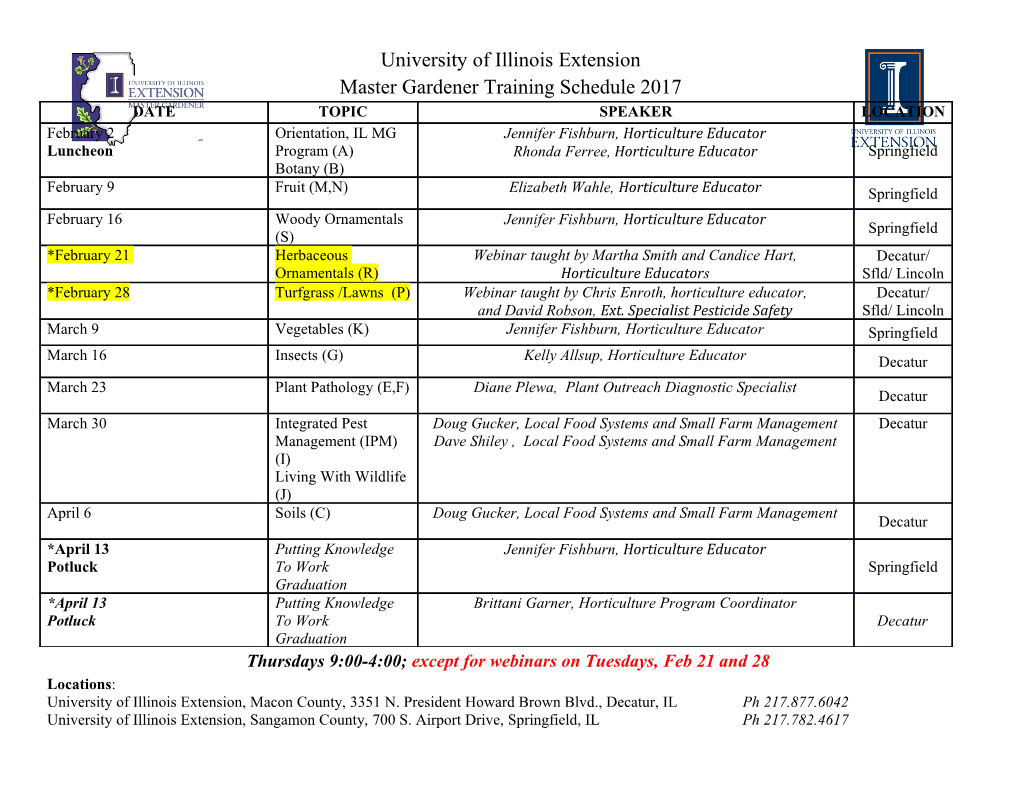
This manualis for CHAMPION FIRE PUMP: PumPNumber Model RECOMMENDEDPERFORMANCE: PumPPressure Method of Pump CaPacitY Operation GPM PSI. - DESCRIPTION: series-parallel, Type S & SE fire pump is a high speed,two.stage centrifugal PUfrP, The or in parallel with the designedto operati *itr, itr i*o i.p.ttrtsltt a'srties as a two-stagePumP, characteristicsof a single stagepump' pressuresor lower engine The pump is operated in seriesat restricted capacitiesfor higher at lower pressures' .pr.ai p-u;llif op.-tulion is employed for maximum capacities the capacity reducedby one- If a two-stagepump operating in parallel is-switched to series; pressurewill be doubled' half and the engine-rp.Ja kept thJsame, then the output first two stagesare identical The Type sH & SEH fire pump is a three-stagepump i1.1tri9!r the it to operatesimultaneously to the Type S. The third stagehas a tlp"iurrrlutitr geaiwhich allows as a two-stage' with the iirst two stages,or stand idle while the pump runs pressuresrequired for fog with the three stagesoperating in seriesat low volume, very high streamsare delivered. underwriter requirements, The two-stageunit of this pump will gen^erallydeliver class A third stage' while simultaneourfy-Iai*tittg ttigtt pressuiefog streamsfrom the page' External featuresof this pump are illustrated on the next l7oooll "' TYPE SE & SEH FIRE tsUMP 11 L2 I 1 2 2 3 L3 5 4 L4 5 15 6 16 2L L7 7 23 18 10 22 7 1 Discharge Gate Valves L5 Third Stage Outlet 2 Drain Valves 16 Discharge Pressure Tap 3 Pressure Relief Valve L7 Suction Screen - Third Stage 4 Re1ief Valve Shutoff 18 Purrp Drain Valve 5 Suction Inlet 19 Pump Power Shift 6 Exhaust Heater Connection 20 Tachometer Drive 7 Packing Gland Adjustment Screw I Booster Discharge Outlets LUBRICATION POII,ITS 9 Booster Suction Inlets 10 Third Stage Power Shift 2L Impeller Shaft Grease Zerk L1 Double FLoat Primer Assembly 22 Transmission Oil Level- Plug L2 Discharge Check Valve 23 Rear Drive Shaft Grease Zerk L3 Staging Control Valve 24 Transmission Case Oil FiII Plug L4 Cooling Line Strainer sE-2 1{1 lSut;p1t W.S. DARLEY & CO. REPAIR SERVICE INSTRUCTIONS TYPE SESOO/SE75O/SEIOOOMIDSHIP FIRE PTJMPS Type SE T9ship fire pumpsare assembledin two main sectionswhich separateon a horizontalplane at the top of the pump casing. The lower section of the assembly(comprising all moving parts of the pump and transmission)can be unbolted from the upper sectionand lowered for removaland repair. It is not necessaryto removethe uppersection of the pumpassembly from the truck chassisor to disturb the manifold, valves,piping, accessoriesor body deails whenonly the pumpand transmission need repair or overhaul. TO REN,IOVE PTJMP CASING AND TRANSMISSION OI\ILY FROM TRUCK CHASSIS Refer to Drawing 5825 l. Disconnectcasing drain valverod, coppertubing lines, clutch shift rod, brakelever rod or cable, tachometerdrive cable, and removedrain valve. 2. Disassembleuniversal joint at front of pumpby removingcap screwsto freeone yoke, and remove drive shaft betweenpump and truck transmission. 3. Disassembleuniversal joint at rear of pump to free propellerdrive shaft. 4. Placeblocking of floor jacks undei both pump casingand transmissioncase to supportits weight. 