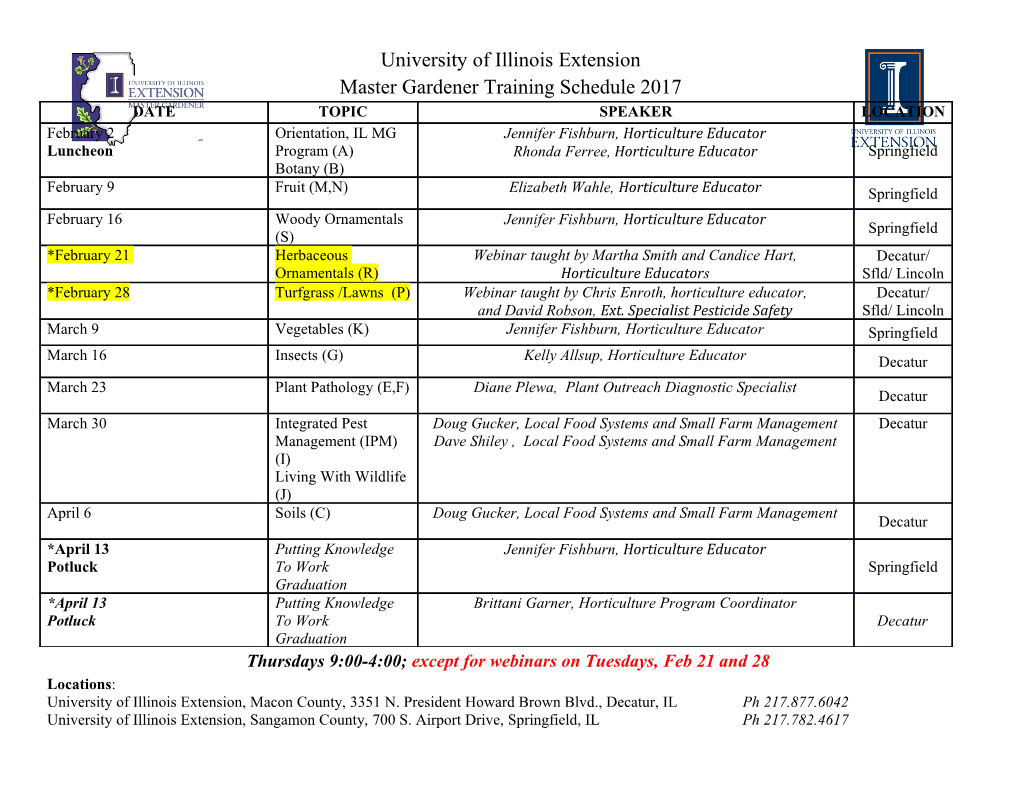
Fall 2001 Pottery Making illustrated 1 2 Pottery Making illustrated Fall 2OO1 Features Stick in the Mud..........................................................................9 by Marj Peeler Veteran potter shares an innovative low-stress technique for forming cylinders. Glaze Making 101......................................................................14 by Michael Hamlin Develop inexpensive glaze bases using readily available ingredients. Creating Original Designs........................................................17 by Ivor Lewis Step-by-step technique for designing your own pots. Plaster: Getting It Right........................................................... 22 Valuable technical information from the United States Gypsum Corporation demon­ strates the effects of materials, time, and consistency on your molds. Festive Ornaments......................................................................25 by Hanna Lore Hombordy Delight family and friends with personalized ornaments this holiday season. What Is Slipware?.......................................................................30 by Mary Wondrausch An excerpt from Wondrausch’s updated book answers a perennial question. Making an Inexpensive Light Box..........................................33 by Anderson Turner and Aaron Calvert When you want to make professional-looking photos, you need the right equipment. From the Biggest to the Smallest............................................41 by Craig Hinshaw Little kids learn about giant horses and sculptures in clay. GFCI Extension Cord...............................................................43 by Don Adamiatis Reduce shock hazards in your studio with a low-cost, easy-to-make extension cord. Departments Down to Business—Website Fever..............................................................36 by Chris Campbell Guidelines to help you decide if a website is right for you. The Budget Potter—Design Transfer......................................................... 38 by Sylvia Shirley Now you can get design from a bottle. O ff the Shelf: The Aesthetics of Functional Pottery............................46 by Sumi von Dassow A look at books that take you beyond the basics. Cover: Marj Peeler uses a stick to form a cylinder from the inside. See story on p. 9. Fall 2OO1 Pottery Making illustrated 3 Editor: Bill Jones Production Manager: John Wilson Circulation Supervisor: Cleopatra G. Eddie Graphic Design: Debi Hampton Graphic Production: Dave Houghton Advertising Manager: Steve Hecker Advertising Assistant: Debbie Plummer Customer Service: Mary Hopkins Publisher: Mark Mecklenborg Editorial, Advertising & Circulation Offices 735 Ceramic Place PO Box 6136 Westerville, OH 43086-6136 Phone: (614) 794-5890 Fax: (614) 794-5892 E-mail: [email protected] www.potterymaking.org Pottery Making Illustrated (ISSN 1096-830X) is pub­ lished 5 times a year in January, April, June, September and October in 2001, and bimonthly commencing in 2002, by The American Ceramic Society, 735 Ceramic Place, Westerville, OH 43081. Periodical postage paid at Westerville, OH, and addi­ tional mailing offices. Opinions expressed are those of the contributors and do not necessarily represent those of the editors or The American Ceramic Society. Subscription rates: 6 issues (1 year) $22,12 issues (2 years) $41, 18 issues (3 