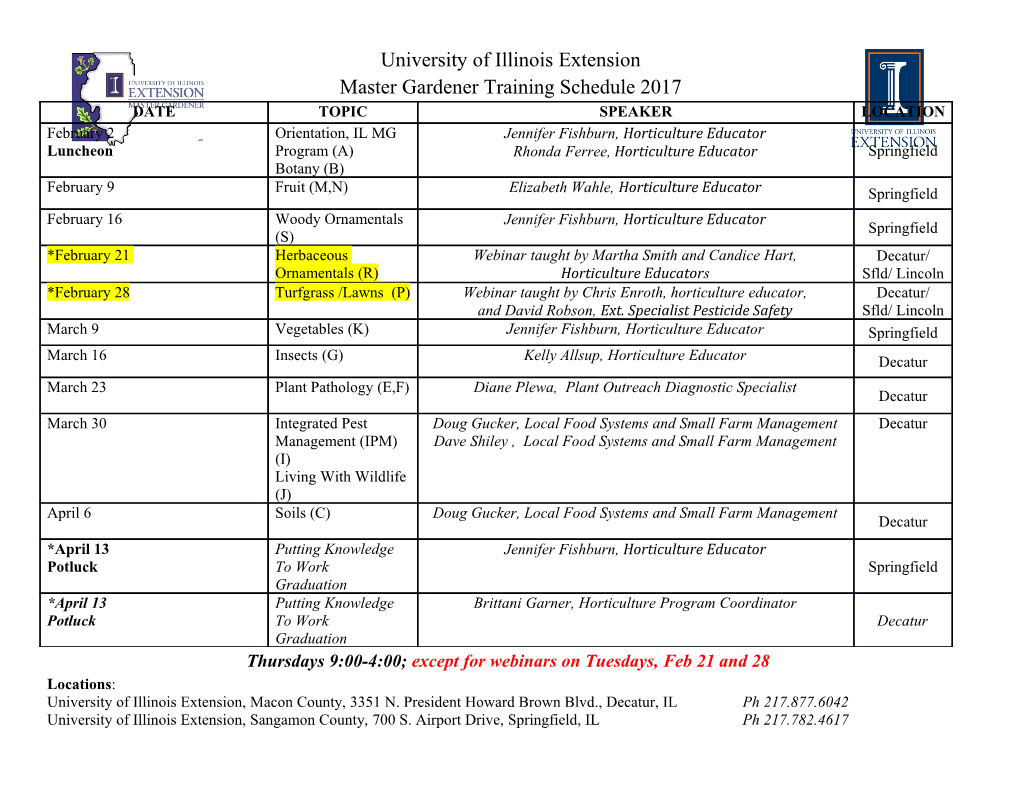
www.ijemr.net ISSN (ONLINE): 2250-0758, ISSN (PRINT): 2394-6962 Volume-5, Issue-1, February-2015 International Journal of Engineering and Management Research Page Number: 303-307 Improving Wear Resistance of Grey Cast Iron using Detonation Gun Sprayed Coatings: A Review Gobind1, Jawala Parshad2, Dr. Neel Kanth Grover3 1,2,3Department of Mechanical Engineering, S.B.S.S.T.C, Ferozepur, Punjab, INDIA ABSTRACT finely divided metallic or nonmetallic materials are Materials are precious resources. Different methods deposited in a molten or semi molten condition to form a and techniques are employed to protect the materials from coating. The coating material may be in the form of degradation. As the wear is a surface phenomenon and occurs powder, ceramic-rod, wire, or molten materials [2]. mostly at outer surfaces. Failure of mechanical components As shown in figure 1, Thermal spraying can provide due to wear is the most common and unavoidable problem in thick coatings (approx. thickness range is 20 micrometers automobiles, power generation units (hydro power plants), construction equipments, marine sector, gas and fuel to several mm, depending on the process and feedstock), pipelines and other mechanical processing industries. It not over a large area at high deposition rate as compared to only affects the life of a component but also reduces its other coating processes such performances. Therefore due to heavy economic losses as electroplating, physical and chemical vapor deposition. associated with wear, this problem has attracted the attention Coating materials available for thermal spraying include of the researchers worldwide. To overcome this problem of metals, alloys, ceramics, plastics and composites. They are wear, wear resistant alloys or suitable wear resistant coatings fed in powder or wire form, heated to a molten or semi deposited by various advanced techniques are generally used. molten state and accelerated towards substrates in the form Now a day’s Detonation gun spray coatings are gaining of micrometer-size particles. Combustion or electrical arc popularity due to exceptional hardness, wear resistance and cost effectiveness. A detonation gun spray coating is a type of discharge is usually used as the source of energy for thermal spray coating technique. In this paper, principle of thermal spraying. Resulting coatings are made by the detonation gun sprayed methods is discussed and the results accumulation of numerous sprayed particles. The surface of various previous researches done by various authors on may not heat up significantly, allowing the coating of detonation gun sprayed coatings have been reviewed. flammable substances [3]. Selection of the appropriate thermal spray method Keywords--- thermal spraying, detonation gun, grey cast typically is determined by: iron. • Desired coating material • Coating performance requirements • Economics I. INTRODUCTION • Part size and portability “Thermal spraying is a coating process in which a II. METHODOLOGY coating material is heated quickly in a hot gaseous medium to become molten or semi-molten and at the same Thermal spraying has emerged as an important time projected at high velocity onto a substrate surface to tool of increasingly sophisticated surface engineering develop a desired coating. (Hasan 2009). Thermal technology. To reduce the wear problem, wear resistant spraying techniques are coating processes in which melted coatings are deposited on the grey irons. Standard test (or heated) materials are sprayed onto a surface. The methods for wear testing with pin-on disc apparatus are "feedstock" (coating precursor) is heated by electrical employed to study the wear behavior of the uncoated and (plasma or arc) or chemical means (combustion flame) [1]. coated grey irons as well. Thermal spraying, a group of coating processes in which 303 Copyright © 2011-15. Vandana Publications. All Rights Reserved. www.ijemr.net ISSN (ONLINE): 2250-0758, ISSN (PRINT): 2394-6962 accelerate the particles to a velocity of 1200m/sec. These particles then come out of the barrel and impact the component held by the manipulator to form a coating. The high kinetic energy of the hot powder particles on impact with the substrate result in a buildup of a very dense and strong coating. The coating thickness developed on the work piece per shot depends on the ratio of combustion gases, powder particle, size carrier gas flow rate, frequency and distance between the barrel end and the substrate Depending on the required coating thickness and the type of coating material the detonation spraying cycle can be repeated at the rate of 1-10 shots per second. The chamber is finally flushed with nitrogen again to remove all the remaining “hot” powder particles from the chamber as these can otherwise detonate the explosive mixture in