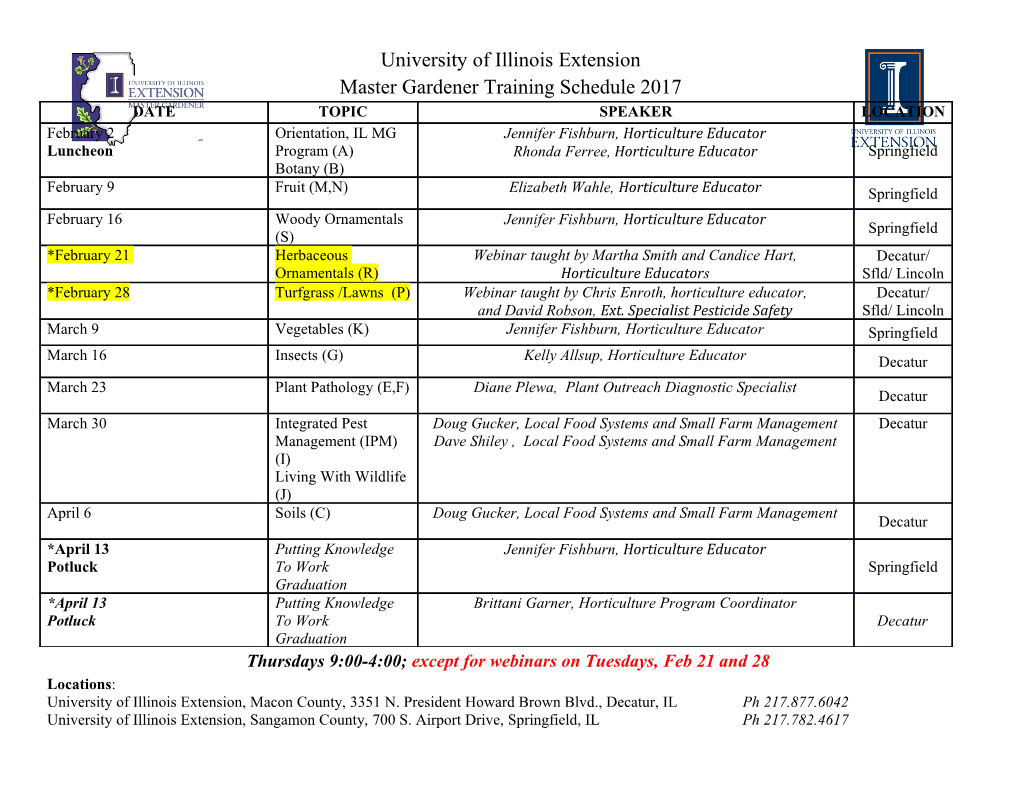
Iowa State University Capstones, Theses and Graduate Theses and Dissertations Dissertations 2015 Physical properties of various conductive diborides and their binaries Austin Harold Shaw Iowa State University Follow this and additional works at: https://lib.dr.iastate.edu/etd Part of the Materials Science and Engineering Commons, and the Mechanics of Materials Commons Recommended Citation Shaw, Austin Harold, "Physical properties of various conductive diborides and their binaries" (2015). Graduate Theses and Dissertations. 14496. https://lib.dr.iastate.edu/etd/14496 This Dissertation is brought to you for free and open access by the Iowa State University Capstones, Theses and Dissertations at Iowa State University Digital Repository. It has been accepted for inclusion in Graduate Theses and Dissertations by an authorized administrator of Iowa State University Digital Repository. For more information, please contact [email protected]. Physical properties of various conductive metal diborides and their binaries by Austin Harold Shaw A dissertation submitted to the graduate faculty in partial fulfillment of the requirements for the degree of DOCTOR OF PHILOSOPHY Major: Materials Science and Engineering Program of Study Committee: Alan Russell, Major Professor Iver Anderson Ashraf Bastawros Scott Beckman Terrence Meyer Iowa State University Ames, Iowa 2015 Copyright © Austin Harold Shaw, 2015. All rights reserved. ii TABLE OF CONTENTS ABSTRACT iii CHAPTER 1: INTRODUCTION 1 CHAPTER 2: EXPERIMENTAL PROCEDURE 17 CHAPTER 3: RESULTS AND DISCUSSION 22 CHAPTER 4: CONCLUSION 57 CHAPTER 5: FUTURE WORK 60 APPENDIX 1: XRD ANALYSES 61 APPENDIX 2: TERNARY PHASE DIAGRAMS 75 APPENDIX 3: LOOP ABRASION DATA 81 APPENDIX 4: COUNTER-FACE PROFILOMETRY DATA 109 REFERENCES 117 iii ABSTRACT Hard, wear-resistant materials have potential utility as both coatings and bulk components in wear-prone applications. First-principle calculations performed by other investigators indicated that TaB2 and WB2 could be in the class of ultra-hard materials (hardness > 45 GPa), while MoB2 could be slightly less hard, but still in the “super-hard” range (hardness >30 GPa). However, relatively little empirical work has been done to confirm or refute such ultra-hard/super-hard expectations for the materials, and they have seen essentially no engineering use. In this study, research was performed to determine whether: MoB2, NbB2, TaB2, and WB2 have high hardness. These borides have potential to be used as wear- and corrosion-resistant materials. Their engineering properties could be improved by mixing two of the diborides together. The study determined that only the mixed-phase diborides with no WB2 content showed an increase in hardness vis-à-vis the four pure compounds. However, all of the mixed-phase samples except the WB2-NbB2 specimens showed improved wear-resistance. Ball-on-flat testing was conducted on the four pure diborides using a base 0W30 oil and also using 0W30 base oil containing 1% zinc dialkyldithiophosphate (ZDDP) additive, a wear- reducing agent that is sometimes added to lubricating oils. In these tests MoB2 showed the lowest steady-state coefficient of friction and the least wear of the steel counter-face. The iv ZDDP