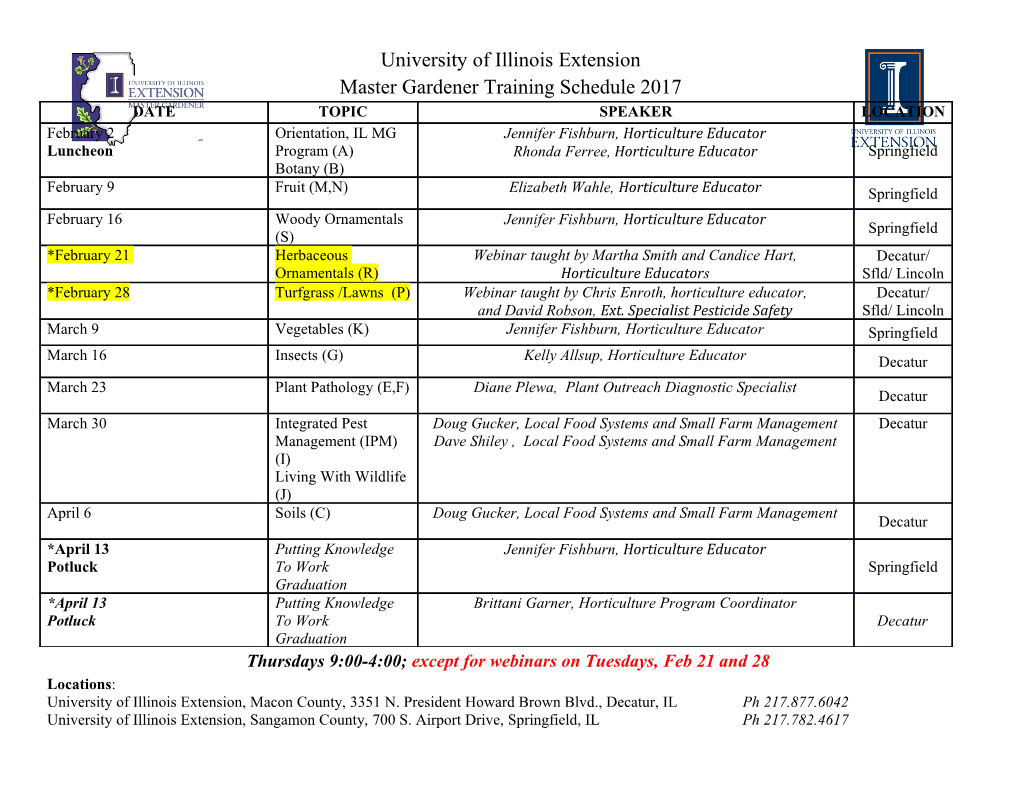
INDUSTRY GUIDE HANDLING AND ASSEMBLY TECHNOLOGY EFFICIENT APPLICATIONS SOLUTIONS HANDLING AND ASSEMBLY TECHNOLOGYSubject to change without notice TABLE OF CONTENTS 2 HANDLING AND ASSEMBLY TECHNOLOGY | SICK 8019952/2016-05-13 Subject to change without notice TABLE OF CONTENTS Challenges Challenges in handling and assembly technology 4 Applications in focus The application graphics shown are not binding, they are no substitute for the need to seek expert technical advice. Small part assembly: Example of pre-assembly involving an optics module 6 Small part assembly: Example of pre-assembly involving a housing assembly 14 Small part assembly: Example of final assembly involving a sensor 28 Products Product overview 42 Special pages We simply detect any object 118 IO-Link 120 Software Tool Sopas 122 Smart Sensor Solutions 124 4Dpro 126 Expertise in machines safety 128 Safe control solutions 130 Safety controller Flexi Soft 132 Safe networking: Flexi Line 134 Safe sensor cascade: Flexi Loop 135 Safe motion monitoring 136 Encoder and Motor feedback systems 138 General information Company 140 Industries 142 SICK LifeTime Services 144 Versatile product range for industrial automation 146 Industrial communication and device integration 150 Services 155 8019952/2016-05-13 HANDLING AND ASSEMBLY TECHNOLOGY | SICK 3 Subject to change without notice HANDLING AND ASSEMBLY TECHNOLOGYSubject to change without notice CHALLENGES Challenges in handling and assembly technology Many industries such as automotive, electronics, metal, machine tools, and medical engineering can be identified as the driving force behind handling and assembly technology. They rely heavily on automated han- dling and assembly processes that in turn contribute to streamlining high quality and accuracy and improving productivity and PSDI times. Develop- ing more intelligent machines by using a larger number of sensors leads to new applications, improved quality assurance, and even more flexible production. At an early stage, SICK recognized the trend towards imple- menting more intelligence and functionality in the field level, making its sensor technology ideal for meeting the requirements of handling and assembly applications. Monitoring and controlling Protecting Assembly processes are strongly influenced by the product Linking automated production equipment with semi-auto- and require flexibility and openness to develop and implement mated assembly cells requires intelligent and flexible safety individual processes. Reliability is an important requirement concepts. SICK safety solutions ensure the protection of oper- for each of these different processes, posing a highly chal- ating personnel, optimize production, and reduce the machine lenging task for quality control. SICK’s distance sensors, vision footprint and downtime. sensors and systems support nearly every type of monitoring. 