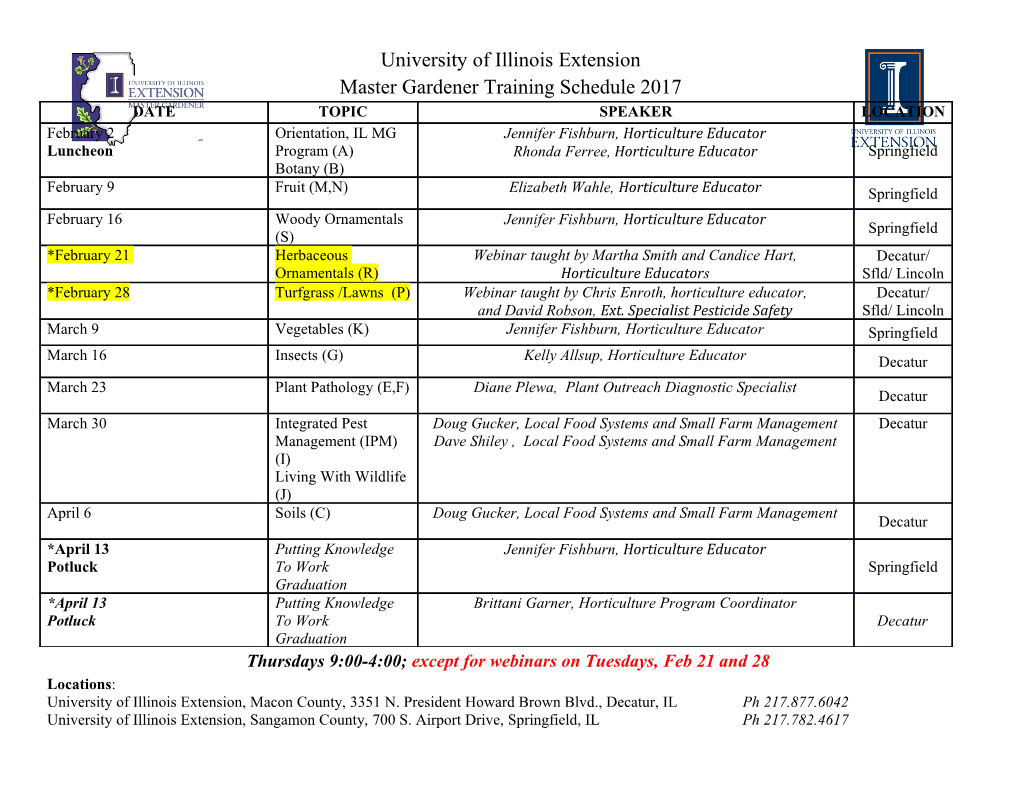
ICES-2020-164 Thermal design, analysis and testing of Solar Orbiter Stood- Off Radiator Assembly Stefan Herndler1 and Christian Ranzenberger-Stindl2 RUAG Space GmbH, Stachegasse 16, 1120 Vienna, Austria Mark Grimminck3 Airbus Defence and Space Netherlands B.V., Mendelweg 30, 2333 CS Leiden, The Netherlands and Claudio Damasio4 European Space Agency, ESTEC, Keplerlaan, 1, 2201 AZ Noordwijk, The Netherlands Solar Orbiter is a solar-heliospheric ESA mission investigating how processes on the Sun drive the properties and phenomena of the heliosphere. To achieve this, Solar Orbiter will perform 22 orbits around the Sun, with perihelions up to 0.28 AU and 1.02 AU as maximum aphelions, carrying a payload of six remote sensing instruments and four in-situ instruments. Five of the six remote sensing instruments (EUI, METIS, PHI, SPICE, STIX) have very stringent temperature requirements and are therefore mounted on the internal side of the spacecraft (S/C). To maximize efficiency of the radiators of these instruments it is necessary to thermally decouple the radiators from the S/C’s interior and structure to a maximum extent. Therefore, they are attached to the external sides of the S/C via insulating iso-static mounts, forming the so-called Stood-Off Radiator Assembly (SORA). The instruments are thermally coupled to the radiators by flexible thermal links and rigid conduction bars. For an improved thermal efficiency of the radiators in some cases encapsulated annealed pyrolytic graphite (APG) is used. Heat pipes are also used for heat transportation to allow for the geometric distribution of the separate radiators in the limited available volume. The SORA radiators are white-coated except for one, which uses optical surface reflectors (OSRs). In addition to an extensive testing and characterization on component level a sub-system verification was performed via a Thermal Balance (TB) test on a subset of the SORA containing all relevant technologies (iso-static mounts, flexible thermal links, conduction bars, encapsulated APG, white coating, OSRs, heat pipes and multi-layer insulation). The paper provides details about the thermal design of the SORA, the component and TB test campaign as well as the correlation of the TB test thermal model yielding verified modelling parameters for flight predictions of the SORA. Nomenclature APG = Annealed Pyrolytic Graphite AU = Astronomic Unit CE = Cold Element EMC = Electro-Magnetic Compatibility ESD = Electrostatic discharge EUI = Extreme Ultraviolet Imager - Internal Remote Sensing Instruments 1 Systems Engineer, Thermal Systems, [email protected] 2 Manager Engineering Space, Thermal Systems, [email protected] 3 Lead Engineer, [email protected] 4 Solar Orbiter Thermal System Engineer, Thermal Division (TEC-MT), [email protected] Copyright © 2020 Stefan Herndler GAM = Gravity Assist Maneuver GFRP = Glass-Fiber Reinforced Plastic HE = Hot Element ISM = Iso-Static Mount ITO = Indium Tin Oxide ME = Medium Element METIS = Multi Element Telescope for Imaging and Spectroscopy, coronagraph - Internal Remote Sensing Instruments MLI = Multi-Layer Insulation OSR = Optical Surface Reflector PHI = Polarimetric and Helioseismic Imager - Internal Remote Sensing Instruments S/C = Spacecraft SLI = Single-Layer Insulation SORA = Stood-Off Radiator Assembly SPICE = Spectral Imaging of the Coronal Environment - Internal