years) $58. Add $18 per year for subscriptions outside North America. In Canada, add 7% GST (R123994618). All payments must be in US$ and drawn on a US bank. Allow 6-8 weeks for delivery. Advertising: Ad rates and ad information are available on the web site or by contacting Steve Hecker at the address above or by phone at (614) 794-5809. Change of address: Send your change of address via e-mail, to the Circulation Department, or on our web­ site. Allow six weeks advance notice. Contributors: Writing and photographic guidelines are available on request and on the web site. Mail man­ uscripts and visual materials to the editorial offices. Photocopies: For a fee, searchable databases and doc­ ument delivery are available through The American Ceramic Society’s Ceramic Information Center, PO Box 6136, Westerville, OH 43086-6136; e-mail [email protected]; or phone (614) 794-5810. Permission to photocopy for personal or internal use beyond the limits of Sections 107 and 108 of the U.S. Copyright Law is granted by The American Ceramic Society, ISSN 1096-830X, provided that the appropriate fee is paid directly to the Copyright Clearance Center, 222 Rosewood Dr., Danvers, MA 01923 USA (978) 750- 8400; www.copyright.com. Prior to photocopying items for educational classroom use, please contact Copyright Clearance Center, Inc. This consent does not extend to copying items for general distribution, for advertising or promotional purposes or to republishing items in whole or in part in any work and in any format. Please direct republication or special copying permis­ sion requests to the Director of Publications, The American Ceramic Society, PO Box 6136, Westerville, OH 43086-6136. Back Issues: When available, back issues are $5 each plus $3 postage for the first copy and $1 for each additional copy thereafter. For orders outside North America, add $6 ($2 for additional copies). In Canada, add 7% GST. Postmaster: Send address changes to Pottery Making Illustrated, PO Box 6136, Westerville, OH 43086-6136. Form 3579 requested. Copyright © 2001 The American Ceramic Society All rights resewed www.ceramics.org 4 Pottery Making ILLUSTRATED Fall 2001 Fall 2001 Pottery Making illustrated 5 8 Pottery Making illustrated Fall 2001 A handbuilding technique for forming cylinders by Marj Peeler Clay! Wonderful clay! For me, it has been a lifelong love affair—mud pies in the back yard, Permoplast clay for Christmas, little clay sculptures in high school, coiled pots in college and, finally, our own wheel and kilns. My husband, Richard, and I worked together in clay PHOTOS: MARY FIELD for 51 years. For the last 30 years, we were professional potters. We enjoyed wheel throwing, slab building, coiling—we used all methods of clay working to make pottery and sculpture. Because I had surgery on my right shoulder, I have been unable to throw on the wheel these last two years. I found that handbuilding was less stressful on my hands and arm, and I worked out a low-stress method for form­ ing cylinders by taking a fat coil and rolling it from the center with a dowel rod. Then it was easy to add a bot­ tom and a top to form an interesting vase shape. I believe this technique could be used to create some interesting pottery or sculpture. Try it. Maybe you’ll like it! Vase, 8½ inches high, handbuilt stoneware with copper blue glaze and fired to cone 10 reduction. Oval-shaped vase form, 9 