additive was found to actually degrade performance of the MoB2 sample, while having no effect on the other diborides. Corrosion testing showed that none of the 28 samples reacted with deionized water or a 20% sodium hydroxide solution. All the samples showed reaction in the 5% sodium chloride aqueous solution, forming an adherent surface film that was not removed during a subsequent cleaning process. All three samples with 80% MoB2 content were severely attacked by a 50% nitric acid solution, and the pure MoB2 sample dissolved completely in nitric acid. Ultimately, it was concluded that the sample with the best properties for engineering use was the Nb0.8Ta0.2B2 mixed phase diboride. 1 CHAPTER 1: INTRODUCTION Many engineering components rely not only on their bulk properties, but also on their surface characteristics. This is especially true in wear-resistant components, which often must function in a wide variety of environments. The behavior of a material interacting with other objects is dependent on three major aspects: the surface properties, the surface contact area, and the environment in which the material must operate. Surface properties like coefficient of friction and surface roughness play a crucial role in the wear of a material. High surface roughness, if your material is soft, will cause a decrease in contact area, which will lead to higher stresses, more wear, and will lead to three-body wear. If your material is hard, it can act as an abrasive and wear into the opposing surface. The coefficient of friction, µ, of your material will also affect the performance. If the coefficient is high, it will lower the efficiency of the system and will cause the surfaces to heat up. A low coefficient of friction means less energy lost due to friction and less strain on the material. The surface contact area between two new surfaces is usually very low, due so surface roughness, and surface defects, like asperities. Due to the low contact area, the stress is concentrated on these points, which causes them to wear down faster or break off. As this occurs, the surfaces of the materials come into greater contact with each other, increasing the contact area thus decreasing the contact stress. The environment is the most crucial aspect to take into account when choosing the appropriate material for a component. The environment determines the constraints the material will be under. The material could be used under a high load, strain, or temperature. It could be in a corrosive environment, where the material is under chemical attack. 2 Transition metal borides exhibit unique combinations of properties such as high melting points, high hardness, high thermal and chemical stability, and excellent corrosion and oxidation resistances, so they have been the focus of much research. They are seen by many to be promising materials for new heat-, corrosion-, and wear-resistant alloys and coatings because their properties compare favorably with many widely used non-boride materials [1] (Table 1.1), many of these physical properties and their relationships with wear will be discussed in further detail later. Even though extensive research has been done on transition-metal borides, a majority of the work has been focused on preparation of TiB- or TiB2-containing composites. With the exception of superconducting MgB2, other borides have received less research attention. This work focuses on other transition metal borides, specifically TaB2, MoB2, WB2, and NbB2, and their combinations. 