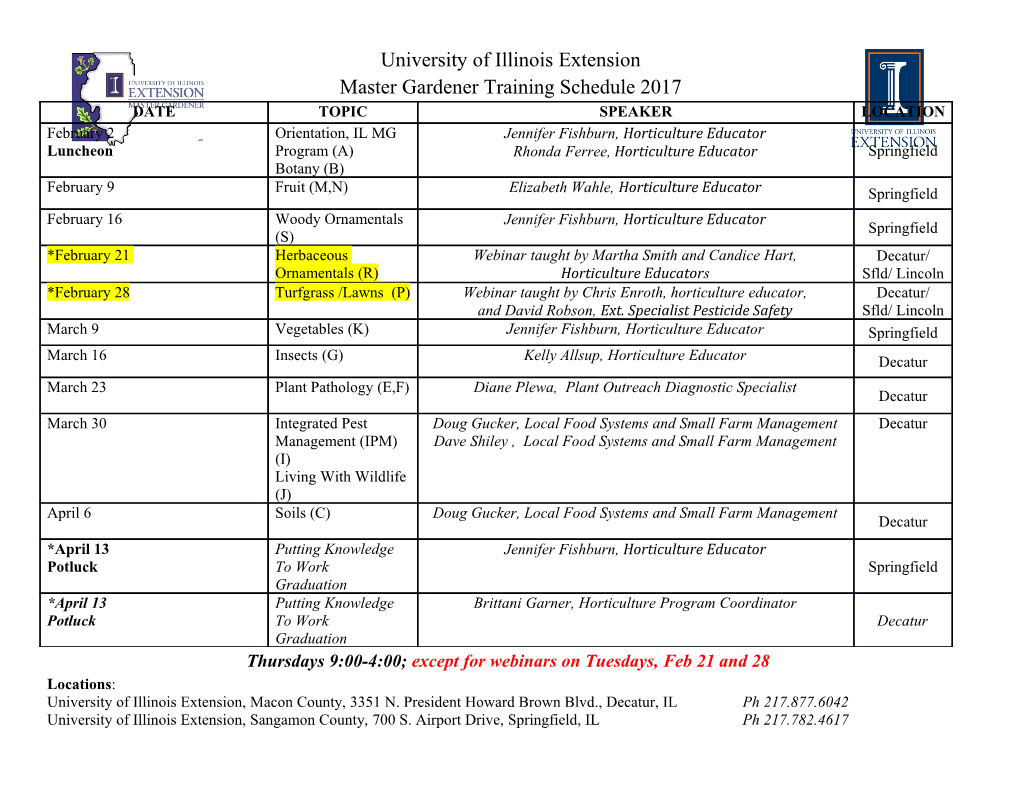
ZZM/CLAB-MOEF/17/ 12-06-2019 THE DIRECTOR (S), Speed Post with AD Ministry of Environment & Forest, Regional Office – (Southern Zone), Kendriya Sadan, 4th Floor, E & F Wings, 17th Main Road, 2nd Block, Koramangala, BANGALORE – 560 034. Dear Sir, Sub : Expansion – cum - modernisation of paper unit (1,80,000 to 3,20,000 TPA) and captive Power plant (30 MW to 74.8 MW) at Dandeli, Haliyal, Uttara Kannada by M/s The West Coast Paper Mills Ltd., - Environmental Clearance –reg. Ref : 1. Letter No J-11011 / 408 / 2006 – 1A. II (I) dated – 19-07-2007 of Ministry of Environment & Forests. Government of India, New Delhi. 2. EP/12.1/478/KAR/4536 dated: 20th May, 2009. We enclose here with point wise compliance report from Oct - 2018 to Mar-2019. We hope, you will find the same in order. Thanking You, Yours faithfully, For WEST COAST PAPER MILLS LIMITED, DANDELI. B.H.RATHI PRESIDENT (TECH) Encl: as above. CC : ENVIRONMENT OFFICER, Speed Post with AD Karnataka State Pollution Control Board, Regional Office, “Parisara Bhavan”, LIG-11 b – 217, Near Hari Om Trust, Habbuwada, KARWAR. West Coast Paper Mills Limited, Dandeli. Status from Oct - 2018 to Mar-2019 Date: 12-06-2019 Sub: Compliance Report for the Consent Conditions by Ministry of Environment & Forests. Ref: MoEF letter no J-11011/408/2006-1A. II (I), dated 19th July, 2007. Consent Conditions WCPM compliance status from Oct - 2018 to Mar-2019 A. SPECIFIC CONDITION: i) The gaseous emissions (SPM, SO2, NOX, & H2S) from The gaseous emissions from the entire unit are various process units shall conform to the standards maintained within stipulated norms. We are monitoring prescribed from time to time. The KSPCB may specify the PM 2.5, PM10, SO2, NOX & H2S the results of the more stringent standards for the relevant parameters analysis are being sent to KSPCB in the monthly reports. keeping in view the nature of the industry, its size & location. At no time, the emission level shall go beyond the prescribed standard in the event of failure of any Pollution Control system (S) adopted by the unit, the respective unit should not restarted until the control measure are rectified to achieve the desired efficiency. ii) Three on- line monitoring station for ambient air near We have already installed the 3 nos of On-line CAAQM the boundary of the plant shall be set up along with stations in our mill area & 8 online stations are installed another on – line stack monitoring system for recovery to RLK, CRB, and power boilers. boiler for particulate matter, SO2, NOx & H2S & the We are already connected the WQMS & CEMS data to on- line data shall be submitted to the CPCB & KSPCB. CPCB website. iii) The company shall phase out Elemental Chlorine from Our new cooking system is based on the state of art pulp bleaching process. Obsolete bleaching sequence technology having modified batch cooking process, new ( C/D- EP- H – D ) technology shall be replaced by new brown stock washing, oxygen de-lignifications, knot Oxygen de- lignification combined with elemental separation & screening plant. Obsolete bleaching chlorine free bleaching sequence (D0 – E0p – D 1) to sequence (C/D-EP-H-D) technology has been replaced bring down the