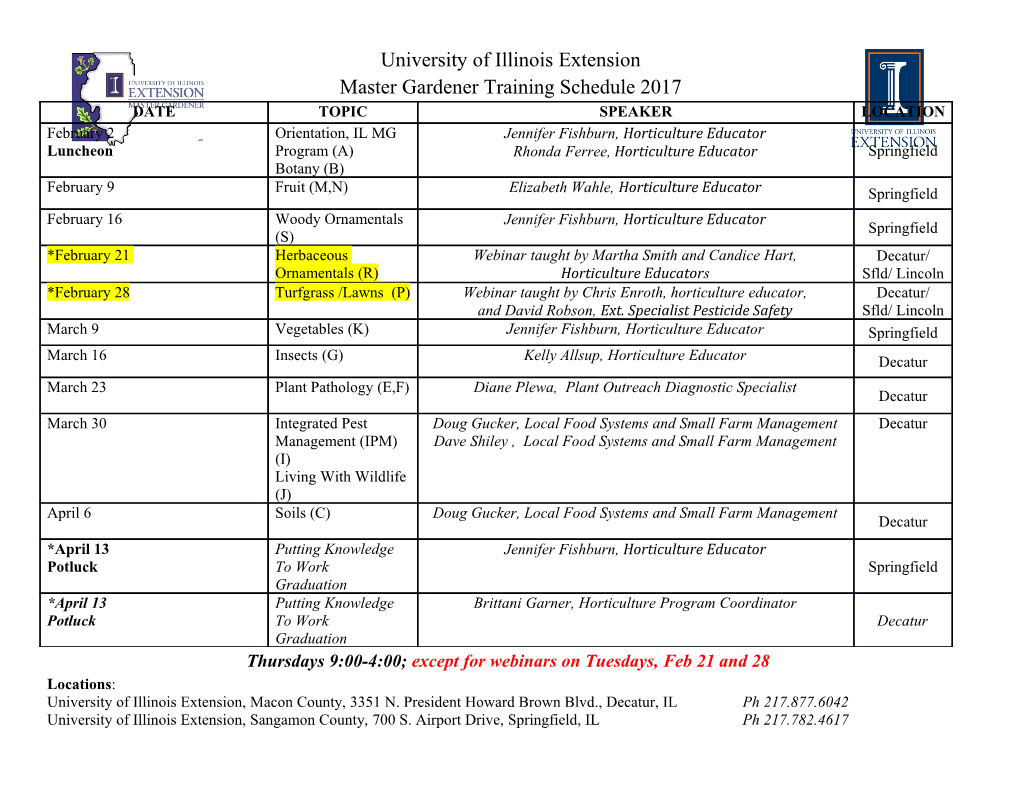
MULTI-SCALE MECHANISM BASED LIFE PREDICTION OF POLYMER MATRIX COMPOSITES FOR HIGH TEMPERATURE AIRFRAME APPLICATIONS by PRIYANK UPADHYAYA SAMIT ROY, COMMITTEE CHAIR ANWARUL HAQUE JAMES P. HUBNER MARK E. BARKEY NITIN CHOPRA A DISSERTATION Submitted in partial fulfillment of the requirements for the degree of Doctor of Philosophy in the Department of Aerospace Engineering and Mechanics in the Graduate School of The University of Alabama TUSCALOOSA, ALABAMA 2013 Copyright Priyank Upadhyaya 2013 ALL RIGHTS RESERVED ABSTRACT A multi-scale mechanism-based life prediction model is developed for high-temperature polymer matrix composites (HTPMC) for high temperature airframe applications. In the first part of this dissertation the effect of Cloisite 20A (C20A) nano-clay compounding on the thermo-oxidative weight loss and the residual stresses due to thermal oxidation for a thermoset polymer bismaleimide (BMI) are investigated. A three-dimensional (3-D) micro- mechanics based finite element analysis (FEA) was conducted to investigate the residual stresses due to thermal oxidation using an in-house FEA code (NOVA-3D). In the second part of this dissertation, a novel numerical-experimental methodology is outlined to determine cohesive stress and damage evolution parameters for pristine as well as isothermally aged (in air) polymer matrix composites. A rate-dependent viscoelastic cohesive layer model was implemented in an in-house FEA code to simulate the delamina- tion initiation and propagation in unidirectional polymer composites before and after aging. Double cantilever beam (DCB) experiments were conducted (at UT-Dallas) on both pristine and isothermally aged IM-7/BMI composite specimens to determine the model parameters. The J-Integral based approach was adapted to extract cohesive stresses near the crack tip. Once the damage parameters had been characterized, the test-bed FEA code employed a micromechanics based viscoelastic cohesive layer model to numerically simulate the DCB ex- periment. FEA simulation accurately captures the macro-scale behavior (load-displacement history) simultaneously with the micro-scale behavior (crack-growth history). ii DEDICATION This dissertation is dedicated to my sister Mrs. Ruchi Upadhyay. iii LIST OF ABBREVIATIONS AND SYMBOLS HTPMC High Temperature Polymer Matrix Composite BMI Bismaleimide C20A Cloisite 20A DCB Double Cantilever Beam FEA Finite Element Analysis RVE Representative Volume Element 2-D Two Dimensional 3-D Three Dimensional C Oxygen Concentration Di j Orthotropic Diffusivity R(C) Reaction Rate W Weight of Specimen DNC Diffusivity of C20A modified BMI DBR Diffusivity of BMI a Scalar Damage Parameter d Crack Opening Displacement q Rotation at the Load Pin P Reaction Force at the Load Pin Tg Glass Transition Temperature iv Ti Traction feg Strain Vector fHg Hereditary Strain Vector fsg Stress Vector [M(t)] Viscoelastic Stiffness Matrix lcr Critical Principal Stretch l¯ Principal Stretch Measure sr Radial Stress sq Hoop Stress scohesive Cohesive Stress s¯ ud Undamaged Stress f Oxidation State Variable fox Threshold Value of Oxidation State Variable e Weight Fraction due to Oxidation in Air g Weight Fraction due