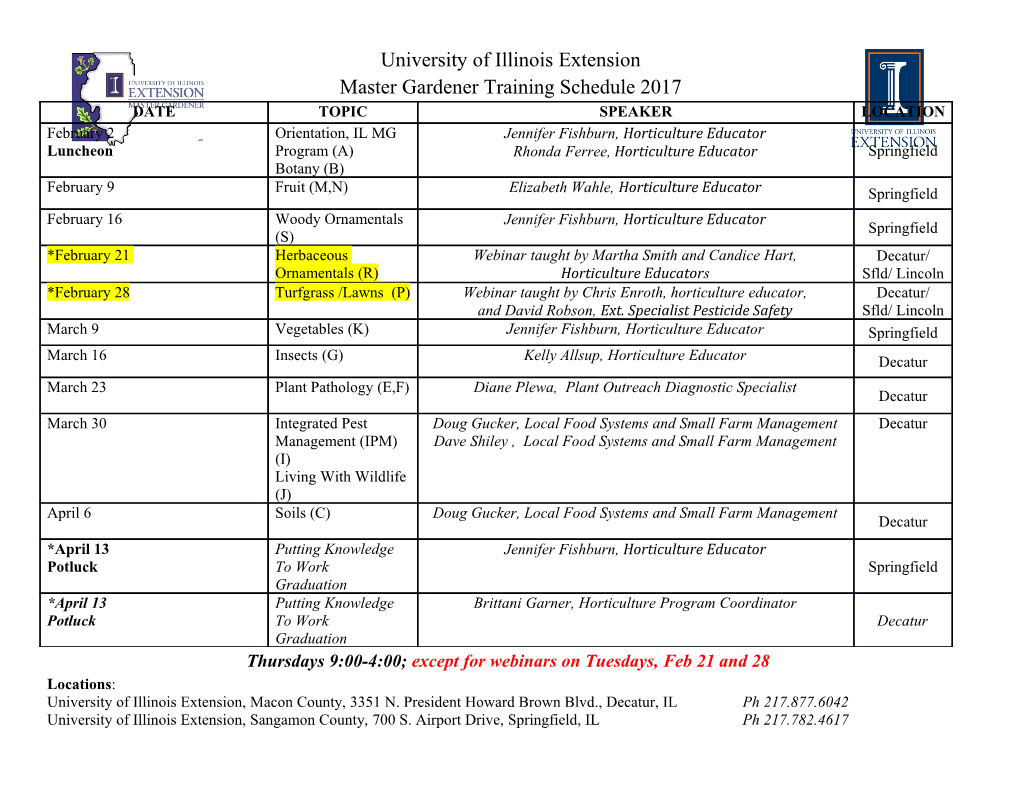
Metallographic preparation of titanium Application Titanium is a relatively new metal titanium production and processing Notes and expensive to produce, but its is extremely important. outstanding properties of high strength to weight ratio, excellent This is why metallography of corrosion and heat resistance have titanium is an integrated part of made titanium and its alloys well quality control of titanium, from established engineering materials. monitoring the initial production process, to porosity checks on Titanium is exceptionally resist- cast parts and controlling heat ant to corrosion by a wide range treatment processes. In addi- of chemicals. Its high affinity for tion, metallography plays a role oxygen results in a thin, but dense, in research and development of self-healing stable oxide layer, which titanium alloys and products. provides an effective barrier against incipient corrosion. In addition, it Titanium is a very ductile metal is the high strength to weight ratio, and prone to mechanical de- maintained at elevated tempera- formation. For the abrasive tures, which makes titanium and processes in metallographic its alloys attractive cutting, grinding and polish- for many critical ing, this aspect has to be applications. taken into consideration. Titanium and its al- loys are widely used in the aerospace and aircraft, chemical and medical industry, where high safety is essen- Martensitic structure in the heat influenced zone on a tube weld. tial. Consequently, quality control of Etchant: Weck's reagent, 1000 x Difficulties during metallographic preparation Cutting: Titanium can easily overheat Grinding and polishing: during cutting and large burrs can Due to its ductility titanium deforms occur: and scratches easily: Solution: Special cut-off wheel for titanium. Chemical-Mechanical polishing. Electrolytical polishing. Fig. 1 Fig. 2 DIC, 50 x Fig. 5: Screws and bone Production and plate electro-chemically oxidized for colour coding. The colours are the result applications of different thickness of of titanium the oxide layer. The production of titanium is a three-step process: 1. The first step is the manufacture of titanium sponge and involves the chlori- Fig. 3: Grey oxide (defect) rolled into surface of bar. nation of rutile ore (TiO2). Chlorine gas and coke are combined with the rutile and react to form tita- Fig. 3 shows a defect on a rolled tita- nium tetrachloride. This is purified by nium bar, grey oxide has been rolled distillation and then reduced with into the surface. magnesium to titanium sponge and Fig. 6: Hip implant with CaP-coating magnesium chloride. Secondary fabrication for produc- ing parts from mill products includes material for the chemical, medical and 2. This titanium sponge is then crushed manufacturing processes such as die food industry, and for ocean research into grainy powder, mixed with scrap forging, extrusion, hot and cold forming and development. With its passive oxide and/or alloying metals such as vana- etc. Hot forming of titanium is not only film it has a high corrosion resistance dium, aluminium, molybdenum, tin and a shaping procedure, but a method to against salt solutions, nitric acid solu- zirconium, and melted in a vacuum arc produce and control the microstructure. tions, seawater, body fluids, fruit and reduction furnace to produce titanium vegetable juices. Typical