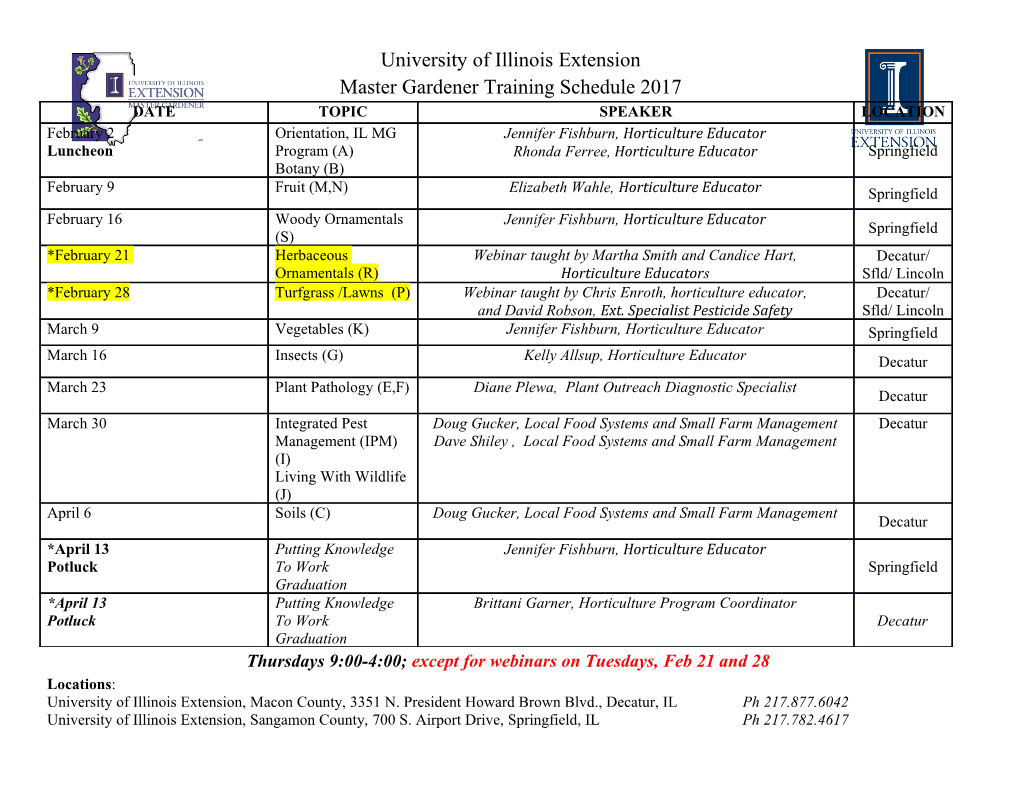
ACOUSTIC INERTIAL CONFINEMENT FUSION: CHARACTERIZATION OF REACTION CHAMBER A Thesis Submitted to the Faculty of Purdue University by Adam Butt In Partial Fulfillment of the Requirements for the Degree of Master of Science in Nuclear Engineering December 2005 West Lafayette, Indiana ii Dedicated to my parents Nasir and Patricia, My brother Dan, And my wife Marianne, For their continuous love, encouragement, and support. iii ACKNOWLEDGMENTS I would like to thank my advisor Dr. Rusi Taleyarkhan for the opportunity, guidance, and support for working on such an interesting and important topic. I also want to thank my advisor Dr. Ivana Hrbud for her guidance and support, as well as for her hard work in determining everything that needed to be done to purse two master’s degrees with joint research. I would also like to thank my other committee members Dr. Chan Choi and Dr. Stephen Heister for their relevant classroom instruction and encouragement. I would like to thank Dr. Yiban Xu for many technical discussions that helped to clarify and expedite my modeling and experimental work. Fellow masters students Joe Lapinskas and Phil Smacgaz were also helpful in many research aspects. There are many other friends that I would like to thank for their support, Ben Stein, Chris Burnside, Jeremy Corpening, Enrique Portillo, Cyril Jos, and Jim Sisco. Finally I would like to thank my brother Dan and my wife Marianne for their help in reviewing and organizing the thesis. iv TABLE OF CONTENTS Page LIST OF TABLES………………………………………………………………… …..viii LIST OF FIGURES.…………………………………………………………………….ix ABSTRACT…………………………………………………………………………......xii CHAPTER 1: INTRODUCTION ……………………………………………………….1 1.1 Background on Thermonuclear Fusion……………………………….2 1.2 Acoustic Inertial Confinement Fusion (AICF)………………………...5 1.3 Motivation for Research………………………………………………...7 CHAPTER 2: RESEARCH OUTLINE…………………………………………………8 2.1 FEMLAB™ AICF Chamber Analysis……………………………….…9 2.2 Pressure Mapping and Power Experiments………………………...12 2.3 Fusion Fuel Analysis…………………………………………………..13 2.4 Preconceptual AICF Reactor Design………………………………..13 2.5 Shielding Analysis……………………………………………………..13 v Page CHAPTER 3: ANALYTICAL AND EXPERIMENTAL SETUP……………………..14 3.1 FEMLAB™………….…………………………………………………..14 3.1.1 Application Modes……………………………………………..14 3.1.1.1 Structural Mechanics………………………….15 3.1.1.1.1 Theory…………………………………..15 3.1.1.1.2 Frequency Response Analysis……….17 3.1.1.1.3 Axial Symmetry, Stress-Strain………..18 3.1.1.2 Acoustics………………………………………..19 3.1.1.3 Fluid Dynamics…………………………………20 3.1.2 Boundary Conditions…………………………………………..21 3.1.2.1 Structural Mechanics………………………….21 3.1.2.2 Acoustics………………………………………..22 3.1.2.3 Incompressible Navier-Stokes………………..24 3.2 AICF Chamber Multiphysics Modeling Approach…………………..25 3.2.1 Geometry……………………………………………………….26 3.2.2 Physics Settings……………………………………………….27 3.2.2.1 Structural Mechanics………………………….27 3.2.2.2 Acoustics……………………………………….29 3.2.2.3 Incompressible Navier-Stokes……………….31 3.2.3 Piezoelectric Ring……………………………………………..33 3.3 Experimental Setup……………………………………………………34 3.3.1 Pressure Mapping Experimental Setup……………………..34 3.3.2 Power Measuring Experimental Setup………………………38 3.3.3 AICF Experiments……………………………………………..38 vi Page CHAPTER 4: RESULTS AND DISCUSSION………………………………………39 4.1 AICF Multiphysics Chamber Modeling………………………………39 4.1.1 Chamber Modeling Progression……………………………..41 4.1.1.1 Determination of Structural Damping Parameters………………….