large and the need for cost effectiveness, there is a significant demand for heavy gauge plate steel. However, for low carbon low alloy heavy-gage plate steel manufactured by thermomechanical controlling process (TMCP), austenite grains in the center of the plate gradually become larger due to insufficient reduction in thickness during controlled rolling. This leads to the deterioration of mechanical properties, especially low-temperature toughness [4–6]. Therefore, a heat treatment process should be applied to optimize the mechanical properties of heavy plate. Austenite grain refinement is well recognized as being of great importance in enhancing mechanical properties of high strength low alloy steels [7–9]. Several efforts have been made towards the refining of austenite grain size. Grange [10] reported that the thermal cycling process between martensite and austenite is helpful in refining austenite grain size by reversed transformation. The effect of the Metals 2020, 10, 132; doi:10.3390/met10010132 www.mdpi.com/journal/metals Metals 2020, 10, x FOR PEER REVIEW 2 of 11 Metals 2020, 10, 132 2 of 11 effect of the two-step quenching (TSQ) and one-step quenching (OSQ) heat treatment process on austenite grain size was studied [11], and the results showed that the prior austenite grain size of TSQtwo-step heat-treated quenching specimen (TSQ) andwas one-step 50% finer quenching than OSQ (OSQ) heat heattreatment. treatment Further process studies on austenite[12–14] found grain twosize morphologies was studied [11 of], reversed and the resultsaustenite showed from marten that thesite prior or bainite: austenite equiaxed grain size austenite of TSQ and heat-treated acicular austenitespecimen during was 50% thermal finer than cycling OSQ heatprocess treatment. and multi- Furtherstep studiesheat treatment [12–14] found process. two In morphologies addition, the of mechanismreversed austenite of prior from austenite martensite grain or bainite:refinement equiaxed was attributed austenite and to acicularthe enhancement austenite during of nucleation thermal densitycycling processof equiaxed and austenite multi-step by heat thermally treatment activat process.ed nucleation In addition, or static the mechanism recrystallization of prior [15]. austenite grainThere refinement is a vast was literature attributed [13,14 to the,16–21] enhancement reporting ofthat nucleation reversed density austenite of equiaxednucleates austeniteat the prior by austenitethermally grain activated boundary, nucleation intersection or static recrystallizationof multiple-grains, [15 ].packet boundary, block boundary and cementite.There Miyamoto is a vast literature [22] pointed [13,14 ,out16– 21that] reporting austenite that preferentially reversed austenite nucleates nucleates at the athigh the angle prior boundaryaustenite grainof pearlite-ferrite. boundary, intersection Studies [23,24] of multiple-grains, on the crystallographic packet boundary,characteristics block determined boundary that and acicularcementite. austenite Miyamoto [had22] pointedKurdjumov–Sachs out that austenite (K-S) preferentially orientation nucleates relationship at the high ((111) anglefcc boundary//(011)bcc, [of−101] pearlite-ferrite.fcc//[−1–11]bcc) Studieswith the [23 matrix,,24] on while the crystallographic equiaxed austen characteristicsite nucleated determinedat prior austenite that acicular grain boundariesaustenite had grew Kurdjumov–Sachs into the adjacent (K-S) prior orientation austenite relationship grain at high ((111) angle// misorientation(011) ,[ 101] [23].//[ This1–11] also) fcc bcc − fcc − bcc suggestedwith the matrix, that the while equiaxed equiaxed austenit austenitee was nucleatedbeneficial in at refining prior austenite austenite grain grain boundaries size. In addition, grew into some the literaturesadjacent prior [25–28] austenite published grain that at high cementite angle misorientation was the core [of23 ].austenite This also nucleation. suggested However, that the equiaxed in this study,austenite the was content beneficial of carbon in refining is 0.08 austenite wt. %, grain which size. was In addition,too low to some grow literatures to the [core25–28 of] publishedaustenite nucleation.that cementite In contrast, was the corethe cement of austeniteite was nucleation. easily decomposed. However, inIn thisthis study,study, the a novel content pre-annealing of carbon is process0.08 wt. prior %, which to quenching was too low was to growintroduced to the coreto increase of austenite nucleation nucleation. density In contrast,of equiaxed the cementitereversed austenitewas easily and decomposed. refine austenite In this grain study, size a novel in the pre-annealing core of heavy process plate. priorMicrostructure to quenching evolution was introduced during heatto increase treatment nucleation was studied density to of elucidate equiaxed the reversed mechanism austenite of andaustenite refine grain austenite refinement grain size by in pre- the annealingcore of heavy and plate.quenching. Microstructure evolution during heat treatment was studied to elucidate the mechanism of austenite grain refinement by pre-annealing and quenching. 2. Experimental Material and Procedure 2. Experimental Material and Procedure The chemical composition of experimental steel was C 0.08, Si 0.23, Mn 1.21, P 0.011, S 0.002, Ni 1.1, (CuThe + chemicalCr + Mo) composition < 2.0, Nb 0.022, of experimental B 0.0012 and steel Ti 0.014 was in C 0.08,weight Si 0.23,percent Mn (wt. 1.21, %). P 0.011,The A SC1 0.002, and A NiC3 temperatures1.1, (Cu + Cr +wereMo) measured< 2.0, Nb by 0.022, dilatometry B 0.0012 to and be Ti 715 0.014 and in 863 weight °C, respectively. percent (wt. Three %). The specimensAC1 and (denotedAC3 temperatures as 1#, 2#, were 3#) with measured dimensions by dilatometry of 10 mm to (rolling be 715 direction) and 863 ◦C, × 3 respectively. mm (transverse Three direction) specimens × 10(denoted mm (thickness) as 1#, 2#, were 3#) with cut dimensionsfrom the center of 10 of mm the (rolling experimental direction) plate 3steel mm which (transverse was hot direction) rolled to × × 10010 mm mm (thickness) by TMCP, were because cut from of inferior the center mechanical of the experimental properties plate of center steel which plate. was Heat hot treatments rolled to 100 were mm carriedby TMCP, out because as shown of inferior in Figure mechanical 1. Specimen properties 1# wa ofs reheated center plate. to 900 Heat °C treatments for 30 min were for carriedcomplete out re- as austenitization,shown in Figure 1and. Specimen then quenched 1# was reheated to room to 900temp◦Cerature for 30 min(Figure for complete 1a). To re-austenitization,isolate the effect and of intercriticalthen quenched annealing, to room temperaturespecimen 2# (Figurewas isothermally1a). To isolate held the for effect 30 ofmin intercritical at 740 °C annealing,followed specimenby water quenching2# was isothermally to room temperature held for 30 min(Figure at 740 1b),◦C to followed distinguish by water the
Details
-
File Typepdf
-
Upload Time-
-
Content LanguagesEnglish
-
Upload UserAnonymous/Not logged-in
-
File Pages11 Page
-
File Size-