5. Removetop support stud nuts from cross membersat front and rear of pump. 6. U"lglt pump cqgingfrom manifoldb.y rgmoving sixteen V2"NC nutsunderneath the pump casing and dischargeelbow flange,one l/2"NC nut undermiddle of dischargeelbow, and three-l/2"Ne nuts on top side of manifold on drivers side. 7. Tapnedholes for jack screwsare provided in pumpcasing flange to facilitateseparation of gasket joint. $e 8. Alwayskeep casing flange parallel with bottomof manifoldwhile separatingto avoidinterference. 9. Lower pumpand transmissionassembly to the floor and slideout from underthe truck. Truck may haveto be jacked up for clearance. TO REMOVE COMPLETE SE PTJMPFROM TRUCK CHASSIS Refer to Drawing 5825 l. Disconnectthe following from the pump: Suctionand dischargebooster piping Heaterpiping Gageline tubing Primer tubing Relief valve or pressureregulator tubing Auxiliary cooler tubing Drain valve and extensionrod Clutch shift rod Thchometerdrive cable Dischargevalve operating linkage Control valveoperating rod Brake lever control rod or cable 2. Separateuniversal joint at truck transmissionand removejack shaft. leeaTl 3. Separateuniversal joint at rear of pump and drop propeller shaft. 4. Removetop support stud nuts from cross membersat front and rear of pump. 5. Block up underpump and transmissioncases to supportis weight. 6. Unbolt dischargeextensions (113) from dischargehead (lCI) and pull out throughopenings in body panels. 7. Unbolt suctionextensions (D0) and (109)from pump manifold(52). Loosenset screwsin suction extensionsupport bracketsand pull out through body panels. 8. Lift pump out of chassiscarefully with hoist of not less than t/z ton capacity. PT]MP DISASSEII,IBLYFOR OVERHATJL Refer to Drawings 5972 and 5825 l. Setpump and transmissionassembly on a benchwith bottom side up. REAR DRTVE SHAFT DISA^SSEMBLY If disassemblyof rear drive shaftis not required,complete steps lQ ll, and D to removerear drive shaft assemblyfrom pump. 2. Cut and removesafety wire from brake drum Qq. Removesix 3/8"NF cap screwsand remove brake drum from brake drum flange Qls). 3. Removecotter keys from clevis pins (208) and removeclevis pins from yoke ends (210)and (2ll). 4. Removecotter key from bell crank pin QA|) and slide washerQl7) andbell crank Ql3) otr of bell crankpin. 5. Pry tabof lock washer(218) out of groovein lock nut (214).Remove lock nut andlock washer-from rear drive shaft (48). 6. Slide brakedrum flange Qls) off of rear drive shaft (48). 7. Removefour U2"NC capscrews and remove mechanical brake assembly (216) from brakeyoke (50) and removebrake lever (209). 8. Removefour 3/8"NC cap screwsand removebrake yoke (50). 9. Pressbrake drum oil seal (22) out of brake yoke (50). 10. Removetwelve 1/4"NC Fillister headcap screwsand removetransmission case cover (45). ll. Loosensix 3/8"NC capscrews holding transmission bearing cap (39) to allow removalof rearbear- ing bracket(49). 12. Removetwo 3/8"NC capscrews holding bearing bracket (49) to pumpcasing (l). Removefour 3/8"NC capscrews holding bearing bracket to transmissioncase 09). A 9116"stafter wrench with a curved handle,such as Duro Chrome#2081, is necessaryfor two of thecap screws. Slide the bearing bracket to the rear and awayfrom the transmissioncase. 13. Pressrear drive shaft(48) out of rear bearingbracket (49). Removebearing backup washer (226) and presstransmission shaft bearing (47) ott of rear drive shaft. 14. Tapoil seals(205) and (219)out of rear bearingbracket (49). nnu89 l)uazt CLUSTER GEAR DISASSEMBLY If disassemblyof clustergear is not required,complete step 15 to removecluster gearltransmission shaft assemblyfrom transmissioncase. 15. Removesix 3/8"NC cap screwsfrom transmissionbearing cap (39). Slidetransmission shafl/drive gear assemblyout of transmissioncase (D). 