Remote Sensing Instruments STIX = X-ray Spectrometer/Telescope - Internal Remote Sensing Instruments TB = Thermal Balance TMM = Thermal Mathematical Model TP = Test Phase VDA = Vacuum Deposited Aluminum I. Introduction HE mission of Solar Orbiter S/C is dedicated to solar and heliospheric physics. Solar Orbiter is an ESA-led T mission with strong NASA participation. It was selected as the first medium-class mission of ESA's Cosmic Vision 2015-2025 program. It will be used to examine how the Sun creates and controls the heliosphere, the vast bubble of charged particles blown by the solar wind into the interstellar medium. The science payload of Solar Orbiter comprises six remote sensing and four in situ instruments to gain new information about the solar wind, the heliospheric magnetic field, solar energetic particles, transient interplanetary disturbances and the Sun's magnetic field. Launched on February 10th 2020, the mission will provide close-up, high-latitude observations of the Sun. Solar Orbiter will perform 22 highly elliptic orbits – between 1.02 AU at aphelion and 0.28 AU at perihelion. It will reach its operational orbit just under two years after launch by using gravity assist maneuvers (GAMs) at Earth and Venus. Subsequent GAMs at Venus will increase its inclination to the solar equator over time, reaching up to 24° at the end of the nominal mission (approximately 7 years after launch) and up to 33° in the extended mission phase. To allow Solar Orbiter to withstand the very high solar flux at 0.28 AU, about 17500 W/m2 (i.e. about 13 solar constants), the sun-pointing S/C features a heat shield to provide a complete sun shielding of the platform itself and act as thermal insulation of the entire S/C including all equipment and parts of the structure within an 8º half-cone to cover both the operational modes of the satellite and maximum allowed off-pointing when the satellite enters safe mode. II. Description of Stood-Off Radiator Assembly Five remote sensing instruments installed within the platform (EUI, METIS, PHI, SPICE, STIX) are operational around closest approach, and at the minimum and maximum heliographic latitudes. Key to the mission success is the maintenance of the stringent thermal environment of the payload sensors: some instrument interfaces (called elements) have to be kept at temperature lower than -40°C or -50°C with a heat rejection capability of 5 W or more. In addition, payloads require accurate and adjustable alignment at integration using iso-static mounts (ISMs), which restrict the efficiency of heat rejection as the payloads are not directly mounted to the panel. The temperature distribution across the platform affects the thermoelastic distortion of the platform and thus the pointing accuracy of the payloads. An additional and important driving requirement is the mechanical interface load to the instrument feet. Those requirements drive the choice to control the thermal environment of these items primarily by stood-off radiators which are connected to the units via thermal links to avoid heat transfer from the S/C structure to the payload radiators. 