products are ingots. The high strength/low density of tita- reaction vessels, heat exchangers, nium make it a crucial material in the valves, and pumps; prosthetic devices 3. These ingots from the first melt are aerospace industry. Its main gas turbine such as implants, artificial bones, artifi- then used in a second melt as consum- engine applications include compressor cial heart pumps and valve parts. able electrodes. This process is called rings, discs, and spacer casings, ducts The most widely used alloy for these “double consumable-electrode vacuum and shrouds. In aeroplane structural products is Ti-6Al-4V. melting process”. For very pure and frames, titanium alloys are used in under clean titanium with very homogenous carriage parts, engine mountings, and Its light weight combined with aesthetic structures, an additional third melt can control mechanism parts, sheet and fas- design has made it a favorite for high be carried out. teners for outer body construction. class consumer goods such as jewel- lery, golf clubs, eyeglasses, bikes and In a first fabrication step, the cast in- Titanium’s superior corrosion resistance watches, and in architecture it is used gots, either cylindrical and 15 metric and biocompatibility make it an ideal for decorative façades (Fig. 4) tons, or square and 10 metric tons, are hot forged into general mill products such as smaller billets, slabs, bar and plate. As cast ingots can have an inher- ent coarse microstructure, which makes them sensitive to cracking, close tem- perature and process control are main- tained during forging operation. The finished products consist of forg- ings for aerospace applications as well as slab, bar, and other feedstock for further processing into bar, rod, wire, sheet or plate. Fig. 4: Entrance Experience Music Project, Seattle. Difficulties in the Preparation Method preparation of Grinding titanium Step PG FG Surface MD-Mezzo MD-Largo Type Diamond Diamond Abrasive Size #220 9 μm Suspension/ Water DiaPro The main problem of preparing titanium The first step is a plane Lubricant Allegro/Largo 9 for microscopic observation is its high grinding with resin bonded ductility, which makes titanium difficult diamonds in a rigid disc. rpm 300 150 to cut, grind and polish. In the follo- Plane grinding is followed wing recommendations, specific advice by a single fine grinding Force [N]/ 40*** 30 is given on how to overcome this typical step on a hard surface such specimen behavior of titanium. as MD-Largo or MD-Plan. As abrasive 9 µm diamond Time (min) Until Plane 5 Recommendations for the suspension DiaPro Allegro/ preparation of titanium and Largo 9 or DiaPro Plan 9 is used. Polishing its alloys Pure titanium should always Step OP Cutting: Due to its high ductility, titanium be ground using silicon car- produces long chips when machined or bide foil for plane grinding, Surface MD-Chem cut, which makes metallographic cutting see table 2. with regular aluminium oxide cut-off Type Collodial Silica wheels very ineffective. Heat damage can Abrasive The third and final step Size 0.04 μm occur easily (see Fig.1) and there- for titanium alloys is a fore silicon carbide cut-off wheels Suspension/ OP-S* chemical-mechanical Lubricant have been developed specifically polishing with a mixture of for sectioning of titanium (e.g. colloidal silica (OP-S) and rpm 150 20S30 and 20S35). hydrogen peroxide (30%). Cutting