an irregular fashion and render the whole process uncontrollable. With this, one detonation cycle is completed above procedure is repeated at a particular frequency until the required thickness of coating is Figure 1- Thermal spray processes deposited. Thermal spray processes that have been considered to deposit the coatings are enlisted below (1) Flame spraying with a powder or wire, (2) Electric arc wire spraying, (3) Plasma spraying, (4) Spray and fuse, (5) High Velocity Oxy-fuel (HVOF) spraying, (6) Detonation Gun. Among the commercially available thermal spray thermal spray coating techniques detonation gun sprayed coatings process is popularized because it gives an extremely good adhesive strength, low porosity and coating surface with compressive residual stresses [4]. III. DETONATION GUN SPRAYING PROCESS In detonation Gun spraying Process, as shown in figure 2, A mixture of spray material, acetylene and oxygen is injected into the detonation chamber. A precisely Figure.2 Detonation Gun process measured quantity of the combustion mixture consisting of oxygen and acetylene is fed through a tubular barrel closed The chamber is finally flushed with nitrogen again to at one end. In order to prevent the possible back firing a remove all the remaining “hot” powder particles from the blanket of nitrogen gas is allowed to cover the gas inlets. chamber as these can otherwise detonate the explosive Simultaneously, a predetermined quantity of the coating mixture in an irregular fashion and render the whole powder is fed into the combustion chamber. The gas process uncontrollable. With this, one detonation cycle is mixture inside the chamber is ignited by a simple spark completed above procedure is repeated at a particular plug. The combustion of the gas mixture generates high frequency until the required thickness of coating is pressure shock waves detonation wave), which then deposited [5]. propagate through the gas stream. Depending upon the ratio of the combustion gases, the temperature of the hot gas IV. STUDIES RELATED TO stream can go up to 4000 deg C and the velocity of the DETONATION GUN SPRAYED COATINGS shock wave can reach 3500m/sec. The hot gases generated in the detonation chamber travel down the barrel at a high Sova et al. [6] studied the development of multi velocity and in the process heat the particles to a material coatings by cold spray and gas detonation plasticizing stage (only skin melting of particle) and also spraying. The basic objective was the development of 304 Copyright © 2011-15. Vandana Publications. All Rights Reserved. www.ijemr.net ISSN (ONLINE): 2250-0758, ISSN (PRINT): 2394-6962 multifunctional multi material protective coatings using porosity were obtained. However, the coatings with the cold spraying (CS) and computer controlled detonation highest hardness did not exhibit the best tribological spraying (CCDS).As far as CS was concerned, the separate performance. A comparison of the tribological injection of each powder into different zones of the carrier performance of the optimized TiMo(CN) type coatings with gas stream was applied. Cu–Al, Cu–SiC, Al–Al 2O3,Cu– that of optimized WC–Co coatings revealed that the Al2O3 ,Al-Ti and Ti-SiC coatings were successfully abrasion resistance of TiMo (CN) type coatings is sprayed. As to CCDS, powders were sprayed with a comparable to that of WC–Co coatings. However, the recently developed apparatus that was characterized by a erosion and sliding wear resistance of TiMo (CN) type high-precision gas supply system and a fine dosed twin coatings were considerably lower than that of WC–Co powder feeding system. Computer control provided a coatings. flexible programmed readjustment of the detonation gases Kamal et al. [9] investigated the microstructure energy impact on powder thus allowing selecting the and mechanical properties of detonation gun sprayed optimal for each component spraying parameters to form NiCrAlY+CeO2 alloy coatings deposited on superalloys. composite and multilayered coatings. Several powders were The morphologies of the coatings were characterized by sprayed to obtain composite coatings, specifically, among using the techniques such as optical microscopy, X-ray others, WC– Several powders were sprayed to obtain diffraction and field emission scanning electron composite coatings, specifically, among others, WC– Co– microscopy/energy-dispersive analysis. The coating Cr + Al 2O3, Cu +Al 2O3, and Al2O3 + ZrO2. depicted the formation of dendritic structure and the micro Estimation of residual stress and its effects on the structural refinement in the coating was due to ceria. mechanical properties of detonation gun sprayed WC–Co Average porosity on three substrates was less than 0.58%
Details
-
File Typepdf
-
Upload Time-
-
Content LanguagesEnglish
-
Upload UserAnonymous/Not logged-in
-
File Pages5 Page
-
File Size-