4 HANDLING AND ASSEMBLY TECHNOLOGY | SICK 8019952/2016-05-13 8019952/2016-05-13 HANDLING AND ASSEMBLY TECHNOLOGY | SICK Subject to change without notice Subject to change without notice CHALLENGES Data management and identification Detecting and measuring Reliable identification of objects is a prerequisite for a smooth The automation of assembly and handling processes under production flow, and lays the foundations for traceability and the most stringent accuracy requirements needs high reso- continuous quality improvement. SICK offers a wide range of lution positioning systems, flexible production lines, and high both permanently installed and mobile readers for bar codes, diagnostic abilities. Modern, intelligent sensors from SICK are 2D codes, and RFID technology. able to store settings, use automatic teach-in and diagnostic capabilities, and independently evaluate and relay the sensor data in the process, thus making a significant contribution towards meeting these challenges. HANDLING AND ASSEMBLY TECHNOLOGY | SICK 8019952/2016-05-13 8019952/2016-05-13 HANDLING AND ASSEMBLY TECHNOLOGY | SICK 5 Subject to change without notice Subject to change without notice Small part assembly: Example of pre-assembly involving an optics module APPLICATIONS IN FOCUS 2 3 1 6 HANDLING AND ASSEMBLY TECHNOLOGY | SICK 8019952/2016-05-13 Subject to change without notice Small part assembly: Example of pre-assembly involving an optics module APPLICATIONS IN FOCUS Small part assembly: Example of pre-assembly involving an optics module Focus 1 8 1 Depalletizing and infeed of printed circuit boards Focus 2 10 2 Sorting and storing small parts Focus 3 12 3 Hybrid assembly system for an optics module 8019952/2016-05-13 HANDLING AND ASSEMBLY TECHNOLOGY | SICK 7 Subject to change without notice Focus 1: Depalletizing and infeed of printed circuit boards SMALL PART asseMBLY: EXAMPLE OF PRE-asseMBLY INVOLVING AN OPTICS MODULE 1 Access protection with muting on belt conveyors Tray stacks are automatically fed to the pallet handling machine using the (dual) belt conveyor. During this process, a miniTwin safety light curtain reliably secures access to the conveying line. The benefits of the miniTwin are its lack of blind zones and the various differ- ent brackets that allow quick and easy mounting. The muting function is used during the interaction between the light curtain and Flexi Soft safety controller in order to properly differentiate between people and materials. Four muting sen- sors allow flexible setup for inlet and exit monitoring. W4S-3 g p. 45 miniTwin4 g p. 78 Flexi Soft g p. 88 2 Height control for tray stacks 3 Singulation of printed 4 Advanced identification technology and printed circuit boards circuit boards Alongside the laser scanners of the A gripper arm removes the top tray from The Inspector PI50 2D vision sensor CLV62x product family, the Lector 62x the tray stack and lifts it into an interme- provides precise detection of the regis- image-based code reader also belongs diate position before the printed circuit tration marks on different printed circuit to the group of 4Dpro devices. These boards are feed to the assembly line. To boards, thereby accurately determining the devices deliver reliable reading of 1D ensure that the gripping arm grasps the position of the individual boards in the tray. and 2D codes and output the results via right part of the printed circuit board, This means that an offset in the x- and y- serial interfaces, Ethernet or CAN. The the OD Mini short-range distance sen- direction, as well as the