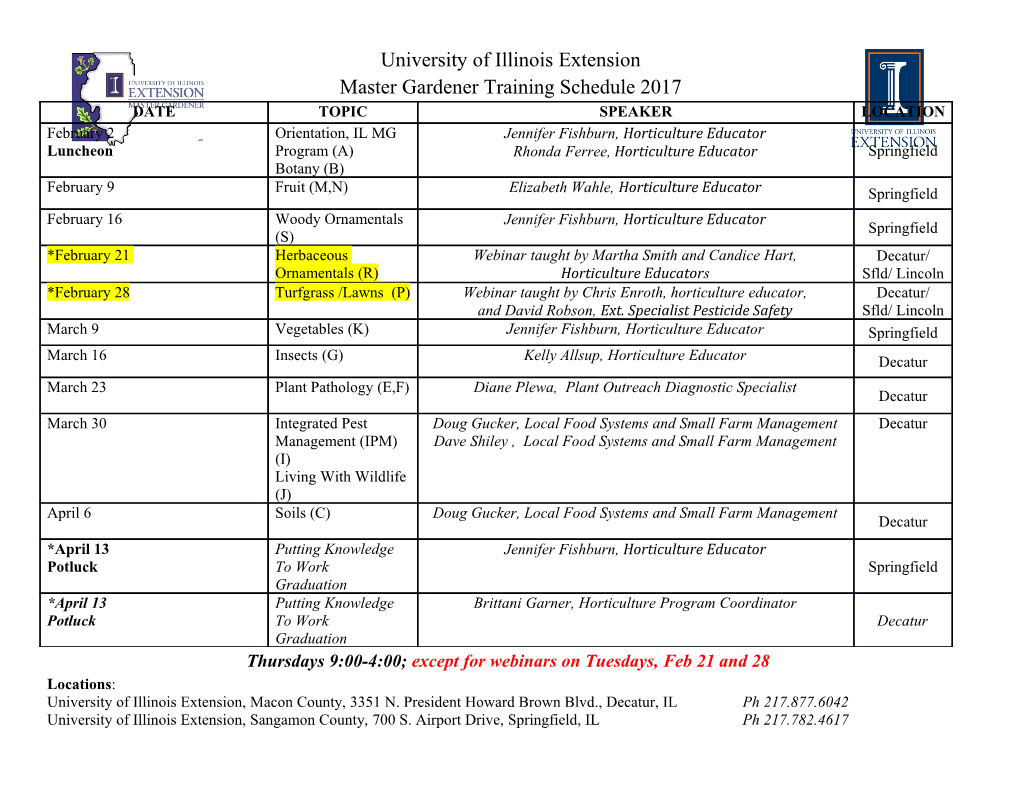
Europäisches Patentamt *EP000815285B1* (19) European Patent Office Office européen des brevets (11) EP 0 815 285 B1 (12) EUROPEAN PATENT SPECIFICATION (45) Date of publication and mention (51) Int Cl.7: C23C 18/12 of the grant of the patent: // C04B41/87, C04B41/50 22.08.2001 Bulletin 2001/34 (86) International application number: (21) Application number: 96901675.7 PCT/CA96/00088 (22) Date of filing: 13.02.1996 (87) International publication number: WO 96/29447 (26.09.1996 Gazette 1996/43) (54) METHOD FOR PRODUCING THICK CERAMIC FILMS BY A SOL GEL COATING PROCESS VERFAHREN ZUR HERSTELLUNG DICKER KERAMIKFILMS DURCH SOL-GEL-BESCHICHTUNGSPROZESS PROCEDE DE FABRICATION DE FILMS DE CERAMIQUE EPAIS METTANT EN UVRE UN PROCESSUS DE REVETEMENT SOL-GEL (84) Designated Contracting States: (74) Representative: AT BE CH DE DK ES FR GB GR IE LI NL PT SE Simpson, Alison Elizabeth Fraser et al Urquhart-Dykes & Lord, (30) Priority: 22.03.1995 US 409127 30 Welbeck Street London W1G 8ER (GB) (43) Date of publication of application: 07.01.1998 Bulletin 1998/02 (56) References cited: EP-A- 0 433 915 EP-A- 0 482 659 (73) Proprietor: QUEEN’S UNIVERSITY AT KINGSTON EP-A- 0 564 866 WO-A-96/00198 Kingston Ontario K7L 3N6 (CA) US-A- 4 921 731 (72) Inventors: • TECHNICAL DISCLOSURE BULLETIN, vol. 37, • BARROW, David No 09, September 1994, "Low Leakage, Ajax, Ontario L1S 6Z4 (CA) Temperature Invariant, High Dielectric Constant • PETROFF, Edward, T. Films, using Multilayered Sol-Gel Fabrication", Scarborough, Ontario M1T 1V8 (CA) page 27 - page 28 • SAYER, Michael • PATENT ABSTRACTS OF JAPAN, vol. 14, no. Kingston, Ontario K7L 1E4 (CA) 43(C-681); & JP,A,01275765 (SEIKO EPSON CORP), 06-11-1989 Note: Within nine months from the publication of the mention of the grant of the European patent, any person may give notice to the European Patent Office of opposition to the European patent granted. Notice of opposition shall be filed in a written reasoned statement. It shall not be deemed to have been filed until the opposition fee has been paid. (Art. 99(1) European Patent Convention). EP 0 815 285 B1 Printed by Jouve, 75001 PARIS (FR) EP 0 815 285 B1 Description Field of the Invention 5 [0001] This invention relates to the production of thick ceramic films, including composite films, on selected sub- strates, using a sol-gel coating technique. More particularly this invention relates to a technique for depositing poly- crystalline ceramic films such as lead zirconate titanate and partially stabilized zirconia, in thicknesses greater than 10µm. 10 Background of the Invention [0002] Ceramic coatings can be prepared by thermal or plasma spraying and physical vapour deposition (PVD) techniques. In plasma spray, a bulk powder is passed through a plasma and directed towards a substrate where it cools on contact. Films up to 10 mm thick can be produced in this way but usually need post-deposition heating as the 15 deposited film tends to be porous (10% porosity is considered good). Another drawback of the plasma spray technique is that only line of sight geometries can be successfully coated. In PVD, expensive vacuum systems are required to coat high quality ceramic films of less than 10 µm. In