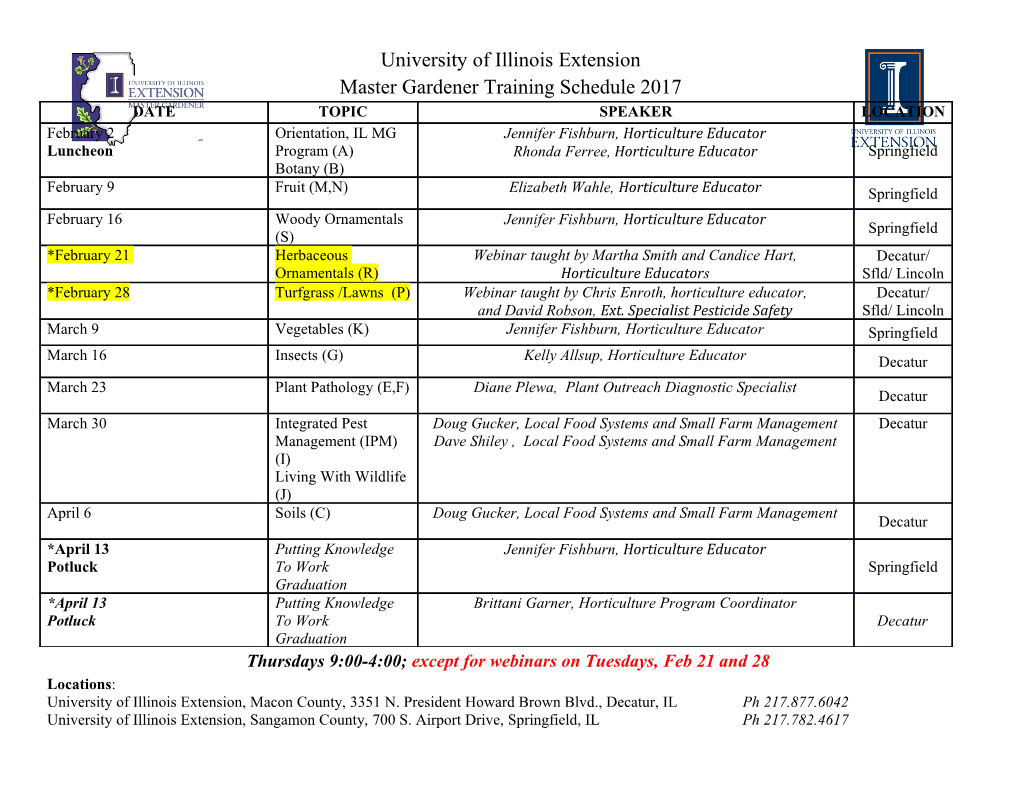
Part 1 of a Series: Lean Thinking Henry Ford’s Managerial Mindset Moral of the story: Don’t hang on to a fading dream. Robert W. Hall espite his own writing, plus vol- Design of the Model T umes written about him, Henry Several people tried automotive Ford’s complex contradictions are D assembly lines before the Model T, notably hard to fathom. Many, including Taiichi Ransom Olds; low volumes and poor parts Ohno, the leader of Toyota’s development fit caused a few problems, but the Curved of the Toyota Production System, have cited Dash Olds is acknowledged to be the first the development of his Model T as the cra- mass-produced car. (Mass production of dle of ideas for lean manufacturing. Henry’s watches and other items was old news, but story is not as simple as thumbnail versions the car was a big leap.) Henry’s vision of an depict, so it is worth review, in three sec- assembly line was foggy, but he — among tions; design, development of the Ford about a hundred other entrepreneurs — System, and his leadership, with lessons was determined to design a “car for the still relevant in a Web 2.0 age. masses.” Low-end vehicles then sold in the $400 to $900 range, but nobody gained enough margin on them to draw the capital to go big time. Upper-end cars went for $2000 to $4000. So Henry was on a mis- sion; bring cars to the masses. From 1903 until birth of the Model T In Brief in1908, The Ford Motor Company was like a development lab that sold cars. The T was The sharp contrasts between “Fordism” and its younger cousin, the successor to Models A, B, C, F, K, N, R, lean thinking, meet in the mindset of Henry Ford I. Now, even lean and S, skipping the prototypes never sold. systems as we practiced them are apt to be insufficient for the per- Determined to make the 1908 T design a formance necessary in the new era of global financial uncertainty. breakthrough, Ford combined the best First of a series. ideas he could find to improve performance for the customer in a simple package: the 14 Target Volume 25, Number 2 best materials, best men to be hired, and simplest, lightest design that could be devised. Ford was intrigued with vanadium alloy steel, lighter and stronger than carbon alloys. It had been used for specialty parts, but producing it in quantity for a mass pro- duced vehicle was another matter. Henry gambled and went for it. The engine block for four cylinders was cast as one piece, with a detachable head, unusual at the time. It had fewer parts, and they were simpler to cast and Figure 1. Ford Model T motor car, 1916. The Ford Model T was introduced by Henry machine. By mounting the engine at only Ford (1863-1947) in 1908. three points, the frame could twist on the rough roads without breaking a mount, also a problem with cars of the period, whose frames were heavy and rigid rather than light and flexible. And the T’s ten-inch road clearance helped avoid bellying down in mud or bellying up on a tree stump. The two-speed planetary gear trans- UPS delivery truck was a modified Model T. mission wasn’t novel, but was kept because This design coup let Ford cream the it was easy for novice drivers to master. The market with an $850 price tag and start master-stroke was integrating the magneto rolling in cash to build a huge integrated (designed by Spider Huff, an outside con- production system, only part of which was sultant) with the engine and transmission the assembly line. Henry needed no into a single unit that could be installed at accountants wielding sharp pencils; he just final assembly, and all using the same oil. did it. As the volume went up, the price The 1200-pound curb weight of the eventually dropped under $300 for the basic whole package gave it a horsepower-to- touring car, less than four month’s pay for weight ratio equal to expensively engi- the average worker. Cash also let Ford pur- neered performance cars of the day, but sue all kinds of innovative ideas, for exam- easy to fabricate and assemble. (The author ple, uses for soybeans, which turned it into once participated in a college prank of dis- a popular Mid-Western crop. In 1941, he assembling one and reassembling it in the exhibited a “soybean car,” with a body part- hapless owner’s dorm room.) And this base ly derived from soybeans, although nobody design let Ford adapt it to many purposes: knows exactly how it was done. Ford also town cars; runabouts; trucks; panel trucks. believed that eventually petroleum scarcity That all Model Ts looked alike is a legend; would make biofuels necessary, so he Ford morphed it into many configurations