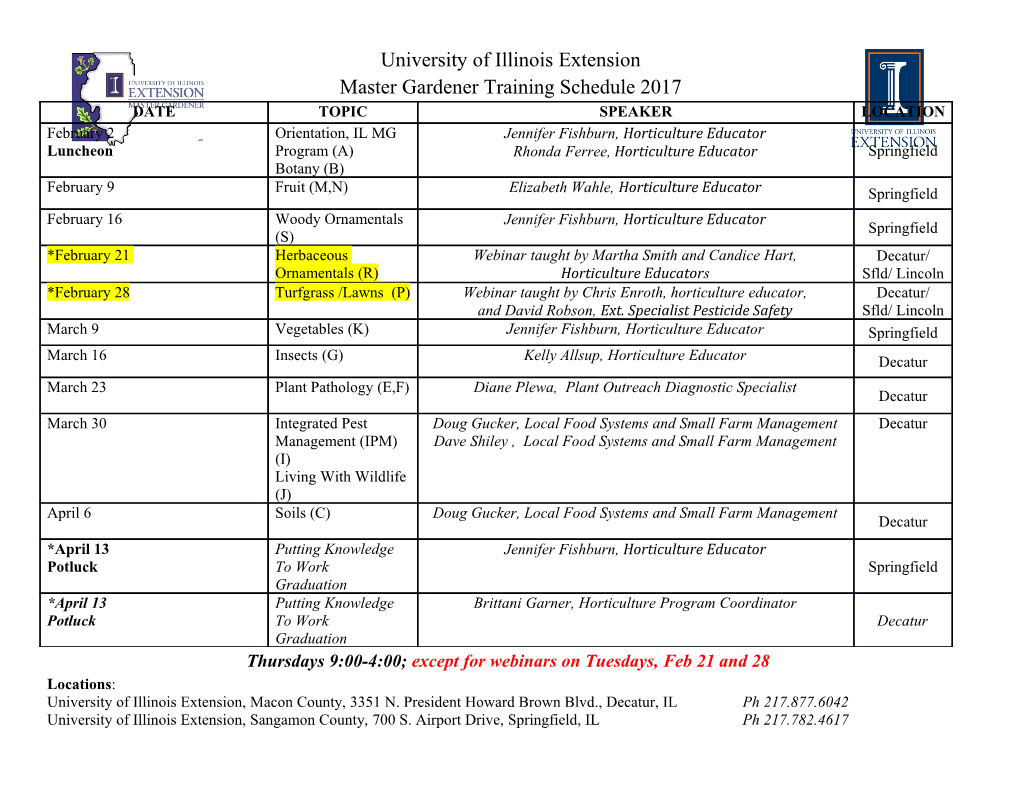
2020 AFS Proceedings of the 124th Metalcasting Congress Paper 2020-076 (10 pages) A Casting Trial to Evaluate Various Chemically Bonded Sand Disc-Shaped Specimens for Surface Finish and Erosion Defects M. Raval Altair Engineering Inc., Troy, MI S. Ramrattan Western Michigan University, Kalamazoo, MI Copyright 2020 American Foundry Society ABSTRACT greatest proportion of sand/metal defects associated with thin and tiny sections in the casting occurs with the Casting issues on thin wall surfaces and in complex chemically bonded sand process. AFS Research geometry interface is not negligible and can result in Committees are studying the troublesome and energy costly defects. Foundries prefer chemically bonded sand intensive issues related to sand defects with a plan to mold over green sand when it comes to castings with thin- minimize or eliminate the concern. This study examines wall sections and complex internal dimensions. Still, various chemically bonded silica sand systems for sand interfacial defects defects in chemically bonded sand erosion and surface finish in cast iron and aluminum process are an issue. This paper addresses chemically castings at different head heights. bonded sand erosion and surface finish issues for aluminum and cast iron castings. Erosion in chemically Erosion defects are major concerns with any casting bonded sand can occur when molten alloy dislodges process involving bonded sand. Erosion usually occurs grains of sand, resulting in a rough as-cast finish. within the gating system and/or at a mold-metal interface of the pattern cavity. Sand erosion is caused when molten Based on a casting trial used to study the erosion in alloy dislodges grains of sand resulting in a rough as-cast alternative green sand specimens; a new trial was finish. This defect is associated with turbulent metal fill. developed to teste to evaluate erosion on multiple This phenomenon of high velocity pouring can cause chemically bonded sand specimens simultaneously. Gray surface defects on casting. The reasons for erosion defects cast iron and an aluminum alloy were delivered from are due to one or a combination of the following: design, controlled head pressures and temperatures to achieve a raw materials (sand, binder and additives), molding and turbulent flow across chemically bonded sand specimens filling technology. Poor sand characteristics such as prior to solidification of the castings. Flow and reactive contaminants, weak sand properties, turbulent solidification simulation of the casting trial model was metal flow, head pressure, cross-sectional area of the conducted. The simulated predictions were evaluated gating system and molding technology are some examples along with results of aluminum and gray cast iron casting that can lead to erosion defects. trials at two different head heights. Results show that in both alloys there are surface differences among the Erosion phenomenon is the relation between a stationary various chemically bonded sand systems studied. entity and fluid flow. In other words, it is the defect caused by the kinetic energy of fluid flow. A sand mold Keywords: casting surface finish, remains stationary while molten metal flows inside the chemically bonded sand, disc-shaped specimens, sand cavity with some definite momentum. This impetus can erosion dislodge sand particles. When the bond