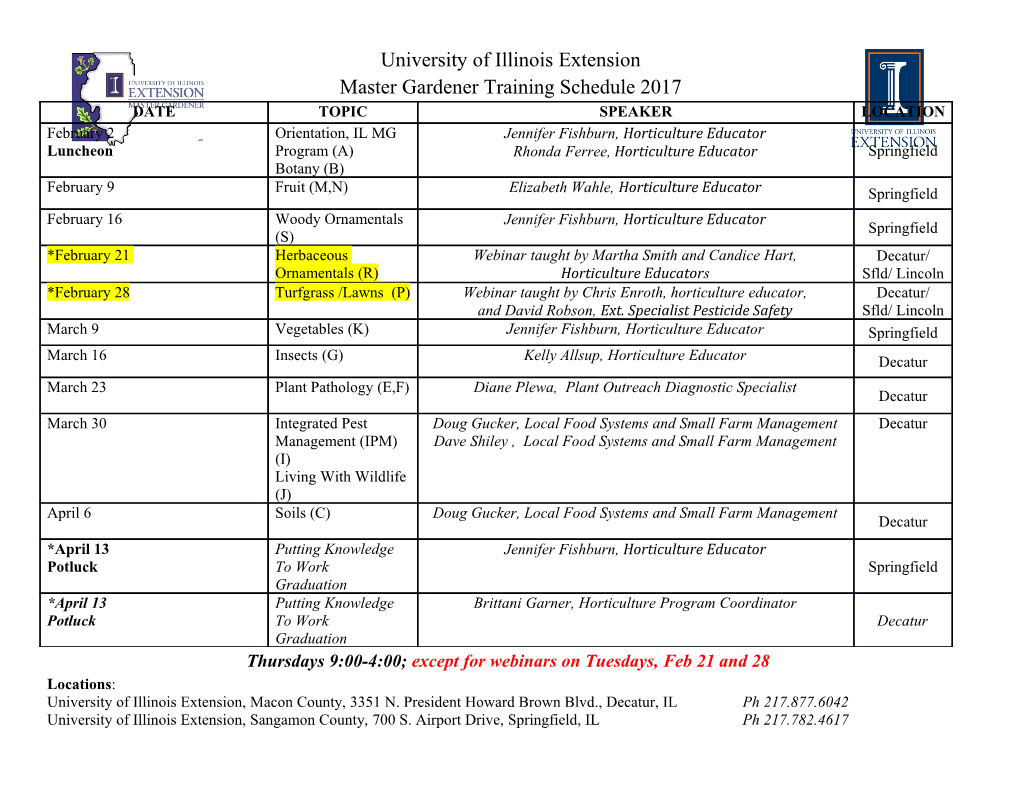
coatings Article Performance Enhancement in Borocarburized Low-Carbon Steel by Double Glow Plasma Surface Alloying Zheng Ding, Qiang Miao *, Wenping Liang, Zhengang Yang and Shiwei Zuo College of Materials Science and Technology, Nanjing University of Aeronautics and Astronautics, Nanjing 210000, China; [email protected] (Z.D.); [email protected] (W.L.); [email protected] (Z.Y.); [email protected] (S.Z.) * Correspondence: [email protected] Received: 12 October 2020; Accepted: 2 December 2020; Published: 10 December 2020 Abstract: In this paper, the performance of low-carbon steel is enhanced after introducing a·borocarburized diffusion layer via double glow plasma surface alloying technology. Due to the boron-carbon gradient structure of low-carbon steel, the protective coating exhibits an excellent wear and corrosion resistance. Interestingly, the borocarburized layer consists of a 64 µm carburized layer and a 27 µm boride layer, which plays an effective role in enhancing the microhardness of borocarburized low-carbon steel, exhibiting a 1440 Vickers hardness increase in the surface microhardness of low-carbon steel. The potentiodynamic polarization measurement and impedance measurement results indicate that the boride protective film can effectively prevent aggressive chloride ions from invading the substrate, which indicates an excellent property of corrosion resistance. This systematic study paves a promising way for the future application of hard coatings in severe environments. Keywords: borocarburizing; double glow; gradient structure; Fe2B; corrosion resistance 1. Introduction Due to the desirable weldability, plasticity and toughness, low-carbon steel has gained worldwide attention for its versatile applications in construction and mechanical parts. The surface hardened low-carbon steel can be widely used, for example, in wear-resistant parts of vehicles and ships [1–4]. The fast development of relative industries has boosted the demand of low-carbon steel, but features more and more rigorous market criteria on friction damage since the caused indirect damage could be much more expensive than the value of the material itself. Moreover, the inferior wear resistance, low hardness and poor corrosion resistance of low-carbon steel largely limits its application in these areas. In recent years, most surface modify techniques such as nitriding [5], carburization and nitrocarburizing [6–8] are based on studying the tribological behavior of low-carbon steel. Among all the available techniques, boriding has been proven to be an effective surface modification method that can diffuse boron atoms into substrate to form a boride layer of FeB phase and Fe2B phase [9], thereby enhancing wear resistance and hardness. However, due to the brittleness of the single boride layer, especially FeB phase, inevitable inner stress during the cooling process generates, leading severe crack propagation in the boride layer [10,11]. Based on these issues, a series of research studies have been carried out. S.A. Kusmanov et al. [12] pointed out that the brittle failure phenomenon is more likely to occur with a boride layer with FeB phase and Fe2B phase than with a boride layer with single Fe2B phase. The thermal expansion coefficient difference of FeB and Fe2B will induce a non-uniform distribution of thermal stress, thereby leading to a spalling of the boride layer during cooling process. Coatings 2020, 10, 1205; doi:10.3390/coatings10121205 www.mdpi.com/journal/coatings Coatings 2020, 10, 1205 2 of 13 In this case, the large stress difference between the boride layer and substrate will also result in a peeling phenomenon on the boride layer during its working time [13,14]. Hence, an effective method to acquire a work piece with desirable hardness and wear resistance is quite urgent both for researchers and markets. Up untilCoatings now, 2020 lots, 10, x ofFOR techniques PEER REVIEW and methods have been carried out to obtain a hardness2 of 13 layer on multiple metals,during cooling such as process. nitriding, In this electroplating, case, the large stre ionss difference implantation, betweenspark the boride plasma layer and sintering, substrate chromium plating andwill laser also result modification in a peeling withphenomenon Mo or on Ni the [boride15–22 layer]. The during technique its working of time double [13,14]. glowHence, has been successfullyan employedeffective method to fabricate to acquire various a work kindspiece with of coatings. desirable hardness This technique and wear employsresistance ais plasmaquite region, which is producedurgent both by for double researchers glow and discharges, markets. to fabricate a coating on substrate surface. The target Up until+ now, lots of techniques and methods have been carried out to obtain a hardness layer bombardedon by