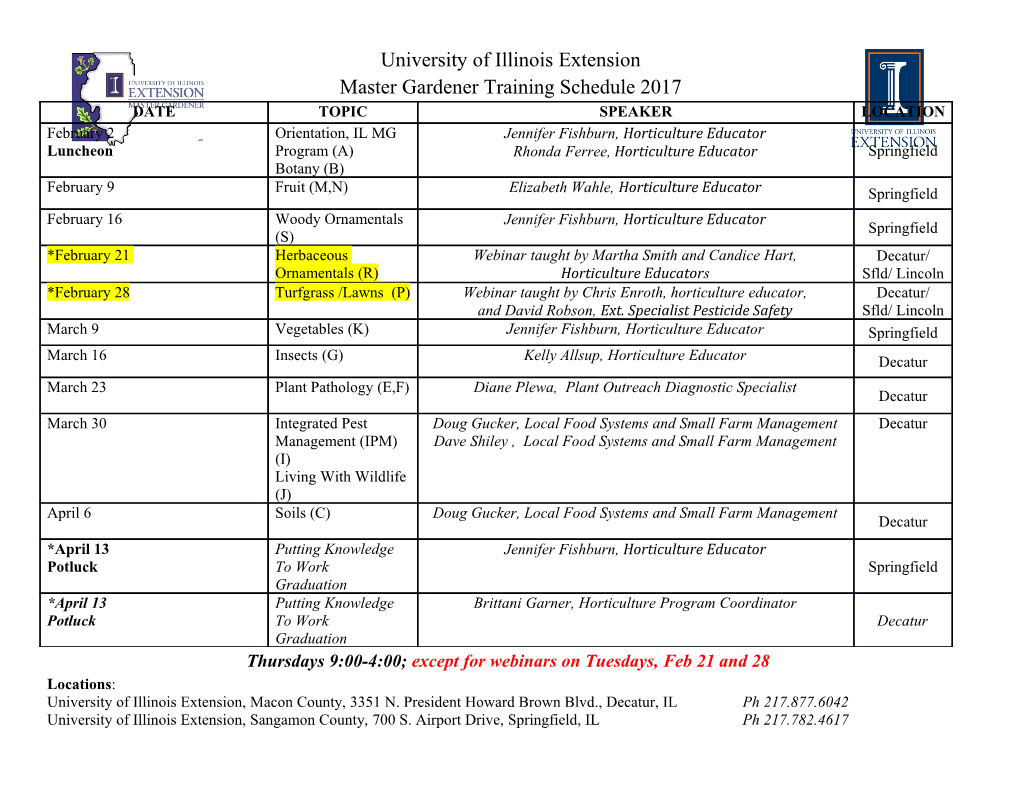
Materials Express 2158-5849/2018/8/245/009 Copyright © 2018 by American Scientific Publishers All rights reserved. doi:10.1166/mex.2018.1434 Printed in the United States of America www.aspbs.com/mex Study on diffusion model and corrosion performance of nanocrystalline Fe–Ni alloy Wei Lan∗, Shuai Zhao, and Wen Zhou School of Metallurgy and Materials Engineering, Chongqing University Science and Technology, Chongqing 401331, China ABSTRACT Nanocrystalline Fe was obtained from the surface of low carbon steel by shot peening technology and nanocrys- talline Fe–Ni alloy was obtained from the surface by electroplating nickel. A series of diffusion layers of nanocrys- talline Fe–Ni alloy were prepared by controlling the temperature during heat treatment. The micro-morphology and interface composition was observed by scanning electron microscopy and X-ray diffraction. The nanocrys- Article talline Fe–Ni alloy corrosion resistance was evaluated by electrochemical workstation. The results show that with the increase of shot peeningIP: 192.168.39.210 time, the iron On: grain Mon, size 27 decreased,Sep 2021 07:01:00 the smallest grain size reached was 256 nm. According to the analysisCopyright: of error function, American the Scientific inter-diffusion Publishers coefficient of Fe–Ni alloy increases with Delivered by Ingenta increasing diffusion temperature. When heat treatment temperature reaches 923 K, the diffusion layer thickness is 18.59 m, the diffusion coefficient of Ni in Fe is 9.36 × 10−16 m2/s. The diffusion model of nanocrystalline Fe–Ni plating layer is obtained by the Boltzmann-Matano method. It is found that the corrosion potential and the corrosion current density at a temperature of 923 K are −0.4379 V and 2.145 × 10−6 A/m2, respectively, and the corrosion resistance of the plating increases with increasing temperature. Keywords: Nanocrystalline, Fe–Ni Alloy, Diffusion Coefficient, Boltzmann-Matano Method, Electrochemistry, Corrosion. 1. INTRODUCTION resistance, and high temperature oxidation resistance, and The preparation of nano-particles has attracted increasing is thus widely used in manufacturing. 4 attention due to their unique physical and chemical prop- There are multiple ways to prepare nanocrystalline erties. Nano iron, cobalt, nickel and its alloys are widely alloys. Valderrunten 5 used high-energy milling and used in national defense, medicine, metallurgy, electron- nanotechnology methods of preparation that allowed ics, chemical environmental protection, and other fields.1 powdered samples with different structures and novel This interest is especially so in the field of oil exploita- properties to be obtained. Some experts have adopted a tion, as deep well development leads to a rise in temper- mechanical treatment method, which makes the surface of ature and pressure, and increased CO2,H2S, and chloride the material plastically deformed so that grain refinement 2 ion concentrations. In humid H2SandCO2 environments, is achieved. These mechanical treatment methods include metal materials can suffer severe corrosion, resulting in dif- ultrasonic mechanical vibration technology, ultrasonic shot ferent types of corrosion in different parts of the downhole peening technology, mechanical grinding, surface rolling, casing. To prevent accidents due to this corrosion, corrosion and laser peening. 