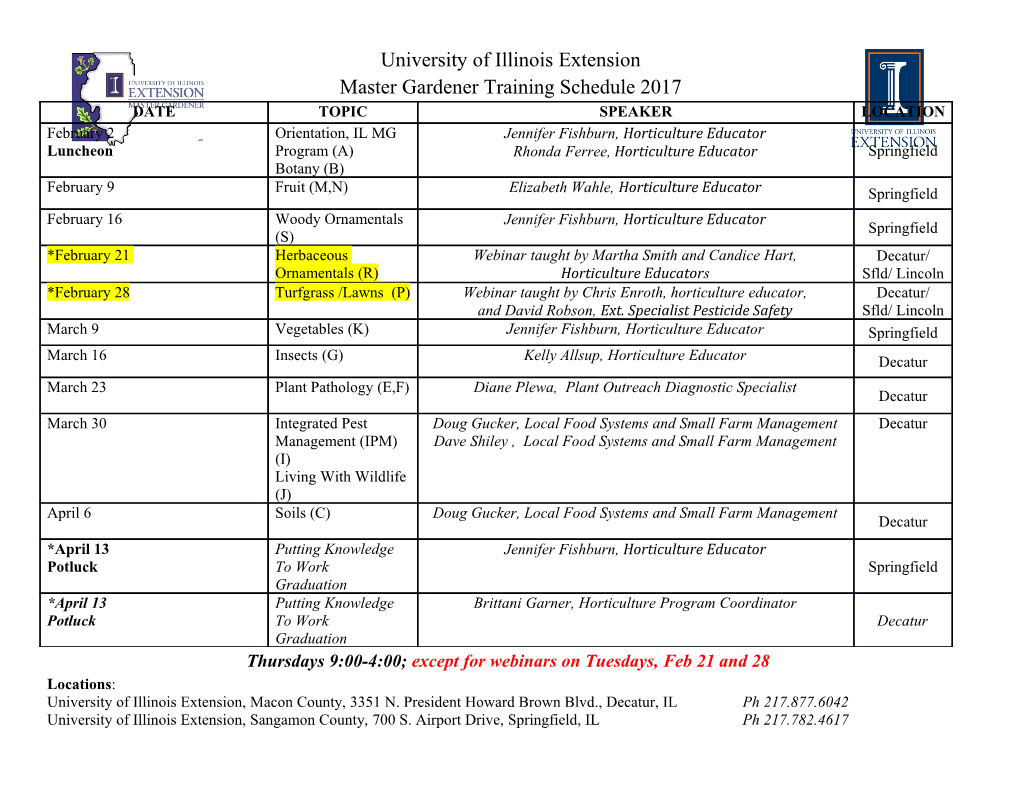
A. Fundamentals 1. Introduction 1.1 Principle mechanism Shaft kilns and cupola furnaces are used for the mass conversion and melting of granular and coarse materials. The material is transported through the vertical shaft by gravity. The hot gas flows in a counter current to the material. Typical processes are summarized in Table 1-1. For calcination processes mainly the name shaft kiln is used and for melting processes mainly the name cupola furnace. For the reduction of iron ore the name blast furnace is common. In the following for the general description the designation shaft kiln is used. Calcination of calcite CaCO3 CaO + CO2’ Calcination of magnesite MgCO3 MgO + CO2 Calcination of dolomite CaCO3 MgCO3 CaO MgO + 2 CO2 Calcination of iron ore FeCO3 FeO + CO2 Reduction of iron ore FeO + CO Fe +CO2 Reduction of lead ore Sintering of fireclay Melting of cast iron scrap Melting of copper scrap and anodes Melting of zinc scrap and ingots Melting of lead scrap Melting of aluminium scrap and ingots Melting of rock for mineral wood Melting of solid waste Table 1-1: Typical processes in shaft kilns Table 1-2 summarizes typical characteristic values of cupola furnaces and blast furnaces and Table 1-3 presents those values of common shaft kilns. From the two tables it can be seen that blast furnaces are the biggest one in size and max. outflow. However, the outflow in relation to cross section is only a little bit larger than that of normal shaft kilns. Pure melting furnaces have the highest output flux. Here, the material has only to heat up and to supply with the melting enthalpy. In lime calcination and iron ore reduction the material needs a lot of reaction enthalpy for the mass conversion. This results in a higher energy consumption and a lower outflow flux. The energy supply is relatively high in the coke fired melting furnaces. The air has to be burnt with an excess air number lower than one that CO is produced to protect the iron from oxidation. The flue gas leaving the furnace contains a CO concentration of 20 – 25 %. This gas is after burnt to preheat the combustion air. Coke must be used as fuel because it builds a carrier framework for the material and the hot melt flow. Figure 1-1 shows schematically a shaft kiln as an example for the calcination of limestone. Limestone particles are filled in a container, weighed on a balance, lifted to the top of the kiln and then poured into the shaft. The material passes a sluice 101 before it falls on the packed bed. The gas has to be separated for cleaning. On the way down the particles are initially preheated from the hot gas and after reaching the reaction temperature calcinated. For the supply with energy fuel and air are injected with burners placed in the wall. The jet hits immediately after leaving the burner against particles and is converted into the vertical direction. The penetration depth of the burner jet in horizontal direction is therefore very low. As a consequence burners inside the bed are necessary. Blast Characteristics Cupola furnaces furnaces iron scrap mineral copper iron ore Process melting melting melting reduction Max. diameter in m 2-4 1.5 - 3 1 - 2 10-15 Cross sectional area in m2 4-20 2 - 8 1 - 2 80-180 round Shape cross section rectangular round round round Height of packed bed in m 3-20 4 - 8 10 - 12 25-33 Max. working volume in m3 5000 20-150 Size of particles in mm scrap 50 - 250 scrap 20-40 irregular Max. output in t/d 2000 500 70 17000 Output flux in t/d/m2 200 100 20 50-70 Production rate in t/d/m3 1,5 1.5-2.5 Mean solid velocity in m/h 2-3 2 - 3 2 - 3 1.5-2 3 2 Air flux in mSTP / m / s 3-4 1 – 1.5 .... 