………………….44 4.1.1.2 Determination of Fluid Damping Parameters………………………….………….46 4.2 Experimental Benchmarking Results……………………………….54 4.2.1 Electrical Resonance Characterization…….………………..54 4.2.1.1 Coupling Factor k…………….………………..56 4.2.2 Pressure Mapping Experiments……..……………………….56 4.2.3 Benchmarking Against Rensselaer Polytechnic Institute AICF Chamber Study………………..………………………..60 CHAPTER 5: PRECONCEPTUAL AICF REACTOR DESIGN………………….64 5.1 Design Approach……………………………………………………..64 5.1.1 Determination of Sensitive Volume….………………………67 5.1.2 Trends and Assumptions…………….……………………….69 5.2 Reactor Sizing for D-D Reactions…………………………………..72 5.2.1 Reactor Design for a 1 W Breakeven Power Density Level……………………………………………………………74 5.2.2 Reactor Design for a 1 kW Breakeven Power Density Level……………………………………………………………76 5.2.3 Reactor Design for a 1 W Q =100 Power Density Level……………………………………………………………78 5.2.4 Reactor Design for a 1 kW Q =100 Specific Power Level…………………………………………………………….80 5.3 Reactor Sizing for D-T and D-3He Reactions………………………82 vii Page 5.3.1 Reactor Sizing for a D-T Reaction…………………………..82 5.3.2 Reactor Sizing for a D-3He Reaction………………………..85 5.4 AICF Reactor Shielding Analysis…………………………………….88 CHAPTER 6: CONCLUSION…………………………………………………………97 REFERENCES……………….………………………………………………………101 APPENDICES Appendix A Additional Benchmark Comparision……………………..…104 Appendix B Determination of Scaling Parameters used for Reactor Design…….…………………………………………105 Appendix C Supporting Publications……………………………………..129 Appendix D FEMLAB™ Final Chamber Model Report…………………150 viii LIST OF TABLES Table Page 3.1 Material properties for structural mechanics modeling……………..……..27 3.2 Material properties for acoustics modeling………………………………….29 3.3 Material properties for incompressible Navier-Stokes modeling…….……31 4.1 Results summary for FEMLAB™ and ATILLA™ RPI chamber models…63 5.1 Values used for AICF reactor design………………………………………..65 5.2 Summary of Assumptions…………………………………………………….72 5.3 Power Density based on Reaction Output………………………………….73 5.4 Conservative values of Power Density used for Design…………………..73 5.5 Results for 1 W Breakeven Power Density Level, D-D AICF Reactor, ChamberDesign1………………………………………………………………75 5.6 Results for 1 kW Breakeven Power Density Level, D-D AICF Reactor, ChamberDesign2………………………………………………………………77 ix Table Page 5.7 Results for 1 W Q = 100 Power Density Level, D-D AICF Reactor, ChamberDesign3………………………………………………………………79 5.8 Results for 1 kW Q = 100 Power Density Level, D-D AICF Reactor, ChamberDesign4…………………………………………………….………..81 5.9 Results for 1 W Q = 100 Power Density Level, D-T AICF Reactor, ChamberDesign5………………………………………………………………84 5.10 Results for 1 W Q = 100 Power Density Level, D-3He AICF Reactor, ChamberDesign6………………………………………………………………87 5.11 Energy Conversion Material Properties……………………………………..93 5.12 Neutron Flux at Various Positions……………………………………………95 x LIST OF FIGURES Figure Page 1.1 AICF schematic….……………………………………………………………...5 2.1 FEMLAB™ Model Navigator showing the various Application Modes ......