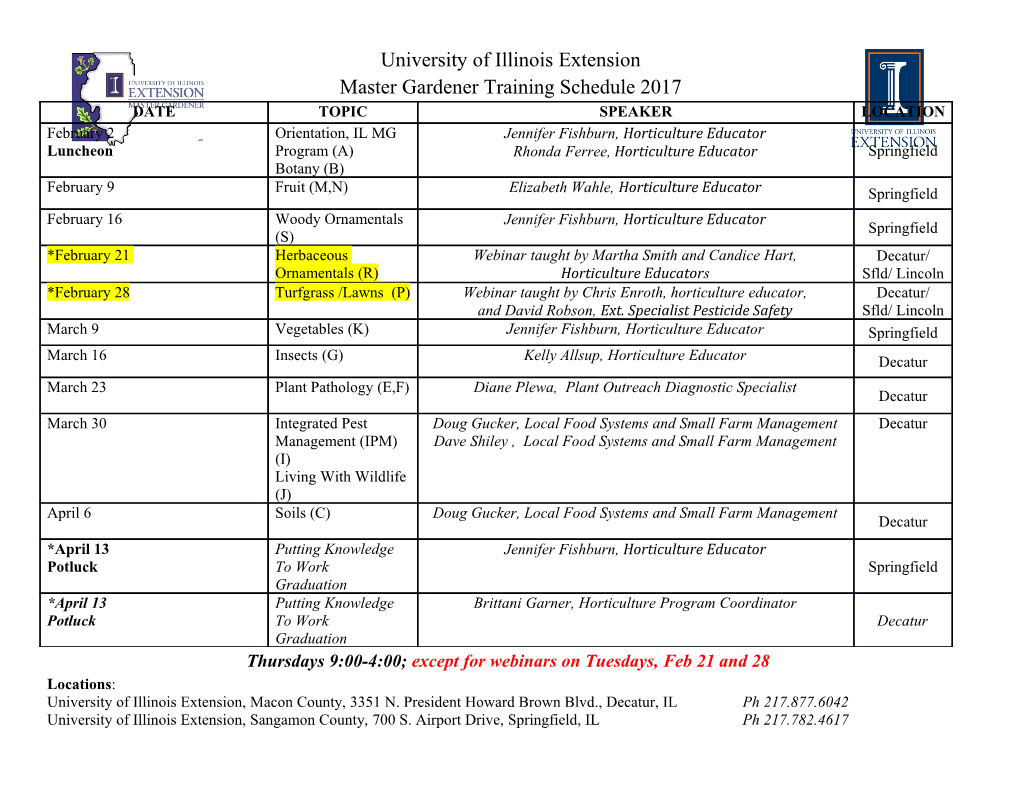
Journal of Exposure Science and Environmental Epidemiology (2006) 16, 156–171 r 2006 Nature Publishing Group All rights reserved 1559-0631/06/$30.00 www.nature.com/jes Chrysotile asbestos exposure associated with removal of automobile exhaust systems (ca. 1945–1975) by mechanics:Results of a simulation study DENNIS J. PAUSTENBACH,a AMY K. MADL,a ELLEN DONOVAN,a KATHERINE CLARK,a KURT FEHLINGa AND TERRY C. LEEb aChemRisk, Inc., San Francisco, CA, USA bCarolina EHS, Lake Wylie, SC, USA For decades, asbestos-containing gaskets were used in virtually every system that involved the transport of fluids or gases. Prior to the mid-1970s, some automobile exhaust systems contained asbestos gaskets either at flanges along the exhaust pipes or at the exhaust manifolds of the engine. A limited number of automobile mufflers were lined with asbestos paper. This paper describes a simulation study that characterized personal and bystander exposures to asbestos during the removal of automobile exhaust systems (ca. 1945–1975) containing asbestos gaskets. A total of 16 pre-1974 vehicleswith old or original exhaust systems were studied. Of the 16 vehicles, 12 contained asbestos gaskets in the exhaust system and two vehicles had asbestos lining inside the muffler. A total of 82 samples (23 personal, 38 bystander, and 21 indoor background) were analyzed by Phase Contrast Microscopy (PCM) and 88 samples (25 personal, 41 bystander, and 22 indoor background) by Transmission Electron Microscopy (TEM). Only seven of 25 worker samples analyzed by TEM detected asbestos fibers and 18 were below the analytical sensitivity limit (mean 0.013 f/cc, range 0.001–0.074 f/cc). Applying the ratio of asbestos fibers:total fibers (including non-asbestos) as determined by TEM to the PCM results showed an average (1 h) adjusted PCM worker exposure of 0.018 f/cc (0.002–0.04 f/cc). The average (1 h) adjusted PCM airborne concentration for bystanders was 0.008 f/cc (range 0.0008–0.015 f/cc). Assuming a mechanic can replace four automobile single exhaust systems in 1 workday, the estimated 8-h time-weighted average (TWA) for a mechanic performing this work was 0.01 f/cc. Under a scenario where a mechanic might repeatedly conduct exhaust work, these results suggest that exposures to asbestos from work with automobile exhaust systems during the 1950s through the 1970s containing asbestos gaskets were substantially below 0.1 f/cc, the current PEL for chrysotile asbestos, and quite often were not detectable. Journal of Exposure Science and Environmental Epidemiology (2006) 16, 156–171. doi:10.1038/sj.jea.7500450; published online 2 November 2005 Keywords: chrysotile asbestos, gasket, automobile exhaust system, mechanic, occupational exposure. Introduction as resist chemical damage under a variety of conditions (Brown and Gordon, 1980). From the advent of the internal Gaskets have been in use from the beginning of the industrial combustion engine, a wide variety of materials have been revolution and through the evolution of the steam engine and used as a gasket material, including leather, paper, steel, the internal combustion engine (Brown and Gordon, 1980). copper, aluminum, cork, rubber, asbestos, and plastic A gasketisa