to Oxidation in Inert Conditions z Nano-clay Loading y Aspect ratio of Nano-clay Platelets v ACKNOWLEDGEMENTS Foremost, my heartfelt gratitude goes to my advisor Dr. Samit Roy for his valuable guidance and continuous support at every step of this work, right from conception of the idea to its conclusion. I am grateful to Dr. Roy for providing me with this opportunity to study at The University of Alabama and for his constant support that was invaluable in the completion of this work. His sense of confidence and level of trust in me has led me to the successful completion of my dissertation work. Besides my advisor, I would like to thank Dr. Mark E. Barkey, Dr. Anwarul Haque, Dr. James P. Hubner, and Dr. Nitin Chopra, for their encouragement, guidance and patience while serving as members of my doctoral committee. I greatly appreciate the contribution by Dr. Hongbing Lu and Dr. Mohammad H. Haque at UT-Dallas towards this study. I am especially thankful to Dr. Mohammad H. Haque for conducting experiments, needed to validate my dissertation work. I am also grateful to all the faculty members of the Department of Aerospace Engi- neering and Mechanics at The University of Alabama, who helped me a lot during my course work and imbibed a learning spirit in me. The blessings of my parents and the love and affection of my sister (Ruchi) and brother (Vijay) has given me the necessary driving force to complete this work. In the end, a special thanks to all who could not be mentioned here, but have always had a positive influence in my life. The research project was funded by the “Low Density Materials Program” of the AFOSR. vi CONTENTS ABSTRACT . ii DEDICATION . iii LIST OF ABBREVIATIONS AND SYMBOLS . iv ACKNOWLEDGEMENTS . vi LIST OF TABLES . .x LIST OF FIGURES . xi 1 INTRODUCTION . .1 1.1 Objective . .4 2 LITERATURE SURVEY . .6 2.1 Thermo-oxidative Behavior of Polymer Resin Systems . .6 2.2 Barrier Properties of Nanoparticles . 10 2.3 Damage Modeling for Composites . 15 2.4 Cohesive Layer Models . 22 3 MATHEMATICAL MODELING OF THERMAL OXIDATION . 25 3.1 Three Zone Oxidation Model . 26 3.2 Determination of Thermo-Oxidative Parameters . 27 3.2.1 Calculation of b .............................. 28 3.2.2 Calculation of aR0 ............................ 28 3.2.3 Calculation of fox ............................. 29 vii 4 INFLUENCE OF NANO-CLAY ON THERMO-OXIDATIVE STABILITY AND MECHANICAL PROPERTIES OF BMI . 31 4.1 Materials and Manufacturing Process . 31 4.2 Thermo-Oxidative Aging Experiments . 32 4.2.1 Isothermal aging of BMI and C20A/BMI in air . 32 4.2.2 Isothermal aging of BMI and C20A/BMI in Argon . 35 4.2.3 Isothermal aging of BMI and C20A/BMI in 60% O2 .......... 36 4.3 Calculation of Thermo-oxidative Parameters from Experimental Data . 41 4.4 Nano-indentation Test for Mechanical Properties . 42 4.5 Thermal Shrinkage Test . 44 5 FINITE ELEMENT SIMULATION OF RESIDUAL STRESSES DUE TO SHRINK- AGE IN IM-7/BMI COMPOSITE . 45 5.1 Finite Element Model . 45 5.2 Simulation Results . 49 6 MULTI-SCALE VISCOELASTIC COHESIVE LAYER MODEL FOR PREDICT- ING DELAMINATION IN HTPMC . 55 6.1 Viscoelastic Cohesive Layer Model . 55 6.2 Damage Evolution Law . 58 6.3 Model Calibration . 60 6.3.1 Flexure Experiment . 