experimented off and on with ethanol as a during its 20-year run, but all those modifi- fuel. During Prohibition, he proposed turn- cations toted up a lifetime parts list of less ing idle distilleries into ethanol factories. than 30,000 part numbers. But this coup also fixated Henry on Best, the design unleashed creativity continuously improving the Model T years among owners converting Model Ts into after road conditions improved and its campers, portable sawmills, and towing design potential was exhausted. In the vehicles. (An uncle made one into a bush 1920s, just as his system to build Model Ts hog.) This was a big factor launching auto- reached its peak (and he was writing books motive aftermarket businesses — and a about it) competitors forced him to give up good many others. For example, the first on the Model T and go to the Model A. 15 Second Issue 2009 www.ame.org The Ford System straight industrial engineering. However, it wasn’t a snap. Not until 1913, five years Because few details of Ford’s methods later, did photographers have much to snap, were precisely codified, much can only be but by 1914, time to assemble a Model T surmised. But Ford’s global vision, then had dropped from 12.5 hours to 1.5 hours. called “Fordism,” was that mass production Charlie Sorenson, one of only a few would bring a higher standard of living to men personally involved, recalls the the entire world, thus assuring universal assembly line evolving by persistent trial health and world peace because of its supe- and error. The other experimenters includ- rior methods and technology, and paying ed “Pa” Klann, who came back full of ideas people above average. Without question after visiting a slaughterhouse “disassem- he always meant well. Fordism, as Henry bly line” in Chicago. But the final assembly summarized it in 1926 was: line was just one stage in creating a mon- 1. “Do the job in the most direct fashion strous integrated system to make nearly all without bothering with red tape or any the parts in a Model T. Ford and his men of the ordinary divisions of authority. wanted to understand and control every 2. Pay every man well — not less than six element of the process. dollars a day — and see that he is Once the first assembly line was employed all the time through 48 developed, others could be replicated hours a week and no longer. everywhere from England to Indonesia. 3. Put all machinery in the best possible Henry Ford’s grand system, including ore condition, keep it that way, and insist boats from Minnesota docking at the Rouge upon absolute cleanliness everywhere and rubber plantations in South America, in order that a man may learn to didn’t all come together until the 1920s. In respect his tools, his surroundings, the first ten years of Model T production, and himself.”1 slightly more than two million were built. In That’s Henry explaining how Ford was the last ten years, another 13 million were turning around a decrepit railroad line, not built. At the apex of this run-up, circa 1927, an auto factory. He deemed his principles — Ford claimed that ore docking in Dearborn distilled from his experience developing left as a finished Model T engine only 41 technology as well as production systems hours later. Ninety percent of all vehicles in — applicable to hospitals, farms, or any the world were Fords.2 organized work. And yes, from 1914 until 1926, Model “Do the job in the most direct fashion” Ts came only in black because only black encapsulated Ford’s distaste for any waste paint dried fast enough to fit the system. as he saw it — government regulations, But competitors soon learned to design financial covenants, accounting systems, assembly lines too, and in 1923, one of and management meetings. He wanted his Charlie Kettering’s first projects at General managers to work hands-on, unfettered by Motors was fast-drying paint in multiple any kind of bureaucratic folderol. Ford’s colors. Henry’s obsession with churning out obsession for using every scrap of material Model Ts started to let Ford be “out-fea- productively became legendary, and he tured” by GM and other competitors. wanted workers always to be busy. Although Henry’s role developing the Henry Ford’s Leadership assembly line itself was limited, that didn’t limit his acceptance of credit for it. He was Although a born mechanic, Henry Ford busy elsewhere developing farm tractors did little hands-on work when developing a and opening markets in foreign lands.
Details
-
File Typepdf
-
Upload Time-
-
Content LanguagesEnglish
-
Upload UserAnonymous/Not logged-in
-
File Pages6 Page
-
File Size-