addition this technique is also limited to line of sight geometries. [0003] An alternative method, which has gained considerable ground and credibility in recent years, is sol-gel processing (cf. US-A-4 921 731, JP-A-1 275 765, EP-A-0 433 915, EP-0 482 659, EP-A-0 564 866). Organo-metallic 20 precursor compounds of the desired ceramic oxides are mixed and dissolved in a suitable solvent. The resultant solution is then hydrolysed to form a structured solution or gel containing organo-metallic polymers or macro-clusters. Additives can be added to control the viscosity and surface tension of the sol gel solution. Films are prepared by either spin, dip or spray coating or painting onto an appropriate substrate. The coated substrate is then fired to remove the organic material and a post-fire heating step is usually performed to fully develop the final ceramic structure. The sol gel process 25 has several advantages over other fabrication methods. It is simple, more economically feasible and permits coating of complex geometries, not necessarily line of sight. Usually ceramic films up to about 0.5µm can be deposited in a single layer but films up to about 3.0µm have been produced using a complex vacuum controlled firing treatment. Thicker films, up to about 10µm in thickness have been produced by successive coatings in 0.1µm layers. Clearly a 10µm film made 0.1µm at a time is a very time consuming and laborious process. In order to exploit the desired 30 properties of the ceramic, it is essential that the ceramic film should be crack-free. Sol gel films are, however, very susceptible to substrate interaction, defects and stresses within the film. Generally the thinner the film the lower the internal stresses and the number of defects. Solvents and organics can escape from 0.1µm layers relatively easily but for thicker layers this is not so resulting in defects which can act as nucleation centres for crack propagation. Sol gel films are also substrate dependent and most films are limited to metallized silicon or other highly polished substrates. 35 Conventional sol gel technology cannot, therefore, be used to produce thick, large area sol gel films. Object of Invention [0004] An object of the present invention is to provide an improved method for applying adherent ceramic films to 40 metallic substrates in thicknesses greater than 5µm and at least up to 200µm without cracking. [0005] Another object is to provide an improved sol-gel process for producing polycrystalline ceramic coatings on a wide range of substrates. Brief Statement of Invention 45 [0006] By one aspect of this invention there is provided a process for producing a crack-free polycrystalline ceramic film on a substrate comprising: (a) mixing a selected organo-metallic sol-gel solution with 5% to about 90% by weight of said solution of a selected 50 finely divided ceramic powder so as to produce a uniform stable dispersion; (b) applying said stable dispersion to a selected said substrate so as to provide a coating thereon up to about 6µm thick; and (c) firing said coated substrate at a temperature up to about 1000°C so as to remove any organic constituents and produce a stable crack-free polycrystalline metallic oxide film on said substrate. 