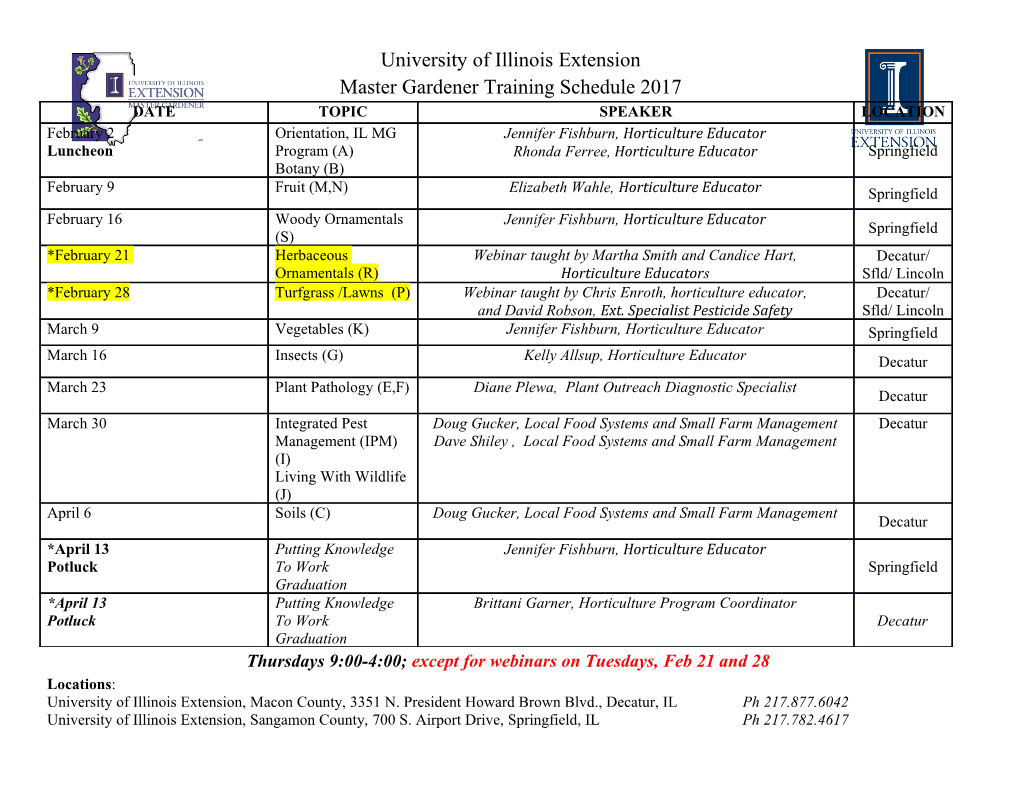
Transactions, SMiRT-25 Charlotte, NC, USA, August 4-9, 2019 Division III Analysis on the Thermal Striping and Thermal Shock of the Lower Head of Central Measuring Shroud in a Fast Reactor Zheng Shu 1, Lu Daogang 1, Cao Qiong 1 1School of Nuclear Science and Engineering, Beijing Key Laboratory of Passive Nuclear Safety Technology for Nuclear Energy, North China Electric Power University, Beijing 102206, China ([email protected]) ABSTRACT The central measuring shroud, as an important in-vessel component, contains the conduits of control rod and a variety of measuring equipment. The distance between the core outlet and the lower head of central measuring shroud (LHCMS), which is located above the core outlet, is only 500mm. Therefore, the LHCMS is affected by the core coolant for a long period, especially the temperature effects of the following two types. Firstly, under the operating condition of the sodium-cooled fast reactor, the uneven distribution of the core power causes the phenomenon of thermal striping, which may cause large stress. In addition, under the scram condition, the coolant temperature at the core outlet is sharply reduced due to the decrease of the core power, inducing the phenomenon of thermal shock that may induce large stress. Therefore, stress analysis of the LHCMS under the operating condition and scram condition is very necessary. In the paper, the simulation first established the finite element model of the LHCMS, and then calculated the thermal stress of the LHCMS according to the temperature fluctuation curve and the scram temperature curve. The results show that the temperature field under thermal shock changes dramatically with time, while the temperature field under thermal striping changes relatively slowly with time. In addition, the maximum von Mises stress caused by thermal shock is nearly three times greater than that of thermal striping, which should provide a preference for the design of the LHCMS. Keywords: lower head; thermal striping; thermal shock; von Mises stress INTRODUCTION The rapid fluctuation of the component temperature is called the thermal striping. The rapid increase or decrease of the component temperature in a short period of time is called the thermal shock. Both temperature variations can cause stress in the components. Under the operating conditions of the sodium cooled fast reactor, the uneven distribution of the core power will cause different temperature distribution of the coolant. When the hot and cold coolant is mixed outside the core outlet, a temperature fluctuation will occur in the LHCMS, causing thermal stress. In addition, under scram conditions, the core temperature drops rapidly due to the sudden drop in core power, and the temperature range is likely to reach 100℃ within 10 seconds, which will cause a strong thermal shock at the LHCMS. Because of the high thermal conductivity of the coolant (liquid sodium), the thermal striping and thermal shock of the sodium cooled 25th Conference on Structural Mechanics in Reactor Technology Charlotte, NC, USA, August 4-9, 2019 Division III fast reactor tend to be more severe than that of the reactor with water coolant, so it is more likely to cause larger stress to the LHCMS. There have been many detailed studies on various components in terms of the thermal striping. The study of Kamaya Masayuki (2014) has shown that at the elbow pipe branched from the main pipe, even if the external membrane constraint did not apply on the pipe, thermal stress will be caused by an inhomogeneous temperature distribution in a straight pipe. The phenomenon studied by Masayuki Kamaya is similar to that of our study. The central measuring shroud is simply constrained at the top of the shroud. There is no constraint around the lower head, but thermal stress occurs because of non-uniform temperature distribution in thickness direction. Besides, Lee Jeong lk et al (2009) has concluded that thermal stress caused by the thermal striping is related to the temperature difference between the hot and cold fluids and the enhanced heat transfer coefficient because of turbulent mixing is one of the factors bringing thermal stress to nuclear facilities as well. Apart from the research above on the causes of thermal stress induced by the thermal striping, there are some studies that show the factors affecting the magnitude of thermal stress. The study of Kamaya Masayuki and Nakamura Akira (2011) used finite element method to calculate the thermal stress at a mixing tee and it showed that the variation ranges of thermal stress and fatigue damage was large near the position 20°from the symmetry line in the circumferential direction. Stress intensity factor and strain energy density factor ranges were studied, by Jones I.S. (2005), as functions for thermal striping frequencies, and both were applied to the calculation of maximum allowable thermal