inches high, handbuilt with carved surface decoration and fired to cone 10 reduction. Fall 2 0 0 1 Pottery Making illustrated 9 Step 1 Step 2 Tools for this project include canvas, heavy rolling pin, dowel Roll three small slabs for bottom, top, and finial. Roll the clay on rods of various diameters, slip and brush, fettling knife, comb, canvas, turning frequently. Roll both directions to form even wooden paddle, and a clean hard surface to roll clay out on. slabs. Put slabs aside. Step 3 Step 4 Wedge clay well! Form into a fat coil and flatten both ends. Gently roll the coil with the dowel rod. This expands the coil Carefully insert a %-inch dowel rod into the center of the coil. from the center. Remove the dowel rod and insert a piece of Tip: Reverse the coil and insert the dowel from the opposite broom handle to further expand the hole. Keep rolling carefully end to meet the hole in the center. This is easier than pushing to make the wall of the cylinder an even thickness. Remove the the rod clear through the clay in one push. broom handle and insert a larger rod until the desired size of the cylinder is reached. Step 5 Stand the cylinder on one of the clay slabs you made earli­ er. Mark the shape and cut the bottom with the fettling knife. Step 6 Score the edge of the cylinder with a piece of comb, then score the slab where the cylin­ der will join the bottom piece. 10 Pottery Making illustrated Fall 2001 Step 7 Step 8 Step 9 Brush thick slip on both surfaces and join Gently but firmly paddle the bottom onto Paddle the bottom of the pot with a them. the cylinder, and paddle the excess clay wooden spoon to form a slightly concave onto the outside of the pot. This becomes shape. Note: A pot with a concave bot­ part of the design of the pot. tom has more stability when sitting on a flat surface. Step 10 Step 11 Step 12 Cut a top from the slab. Place this clay Open a short piece of thick coil with the Reinforce the seams with a thin coil, and slab onto some ½-inch foam rubber, and dowel rod to form a neck cylinder. Attach smooth it into a nice curved transition. gently create a concave form by pressing it to the top dome, then score, slip, and it with a rubber rib. Turn the piece over so paddle. Add a decorative top or finial and that you have a slightly convex piece. repeat the attaching sequence. Cut an This dome shape keeps the top of the opening through the top slab with a fet­ vase form from sagging in the firing. tling knife. Score, slip, and place it on top of the cylinder and paddle. Fall 2001 Pottery Making illustrated 11 Step 13 Step 14 Step 15 The cylinder can be left round or pressed When the clay stiffens to almost leather The vase is complete and ready to dry into an oval shape. For this pot, I formed hard, support the vase on a piece of egg- slowly. For the bottom to dry evenly, set irregular facets. crate foam rubber while carving the the pot on two square chopsticks to pro­ Tip: The back side of a teaspoon works design into the surface of the pot. Bevel mote air circulation. well to make concave facets. the bottom edge of the pot with a veg­ Note: I’ve found that paddling strength­ etable peeler to give the vase a little “lift.” ens the joints so well that the pieces don’t separate in the drying or firing.
Details
-
File Typepdf
-
Upload Time-
-
Content LanguagesEnglish
-
Upload UserAnonymous/Not logged-in
-
File Pages52 Page
-
File Size-