55 [0007] By another aspect of this invention there is provided a process for producing a polycrystalline film selected from zirconia or titania on a substrate selected from aluminum foil and stainless steel, comprising: 2 EP 0 815 285 B1 (a) mixing sol gel mixture selected from titania and zirconia and a solution of a metal salt with 5% to 90% by weight of yttria or ceria stabilized zirconia powder or pure titania powder in a size range between .1 and 10 microns so as to produce a stable dispersion. (b) applying said stable dispersion to a selected said substrate so as to provide a coating up to 6µm thick; and 5 (c) firing said coated substrates at a temperature up to about 500°C so as to produce a stable crack-free polycrys- talline film on said substrate. [0008] By yet another aspect of this invention there is provided a process for producing polycrystalline composite ceramic films on a substrate comprising: 10 a) mixing a first selected organo-metallic sol gel solution with 5% to 90% by weight divided ceramic powder so as to produce a first uniform stable dispersion; b) mixing a second selected organo-metallic sol gel solution with 5% to 90% by weight of said solution of a second selected finely divided ceramic powder so as to produce a second uniform stable dispersion; 15 c) applying a first coating of one of said first and second stable dispersions to a selected said substrate; d) firing said first coating at a temperature up to about 1000°C so as to remove organic constituents and produce a stable crack-free polycrystalline first metal oxide film on said substrate; e) applying a second coating of the other of said first and second stable dispersions to said oxide film on said substrate; 20 (f) firing said second coating at a temperature up to about 1000°C so as to remove any organic constituents and produce a stable crack-free polycrystalline second metal oxide film on said first metal oxide film. Detailed Description of Preferred Embodiments 25 [0009] As noted above, sol-gel processing techniques first require the preparation of an organo-metallic solution of the desired ceramic oxide precursors in an organic solvent, followed by hydrolysation, and pyrolysation to remove the organic phase. Similar techniques are followed in the present invention with the important distinction that the primary organo-metallic solution is mixed with ceramic particles and subjected to ultrasonic mixing to form a sol gel based paint which can be deposited on simple or complex geometry substrates by either spin, dip or spray coating or painting, 30 followed by hydrolysation pyrolysation and heating in air. Typical formulations are described below and it is emphasized that these formulations are not critical but may be varied widely. Preparation of Organo-metallic solutions 35 (a) PZT Solutions [0010] 6 g of lead acetate or lead nitrate was dissolved in 4 g glacial acetic acid. 3.96 g zirconium propoxide, 2.091 g titanium isopropoxide were mixed so that the molar ratio of Zrx +Ti1-x = Pb, and the lead solution was added to the zirconium-titanium organic solution.
Details
-
File Typepdf
-
Upload Time-
-
Content LanguagesEnglish
-
Upload UserAnonymous/Not logged-in
-
File Pages14 Page
-
File Size-