striping amplitudes. Chellapandi P. et al (2009) studied thermal striping limits for SFR (sodium cooled fast spectrum reactors), by using an idealized geometry, he calculated temperature and thermal stresses and concluded that temperature fluctuation with 45K or 70K was acceptable because there was no accumulated creep- fatigue. Also, there have been many detailed studies on various components in terms of the thermal shock. Liu Maolong et al (2019) studied the thermal stress caused by uneven temperature fields through experiment and theoretical investigation. And an analytical model was developed to predict thermal stresses due to nucleate boiling. The results demonstrated that peak tensile stress was induced at the localized cold spot under a growing bubble. The magnitude of the peak stress is predominantly determined by liquid and solid properties. The computation of fluid dynamics and thermal stress analysis performed by Ma Ziqi et al (2017) indicated that in AP1000 reactors, thermal shock may induce local high stress state at the injection nozzle, while away from the nozzle the stress was comparatively safe and retained a low stress state. And Janssens K. G. F. et al (2009) used finite element method to study a combined kinematic-isotropic cyclic hardening material model, which demonstrated that cyclic thermal shock occurred at the tip of notch in the specimens, and the impact on the number of cycles to crack initiation is explored. Plus, Niu Li-Sha et al (2001) established a three-dimension finite element model to simulate thermal shock on the nuclear pressure vessel. The results indicated that thermal stress induced by thermal shock was much higher than the stress induced by pressure change. And the highest stress is located at the joint of the injection pipe and pressure vessel. As discussed above, there have been many studies on thermal striping and thermal shock in nuclear power plants. However, there is still a lack of thermal striping and thermal shock studies on the LHCMS of the sodium cooled fast reactor. Therefore, the research on it has guiding significance on some level for the design and construction of a new generation of nuclear power plants. In this paper, using the finite element method, the model of the LHCMS was first established, and then the temperature fluctuation curve of fluid 25th Conference on Structural Mechanics in Reactor Technology Charlotte, NC, USA, August 4-9, 2019 Division III sodium near the LHCMS under operating conditions and the temperature decrease curve of fluid sodium near the LHCMS under the scram conditions were used as input conditions. The thermal stress of the LHCMS in both cases were obtained. Finally, the effects of thermal striping and thermal shock on the LHCMS were given. FE MODEL Geometry and FE mesh The model of LHCMS is shown in Figure 1. Since it is a symmetric model, in order to properly simplify, the simulation uses the 1/6 model, as shown in Figure 2. The top view of the 1/6 model is shown in Figure 3. Several conduits of control rod are arranged on the LHCMS, the main function of which is to provide passages for the control rods. The main dimensions of the LHCMS and the conduits of control rod are shown in Table 1. Figure 1. Model of the LHCMS. Figure 2. The front view of 1/6 model. Figure 3. The top view of 1/6 model. Table 1: Dimensions of the LHCMS. Geometry Dimensions/(m) Inner Radius Outer Radius Height Sleeves 0.085 0.107 0.4 Lower Head 1.055 1.075 - 25th Conference on Structural Mechanics in Reactor Technology Charlotte, NC, USA, August 4-9, 2019 Division III In the paper, the calculation of thermal stress involves two aspects. Firstly, the thermal analysis is used to obtain the transient temperature field of the model, and then the boundary constraint and transient temperature field are applied to the model to obtain the thermal stress due to temperature change. That is, we use an indirect method to get thermal stress. Therefore, the calculation requires high precision mesh, otherwise it is prone to have errors in the process of temperature conversion. The hexahedral mesh is applied to ensure the accuracy of the calculation and reduce the amount of mesh. Besides, in order to get the most suitable mesh size, sensitivity analysis is performed on several different mesh sizes, which are 0.01m, 0.008m, 0.007m and 0.005m. The results of mesh sensitivity analysis are shown in Figure 4. Figure 4. The results of mesh sensitivity analysis. As shown in Figure 4, the von Mises stress tends to be stable when the mesh size is 0.005m. Therefore, 0.005m is selected as the mesh size. The mesh of the model adopted 0.005m mesh size is illustrated in Figure 5. Figure 5. The mesh of the model. BOUNDARY CONDITIONS As can be seen from Figure 6, the model is divided into three parts.
Details
-
File Typepdf
-
Upload Time-
-
Content LanguagesEnglish
-
Upload UserAnonymous/Not logged-in
-
File Pages8 Page
-
File Size-