multiple Ar and metals, the elementssuch as nitriding, from the electroplating, target can beion depositedimplantation, on spark the substrateplasma sintering, [23–25 ]. Due to the metallurgicalchromium bonding plating and eff laserects, modification the double with glow Mo techniqueor Ni [15–22]. can The providetechnique aofgradient double glow structure has with desirable bondingbeen successfully strength employed between to fabricate the substrate various ki andnds coating.of coatings. Additionally, This technique employs the preparation a plasma of large area coatingsregion, can which also beis produced realized by by double the double glow discharges glow technique, to fabricate [26 a coating–28]. In on thissubstrate paper, surface. Q235 The low-carbon target bombarded by Ar+ and the elements from the target can be deposited on the substrate [23–25]. steel was borocarburizedDue to the metallurgical by the bonding double effects, glow the technique. double glow The technique morphological, can provide structural,a gradient structure wear resistance and corrosionwith resistance desirable bonding of samples strength under between diff theerent substr speedate and conditions coating. Additionally, with and without the preparation a borocarburized of layer werelarge systematically area coatings studied.can also be The realized friction by the performance double glow technique of the coating [26–28]. In under this paper, different Q235 loads has been shownlow-carbon in our previous steel was borocarburized study [29]. by the double glow technique. The morphological, structural, wear resistance and corrosion resistance of samples under different speed conditions with and without a borocarburized layer were systematically studied. The friction performance of the coating 2. Materials and Methods under different loads has been shown in our previous study [29]. As observed in Figure1, the workpiece and target are both cathodes, the device chamber is 2. Materials and Methods an anode. Argon is continuously introduced during the double glow process, which can be excited to As observed in Figure 1, the workpiece and target are both cathodes, the device chamber is an active plasma ions (Ar+). Due to the hollow cathode effect, the sharply increased plasma in the furnace anode. Argon is continuously introduced during the double glow process, which can be excited to cavity canactive bring plasma an increased ions (Ar+). temperatureDue to the hollow to cathode target effect, and workpiece.the sharply increased The sputtered plasma in the atoms furnace and ions of the target willcavity increase can bring subsequently. an increased temperature The strike to target of these and workpiece. particles willThe sputtered also increase atoms and the ions temperature of of the substrate.the target By adjusting will increase the subsequently. work voltage The strike and of current, these particles the working will also increase temperature the temperature is maintained in of the substrate. By adjusting the work voltage and current, the working temperature is maintained the ideal range. in the ideal range. Figure 1.FigureSchematic 1. Schematic of the of the double double glow glow plasmaplasma surface surface metallurgy metallurgy technique. technique. Q235 low-carbon steel with a size of 10 mm × 10 mm × 8 mm was selected as substrate. The Q235 low-carbon steel with a size of 10 mm 10 mm 8 mm was selected as substrate. The chemical chemical composition (wt.%) of Q235 steel ×was Mn 0.35%,× Si 0.3%, C 0.18%, S 0.04%, P 0.04%, Fe compositionbalance. (wt.%) Firstly, of Q235 abrasive steel paper was of Mn1200 0.35%,meshes was Si 0.3%, used to C polish 0.18%, theS samples; 0.04%, after P 0.04%, that, the Fe polished balance. Firstly, abrasive papersubstrates of 1200 were meshes ultrasonically was usedcleaned to polishin acetone the to samples; remove surface after that,contamination. the polished The average substrates were ultrasonicallyroughness cleaned of the in substrate acetone was to 0.26 remove μm. The surface whole fabrication contamination. process contained The average two steps. roughness Firstly, of the pure carbon target was used for depositing the carbon layer that was deposited on the substrate; after substrate was 0.26 µm. The whole fabrication process contained two steps. Firstly, pure carbon target that, B4C target was used for depositing the boron layer. After a series of orthogonal experiments, the was used foroptimum depositing technological the carbon parameters layer of that the waslayer deposited preparation on were the obtained. substrate; The aftervoltage that, of source B4C target was used for depositingelectrode, thevoltage boron of the layer. cathode, After working a
Details
-
File Typepdf
-
Upload Time-
-
Content LanguagesEnglish
-
Upload UserAnonymous/Not logged-in
-
File Pages13 Page
-
File Size-