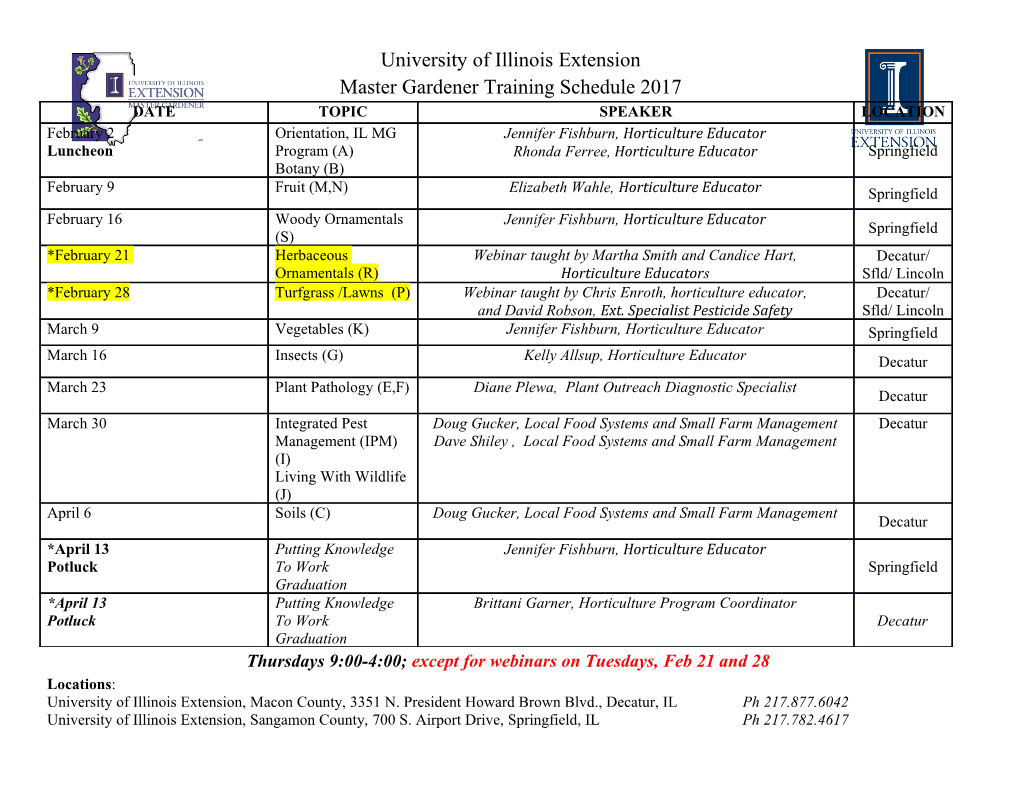
29 CHAPTER III TECHNIQUES OF QUARRYING AND DRESSING HUMMELSTOWN BROWNSTONE All brownstone contains a variable amount of water when freshly quarried which enables it to be cut readily, but at the same time it will crack and freeze more easily in cold weather. As a result the actual quarrying had to be done in the months when there was no frost in the ground. The coldest months of the year were used for stripping and cleaning the bottom of the quarry as the weather permitted. In November of 1884 and January of 1885 The Sun reported on three different occasions: Work at the sawmill owing to the cold weather greatly impeded operations. The cold snap Monday evening did considerable damage to the quarried stone at the quarries. Work has not yet resumed with the Brownstone mill and it is probable it will not until the weather becomes warmer. 1 One of the first problems facing Allen Walton as the new superintendent of a novice company was to combat the affects of cold weather and freezing conditions. He immediately informed the directors: The sawmill should be heated and floored overhead to keep it from freezing, that is if I am to man the mill all winter. I think I can keep the mill in saw blocks. 2 The concern regarding freezing was not necessarily directed to the work force. This freezing affected the stone that was in the stone yard to be seasoned. The purpose of the 1 The Hummelstown Sun , Nov. 21 & 28, 1884, and Jan. 30, 1885, Hummelstown Area and Derry Township Historical Societies, Hummelstown Brownstone Manuscript Group. 2 “Letter of Allen Walton to Louis Brown”, Dec. 6, 1868, Hummelstown Brownstone Manuscript Group, Dauphin County Historical Society. 30 seasoning was to decrease the amount of water in the stone so that it was less susceptible to cracking and breaking during the winter months. Certainly it would be impractical and economically unfeasible to provide storage buildings large enough to cover and heat all the stone in the stone yard. The Hummelstown quarrymen had an ingenious method of ensuring that the quarried stone did not freeze as related in this account from The Sun . At present the majority of the men employed at the Brown Stone Quarries are engaged in packing large saw blocks of stone in a pit especially made to protect the stone from the extreme cold weather. These are then carefully covered with a heavy coat of manure, a precaution necessary to prevent the rocks from freezing and bursting. This care must be taken in the winter with the stone not thoroughly seasoned or run the risk of becoming shattered by the frost which means heavy pecuniary loss. 3 When the season for quarrying began, the pits would suddenly spring to life and the pace would continue rapidly until the first deep frost at which time the quarrying ceased. The scrap and waste would be cleared off the surface exposing the strata of rock. Unlike marble, granite, limestone and a few sandstone quarries, the Hummelstown pits did not use channeling or gadding machines to remove the rock. This was most likely due to the considerable rake or angle of the rock strata. Rather, if a fissure or fault of a regular nature was evident it was desirable, for the workmen would then not have to blast the C-1: Eclipse Rock Drill 3 The Hummelstown Sun , loc. cit., January 9, 1903. 31 stone. Steel wedges were driven into the fault and hammered with a sledge until the stone separated. When this system was not feasible, particularly with the harder stone, a row of channels was drilled with Ingersol Rock Drills (in appearance much like the Eclipse Rock Drill) and charged with black powder, but this was done as a last resort. Dynamite was not used, for too heavy a charge could fracture and damage the stone. Engle and Bossler of Middletown, was the chief source of blasting material for the C-2: Men Drilling company in 1875. Although records for the Hummelstown Brownstone Company and the Pennsylvania Brown Free Stone Company are woefully lacking, the following itemized list for the month of February in 1875 gives one a general idea of the cost for blasting equipment during a productive month and a half for that year. Jan. 26 To Balance on caps $ .50 Feb. 9 “ 50 lbs. of dynamite 23.35 “ 23 “ “ “ “ “ “ 23.35 “ “ “ 6 kegs of powder 18.00 “ “ “ 1000 ft. of fuse 4.50 “ “ “ 25 lbs. nail rods 2.25 March 16 “ 6 kegs of powder 18.00 $93.95 4 When viewing the quarries from a distance, of all the equipment used, the derricks were the most impressive. Indeed, hoisting large stones that could weigh as much as ten tons or more demanded gigantic rigs for the job. In quarry #4 which was the 4 “Account of Pennsylvania Brown Free Stone Company with Engle & Bossler, March 1, 1875, Hummelstown Brownstone Manuscript Group, Dauphin County Historical Society. 