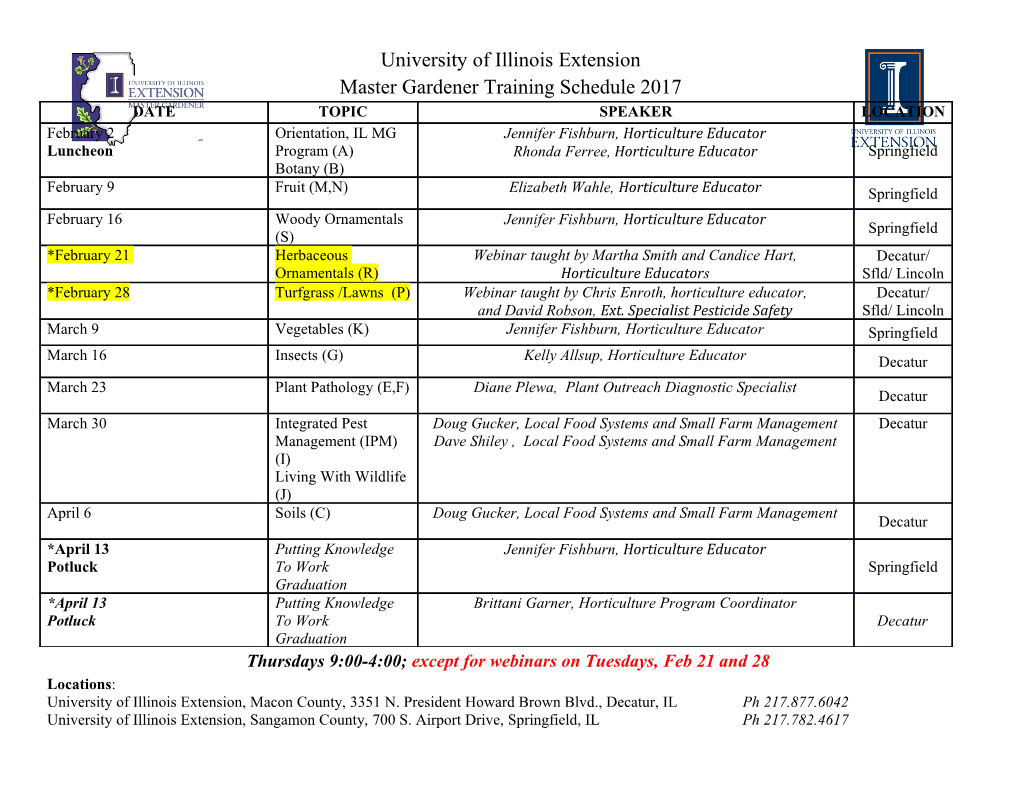
MAKATOTE VIADUCT – UNDERPINNING PIER 7 CHALLENGING NATURE WITH A COLLABORATIVE APPROACH Peter Wissel1, Alastair Blackler2, Walter Rushbrook3, Matthew Callaghan4 INTRODUCTION Located between Ohakune and National Park, the Makatote Viaduct is the third highest railway viaduct in New Zealand. Land instability and erosion resulted in Pier 7 of the Makatote Viaduct being vulnerable to foundation failure and was identified as the greatest risk to any of the structures on the New Zealand Railway Network by its owner ONTRACK. A project was put together by ONTRACK to underpin the vulnerable foundations. The project team faced demanding constraints and difficulties that had to be overcome to ensure a successful outcome of the project. The construction was effectively undertaken inside a National Park with numerous environmental challenges including undertaking construction in a rare blue duck habitat and in a pristine trout spawning stream. Most critically, there was a possibility that the construction activities may in themselves destabilise the viaduct. ONTRACK, Fulton Hogan Civil Ltd and specialist engineering consultants worked collaboratively based on a no-blame and best for project approach to successfully complete the $4.2M project between May 2006 and February 2007. This paper provides an overview of the challenging work to underpin the eroded pier foundation in difficult topography and during extreme weather conditions. HISTORY It is the combination of this exposure, continued lowering of the bed level due to scour, unknown lateral soil pressure on the upstream footing, risk of further embankment erosion at the downstream footing and the potential for the volcanic ash layer to slip against the footings that raised the stability of Pier 7 to the highest priority requiring remedial action by ONTRACK Structures Engineering. DESIGN Several options were considered during the scope and conceptual phase of the project such as: The placing of rock rip rap protection at the toe of the upstream footing to prevent further scour [1] Makatote Viaduct being tested in 1908 and installation of soil nails / rock bolts along the face of the embankment. Completed on 10 July 1908 by company J. and A. The construction of a concrete retaining wall Anderson and Co. for the sum of ₤53,369, the utilising soldier piles and ground anchors which Makatote Viaduct is the third highest railway would protect the toe of the footings and viaduct in New Zealand with a total height of prevent further attack to the embankment from 78.6m. As part of the North Island Main Trunk Line the river (NIMT) the viaduct serves as a vital link between The underpinning of the two front footings by Wellington and Auckland. installing a large pile at each footing and spanning a large cross beam between piles to Regular rainfalls and seasonal melting water from support the lattice tower legs and relieve load Mt. Ruhapehu eroded the river banks and exposed on the existing footings the toe of the upstream mass concrete footing of Pier 7. The last option was considered to be the most acceptable form of construction to meet Resource Consent conditions, provided an acceptable 1 Peter Wissel, Regional Manager, Fulton Hogan Civil Ltd 2 Alastair Blackler, Project Manager, Fulton Hogan Civil Ltd 3 Walter Rushbrook, Manager Structures Engineering, ONTRACK 4 Matthew Callaghan, Director, Novare Design Ltd reduction of risk to ensure ongoing operation of the and recognised as adjustments (plus/minus) to the Viaduct and was cost effective in comparison to TOC. the other options. In order to drive ONTRACK’s key objectives for the The proposed underpinning structure consists of contract a performance incentive was established, two 2m diameter bored concrete piles constructed which solely focused on safety, program, to a depth of 38m below beam soffit level. The environmental compliance and quality. Only piles were spanned by a post-tensioned cast-in- exceptional performance of the contractor was situ bone-shaped concrete beam 37m long, 1.5m meant to be rewarded with no incentive for wide and 3m deep. The horizontal loads are business as usual performance. transferred through three steel struts from the concrete cross beam to six ground anchors, which were installed in pairs of two and connected with a ENVIRONMENT pre-cast concrete tie beam. A major focus of the contract was the minimisation of environmental impacts and therefore all work was planned and executed with close co- ordination between ONTRACK, Fulton Hogan Civil Ltd, Horizon Regional Council (HRC), the Department of Conservation (DOC) and Fish and Game. The Makatote River is protected by a National Water Conservation Order. The Order protects the river’s outstanding wild and scenic characteristics, the outstanding qualities provided by the gorge and riparian margins, the unique wildlife habitat for the blue duck (whio), and the outstanding recreational trout fishery. The construction had to be programmed around the breeding season of the endangered whio and the trout spawning season. Final design of structure Besides continuous monitoring of water quality the construction team developed together with DOC a detailed monitoring program of the whio pairs in CONTRACT particular during the breeding and hatching season. The basis of the contract document was NZS 3915 with no appointed Engineer to the Contract. Due to the significant construction risks including ground CONSTRUCTION conditions, weather, topography, environmental considerations and the requirement to keep the Temporary Work viaduct fully operational at all stages of the construction a simple Alliance Agreement acted as Access to the construction site was gained in May an umbrella over the standard NZS 3915 contract. 