titanium also generates The concentration can vary Force [N]/ 30 a characteristic smell that can become between 10-30%. specimen pronounced when cutting large pieces Time (min) 5** or quantities. In these cases, it is recom- Unlike some other colloidal mended to connect a fume extraction to silica, OP-S was developed Table 1 shows a general, automatic preparation method for titanium alloys with grade 5 or the cut-off machine. to accommodate chemical higher unmounted samples, 30 mm dia. Please be aware that the polishing time can vary additions without transform- depending on the purity of the titanium and the area of the sample surface. Mounting: In primary production control ing into a gel-like consist- * Mix 90% OP-S with 10-30% H2O2 (30%). ** The polishing time depends on the sample area. Very large samples require more labs, which check mainly ingots, billets ency, and is therefore well polishing time than small ones. and slabs, large samples of titanium are suited for polishing titanium *** Decrease to 25 N to avoid pencil shapes in single sample preparation of mounted samples. metallographically processed and titanium alloys. During Note: during the last 20-30 seconds of the preparation step with OP-S, the rotating cloth is unmounted. For smaller manu- chemical-mechanical polish- flushed with water. This will clean the samples, holder and cloth. factured parts that need to be ing, the reaction product of mounted, such as wires or fas- the hydrogen peroxide with These reagents may work faster, how- teners, hot compression mount- titanium is continuously ever, Struers does not recommend to ing with phenolic resin (Multi- removed from the sample surface with use them for polishing, because they are Fast) or cold mounting with slow curing the silica suspension and leaves the more corrosive than hydrogen peroxide epoxy (EpoFix) are recommended. surface free of mechanical deformation. and proper precautions have to be ob- References in the relevant literature also served when handling these acids in the Grinding and polishing: Its extreme mention nitric and hydrofluoric acid mix- polishing procedure. When working with ductility makes titanium prone to me- tures for chemical-mechanical polishing hydrogen peroxide it is recommended to chanical deformation and scratching, of titanium. wear rubber gloves. which necessitates a chemical- mechanical polish. The three-step, If this chemical-mechanical polish is not automatic method described in Table 1 used, the surface of the titanium sample is a proven procedure, which gives will exhibit a very scratched appearance, excellent, reproducible results for tita- and it is almost impossible to achieve a nium alloys. good polish with diamond only. Preparation Method Grinding Step PG FG Step PG FG OP Surface Foil/Paper MD-Largo MD-Chem Type SiC Diamond Collodial Silica Abrasive Fig. 7: Titanium after 3 µm diamond polish, Size #320 9 μm 0.04 μm deformation and scratches are not removed. Suspension/ Water DiaPro OP-S* Contrary to the usual procedure of using Lubricant Allegro/Largo 9 finer and finer diamond for polishing, diamond polishing actually introduces rpm 300 150 150 continuously mechanical deformation which leaves scratches and smearing Force [N]/ 15 20 20 on the surface (see Fig.
Details
-
File Typepdf
-
Upload Time-
-
Content LanguagesEnglish
-
Upload UserAnonymous/Not logged-in
-
File Pages6 Page
-
File Size-