6 7 The Chinese Academy of Sciences resistant metals are needed.3 Nickel-based alloys have Luke research group used the surface mechanical grind- excellent resistance to erosion, wear resistance, corrosion ing method, in a variety of engineering materials carried out in-depth surface from the nano-research, such as pure ∗Author to whom correspondence should be addressed. iron, 316 L stainless steel, aluminum, titanium, low carbon Email: [email protected] steel, copper among other studies. 8–11 Mater. Express, Vol. 8, No. 3, 2018 245 Materials Express Study on diffusion model and corrosion performance of nanocrystalline Fe–Ni alloy Lan et al. Ni-based alloying of low-carbon steel is achieved 2.3. Heat Treatment through surface alloying. According to reports in the lit- According to the Fe–Ni two-phase diagram, three kinds erature, the current method of surface alloying of metallic of temperature 723 K, 823 K and 923 K were selected. materials adopts surface metallurgy methods. That is, by This experiment chose a box resistance furnace. The sam- using high density energy on the surface of the material, ple was heated in the box type resistance furnace to the the surface layer melts, and the alloy is made in the molten temperature specified in the experiment, the sample kept pool. Sergey Zherebtsov produced a new alloy. The alloy- in the box type resistance furnace for 10 h, and finally ing was produced by melting pre-deposited Al–Si pow- cooled with the furnace. der and a portion of underlying substrate with a pulsed Nd:YAG laser beam. The microhardness of the modi- 2.4. Electrochemical fied layer was found to be 2.5 times higher than that of Electrochemical tests were carried out in a conventional untreated steel. The erosion test of the laser alloyed surface three electrode system using a PARSTAT P4000 elec- and steel in mercury was carried out by using an electro- trochemical workstation. Experiments were conducted at magnetic impact testing machine. The laser alloyed surface ambient temperature (293 ± 2 K), and at atmospheric was found to be less damaged after 105 cycles of impacts pressure. For the room temperature electrochemical mea- compared to untreated stainless steel. 12 Rotshtein chose surements, a conventional three-electrode configuration Cu to sputter onto a 316 stainless steel substrate to form a including a KCl-saturated Ag/AgCl reference electrode layer of Cu film in the microwave discharge of the plasma (200 mV SHE) and one Pt counter electrode were used. environment, they used low energy (20–30 keV) and high For each test a new specimen and freshly prepared test current pulsed electron beam (2–3 s, 2.8–8.4 J/cm) on solutions were used. L-shaped specimens with a measur- the Cu film and matrix metal system melting and alloying ing surface of ca. 100 mm2 were cut by wire electri- treatment, surface formed in a 120–170 m alloy diffusion cal discharge machining from bars along the longitudinal layer. 