2006 from an existing track constructed in the This proved to be enormously successful as it 1980s on the southern side of the gorge. The meant that ONTRACK, Fulton Hogan Civil Ltd and track was covered in thick scrub and had washed the expert advisors could literally act as one team out in several places and required widening along to address and successfully resolve engineering the length of the track to allow access for and construction issues. The simplicity of the construction equipment, in particular the crawler Alliance Agreement meant that administration cranes, to the bottom of the gorge. The installation costs from this process were low and a lot of value of sediment control measures like cut-off drains, was gained from the close working relationship sediment ponds and hay bale barriers was carried between the principal, consultants and contractor. out in parallel to the earthworks associated with the access track. Following a registration of interest, Fulton Hogan Civil Ltd was invited by ONTRACK to develop, together with ONTRACK, the best suited construction technique, program, risk register and finally the Target Outturn Costs (TOC). Any deviations from the original contract scope had to be agreed between the parties as scope changes proposed ground investigation included two 40m deep boreholes holes at each pile location and three 12m deep boreholes at each ground anchor set, with cores recovered and SPTs carried out every 1.5m. The downstream pile borehole was the first borehole to be drilled. Andesite boulders and gravels cemented in a sand matrix were generally encountered for the length of the bore. At 38m below ground level (7m below pile founding) the investigation drilling struck an aquifer. The borehole was drilled a further 13.5m to 51.5m total depth, to determine the consistency of the aquifer and to investigate artesian water pressures at lower level. From the time artesian water was encountered at 38m depth the head was measured Installation of downstream bridge consistently at 6m above ground level, equating to a pressure head of 44m. Levelled storage at the bottom of the gorge was minimal and confined within the boundaries of Immediate consultation between the designer, ONTRACK owned land. Truck and trailer access to geotechnical engineer and contractor commenced the bottom of the gorge was difficult and trailers and it was concluded to plug the borehole by had to be turned around by a crane with trucks means of grouting, ensuring that no artesian water often being towed back up the hill. Often it was would penetrate into the pile during the excavation. easier to offload plant and materials at the top of Another borehole about 5 metres to the side of the the hill and transport it in a 6 wheel drive dump pile was drilled to determine the consistency of the truck to the bottom. artesian water pressure and to install a piezometer and inclinometer to measure any changes in water Once access to the bottom of the gorge was pressure and ground stability during piling. Tilt gained, a bridge across the river and an access meters were also attached to the four existing track to Pier 7 itself had to be constructed. Thick viaduct footings of Pier 7, to monitor any rotational vegetation on the 15m high bank to Pier 7 was movement during piling operation. cleared by hand until an excavator could start with the forming of the access track to Pier 7. The The 12m ground anchor boreholes were the next ground consisted typically of a 2-3m deep layer of boreholes to be drilled with fewer surprises, though sensitive wet ash overlying the lahar boulder on the upstream anchor, all of the drill water was deposits. Springs and ground water were lost at about 9.3m depth, identifying potentially a frequently discovered during the excavation of the very porous layer or possible fissure in the road. The 120m of access track from the lower cemented lahar deposit. bridge to Pier 7 required 9 tons of cement, which was hand spread, to sufficiently stabilise the Access to the upstream pile borehole was not subgrade before the road could be used. available at the time of the initial investigation, as clearing the vegetation around the upstream footing of Pier 7 unveiled that the footprint of the Site Investigation and Geology upstream pile was part way up the 17m high river bank.
Details
-
File Typepdf
-
Upload Time-
-
Content LanguagesEnglish
-
Upload UserAnonymous/Not logged-in
-
File Pages8 Page
-
File Size-