32 deepest and terraced, these steam driven arms ascended from one tier to the next in awesome magnificence. In the first decade of the 20th Century as many as twenty-two derricks each with a separate steam hoist labored throughout the day heaving immense blocks to flat cars waiting above. (Prior to building the Brownstone - Middletown C-3: Postcard Showing Derricks at Corner of Quarry #4 Railroad the stones were placed on teamsters’ wagons.) The timbers for the largest derricks could not be provided from local timber, so they were shipped from the West and the South. The upright beam was held erect with guys while the oblique arm or boom hoisted and swung the stone into position. Manila rope was first used for the guys, but this was later replaced with the more substantial steel rope. Fitler, Weaver & Co., Rope Makers and Chandlers (later know as Fitler and Co.) in Philadelphia was the major supplier of manila rope while the G. DeWitt Brothers & Co. of the same city was the chief source of wire rope. 33 Shortly after his appointment as superintendent of the quarries, Allen Walton improved the ability to hoist stone in the quarry, and it became a never-ending search to improve this capacity. In December of 1867 he was pleased to report: I have the derrick and horse power all up, and in use. I think it will pay for itself in 2 months. I can raise a stone weighing about 3 tons with the horsepower. I think you will be pleased with all I have done when you come up. 5 And in May of 1870 his monthly report to the directors proudly stated: We are now sawing the largest stone ever quarried here, it is 10 ft. x 5 ft. x 20 in. wide. We have one at the quarry not yet brought in 12 ft. x 4.6 ft. x 1.8 ft.; some of the people that think we cannot quarry larger stone should now pay us a visit. I think we could change their minds. 6 Indeed, as time progressed they were able to raise considerably larger and heavier blocks from the pits. After a slab was removed from the quarry, it was hoisted to a scabbling bank at which time the workmen drilled a series of one inch holes along a line and into these holes they placed small, half-round iron bars called feathers with a small steel wedge inserted between the feather and the rock. They would then strike the feathers with sledges until the strain split the stone apart producing a rough shaped slab. They then proceeded to hammer or scabble the rough edges off the stone and shape it into a rough rectangular solid in preparation for sawing. The hammer used for this operation was a heavy, square-faced hammer called a face hammer, although the men at Hummelstown commonly referred to it as a scabbling hammer. To speed the process on rougher 5 “Letter of Allen Walton to Louis Brown”, Dec. 7, 1867, Hummelstown Brownstone Manuscript Group, Dauphin County Historical Society. 6 “Report of Allen Walton to the Directors of the Pennsylvania Brown Free Stone Company”, July 30, 1870, Hummelstown Brownstone Manuscript Group, Dauphin County Historical Society. 34 surfaces they also used a scabbling pick which was similar to an ordinary pick only shorter of handle and stout of casting. The scabbled blocks or saw blocks as they were then called were taken to the sawmill and placed in the stoneyard for seasoning. Work in the pits was dangerous and accidents were frequent. Bruised and smashed fingers, hands, toes and feet were some of the more common injuries with which Dr. Baker, the company doctor, had to contend. Fatalities sometimes occurred, but the most devastating accident of this nature occurred at the end of November in 1887. At that time the north band of quarry #1 gave way and hundreds of tons of earth and rock entombed four men. John Boyer of Londonderry Township was freed and escaped with a broken leg, but John Bricker also of Londonderry Township, John Montpiere of France, father of seven children, and Hungarian #64 were killed. The body of John Bricker was not recovered until January of the following year and the description of the body in The Sun spared no detail: After an incessant search, ever since the terrible accident, the body of Mr. John Bricker has at last been found. The unfortunate victim was caught between great boulders, and literally cut in two. His head was crushed into a mass, and his hands were torn off.
Details
-
File Typepdf
-
Upload Time-
-
Content LanguagesEnglish
-
Upload UserAnonymous/Not logged-in
-
File Pages18 Page
-
File Size-