3 Table 1.1. Mechanical and physical properties of several ceramics used as wear-resistant materials and the four materials studied in this project (shown in italics). Elastic Deformation Fracture Friction Coating Hardness, Modulus, relative Density Toughness Coefficient 3 Material H (GPa) E (GPa) to yielding (H/E) (g/cm ) K1C (MPa√m) μ 600-720 0.4-0.6 WC 15 [2] [3] 0.0227 15.63 2.0-3.8 [3] (WC on steel) [4] 0.06-0.09 470-510 (Steel pin-on-disk) AlMgB14 32-35 [5] [6] 0.0673 2.59 3.0-4.0 [7] [8] 0.15 (ball on flat) MoS2 8.1 [9] 200 [10] 0.0405 5.06 1.8 [9] [11] TiB2 25-35 [12] 565 [12] 0.0531 4.52 6.2 [12] 0.9 [12] 0.8-1.2 TiN 31 [13] 550 [13] 0.0564 5.22 5 [14] (TiN on Steel) [15] 215-413 Al2O3 15 [16] [3] 0.0478 3.90 3.3-4.8 [3] 0.4 [16] MoB 16.4* [17] 519* [17] 0.04104 8.65 Unavailable Unavailable WB 24.5* [18] 552* [18] 0.04438 15.3 Unavailable Unavailable MoB2 16.4* [17] 429* [17] 0.03823 7.12 Unavailable Unavailable 0.23 (Thin film) (Al2O3 ball on disk) WB2 43.2* [19] 360* [20] 0.1200 10.77 Unavailable [19] MoB2 33.1* [21] 569* [22] 0.0429 - Unavailable Unavailable NbB2 19.1 [23] 512 [24] 0.0373 6.97 Unavailable Unavailable TaB2 42-45 [23] 551 [25] 0.0789 11.15 3.5-4.5 [26] Unavailable *Calculated Hardness The hardness of a material is one of the most important mechanical properties in wear and has been widely employed as a criterion to predict abrasive wear resistance. For some annealed pure metals and steels, the abrasive wear resistance has been found to be linearly proportional to their hardness. In contrast, metals and alloys that have been work hardened have a considerable increase in hardness, but the wear resistance remained unchanged, and in 4 some cases, decreased. In the case of martensitic and pearlitic steels, the hardness was proportional to the wear resistance; however, this is not the case with ferritic steels (See Fig. 1.1). It has been suggested that the microstructure has a greater influence on abrasive wear resistance than bulk hardness. Figure 1.1. Wear resistance vs hardness, general trends [27]. In the cases of WC-Co, it was found that abrasion resistance tends to increase with increasing hardness [28]. According to most investigators, when the hardness of WC-Co alloys increases but is lower than the hardness of the abrasive material, the rate of increase in the abrasive resistance is low. However, when the hardness of the abrasive is lower than that of the alloy, the rate of increase in abrasive resistance with increasing hardness is high [29]. Figure 1.2 shows the wear curves of five different coatings and uncoated substrate of high-speed steel in an abrasive wear test with Al2O3 abrasives [30]. The numbers in brackets show the micro-hardness values. The figure clearly shows that the wear rate of Ti-B-C coating is about one tenth of the uncoated substrate, while the hardness of Ti-B-C is about ten times larger than that of the substrate.
Details
-
File Typepdf
-
Upload Time-
-
Content LanguagesEnglish
-
Upload UserAnonymous/Not logged-in
-
File Pages126 Page
-
File Size-