between two particles breaks, because of flow momentum a lift occurs, INTRODUCTION and it removes these particles from the surface. This progression causes cavities on the mold surface that leads In the foundry industry, there can be many types and to surface roughness. causes of metal casting defects. These casting defects can be related to the alloy and/or the mold/metal interfacial Solidification simulation is a valuable tool in the foundry issues. There are several publications dedicated to industry. They can be used to predict casting defects. imagining and identifying causes for these defects. Simulations are mainly used for design and sometimes for However, the processing parameters related to such manufacturing problem solving. Nowadays the metal defects are lacking.1,2 Casting issues at the sand/metal casting industry is using a solidification simulation interface result in defects such as inclusions, veining, software to predict casting quality. The rational for using penetration, scabs, scars, erosion, etc.3 Moreover, the this approach would be to identify casting design issues Page 1 of 10 2020 AFS Proceedings of the 124th Metalcasting Congress Paper 2020-076 (10 pages) and detect metallurgical concerns prior to actual materials and processes, testing will be performed over production. various sand binder systems. The disc-shaped specimens used in this study is identified in Table 1. Current solidification simulation tools contain superior alloy property data but property data for granular media is PUCB Specimens lacking. Real time information such as temperature, The PUCB disc-specimens were prepared by blowing the pressure and fill velocities derived from simulation specimens with a laboratory core blower into a core box. software is useful in understanding erosion phenomena. Researchers can make a reasonable argument that either Materials: metal flow or the sand binder properties are responsible The sand was a washed and dried Wisconsin round grain for erosion defects by studying the properties of the silica sand 65 GFN, 3 screen, roundness/sphericity chemically bonded sand and simulation results. (Krumbein) 0.8/0.8, pH 7.1, acid demand 0.8 and the total Polyurethane binder level was 0.9% B.O.S. This chemically bonded sand erosion study uses a casting trial model developed at Western Michigan University Procedure: (WMU) and involves acquired related data from both 1) Add weighed sample of sand to DeLonghi Mixer. casting simulation and laboratory sand testing. The 2) Make two pockets in the sand. purpose of this study was to determine if there are 3) Add Part 1 component into one pocket and Part II to different erosion tendencies among various chemically the other pocket. bonded sands with respect to iron and aluminum castings. 4) Mix for 1 minute. 5) “Flip” mixture and mix for 1 additional minute. OBJECTIVES 6) Using laboratory core blower set at 0.379 MPa (55 1. To measure the surface roughness of a cast psi) for 0.5 seconds and blow the mixed sand into the alloy/chemically bonded sand specimen interface at four cavities of the core box. different head pressures. 