60 6.3.2 FEA simulation of flexure experiment . 60 6.4 Double Cantilever Beam Experiment . 67 6.4.1 Specimen preparation and DCB specimen geometry . 67 6.4.2 Experimental method . 68 viii 6.5 Determination of Cohesive Stress using J-integral . 69 6.6 Estimation of Damage Evolution Law . 74 6.6.1 Determination of critical principal stretch lcr ............. 75 6.6.2 Determination of damage parameters a0 and m ............ 77 6.7 Numerical Simulation of DCB Experiments . 81 6.8 Sensitivity study on model parameters . 87 7 CONCLUSIONS . 90 7.1 Conclusions . 90 7.2 Future Work . 92 REFERENCES . 95 ix LIST OF TABLES 4.1 Oxidation parameters for neat BMI and C20A modified BMI . 42 4.2 Comparison of mechanical properties for neat and C20A modified BMI(3 wt%) 43 5.1 Material properties used in FEA simulation . 49 6.1 Elastic properties used in FEA modeling for un-aged and aged (for 3000 hours at 250 °C) IM-7/BMI unidirectional laminate . 62 6.2 Creep Compliance of BMI resin (Reference Temperature = 204 °C) . 64 6.3 Micromechanical damage parameters used in FEA modeling for un-aged and aged (for 3000 hours at 250 °C) IM-7/BMI unidirectional laminate . 65 6.4 Damage evolution law parameters used in FEA model for IM-7/BMI . 80 6.5 Elastic properties of transversely isotropic IM-7/BMI lamina[Andrews and Garnich, 2008]................................... 81 x LIST OF FIGURES 2.1 (a) Cross section of a G30-500/PMR-15 unidirectional composite after 2092 hours of isothermal aging in air at 288 °C (b) Close-up view of oxidized com- posite showing fiber matrix debond [Ripberger, Tandon, and Schoeppner, 2005]9 3.1 Schematic diagram showing three zones during thermal oxidation . 25 3.2 Oxidized and un-oxidized regions depicted in section view . 29 4.1 Neat and C20A modified BMI specimens . 32 4.2 Specimens inside the oven during isothermal aging experiment . 33 4.3 Weight loss data for BMI and 3% C20A compounded BMI at 250 °C in air . 33 4.4 Experimental set up for weight loss experiment in Argon and 60% O2 envi- ronment . 36 4.5 Weight loss data for BMI and 3% C20A compounded BMI at 250 °C in Argon 37 4.6 Weight loss data for BMI and 3% C20A compounded BMI at 250 °C in 60% O2 37 4.7 Comparison of weight loss data for BMI and 3% C20A compounded BMI at 250 °C in (a) air (b) argon (c) 60% O2 environment . 40 4.8 Measured shrinkage strains for neat BMI and C20A modified BMI . 43 5.1 (a) Hexagonal arrangement of fibers and (b) In-plane displacement boundary conditions on the RVE with fiber-fiber interaction . 46 5.2 3-D finite element mesh of RVE showing boundary conditions . 47 5.3 3-D contour showing oxidation state variable f (neat BMI case) . 50 5.4 3-D contour showing radial strain er (neat BMI case) . 51 5.5 3-D contour showing radial stress sr (neat BMI case) . 51 5.6 3-D contour showing hoop stress sq (neat BMI case) . 52 xi 5.7 FEA prediction of oxidation state variable f at the interface along z direction along fiber-matrix interface at different aging times . 53 5.8 FEA prediction of sr at the interface along z direction along fiber-matrix interface at different aging times .
Details
-
File Typepdf
-
Upload Time-
-
Content LanguagesEnglish
-
Upload UserAnonymous/Not logged-in
-
File Pages115 Page
-
File Size-