material that isclamped between two, typically (Brown and Gordon, 1980). metal, facesand actsasa staticseal. The primary function of In the early yearsof the automotive industry(during WW a gasket is to insure that fluids, such as oils, fuels and I), gasket material primarily consisted of paper or cork. coolants, do not leak to the outside and keep dirt, Cellulose fibers were often saturated with a variety of contaminants, and air out of engines and other mechanisms products, such as glycerine, animal glue, and rubber latex, of the drive linesand associatedvehicle components(Brown to improve the seal of paper gaskets. During WW II, the and Gordon, 1980). For proper engine function, gasket formulation of paper gaskets (usually containing a mixture of materialsare often required to handle extreme temperatures, asbestos and cellulose fibers) went through a major revolution. pressures, and thermal expansion of adjoining flanges, as well Styrene and nitrile rubber elastomers were mixed with the cellulose and asbestos fibers to form an encapsulated material. Asbestos containing an elastomeric binder was a common 1. Address all correspondence to: A.K. Madl, ChemRisk, Inc., 25 Jessie gasket material during the early years of the automotive Street at Ecker Square, Suite 1800, San Francisco, CA 94105, USA. industry (Brown and Gordon, 1980). Historically, asbestos Tel.: 1 415 896 2400. Fax: 1 415 896 2444. þ þ gaskets primarily contained chrysotile asbestos, whereas E-mail: [email protected] Received 4 April 2005; accepted 27 June 2005; published online 2 crocidolite fiberswere typically usedwhen concentrated acid November 2005 media were handled (Kelleher and Bartlett, 1983). Chrysotile asbestos exposure Paustenbach et al. Chrysotile asbestos has several beneficial qualities that and the engine. The exhaust pipe, which extends from the make it an effective gasket material. It is heat and chemical exhaust manifold, is typically interrupted by a flange that is resistant, flexible, and economical (Kelleher and Bartlett, located underneath the engine. Thisexhaustpipe flange is 1983). Chrysotile absorbsand holdslubricantswell and has usually fitted with a gasket and the remaining exhaust pipe great compressive and tensile strength (Kelleher and Bartlett, extendsto the muffler and tail pipe in one piece, after which 1983). In addition, asbestos provides a good reinforcement the engine exhaust is released into the air. Mufflers are used for elastomers in that the magnesium ion in asbestos in exhaust systems to reduce the noise of the engine’s exhaust reportedly reactswith carboxylated rubbersand producesa and typically have passageways for the exhaust gases to flow. more complete vulcanization (tighter cure) (Kelleher and The asbestos paper contained within some historical mufflers Bartlett, 1983). was usually encased between two metal sheets that comprised In 1971, the Occupational Health and Safety Adminis- the outside shell of the muffler. Catalytic converters were tration (OSHA) promulgated the first in a series of several introduced in the mid-1970s to lower exhaust emissions by federally regulated workplace Permissible Exposure Limits reacting with gasoline and other organic vapors not (PELs) for airborne asbestos. By the