16. Slide bearingcap (39) off of bearing(38). Pressoil seal(37) out of bearingcap. n. Bump pilot bearing(51) off of transmissionshaft (35) with sliding clutch gearQ9).. 18. Removesix l/4"NC graqe8 cap screwsholding pump clutch gear(31), transmission drive ge,ar(162), and bearing retainer (25) together. 19. Pressor tap transmissionshaft (35) out of pump clutch gear (31)and transmissiondrive gear(162). 20. Pressrear bearing(203) otr of transmissionshaft (35). 21. Pressfiont bearing QO3),bearing retainer (25), bearingspacer (87), and bearing(38) offof transmis- sion shaft (35) together. 22. It may not be necessaryto removeclutch shift bar (33) and shift yoke (30) from transmissioncase. (19).To disassemble:Remove four retainingrings (223) from clutchshift bar (33). Slideshift yoke (30) off of shift bar and slide shift bar out of transmissioncase (19). NOTE: Models after July 1988have a lock bolt shift yoke. Cut safetywire and removelock bolt (227) to removeshift yoke from shift bar. PIJMP DISASSEIVIBLY 23. Removetwelve. 1/2"NC heavynuts from studsand removeoutboard head (8) with outboardstuffing box (174),bearing cap(177), bearing (176), bearing cap cover (173), and waterslinger Q24) attachd. Tlvo 5/l6"NC tappedholes in flangewith facilitate separation.Maintain headsquare with impeller shaft during removal to avoid damageto parts. 24. Removefour 1/4"NC caq scrervsand removeoutboard bearing cap cover(173) and bearing cap (lZ7) with bearing (176).Tap bearing out of bearing cap. 25. Make alignmentmar}s on the outboardstuffing box (174)and the outboardhead (8) with a cent€r punchor a cold chisel. 26. Removetwo 5/l6"NC cap screwsand removepacking plunger guide (163)from outboardstuffing box (174). n. Removesix l/4"NC slotted flat head brassmachine rrrri, and removeoutboard head (8). 28. Removecotter key (4), impellernut (5), andimpeller washer (6) from pumpshaft (18). Place a hard- wood block againstpinion gear (20) to preventshaft from rotating. 29. Pull secondstage impeller (3) off of pumpshaft (18). T\r,o 1/4"NC tapped holes are provided in back of impellerfor puller bar studs.Use a heavy,flat puller bar with two 9132"clearance holes l-ll2" apart and a 3/8"NC tappedhole in centerfor shaftdrive bolt. 30. Removesix 1/2"NC heavynuts and two 1/2."NCjam nuts from inboardhead (12) and separatepump c-asing(l)from inboardhead. TWo 5/16"NC apped holes in flangewill facilitateseparation. Support the weightof transmissioncase (19) and head and keep it squarewith casingbore while separating theseparts. 31. Pry first stageimpeller (11)off of pumpshaft (18) using a pair of flat barsbetween back of impeller and headat oppositeslides. Bear againstimpeller wherevanes provide support. Inspectseal rings (10),and impellers(3) and (11).(See PARIS INSPECTIONAND MEASURE- MENT.) If sealrings (10)are not worn, removalis not necessary.If removalis necessarycontinue with steps33 and 34. 33. Removefour l/4"NC slottedflat headbrass machine screws and removeseal rings (10) from pump casing(l). 3 Aw-c:LL 34. Removefour l/4"NC slottedflat headbrass machine screws and removeintersage seal ring (2) from pump casing(1). 35. It shouldnot be necessaryto removeinboard head (12) from transmissioncase (19). These pans are held togetherwith two 3/8"NC cap screwsand four 1/2"NC cap screws.
Details
-
File Typepdf
-
Upload Time-
-
Content LanguagesEnglish
-
Upload UserAnonymous/Not logged-in
-
File Pages48 Page
-
File Size-