pollution load. with new oxygen de-lignifications system followed by elemental chlorine free bleaching sequence (DHT-Eop- DND). Thus use of elemental chlorine in pulp bleaching has been completely eliminated. Hence complied with. iv) ESP shall be provided to the new boiler viz. Coal fired All the stacks of coal fired boilers, chemical recovery boilers chemical recovery boiler & & lime mud re- boiler & lime mud re burning kiln has been provided burning kiln & SPM emission shall be maintained below with ESP units to conform SPM concentration well below 150mg/Nm3 . Low NOx burners shall be installed to 150 mg/Nm3. the boilers. Dust suppression system shall be provided The company has technologically upgraded Chemical to coal yard. Recovery Plant by replacing old multiple effect evaporators, & direct contact evaporators with falling film evaporators. The black liquor from FFE at higher concentration i.e., above 70 % is fired in a new Chemical Recovery Boiler. These changes have resulted in to reduction of generation of malodorous gases. The H2S emission from CR boiler is negligible. Hence there is no need of installation of NOX burners & we request you to exempt us from this condition. We have installed non condensable gases burner system which is manufactured by M/s Carbone of America, Salem, V.America, exported by M/s A.H.Lundberg Associates Inc. Bellevue W. America & marketed in India by M/s Elof Hansson (India) Pvt. Ltd of Chennai. The system is running satisfactorily. Water sprinklers has been installed at coal handling area & sprinkling is being done using treated effluent. The system is running satisfactorily. v) Fugitive emission shall be controlled by providing dust All the stacks of coal fired boilers, chemical recovery collectors & water spraying system at material boiler & lime mud re-burning kiln have been provided transfer points. Odour shall be controlled by installing with ESP units to conform SPM concentration below 150 odour collection system & subsequently incineration at mg/Nm3. Consent Conditions WCPM compliance status from Oct - 2018 to Mar-2019 Rotary kiln & monitoring of H2S & Mercaptans shall be Appropriate burners for fuel firing have been provided. carried out once in a month in the work environment. Sprinklers have been installed at coal handling area & sprinkling is being done using treated effluent. We have installed non condensable gases burner system which is manufactured by M/s Carbone of America, Salem, V.America, exported by M/s A.H.Lundberg Associates Inc. Bellevue W. America & marketed in India by M/s Elof Hansson (India) Pvt. Ltd of Chennai. The H2S testing is being carried out quarterly as it is non detectable in the test reports. However Mercaptans testing is being done by external agency & the results shows that the mercaptans in the Ambient air is almost NIL. Report of external party is attached as Annexure-II. vi) Total fresh water, requirement from River kali shall We have got the permission to draw up to 1,00,000 m3/d not exceed 1,00,000 m3/d & prior permission from the fresh water from Kali river in the Consent for government of Karnataka for the remaining 15,000 m Establishment from Government of Karnataka & 3/ d shall be obtained. Effort shall