2 International Conference on Environmental Systems The stood-off radiators are thermally isolated from the S/C panel, providing two key advantages. Firstly as the radiators are a separate item to the panel the thermo-elastic distortion of the panel onto which the payload is mounted is reduced due to the warmer panel temperature. Secondly, the required radiator area will be smaller as heat leak to the radiator from the rest of the S/C is restricted. +Z The payload radiators are located on the –Y and +Z walls as +Y shown in Figure 1, with the +X wall carrying the heat shield, which is nominally sun-pointing throughout the mission. Those on –Y wall are +X in view of the solar array, which at the near sun distances operates at a E high temperature. Purpose of the radiators was to radiate to space the E C PIC heat dissipated by the remote sensing instrument, the solar flux S passing through the feedthroughs, the parasitic heat from the platform to the instruments themselves and to radiators, the IR flux from the solar array and last the small amount of solar flux reflected by the solar arrays. Thermal design effort was required to ensure the coldest E I H payload interface temperatures are achievable in these environments. EU The radiator location was optimized mainly taking into account the position of the relevant remote sensing instruments and the IR flux IX ST 1 and reflected solar flux coming from solar arrays. ME UI To minimize the impact of thermo-elastic distortion whilst E E I C ensuring that the instruments are well coupled to any heat rejection EU system, there was the need of a good thermal conduction pathway E H without hard mounting onto the S/C panels. This challenge was TIS ME addressed in the use of flexible thermal links and thermal conductive E2 bars. The use of flexible thermal links enables good thermal contact M E UI C E IS between hot elements and cold fingers of the instruments with the ET E M E radiators whilst the flexibility of the link allows for mechanical M I C TIS PH decoupling of the payload. This permits the payload to be mounted ME E iso-statically, making the design tolerant to any distortions in the S/C H HI panel beneath. As the METIS instrument already planned to use P flexible straps on the payload side of the element interfaces, the link between the element and the radiator needs to be rigid. This is to Figure 1. Stood-Off Radiator Assembly. minimize deflection at the element which would cause the METIS straps to flex. For this reason, conduction bars have been used. III. Detailed Design of Stood-Off Radiator Assembly The radiator panels forming the SORA are nominally designed based on a traditional radiator design of a solid aluminum thermally functional structure in combination with a lightweight mechanical structure to provide sufficient stiffness with a minimum impact on overall mass. The panels are supported by highly thermally isolating glass-fiber reinforced plastic (GFRP) ISMs with a flexible blade design pointing to a nominal thermal center to minimize thermo-elastic loads within the structure. Mechanical decoupling/thermal coupling of the radiators to the instruments (EUI, PHI, SPICE, STIX) is typically made with Airbus Defence and Space Netherlands HiPeR flexlinks ensuring that only marginal mechanical loads are transferred to the instrument interfaces from thermo- elastic, mechanical dynamic or mounting misalignment loads. The METIS instruments are thermally coupled via rigid K-Core thermal links with further thermal and mechanical (de)coupling undertaken by the METIS instrument.
Details
-
File Typepdf
-
Upload Time-
-
Content LanguagesEnglish
-
Upload UserAnonymous/Not logged-in
-
File Pages12 Page
-
File Size-