13 Reference [14] demonstrated that there is a tran- plane. Prior to the electrochemical tests, the surface of the sition layer between the nano-layer on the surface and the samples was treated by mechanical grinding consecutively coarse grain region inside. There are some surface treat- with SiC emery papers up to 360 grit prior to each exper- ment techniques, such as plasma arc welding, 15 thermal iment. The open circuit potential (OCP) and polarization spraying,16 laser cladding17–19IP:among 192.168.39.210 others, which On: have Mon,curves 27 Sep for 2021 the 07:01:00 specimens were measured in 3.5% NaCl Copyright: American Scientific Publishers been widely used in the preparation of nickel-basedDelivered alloy by Ingentasolution (pH 6.7, open to air). After immersion in the solu- coatings to improve the performance of the metal matrix. tion for 1 hour, the polarization curves were obtained by In this paper, we used shot peening to prepare micro- scanning the potential from −0.25 V versus the OCP to Article nanocrystalline iron on the surface of low carbon steel. 0.25 V versus the OCP for every specimen and sweep rate After the shot peening, nickel electroplating is performed of 0.167 mV/s. on the surface of nanocrystalline iron, and micro-nano iron-nickel alloy materials were obtained. The influence of 2.5. Neutral Salt Spray Test different temperatures on the diffusion behavior and corro- Neutral salt spray tests were carried out in salt spray test sion resistance of the nanometer Fe–Ni alloy plating layer chamber. The laboratory ambient temperature is 296±2K. was investigated. XRD and SEM were used to analyze The temperature in the test chamber is 309 ± 0.1∼0.7 K. the phase and morphology of the nanometer Fe–Ni alloy The concentration of saline solution is (5±1)% NaCl solu- plated layer, and the corrosion resistance was evaluated by tion. Settling salt solution pH is 6.5–7.2. The sample is electrochemical workstation. placed at an angle of 30 from the vertical plane. The spray method is continuous spray. The spray time is 24 hours. 2. EXPERIMENTAL DETAILS 2.1. Shot Peening 3. RESULTS AND DISCUSSION We used shot peening to prepare nanocrystalline iron on 3.1. X-ray Diffraction the surface of low carbon steel. The experiment was car- 3.1.1. Effect of Shot Time ried out on a shot blasting machine, the constant pressure Figure 1 shows the XRD spectra of different shot peen- was 0.3 MPa, steel ball size was 0.3 mm, and the shot ing times for nanocrystalline Fe–Ni alloys. It can be seen peening times were 5 min, 10 min and 15 min. that the diffraction peak has shifted to a small angle as the shot peening time increases. As can be seen in Figure 1(b), 2.2. X-ray Diffraction for samples that have not been shot peened, the span of The X-ray diffraction experiments used the DX-2700 the strongest peak is 0.6, while when the shot peening instrument and the diffraction used Cu K radiation. The time is 5 min, the span of the strongest peak is 1.3.The tube voltage was 35 kV, the tube current was 25 mA, the experimental results show that the grain size of the sam- scanning mode is step-by-step scanning, the step width is ple becomes smaller with the increase of shot peening 0.05, step time is 1 sec, and the diffraction angle is 30–90. time. 246 Mater. Express, Vol.
Details
-
File Typepdf
-
Upload Time-
-
Content LanguagesEnglish
-
Upload UserAnonymous/Not logged-in
-
File Pages9 Page
-
File Size-