0.5-0.8 Gas pressure at top in bar 1 1 1 1-3.5 Gas press. at bottom in bar 1.3 1.2 1.2 2-6.5 Hot blast temperature in °C 800-1000 800 200 1100-1300 Max. solid temp. in °C 1000-1500 1400-1600 1060 1400-1500 Max. gas temp. in °C 1800-2000 2000-2200 1150 2000-2200 coke Mean kind of fuel coke natural gas coke natural gas Fuel energy supply in kiln 5-6 5-6 0.8 16-18 MJ/kg output Table 1-2: Typical characteristics of Cupola and Blast furnaces 102 Characteristics Normal shaft Mixed-Feed Annular PFR Output capacity, t/d 150 –300 100 - 200 200 - 600 200 - 800 Inner diameter, m 2.0 – 3.0 2.5 – 6 3.0 – 4.5 2.5 – 3.5* Cross-sect. area, m2 3 –7 6 – 30 20 - 23 6 - 10* Height of solid bed, m 10 – 15 15 - 20 15 - 25 15 – 20 Output flux, t/d/m2 40 – 45 10 - 25 15 - 30 20 - 30* Solid velocity, m/h 1.8 – 2.0 0.5 – 1.0 0.6 – 0.7 0.6 – 1.4 3 2 Air flux, m STP/m /s 0.6 - 0.7 0.1 - 0.12 0.6 - 0.8 0.8 - 1.1 Min. particle size, mm 30 20 30 20 Max. particle size, mm 150 200 250 160 Total press., drop, 200 – 250 10 - 30 200 - 400 300 - 400 mbar natural/lean natural/lean gas anthracite natural/lean gas Mean kind of fuel gas lignite coke lignite/pet coke coal/oil MJ/kg 3.8 - 4.8 3.9 - 4.5 3.8 - 4.1 3.3 - 4.0 Energy lime supply kcal/kglime 910 – 1150 930 - 1080 910 - 980 790 - 950 Max. solid temp., °C 1400 – 1500 1100 - 1300 1100 - 1200 1100 - 1200 Max. gas temp., °C 1500 – 1600 1300 - 1400 1200 - 1300 1200 - 1300 type hard-burnt hard/middle middle/soft soft-burnt Lime reactivity low low/medium medium/high high * Data given for one shaft Table 1-3: Typical characteristics of common shaft kilns 103 The figure shows a central burner with axial supply. A lot more designs exist to improve the horizontal mixing in the cross section. The basic constructions are discussed later in a separate chapter. The homogenization of the temperature and concentration in the cross section is a main problem in shaft kilns. Above the burners the calcination takes place. Below the burners the lime has to be cooled down. Therefore, a part of the combustion air flows from the bottom in counter current through the packed bed. The output of the material is managed in different ways, e. g. by moving plates. The gas leaving the shaft contains a lot of dust which is formed by the friction between the particles, by cracking of particles and from the ash of coal firings. Therefore a filter system is necessary. All openings at the top of the kiln for charging stone and the bottom of the shaft for discharging lime are sealed by hydraulically operated traps. Figure 1-2 shows for a normal shaft kiln as an example the typical profile of the mean temperature of the solid and of the gas. For the explanation of the process it makes sense to divide the kiln into zones. After inserting the particles with ambient temperature these are heated up by the hot combustion gas in counter current. The decomposition of the limestone according CaCO3 CaO + CO2 can start after reaching temperatures of 810°C – 840°C depending on the CO2-concentration of the gas because of equilibrium conditions. This is the end of the preheating zone and the beginning of the reaction zone. The end of this zone has to be reached before the injection level of the fuel. Behind this injection lies the cooling zone. Here the particles have to be cooled down to temperatures of about 50°C – 80°C. The ambient air in counter current serves as a cooling agent. Above the level of the fuel injection the temperature of the gas increases rapidly. After exceeding the particle temperature heat can be transferred for the endothermic reaction. The mass flow of the gas and of the solid changes along the kiln as it is depicted principally in the below part of Figure 1-2. The input flow of the solid (limestone) is about 1.7 times higher than the output flow (lime) because of the CO2 separation. The total mass flow of the air for combustion is up to 1.4 to 1.8 times higher as the mass flow of the lime depending on the kind of fuel. Necessary for the cooling in counter current is a mass flow ratio of almost one because the specific heat capacities of lime and air are similar. So a part at the air can also be injected into the kiln together with the fuel which has advantage for the cross sectional homogenisation of the gas. Beginning at the fuel injection level the gas flow increases due to the CO2 separation and due to the fuel conversion if the fuel is a solid. To calculate the energy consumption for the process energy balances have to be conducted for every zone. This is necessary to ensure that the temperature of the gas at the transition between preheating and reaction zone is always higher than the temperature of the solid. If only the total kiln would be balanced a flue gas temperature could be the result belonging to the dotted line shown in the figure.
Details
-
File Typepdf
-
Upload Time-
-
Content LanguagesEnglish
-
Upload UserAnonymous/Not logged-in
-
File Pages13 Page
-
File Size-