rotational position, built-in SMART intelligent code recon- sor detects the height of the tray stack can be detected and automatically cor- struction technology identifies even using distance measurement technol- rected. As a result, the gripping system can partially covered or damaged codes. ogy. The sensor then transmits the pick the printed circuit boards and place Additional bus interfaces are also measured data to the pallet handling them on the downstream workpiece carrier optionally available via CDF connection machine control. transfer system with millimeter accuracy. modules. Lector62x g p. 99 CLV62x g p. 100 CDF600 g p. 104 OD Mini g p. 108 Inspector g p. 105 CDF600-2 g p. 104 8 HANDLING AND ASSEMBLY TECHNOLOGY | SICK 8019952/2016-05-13 Subject to change without notice Focus 1: Depalletizing and infeed of printed circuit boards SMALL PART asseMBLY: EXAMPLE OF PRE-asseMBLY INVOLVING AN OPTICS MODULE 4 3 2 5 1 6 5 Positioning tray stacks 6 Protrusion monitoring on the tray stack The tray stacks must be precisely Four W4-3 photoelectric retro-reflective thereby eliminating the need for time- positioned on the belt conveyor to allow sensors embedded in the floor check consuming signal processing. W4-3 a gripping arm to supply or remove the tray stack for protrusions and tilted photoelectric retro-reflective sensors of- trays. This task is handled by the CQ4 trays. Two additional photoelectric retro- fer impressive performance thanks to a capacitive proximity sensor. With its reflective sensors detect any workpieces light spot that is highly visible, small and small sensing range and compact form, protruding past the front or back of the precise. This feature allows the sensors the sensor can be integrated in the pallet in the direction of feed. Photoelec- to “see through” covers and gaps be- direct vicinity of the process, even where tric retro-reflective sensors with IO-Link tween belts during operation. To prevent little space is available. The capacitative are especially well suited for this task. a collision, an additional photoelectric sensor technology enables a material- Their internal microcontroller delivers proximity sensor monitors the tray stack independent and safe detection of trays, optimal processing of the detection height as the stack is moved into the no matter what object properties they sequence with maximum frequency, pallet handling machine. have. CQ4 g p. 59 W4-3 g p. 46 8019952/2016-05-13 HANDLING AND ASSEMBLY TECHNOLOGY | SICK 9 Subject to change without notice Focus 2: Sorting and storing small parts SMALL PART asseMBLY: EXAMPLE OF PRE-asseMBLY INVOLVING AN OPTICS MODULE 1 Measuring the conveying speed of a roller conveyor The conveying speed of a roller conveyor is controlled with the help of the position detection feature of a programmable incremental encoder DBS60. With its high 16-bit resolution, the encoder ensures maximum repeatability. The encoder can be easily mounted to the roller conveyor via a belt drive. SICK of- fers a large number of encoder variants to accommodate virtually any mechani- cal and electrical interface. DBS60
Details
-
File Typepdf
-
Upload Time-
-
Content LanguagesEnglish
-
Upload UserAnonymous/Not logged-in
-
File Pages156 Page
-
File Size-