early 1970s, the use of completely consumed by the engine. The catalytic converter asbestos-containing materials was being phased out across islocated along the exhaustpipe between the engine and the several industries, including the automobile industry due to muffler. concerns about the health hazard. Although asbestos- Several studies have evaluated occupational exposure to containing automobile partswere, in general, discontinued airborne asbestos during the replacement of asbestos- a number of yearsago, recent concernshave been raised containing gaskets. However, these studies have primarily regarding the potential exposure to asbestos during auto- focused on the formation, removal, and installation of mobile repair work on exhaust systems and mufflers. industrial-sized gaskets used in a variety of industrial settings, The automobile exhaust system serves several functions. It such as maritime, refineries, and chemical and energy plants ventshigh-temperature engine exhaustgasesawayfrom the (Liukonen et al., 1978; Mangold, 1982a, b, 1983, 1985, combustion chamber of the engine, optimizes engine 1989a–h; Cheng and McDermott, 1991; McKinnery and performance, reducesnoisefrom the engine, and, in modern Moore, 1992; Spence and Rocchi, 1996; Spencer, 1998; cars, reduces exhaust emissions. The automobile exhaust Fowler, 2000; Boelter et al., 2002; Longo et al., 2002). In system is typically comprised of an exhaust manifold, exhaust general, these studies show that asbestos exposures from pipes, muffler, and, after the mid-1970s, a catalytic gasket replacement, asperformed by pipefittersor other converter. The exhaust manifold is a single metal piece that tradesmen using standard tools of the trade, were not likely funnelsexhaustgasesdirectlyfrom the cylindersof the engine to have been in excess of occupational exposure limits into a single exhaust pipe, which extends to the muffler and contemporaneouswith the yearsof exposureor current the tail pipe (Figure 1). The exhaust manifold is usually made occupational exposure standards (in most circumstances). of cast iron due to the extreme temperatures of the engine Data from these studies indicated that, only in a few exhaust and is bolted to the engine block typically with a instances, certain activities may create exposures in excess of manifold gasket between the flange of the exhaust manifold current PELs (i.e., power wire brushing of flanges and gasket formation using workshop tools). While these studies provide insight about occupational exposure to airborne asbestos during the replacement of industrial gaskets, they are not representative of the conditions a mechanic would experience while handling gaskets in automobile exhaust systems. No studies published to date have evaluated such conditions. The purpose of this study was to characterize personal and bystander exposures to asbestos during the removal of automobile exhaust systems (ca. 1945–1975) containing asbestos gaskets. These data were used to estimate an 8-h time-weighted average (TWA) exposure for mechanics performing thistype of automobile repair work. Methods Description
Details
-
File Typepdf
-
Upload Time-
-
Content LanguagesEnglish
-
Upload UserAnonymous/Not logged-in
-
File Pages16 Page
-
File Size-