7) Cure by gassing with TEA using a Luber gas 2. To measure the volumetric changes occurring at a generator. Gassing parameters: 1 second gassing with cast alloy/chemically bonded sand specimen TEA, followed by an air purge for 6 seconds (gas interfaces at different head pressures. pressure at 0.172 MPa (25 psi) and air purge pressure at 0.103 MPa (15 psi)). METHODOLOGY Refractory Coated PUCB: Some of the PUCB disc-specimens were refractory An experimental model was designed to perform a casting coated. The coating used in this study were ceramic- trial on chemically bonded sand specimens. The graphite coatings similar to those used by iron sand chemically bonded sand specimens will be used as the casting foundries. A LabWave IV microwave solids mold/metal interfaces during casting. The methodology analyzer was used to determine the solids content and was divided into three areas: deionized water was used to dilute the coating to 38% 1. Preparation of disc-shaped chemically bonded solids. Disc-shaped specimens were manually dipped into sand specimens. the mixed coating to the same depth for two seconds. 2. Gray cast iron and aluminum casting trials. 3. Data gathering, observation and analysis. SHLHB Specimens SHLHB specimens were prepared using a hot-box core Note: All chemically bonded sand systems used in the making technique used in industry when employing resin experiment were tested in controlled laboratory coated sand systems. conditions: the ambient temperature at 70 ± 2˚F (20 ± 1˚C) and relative humidity at 50±2%. Materials: The sand was an Illinois round grain silica sand 60 GFN, DISC SHAPED SPECIMENS 3 screen, roundness/sphericity (Krumbein) 0.7/0.7, pH In the present work, specimens of phenolic urethane 7.1, acid demand 0.8 and the total Phenolic-Novolac amine cold box (PUCB), hot-box shell (SHLHB) and 3D binder level was 1.3% B.O.S. printed furan (FUR3D) were fabricated. Procedure: Specimens (50 mm in diameter by 8 mm thick) were The hot-box cure temperature used for producing provided by three different manufacturers. The specimens was 250°C for 40 seconds. manufacturers all used dissimilar specimen fabrication techniques, sands, binder levels, and chemistries. The FUR3D Specimens chemical sand binder systems used were not optimized for These disc-specimens were 3D printed. the casting alloy, fill temperature, or head-pressure. To ensure the proposed approach is valid across numerous Page 2 of 10 2020 AFS Proceedings of the 124th Metalcasting Congress Paper 2020-076 (10 pages) Materials: the final casting. This prediction will allow the The sand was a washed and dried round grain silica sand comparison of actual castings to obtain information for 80 GFN, 2 screen, roundness/sphericity (Krumbein) improving the design. Table 1 shows values obtained 0.8/0.8, pH 7.0, acid demand 0.8 and the total Furan from simulation results. binder level was 1.4% B.O.S. Procedure: The FUR3D specimen were printed on an ExOne S Max #8. FUR3D printed disc-shaped specimens were produced within the same build-box. Processing parameters such as binder level, recoater angle, and print speed were controlled. Table 1. Disc-Shaped Specimens Types Specimens Fabrication Method PUCB Phenolic urethane amine cold box Refractory coated phenolic urethane Coat-PUCB amine cold box Figure 1. CAD image of erosion model. SHLHB hot-box shell Table 2. Simulation Predictions FUR3D 3D printed furan No. Temperature Velocity (m/s) CASTING TRIALS Aluminum 6” 730 1.4 The casting trial consisted of the following steps: Gray Cast Iron 6” 1511 (℃) 1.37 i.
Details
-
File Typepdf
-
Upload Time-
-
Content LanguagesEnglish
-
Upload UserAnonymous/Not logged-in
-
File Pages10 Page
-
File Size-