………………………………………………………………………………10 3.1 Shaded area represents a 2-D geometry used to simplify an axis- symmetric 3-D geometry……………………………………………………...19 3.2 The 2-D axis-symmetric FEMLAB™ AICF chamber geometry…………...26 3.3 Boundaries in red are those defined by Eq.(30)……………………………28 3.4 From left to right the three types of boundary conditions used for the acoustics modeling (indicated in red); axial symmetry, sound soft, and normal acceleration……………………………………………………………30 3.5 From left to right the four types of boundary conditions used for the Navier-Stokes modeling (indicated in red); axial symmetry, neutral, normal flow/pressure, and inflow/outflow velocity………………………………..…32 3.6 Coupling relationship flow chart…………………………………………...…33 xi Figure Page 3.7 Block diagram for power measurement experiments……………………...36 3.8 Screen shot of Labview™ program developed to automate pressure mapping tests………………………………………………………………..…37 3.10 Block diagram of pressure mapping experimental setup……………….…38 4.1 Nominal and pressure mapping chamber designs………………………...40 4.2 Results for Chamber1. The far left picture shows the pressure field at the resonant frequency of 16.7 kHz, the center plot shows the response at the third mode at 25 kHz, and the plot on the right shows the pressure as a function of frequency for a point located at the center of the chamber, on the central axis………………………………………………………………....41 4.3 Various mode shapes for longitudinal waves……………………………....42 4.4 Representation of the first radial mode, which should also be the resonant mode, of the system………………………………………………………..….43 4.5 Comparison of solutions for various stiffness damping parameter values…………………………………………………………………………...45 4.6 Multiphysics model Chamber2 geometry……………………………………47 4.7 Model Chamber2 results comparison for cases with and without fluid damping…………………………………………………………………………47 xii Figure Page 4.8 Chamber2 mode shape results at 17.7 kHz, 21 kHz, and 26.9 kHz respectively……………………………………………………………………..48 4.9 Pressure response for the addition of vapor gap and mode shape at resonant frequency (17.3 kHz)……………………………………………….49 4.10 Pressure response for the addition of vapor gap and top piston and as mode shape at resonant frequency (17.3 kHz)…………………………….50 4.11 Pressure response for the addition of vapor gap and both reflectors and mode shape at resonant frequency (18.0 kHz)…………………………….51 4.12 Pressure response for the addition of the AICF chamber geometry, epoxy, silicone, both reflectors, and the vapor gap. The mode shape at the resonant frequency (17.3 kHz) is plotted on the left……………………….52 4.13 Final pressure response results……………………………………………...53 4.14 Experimental power data, characterizing the electrical resonance of the system…………………………………………………………………………..55 4.17 Pressure response at the center of the chamber for a 4 V input (transducer calibration is 10 mV/psi)………………………………………...57 4.18 Comparison of normalized peak-to-peak pressure with experimental Data……………………………………………………………………………..58 4.19 Comparison of computed pressure response for various speeds of sound for Acetone versus the experimental
Details
-
File Typepdf
-
Upload Time-
-
Content LanguagesEnglish
-
Upload UserAnonymous/Not logged-in
-
File Pages235 Page
-
File Size-