be made to reduce agreement is signed on 15-01-2009 with Water Resource water consumption by recycle & reuse. No ground Department G.O.K. water shall be extracted. The waste water from the The Details of recycling of water to reduce fresh water process shall not exceed 85,885 m 3/ d. The consumption vis-à-vis water balance has already been wastewater shall be segregated into pulp mill & paper given to you vide letter reference no machine stream & treated independently in the ZZB/PD&P/18/17578 dated 17-07-2008. No ground water effluent treatment plant (ETP) before discharge to being extracted. The average waste water discharge for Halmaddi Nala leading to river kali. the last six months is 45,749 M3/Day. vii) The company shall make continued effort in reducing Since we have selected the state of art technology, the volume of effluent discharge into the through involving closed system, the fresh water consumption is recycling / reuse techniques & reducing the pollution less. load by adopting advanced wastewater treatment Previously, on an average, we were drawing 72,000 technologies. m3/d of raw water for the paper production of 1,80,000 MT. Now, after a raised production to 3,20,000 MT, the water intake was raised to only 15,000 m3/d. Practically the drawing of raw water on an average is 54,608 m3/d for the last six months. This has been achieved by internal recycling/reuse system of the modernised plants & also the reuse of effluent of oxygen stage of fibre line in to recovery system. Thus the water intake is 63 m3/ton & treated trade effluent discharged has reduced to a level of 52 m3/ton for the last six months. viii) The performance of the Effluent Treatment plant We have tried few pilot trials for removal of colour in shall be improved & effort shall be made to bring effluent. But the process is not economically viable & down the color, total suspended solids in the final there is waste disposal burden causes Air Pollution. treated effluent by adopting processes like activated In this regard, we have stressed more on colour removal Carbon filter, use of better flocculating & at the source due to which, we are able to reduce the decolourising agent etc. The quantity of the treated maximum colour of the effluent. effluent shall conform to the prescribed standards & The colour of treated effluent is around 50 - 70 Co-Pt used for irrigation. units. ix) Effort shall be made to reduce colour in wastewater We have tried few pilot trials for removal of colour in substantially after installation of advance cooking effluent. But the process is not economically viable & system and ECF bleaching. The use of Ferric/Ferrous there is waste disposal burden causes Air Pollution. chloride shall be optimized to further reduce the color In this regard, we have stressed more on colour removal in the treated effluent. at the source due to which, we are able to reduce the maximum colour of the effluent. We have been able to reduce the colour of treated effluent is around 50 – 70 Co-Pt units. In view of this the use of Ferric/Ferrous chloride we had tried it in our lab.
Details
-
File Typepdf
-
Upload Time-
-
Content LanguagesEnglish
-
Upload UserAnonymous/Not logged-in
-
File Pages19 Page
-
File Size-